Гранулятор бытовой своими руками. Грануляторы для комбикормов своими руками
Использование пеллет в системе отопления позволяет существенно сэкономить на обогреве помещения. Данный вид топлива отличается одним из наивысших КПД, среди альтернативных источников теплового производства. Изготовление гранул своими руками — еще один способ сэкономить на покупке пеллет. Как сделать гранулятор, разберем далее.
Принцип и технология производства пеллет
Гранулятор для производства пеллет — это устройство, которое помогает изготовить гранулированое топливо или корм в домашних условиях. Перед тем как ознакомиться с рекомендациями по изготовлению гранулятора, рассмотрим технологический процесс производства пеллет с помощью самодельного гранулятора.
Пеллеты производят из различного рода сырья, например, из древесных опилков или отходов, из торфа, коры дерева, соломы, куриного помета и т.д.
Сырье для производства пеллет должно отвечать следующим требованиям:
- иметь процент влажности 11-13%;
- содержать большое количество клеящихся веществ, смол;
- должно быть очищенным от постороннего мусора.
Технология изготовления пеллет выглядит таким образом:
1. Очищенное от посторонних предметов сырье, попадает в дробилку или первичный размельчитель. В нем, происходит процесс измельчения материала для производства пеллет.
2. Сырье помещается в барабанную или аэродинамическую сушилку. В домашних условиях, для производства такого агрегата отлично подойдет деревянная или металлическая бочка.
3. В сушилке материал доводят до необходимой влажности, если влажность ниже требуемой, сырье обрабатывают горячим паром.
4. Следующий этап: повторное измельчение, которое включает вторичную переработку материала для пеллет.
5. Завершающий этап — переработка материала в грануляторе и, собственно, изготовление пеллет.
6. Готовые пеллеты сушатся и используются для системы отопления.
Преимущества использования гранулятора:
- возможность вторичной переработки отходов,
- получение качественного, готового к дальнейшему использованию продукта,
- легкость работы,
- изготовление гранулятора — довольно не сложный процесс, с которым справится и непрофессионал, при условии тщательного соблюдения инструкции,
- гранулятор способствует изготовлению топлива, которое не занимает много места и удобно в хранении,
- возможность изготавливать как топливные, так и кормовые пеллеты.
Разновидности грануляторов
В зависимости от вида матрицы грануляторы разделяют на устройства:
- с кольцевой матрицей,
- с плоской матрицей.
Первоначально был изобретен гранулятор с кольцевым видом матрицы.
Недостатки таких грануляторов:
- большая стоимость матрицы,
- низкая скорость работы.
Цилиндрическая или кольцевая матрица имеет вид перфорированного барабана, на котором расположены вращающиеся катки. Смесь для гранул вдавливается в барабанные отверстия с помощью катков. При помощи ножей, на внешней части барабана гранулы отрезаются до определенного размера.
Грануляторы с плоским видом матрицы имеют современную конструкцию, отличаются высококачественной и быстрой производительностью. Плоская матрица имеет вид вала, на котором закреплен жесткий диск. Такие устройства способны перерабатывать различного рода отходы, в том числе и с твердых пород деревьев. Для гранулятора с кольцевой матрицей, такая задача является непосильной.
В соотношении с креплением матрицы выделяют грануляторы:
- горизонтального типа,
- вертикального типа.
В соответствии с типом работы выделяют:
- грануляторы редукторного типа,
- пресс-грануляторы.
Осуществление процесса производства пеллет в редукторном гранулятора выполняет редуктор. В зависимости от типа редуктора такие грануляторы разделяют на:
- одноступенчатые,
- двухступенчатые.
Пресс-грануляторы более распространены, чем редукторные. Ключевой деталью, которая отвечает за правильность работы устройства является прессовый узел. Основной его составляющей служат роллеры, отвечающие за раскатку сырья. Матрицы данного устройства оснащены специальными формами, которые формируют пеллеты.
В зависимости от назначения выделяют:
- грануляторы для производства корма,
- грануляторы для изготовления топливных пеллет.
Устройство гранулятора
Основные компоненты гранулятора включают:
- основную раму,
- грануляторный пресс,
- дверцу.
Роллеры — отвечают за процесс выдавливания готовой массы, и за формирование пеллет. В соответствии с заданной длинной, смесь разрезается специальными ножами. После остывания гранул — они готовы к использованию. Остывание является обязательной процедурой, без которой пеллеты не обретут крепости и целостности.
Для изготовления гранулятора своими руками, потребуется наличие:
- электродвигателя,
- редуктора,
- вала,
- основы под гранулятор,
- шерстей,
- матрицы.
Гранулятор для пеллет своими руками
Размер основы для рамы под гранулятор определяет мощность прибора. Для ее изготовления понадобится профиль с прямоугольным сечением. Минимальное сечение профиля 4х2,5 см.
Используйте листовой материал для изготовления корпуса гранулятора. Он состоит из двух частей, одна — отвечает за подачу сырья, а вторая — за выход готовых пеллет. Рекомендуется изготавливать корпус в форме цилиндра. Чтобы матрица осуществляла вращение свободно, сделайте корпус диаметром чуть больше, чем матрица.
Нижняя часть корпуса должна быть оснащена желобом, по которому будут выходить готовые пеллеты.
Не следует соединять две части корпуса, с помощью сварки, для этого лучше использовать болты. Этот процесс обеспечит легкость в чистке гранулятора.
Гранулятор своими руками чертежи:
Изготовление редуктора для самодельного гранулятора
Для изготовления самодельного редуктора возможно использование заднего моста от мотоциклов, таких как Урал или Днепр. Данную деталь легко достать на рынках автозапчастей. Вертикально сзади редуктора расположится электродвигатель.
Если использовать электродвигатель мощностью 1500 оборотов, то выходная мощность составит 325 оборотов.
Гранулятор: особенности изготовления
Схема гранулятора довольно сложная, но вполне выполнимая в домашних условиях. Для изготовления гранулятора понадобится наличие:
- металлического уголка,
- матрицы,
- листов качественного металла,
- вала вращения,
- электродвигателя,
- крепежных элементов,
- сварки.
Инструкция по изготовлению гранулятора:
1. Для сооружения прочного основания под гранулятор воспользуйтесь металлическим уголком и сваркой.
2. Короб — это основание гранулятора. Он изготавливается с помощью металлического листа и сварки.
3. Горизонтальная верхняя часть короба должна содержать отверстие, диаметром, чуть больше матрицы. Это отверстие служит местом загрузки сырья для изготовления гранул.
4. Возьмите металлический лист, ширина которого не превышает 100 мм, и по диаметру отверстия соорудите борт, оторые будет препятствовать выпаданию сырья.
5. Нижняя часть короба должна содержать отверстие, размер которого зависит от диаметра матрицы.
6. Боковая часть должна также содержать отверстие, через которое будут выходить готовые гранулы.
7. Из металлического листа следуйте желоб, который следует прикрепить к боковому отверстию.
8. Чтобы установить вал вращения и матрицу воспользуйтесь гайками. Матрица должна крепиться на одном уровне с верхней частью короба.
9. С помощью гаек и болтов закрепите устройство на основании. Установите и зафиксируйте электродвигатель.
10. С помощью ремневой передачи зафиксируйте вал мотора и матрицу.
11. Используйте старое жестевое ведро, предварительно избавившись от его дна, для изготовления раструба, который облегчит подачу сырья. Соорудить раструб возможно из металлического листа.
12. Произведите установку катка и шестерней на поверхность матрицы.
Матрица — это довольно сложный прибор, от работы которого зависит производительность и качество изготовляемых гранул. Рекомендуется приобрести готовую матрицу для самодельного гранулятора, такие устройства продаются на рынке, как отдельные запчасти к заводским устройствам.
При желании в самостоятельном изготовлении матрицы, следует приобрести диск, минимальная толщина которого составляет 2 см.
От диаметра диска зависит производительность гранулятора. При производстве 150 кг гранул в течении одного часа, следует приобрести диск диаметром 25 см и двигатель мощностью 15 кВт.
Центральную часть диска следует просверлить и сделать отверстие, в соответствии с размером валового сечения. Для выполнения жесткой посадки воспользуйтесь пазом, чтобы пеллеты хорошо прессовались и выводились, нужно сделать конусообразные отверстия.
Ширина роликов или шестерней должна быть такой же как и рабочая поверхность матрицы.
Процесс сборки матрицы включает надевание шестерней на вал, прикрепите вал с шестернями с помощью муфты перпендикулярно редукторному валу.
1. Для изготовления корпуса гранулятора воспользуйтесь металлической трубой или цельным стальным листом. Основная функция верхней части корпуса — осуществление процесса загрузки сырья, а нижняя часть отвечает за выход прессованной массы.
2. Щель между матрицей и корпусом гранулятора должна быть минимальной.
3. Для крепления редукторного выходного вала воспользуйтесь муфтой и подшипниками.
4. Установка корпуса на раму должна быть жесткой.
5. Готовое устройство следует окрасить с помощью краски по металлу, предварительно покрыв поверхность антикоррозийным раствором.
Гранулятор своими руками видео:
Каждый владелец личного подсобного хозяйства стремится вырастить свою живность с минимальными затратами. Гранулированные корма — один из способов для достижения этой цели. Но если приобретать готовые гранулы комбикорма, то они обойдутся значительно дороже, нежели просто рассыпной пищевой продукт. Поэтому многие принимают решение изготовить гранулятор комбикорма своими руками. Чертежи особой сложности не представляют и будут понятны любому животноводу.
Несколько слов о преимуществах гранул
Более высокая цена на комбикорм в гранулах в сравнении с аналогичным по составу, но рассыпным объясняется наличием у него нескольких преимуществ. Так, гранулированный корм дольше хранится, легче транспортируется. Он хорошо переносит изменения климатических условий хранения (температуры и влажности), прямые солнечные лучи. В процессе гранулирования корм консервируется. В новом состоянии в него труднее проникнуть различным бактериям и микроорганизмам.
Еще одно важное достоинства гранулированного комбикорма — сбалансированность. В процессе изготовления гранул смесь можно дополнить различными питательными веществами, минералами, витаминами и другими добавками. Для каждого вида животных, учитывая их возрастную группу, можно приготовить свой отдельный вариант данного вида корма. Все компоненты тщательно перемешиваются и собираются в одну гранулу. За счет этого животные не способны выбрать из пищи только то, что им нравится. Они съедают все вместе. При правильном подборе составляющих продуктивность повышается до 25%. Все эти преимущества можно получить, если изготовить гранулятор корма своими руками.
Принцип действия агрегата
Работают изготовленные своими руками грануляторы по тому же принципу, что и заводские. В емкость засыпается сырье. Снизу расположена матрица со множеством отверстий. Вращающиеся ролики продавливают сырье через отверстия матрицы. Спрессованная масса, которая, пройдя сквозь отверстия матрицы, принимает форму длинного цилиндра, разрезается вращающимся ножом на небольшие гранулы. Через специальное отверстие (окошко) в корпусе готовые гранулы высыпаются наружу в подготовленную тару.
Необходимые материалы
Разобравшись, как сделать гранулятор своими руками, можно приступать к подготовке необходимых деталей. А потребуются для этого следующие комплектующие:
- Рама, на которой будут устанавливаться все остальные элементы.
- Матрица с подготовленными отверстиями.
- Ролики, поверхность которых должна быть зубчатой.
- Электрический двигатель.
Подобрав необходимые комплектующие, можно приступать к сборке аппарата.
Подготовка матрицы
Одним из основных элементов собранного своими руками гранулятора является матрица. Она представляет собой металлический диск с отверстиями. Причем, отверстия должны иметь форму конуса, чтобы смесь плотнее сжималась. Именно по этой причине матрицу чаще всего покупают уже готовую. Для ее изготовления потребуются специальные станки.
Те, кто не боится трудностей, все-таки изготавливают матрицу самостоятельно. Основой для нее является металлический диск. Причем толщина металла должна быть не менее 2 см., а диаметр — соответствовать диаметру корпуса. Большого зазора между ними оставаться не должно.
В центре сверлится отверстие. В нем подготавливаются пазы, которые обеспечивают плотное прилегание матрицы. Далее по поверхности диска делают конусовидные отверстия.
Сборка аппарата
В качестве корпуса часто используют кусок металлической трубы или жестяное ведро (нужно удалить дно). Можно свернуть цилиндр из стального листа. Снизу устанавливают лоток, предназначенный для высыпания готовые гранулы.
Каркас, на котором будет крепиться оборудование, изготавливают из прочного металла. Рама должна выдерживать большие нагрузки и сильную вибрацию в процессе работы.
В нижней части каркаса крепится редуктор, который будет передавать вращение от электрического двигателя к матрице. Он соединяется с электрическим двигателем ременной передачей (можно цепной).
В корпусе снизу устанавливается матрица, немного выше — прижимные ролики. Передача вращения осуществляется с помощью подшипников качения. Они же соединяют катки с валом.
Гранулятор из мясорубки
Существует еще один вид аппарата, который отличается меньшими размерами. Собирают подобные мини-грануляторы своими руками из мясорубки. Принцип их действия немного отличается от описанного выше: смесь кормов продавливается в отверстия матрицы за счет вращения шнека.
Собрать грануляторы своими руками из мясорубки очень просто. Достаточно поменять местами матрицу и нож. К такому варианту также можно подключить электрический двигатель. Делается это через ременной привод. Двигатель должен вращаться на больших оборотах. А шнек, наоборот, на маленьких. Чтобы корма склеивались плотнее, создают и устанавливают маховик.
К мясорубке изготавливают крышку. Ножи устанавливают с наружной стороны матрицы. Закрепляют их с помощью болтов. В последнюю очередь монтируют двигатель, шкивы и ремень.
Как видно, изготовить гранулятор своими руками несложно. Главное выбрать подходящий вариант и отыскать необходимые материалы. Результатом послужит гранулированный корм, который обязательно понравится животным (или птице). Причем очень важным является тот факт, что гранулы будут содержать в себе все самые необходимые вещества. В итоге, при экономии кормов производительность значительно возрастет.
Низкое качество покупных кормов, стремление оптимизировать затраты заставляют заводчиков сельскохозяйственных животных и птиц задумываться о применении более качественных и экономически выгодных гранулированных комбикормов и изготавливать их в домашних условиях.
Идеальным вариантом в этом случае является бытовой гранулятор для комбикорма, который можно купить или сделать своими руками.
Принцип работы и устройство гранулятора
Аппарат выполняет измельчение, смешивание компонентов комбикорма, взятых в определённых пропорциях, последующее прессование полученной массы в цилиндрические гранулы (пеллеты).
Простейший гранулятор состоит из 4 основных узлов:
- Гранулирующий узел. Находится в верхней части устройства. В него входит матрица с отверстиями (именно через них производится выдавливание измельчённой массы).
- Подшипниковый узел. Находится под гранулирующим узлом. Состоит из радиальных и роликового упорного подшипников, надетых на вал.
- Корпус с маховиком, поддерживающим медленное вращение ведущего вала.
- Электродвигатель.
Матрица может быть двух видов, от этого зависит принцип образования гранул:
- Цилиндрическая. Представляет собой цилиндрический барабан с отверстиями.
Внутри матрицы вращаются роллеры, которые прокручивают поступившую массу комбикорма и заставляют её проходить через отверстия матрицы. На выходе цилиндрические гранулы срезаются ножами.
- Плоская. Изготавливается в виде жёсткого диска с круглыми отверстиями, через которые также продавливается корм. Диск надёжно фиксируется к вращающемуся валу. Гранулятор с плоской матрицей способен перерабатывать более твёрдое сырьё.
Устройство работает от электродвигателя или от ручной рукоятки.
Электродвигатель через маховик с клиноременной передачей передаёт вращение валу и установленным на нём гранулирующим и подшипниковым узлам.
Гранулирующий узел – основной элемент, осуществляет:
- размельчение, перетирание компонентов комбикорма в муку;
- прессование полученной однородной массы;
- выдавливание гранул.
Размеры гранул определяется конструктивными особенностями устройства:
- диаметр – величиной отверстий в матрице;
- длина – расстоянием между лопастью и матрицей.
Не везде дрова или уголь — доступное топливо, а вот отходы деревообрабатывающей промышленности или сельского хозяйства найти можно, пожалуй, везде. Давно замечено, что горят они, может, чуть хуже, но отапливаться ими вполне можно. Только просто насыпать опилки или солому очень неудобно. Поэтому придумали их перерабатывать и прессовать в брикеты или гранулы. Для топливных гранул — пеллет — есть даже специальные котлы. При хорошем топливе они обслуживаются (выгребают золу) раз в месяц. Самая хорошая новость состоит в том, что вполне можно сделать пелеты своими руками. Для этого потребуется достаточно много оборудования, но основа — гранулятор (экструдер или пеллетайзер). Без него никак.
Что такое пеллеты и каких видов они бывают
Пеллеты — это топливные гранулы, которые изготавливаются из отходов деревообрабатывающей промышленности, некоторых остатков растениеводства (солома, лузга подсолнечника, гречихи и т.п.) и даже из куриного помета. Технология их производства такова, что никаких добавок и связующих не требуется. То есть, это абсолютно безопасное и стопроцентно натуральное топливо, которое к тому же сделано из отходов.
Пеллеты — хорошее топливо
Так как сырье для топливных пеллет может быть разным, то и характеристики топлива различны. Делят пеллеты на три категории:
- Белые. Это топливо премиум класса с наивысшими характеристиками (и ценой). Названо так за характерный цвет — светло-желтый, почти белый. Но цвет вторичен, первичны характеристики и главная — очень низкая зольность. После сгорания белых пеллет золы остается не более 0,5% от объема топлива. Чистить котел надо будет очень редко. Белые топливные гранулы получают из стружки без коры и других посторонниз включений. Как правило, это столярное или мебельное производство.
- Серые. Сырье для этого типа пеллет может содержать некоторый процент коры, хвои и некоторых других посторонних примесей. Но зольность при этом не должна быть более 1,5%.
- Промышленные или темные пеллеты. Этот вид топливных гранул делают из соломы или жмыха в чистом виде или с добавлением древесных отходов.
Зольность этого типа топлива намного выше, чем описанных выше, тем не менее, она не может быть выше 5%.
Белые и серые пеллеты используются для индивидуального отопления. Их еще называют «первого класса» или первокассными. Они имеют диаметр 6-8 мм, плотность примерно 600 кг/м 3 , количество выделяемого тепла — около 4,7 кВт/ч. Сжигаются они в специальных котлах, которые так и называются — пеллетные. Обычно это оборудование очень требовательно к качеству топлива. Кроме малой зольности предъявляются требования и по целостности гранул, и по отсутствию пылевидной фракции. В противном случае горелка пеллетного котла забивается, котел отключается. Промышленные пеллеты сжигаются тоже в специальных печах, но они имеют абсолютно другое строение и намного большие объемы.
В принципе, любые пеллеты можно засыпать в твердотопливные котлы, только их обычно используют на стадии тления. Когда печь уже разогрета, засыпают некоторое количество гранул.
Технология производства
Для любого хозяина идея превратить отходы в топливо, или даже на этом заработать денег, является привлекательной. В принципе, сделать пеллеты своими руками реально, но ожидать от них промышленного качества не стоит. Заставить на работать импортный пеллетный котел на самодельных гранулах вряд ли получится, но самодельный или твердотопливный агрегат отлично с ними справляется.
Технология производства древесных пеллет состоит из нескольких последовательных этапов:
- Крупное дробление сырья. Фрагменты должны быть не более 1,25 см 3 . Это подготовка для более качественной сушки. Для этой операции нужна дробилка.
- Сушка в сушильной камере. Сырье доводят до влажности 8-12%. Камеры есть разных типов, в некоторых используют прямой нагрев (в сушильную камеру подается раскаленный воздух из топки), в других греется теплообменник, а от него — воздух в сушилке. Второй вариант менее эффективен, но в этом случае исключена возможность попадания сажи в сырье. Даже небольшое количество сажи способно окрасить щепу. В результате по качеству пеллеты могут относится к «белым» (если использовали соответствующее сырье), а по цвету — к серым.
- Мелкое дробление. Просушенную древесину подают в дробилки (обычно молоткового типа). На выходе фрагменты древесины имеют размеры на более 1,5 мм для белых и серых пеллет, и 4 мм для промышленных.
- Увлажнение. Древесные волокна с малой влажностью не смогут склеиться. Потому их увлажняют. Если используются отходы сосны, ели, впрыскивается вода. Сырье из твердых пород — дуба, березы, бука — обрабатывается горячим паром.
- Прессование. Тут работают прессы разных конструкций. Сырье продавливается через матрицу (плоскую или круглую), которые и формируют цилиндры заданных размеров.
- Охлаждение. Под воздействием высокого давления пеллеты нагреваются до 70-90°C. В таком состоянии они легко крошатся, потому их оставлют остывать.
- Готовые гранулы просеиваются (от остатков не склеившихся частиц) и фасуют.
Как видите, процесс многоступенчатый, требует довольно большого количества оборудования. Тем не менее, при наличии дешевого или бесплатного сырья производить пеллеты своими руками выгодно.
Особенности производства пеллет из соломы
Сделать пеллеты из соломы проще. Она изначально идет сухой, потому этап сушки отсутствует. Если же есть мокрая солома, ее сушат в естественных условиях на солнце, а затем измельчают и подмешивают к сухой, добиваясь тем самым требуемой влажности исходного сырья перед прессованием.
Легче происходит и измельчение. Для этого требуется соломорезка, которая сразу нарезает сырье на фрагменты требуемой длины. Так что измельчение тоже проходит за один раз. После доведения массы до требуемой влажности, ее продавливают через пресс. И тут все проще: так как сырье более мягкое, усилий требуется меньше. Менее мощное оборудование — меньшие затраты. При этом производительность линии может быть высокой.
Как видите, оборудования для производства пеллет из соломы требуется меньше, да и затрат времени и энергии тоже меньше.
Самодельные грануляторы
Хоть оборудования для производства пеллет требуется много, основное устройство — гранулятор. С его помощью из сырья формируются пеллеты. Есть несколько моделей грануляторов:
Самый простой по строению шнековый экструдер. Его часто делают для прессовки комбикормов, но можно использовать и для изготовления топливных гранул из мягкого сырья. Если вам необходимо сделать оборудование для производства пеллет, это — самый простой вариант. При условии, что вы умеете обращаться с токарным станком и сварочным аппаратом.
Самодельный шнековый гранулятор
Как и в любом оборудовании подобного типа у шнекового гранулятора есть матрица. В данном случае она похожа на сетку мясорубки, только сделана из пластины намного более толстой. Второй важный узел — шнековый вал. Все эти детали можно сделать своими руками. Как — описывать словами бесполезно, смотрите в видео.
Изготовление матрицы под готовый шнек.
Шнек и матрицу «упаковывают» в корпус или гильзу. Как ее сделать, смотрим в следующем видео.
После сборки основного узла надо установить мотор с редуктором, бункер, в который будет подаваться измельченная солома. Можно запускать.
Как сделать гранулятор с плоской матрицей
Сначала надо разобраться с тем, как он устроен. Все отлично продемонстрировано в видео.
В следующем ролике довольно подробные пояснения по процессу изготовления матрицы и роликов.
На деревообрабатывающем производстве ежедневно образуются отходы. Им можно найти применение, например: изготовить пеллеты из опилок, которые послужат топливом для обогрева помещений. Если даже открыть бизнес, то это будет доходное дело, потому что сырье достается недорого либо бесплатно. А гранулы из опилок пользуются спросом из-за множества преимуществ:
- Топливные гранулы являются практичными, удобными в хранении, транспортировке и использовании.
- Опилки – это доступные отходы на деревообрабатывающих предприятиях, которые после процесса прессования увеличивают свою теплотворную способность, а главное, обладают наименьшей зольностью.
- Во время производства не добавляются химикаты, поэтому гранулы отличаются экологичностью.
- Пеллеты можно изготавливать в домашних условиях и существенно экономить на топливном материале.
Немаловажно то, что в процессе хранения они занимают мало места в помещении, если сравнивать с углем или дровами. Пеллеты можно разложить по мешкам либо целлофановым пакетам и складировать.
Древесные отходы для изготовления гранул удобны, легко добываемы, но при этом они должны соответствовать нескольким требованиям:
- Чтобы получить топливо хорошего качества, следует использовать опилки, получаемые из дерева мягкой породы.
- Исключено применение щепок или обломков, желательно делать гранулы из отходов среднего размера.
- Опилки с влажностью около 15% хорошо гранулируются и дают максимум тепла при сжигании, в случае избытка влаги, наоборот, не прогревают помещение.
Важно! Перед тем как приступить к производству, требуется подготовить сырье, чтобы на выходе получить качественные древесные гранулы.
В промышленности древесные гранулы изготавливают из разнообразного сырья:
- Древесные отходы: опилки, щепа;
- Солома, получаемая из зерновых культур;
- Отходы подсолнечника либо шелуха гречишная;
- Куриный помет.
Обычно производят пеллеты из древесных отходов. Гранулы, полученные из соломы, подсолнечника либо гречихи отличаются дешевизной и низким качеством из-за зольности. Спросом среди покупателей пользуются пеллеты из опилок.
Производство
Изготовление пеллет – это переработка отходов, остающихся при изготовлении пиломатериалов. Давайте выясним, какое оборудование понадобится для их производства.
Этап №1. Изначально подготавливается сырье путем дробления щепы и крупных отходов. Делают это при помощи автоматизированной дробилки, которая на выходе дает опилки размеров в 4 мм.
Машину-дробилку для домашнего пользования можно приобрести либо сделать своими руками.
Этап №2. Необходимо просушить сырье с помощью сушилки. Для этого понадобятся:
- Сушильный барабан
- Сушилка аэродинамического либо ленточного типа
- Пневмосушилка
- Диспергатор
Для испарения избыточной влаги нужна тепловая энергия, поэтому для прессования качественных гранул требуется изготовление сушилки с функцией подогрева.
Этап №3. Основная задача: как сделать пеллеты? Для операции потребуется станок – пресс-гранулятор.
Как сделать гранулятор комбикорма из мясорубки?
Агрегат имеет матрицу, которая может быть цилиндрической либо плоской. Для производства больших объемов древесного топлива применяют цилиндрический станок, который изготовить самому очень сложно. А станок плоского типа как раз наоборот – легок в сборке и отлично подойдет для изготовления топливного материала для личного пользования.
Этап №4. Упаковка полученной продукции. После остывания гранул их расфасовывают в плотные целлофановые пакеты, чтобы избежать деформации упаковки и появления сырости.
В итоге пеллеты, сделанные в домашнем хозяйстве, являются экономически выгодным делом, с учетом того, что сырье сухое, а пресс-гранулятор собран с минимальными затратами. Если комплексное оборудование для производства пеллет из опилок делается на заказ, не собственноручно, а приобретается, вам придется потратиться.
Если рассматривать широкое производство с целью заработка, оборудование собственного изготовления не подойдет. Здесь нужно задуматься о первоначальном вложении в комплект техники.
Советы начинающим производителям древесных гранул
Если вы решили всерьез заняться производством и продажей пеллет в больших объемах, то принять во внимание нужно несколько советов:
- Перед началом работы важно найти постоянный источник древесных отходов, чтобы ваша деятельность была стабильной и без застоев производства. В случае перебоев с доставкой опилок, работа может встать – вы потеряете доверие и свою клиентуру.
- При покупке оборудования не стоит экономить и брать б/у технику. Она может выйти из строя в самый неподходящий момент.
- Выбирая участок расположения завода, предприятия, стоит задуматься о рабочем персонале, о том, как они будут добираться до работы: ходят ли автобусы, маршрутки в эту сторону.
- Важно собрать необходимый пакет документов до начала запуска производства, чтобы избежать проблем с законом.
Затраты
При составлении и расчете бизнес-плана стоит учесть такие пункты по расходам:
- Аренда здания либо большого помещения;
- Зарплата рабочим;
- Закупка комплексного оборудования;
- Сырье;
- Оплата коммунальных услуг;
- Налоги, отчисления в пенсионный фонд;
- Расходы по транспортировке сырья и готовой продукции.
Сбыт продукции
В любом бизнесе нужны стабильные каналы сбыта продукции. Собрав свою базу клиентов, вы сможете расширять дело и объемы производства.
Точкой сбыта могут быть строительные магазины, рынок, сайт в интернете. Наиболее выгодно заключать сделки с оптовиками и сбывать продукцию большими партиями. Не стоит забывать, что древесные гранулы – экологически чистый товар, который пользуется спросом в зарубежных странах. Важно не расслабляться и пополнять базу клиентов: размещайте объявления и звоните владельцам торговых точек с большей проходимостью людей. Ваш доход зависит от того, какой объем продукции будет продан.
Вывод таков: если запускать предприятие по производству пеллет – это перспективно и выгодно, можно зарабатывать приличные деньги. Тем более что экологически чистое топливо в наше время востребовано. Стоимость продукции растет, а при грамотно составленном бизнес-плане вы получите успешно развивающееся дело.
Предыдущая статья: Устройства альтернативной энергетики для частного дома Следующая статья: О новых технологиях в энергетике
На ту же тему
Матрица и ролики для гранулятора: купить все комплектующие в одном месте
В нашем интернет-магазине всегда в наличии множество оборудования для гранулирования и комплектующих запчастей на самые популярные модели. Мы предлагаем матрицы, ролики и другие детали для гранулятора только от производителя. Это гарантирует оригинальное качество отдельно взятой запчасти.
Особым спросом пользуются надежные и эффективные матрицы от немецкого производителя «Muench edelstahl». Компания уже более 30 лет занимается выпуском высококачественного гранулированного оборудования.
При производстве матриц используются самые последние разработки, что продлевает детали срок службы более чем в два раза по сравнению с другими марками. Все запчасти изготовлены точно в соответствии с документацией и характеристиками, указанными на сайте.
Преимущества комплектующих от компании «Дарлит»:
- надежность и долговечность каждой запчасти;
- оригинальное качество завода-производителя;
- низкая стоимость продукции;
- наличие всех необходимых сертификатов качества.
Клиенту мы гарантируем бесперебойную поставку комплектующих в нужном объеме и ровно в оговоренные сроки.
Матрица, ролики для гранулятора любой модели
У вас никогда не будет проблем, связанных с неисправностью оборудования. В нашем магазине широкий ассортимент всех необходимых деталей от лучших мировых производителей. Опытные менеджеры помогут каждому клиенту идеально подобрать матрицы и ролики для гранулятора конкретно для вашей модели. Доставка осуществляется в любой регион России, что делает наш сервис оптимальным для жителей всех регионов.
Преимущества работа с магазином «Дарлит»:
- Бесперебойная поставка запчастей по всей РФ.
- Оригинальное качество от завода-производителя.
- Оптимальная цена без наценки посредников.
- Бесплатная консультация от опытных менеджеров.
Для нас важно не только качество нашей продукции, но удобство сервиса для покупки необходимого товара. С каждым днем мы стремимся сделать его более доступным для наших клиентов.
Как сделать самодельный гранулятор для комбикорма
Гранулятор комбикорма бытовой своими руками чертежи
Гранулятор комбикорма бытовой своими руками, чертежи оборудования с электрическим приводом, клиноременной передачей и плоской матрицей.
Прежде чем приступить к проектированию оборудования произведем несложный расчет.
Следует помнить, что:
- максимальное передаточное отношение клиноременной передачи – не более 6.
- угол обхвата на малом шкиве – не менее 120°
Из стандартного ряда по ГОСТ 17383-73, выберем диаметры шкивов
Ведущий шкив (D1), диаметр 56 (мм)
Ведомый шкив (D2), диаметр 315 (мм)
Чертеж гранулятора .
Чертеж привода матрицы гранулятора.
- Корпус.
- Лопатка.
- Матрица.
- Шайба.
- Винт с внутренним шестигранником DIN 4762 — М8 х 20.
- Шайба пружинная стопорная DIN 128 — А8.
- Шпонка призматическая DIN 6885 — А8 х 7 х 22.
- Гайка DIN 44232 — М8.
- Винт с внутренним шестигранником DIN 912 — М8х1 х 30.
- Подшипник радиально упорный однорядный DIN 625 — 6307 с защитными шайбами или 66307 по ГОСТ 831-75 (35 х 80 х 21).
- Шайба стопорная DIN 6731 — 32.
- Гайка специальная DIN 1804 – М32х1,5.
- Шпонка призматическая DIN 6885 — А8 х 7 х 50.
В дополнение, посмотрим видеоматериал из двух частей, где показан порядок сборки бытового гранулятора комбикорма с плоской матрицей.
Рекомендуем также
Гранулятор своими руками | Изготовление пеллет своими руками
Большое количество различных механизмов, приобретение которых не целесообразно из-за очень высокой стоимости или не возможно из-за ограниченного предложения на рынке может быть изготовлено самостоятельно. Одним из таких механизмов является гранулятор – аппарат для изготовления кормовых или отопительных гранул (пеллет). Использование гранул позволяет значительно разнообразить рацион домашних животных, сохраняя питательные свойства различных видов растительного и животного корма. Применение топливных гранул уже нашло широкое применение в странах северной Европы как прекрасная альтернатива не только твердым (дрова, уголь), но и жидким (солярка, мазут) видам топлива. Для их изготовления используются такие виды отходов обработки древесины, как опилки и стружки. Иногда для получения сырья осуществляют измельчение макушек деревьев, остающихся при лесозаготовке, а так же сучьев и корней.
Предлагаемые к продаже заводские экземпляры имеют либо очень большую производительность, что не позволяет малым предприятиям осуществить их полную загрузку, либо очень высокую стоимость, что не дает возможности предпринимателям или частным подворьям быстро окупить свои данное оборудование. Предлагаем вниманию читателей описание технологии изготовления небольшого гранулятора своими руками для производства пеллет в домашних условиях, себестоимость которого значительно меньше многих промышленных аналогов.
Принцип работы гранулятора
По принципу работы все аппараты для производства гранул из отрубей или древесных пеллет делятся на две группы – с плоской или с кольцеобразной матрицей. Предлагаемый вниманию механизм относится к первой группе. Он состоит из сварной основы, на которую монтируется привод в виде электродвигателя требуемой мощности и редуктора с установленным на нем рабочим узлом. Процесс изготовления потребует выполнения сварочных работ, а так же использования некоторых готовых деталей, подбираемых в зависимости от размеров рабочего узла.
Изготовление основания для самодельного гранулятора
Изготовление агрегата начинаем с основания. Предварительно подготовьте достаточное количество стального проката в виде швеллера или прямоугольного профиля сечением 25×40 миллиметров. С помощью болгарки (угловой шлифовальной машинки) или слесарной ножовки осуществите раскрой материала на отдельные детали в соответствие с фото.
Используя сварочный аппарат или так же газовую сварку соедините детали основания гранулятора в рамную конструкцию с соответствующими площадками для крепления электродвигателя и рабочего узла. В случае изготовления не стационарного, а мобильного устройства установите по углам нижней рамы колеса на болтовом или сварочном соединении.
Рабочий механизм гранулятора для пеллет
Рабочий узел, соединяемый с электродвигателем посредством цепной передачи, состоит из редуктора и цилиндрической емкости, в которой устанавливается дискообразная матрица и пара установленных на валу специальных шестерен.
Матрица представляет собой металлический диск, имеющий толщину не менее восьми миллиметров с просверленными в нем отверстиями. Диаметр отверстий равен диаметру пеллет и составляет восемь – десять миллиметров. Форма отверстий выполнена в виде усеченного конуса, что обеспечивает постепенное обжимание гранулируемой смеси. Этот аспект значительно повышает плотность гранул, не зависимо от используемого сырья. В центре диск имеет отверстие с пазом для крепления на вращающемся выходном валу редуктора с помощью шпонки и крепящейся на болтах муфты.
Корпус рабочего узла состоит из двух полых цилиндров, имеющих прямоугольные прорези для установки пары червячных колёс, обеспечивающих при работе агрегата необходимое давление на гранулируемую массу.
В нижнем цилиндре корпуса имеется выходное отверстие для удаления готовых гранул (пеллет) в какую-либо приемную емкость. Принцип работы готового механизма основан на вращении диска-матрицы синхронно с установленными на валу шестернями. Вращение матрицы обеспечивается приводом редуктора от электродвигателя и жестким креплением рабочего диска. Попадающая через загрузочную верхнюю часть корпуса рабочего узла масса продавливается через отверстия, при этом сжимается и уплотняется, образуя достаточно твердые цилиндры небольшой длины. В зависимости от обрабатываемого сырья масса может дополнительно увлажняться в тех или иных пропорциях.
Описанный в данной статье гранулятор, сделанный своими руками, не требует больших расходов для изготовления и вполне может быть использован для работы небольшими деревообрабатывающими производствами, а так же животноводческими или зерновыми.
В данном видео продемонстрирована работа самодельного гранулятора:
youtube.com/embed/Wp7Y_VfowKg?rel=0″ allowfullscreen=»» frameborder=»0″>
Уважаемые читатели, комментируйте статью, задавайте вопросы, подписывайтесь на новые публикации — нам интересно ваше мнение 🙂
Статьи, которые Вам будут интересны:
основные виды и параметры, матрицы General Dies и Graf
Если вы ищете, где купить матрицу для гранулятора, вы можете приобрести ее в нашей компании по выгодным ценам. Мы поставляем матрицы Graf и General Dies с широким рядом типоразмеров, а также другие запасные части — пресс-вальцы, обечайки и.т.д.Основные характеристики матриц
Матрицу изготавливают из сверхтвердого металла или металлосплава, который может выдержать постоянные нагрузки.
Материалы изготовления :
-
20CrMnTi. Данный сплав стали характеризуется высоким содержанием хрома, увеличивающий коррозионную стойкость, и марганца, уплотняющего сталь.
-
Нержавеющая сталь – легированная сталь, устойчивая к коррозии в агрессивной среде.
-
Высокоуглеродистый сплав. Чаще всего используется для высокоабразивного сырья, с содержанием органо-минеральных примесей.
По виду матрицы делятся на кольцевые и плоские (дискообразные).
-
Грануляторы с плоской матрицей распространены в производстве комбикорма. Исключением для производства пеллет можно назвать грануляторы фирмы Amandus Kahl, которые способны прессовать плотные пеллеты из древесины.
-
Грануляторы с кольцевой матрицей бывают исключительно промышленного назначения. Они обладают повышенной производительностью и высоким качеством прессования. Такие модели, как пресс-гранулятор ОГМ, используются для гранулирования широкого круга материалов: начиная опилками и кормосмесями, заканчивая химическими удобрениями и торфом.
Под каждый вид сырья требуется собственная технология гранулирования. Так при производстве топливных пеллет стараются добиться максимальной плотности для высокой теплоотдачи и прочности. Матрица – один из ключевых моментов в технологии грануляции.
Основные параметры матрицы
-
Длина рабочего канала – это длина фильеры (отверстия, канала в матрице) по которому материал проходит прессование. Он может быть меньше общей длины фильеры в том случае, если ее рассверливают (зенькуют) изнутри или делают встречный канал снаружи диска/кольца для увеличения толщины матрицы.
-
Диаметр фильеры – это, по сути, диаметр будущих пеллет. На современных матрицах разброс диаметров – от 2 до 19 мм. Форма отверстий может быть круглой, квадратной и даже фигурной (например, в форме четырехлистника).
-
Толщина матрицы – то же самое, что и общая длина канала.
-
Степень сжатия – это степень давления фильеры на материал. Она рассчитывается как отношение рабочей длины канала к диаметру отверстия. Чем больше длина и меньше диаметр, тем выше степень сжатия. Для каждого вида материала используется своя степень сжатия.
Матрица пресс гранулятора в процессе гранулирования
Цель гранулирования – получение твердых гранул, которые устойчивы к деформации и крошению, а также сохраняют свойства изначального продукта.
Для достижения этой прочности производители соблюдают определенные пропорции между длиной гранулирования и диаметром отверстий. Чем больше в диаметре пеллеты, тем длиннее должен быть рабочий канал. Также ширина сечения фильер прямо влияет на производительность пресс-гранулятора. Чем уже каналы, тем меньше выход продукции. Если из-за малого диаметра фильер вход сырья осложнен, их раззеньковывают изнутри
Стандартный диаметр отверстий матрицы для пеллет – 6 или 8 мм, для комбикорма — от 2,5 до 10 мм.
Для обработки разных по свойству материалов и смесей выпускают матрицы с самой разной конфигурацией фильер. Суть различий формы каналов – в поиске оптимального пути гранулирования для заданного материала, при котором гранула будет плотно прессоваться, и после выхода наружу не разбухнет и не пойдет трещинами. Чем мягче и эластичнее продукт, тем выше вероятность разбухания гранул. Раскалывание пеллет по окружности показывает, что сырье нужно дольше выдерживать под давлением.
На процесс изготовления пеллет влияет такой фактор, как шлифовка внутренних отверстий. Чем более гладкие внутри фильеры, тем меньше они забиваются, и выше производительность пресса. Когда в смеси для гранулирования присутствует много абразивных частиц, отверстия теряют гладкость, некоторые из них забиваются материалом. Это создает дисбалансы в работе: повышается нагрузка на пресс, а выход гранул снижается. Производительность пресса зависит и от других параметров: давления пара, его температуры и т. д. Однако, матрица – дорогостоящая деталь. Поэтому владельцы обычно пытаются ее восстановить путем шлифовки — полировки внутренней поверхности фильер. Данная услуга продлевает срок эксплуатации старой детали при некритическом износе.
Когда приходит время замены, обычно меняют весь узел гранулирования вместе с пресс-вальцами (роликами), которые соприкасаются со внутренней поверхностью кольца и проталкивают массу в каналы. Если вальцы не заменять, новая матрица может быть повреждена изношенными обечайками роликов.
Матрицы General Dies
Компания General Dies (Дженерал Дайз) ведет производство в Италии, город Верона уже на протяжении 60 лет. Сегодня итальянские матрицы являются эталоном качества в отрасли и работают на грануляторах по всему миру. Материал изделия – хромированная сталь, цементированная сталь, сталь с индукционной закалкой.
Матрицы General Dies – это:
-
Высокий рабочий ресурс детали;
-
Максимально точное исполнение;
-
Настоящее европейское качество, признанное на мировом уровне.
Именно поэтому компания АЛБ Групп устанавливает эти детали на собственные грануляторы ОГМ. Также мы имеем запас данных расходных частей на складе для поставок партнерам, поэтому у нас можно купить матрицу General Dies из наличия. Также у нас всегда есть пресс-вальцы в комплект.
Узнайте прямо сейчас, есть ли у нас нужные вам модели, позвоните по телефону + 7 (831) 211-94-85 или заполните контактную форму, и мы перезвоним вам в течение 10 минут!
Матрицы Graf
Немецкий производитель Graf является одним из лидеров рынка по поставке кольцевых матриц для грануляторов ОГМ и не только.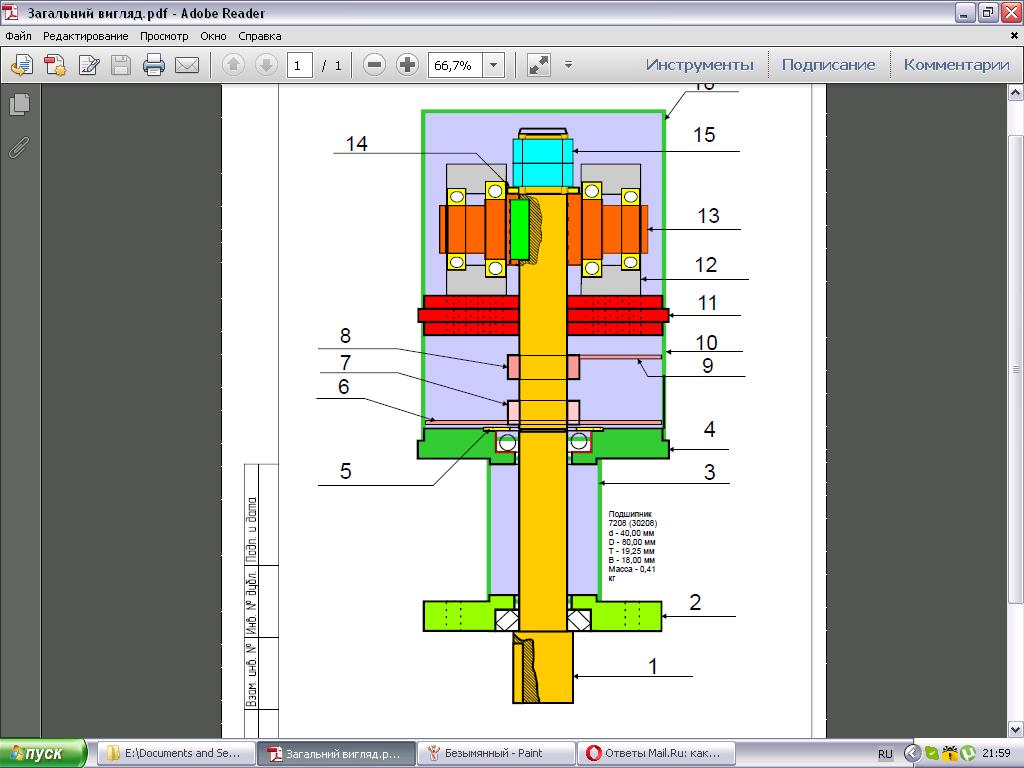
-
Традиционно высокое европейское качество;
-
Выпуск гранул высшего сорта при соблюдении технологий;
-
Быстрый запуск, снижающий себестоимость тонны гранул;
-
Высокий ресурс, выносливость;
-
Устойчивость к коррозии.
Компания АЛБ Групп использует продукцию Graf на своих грануляторах и рекомендует их к приобретению.
В нашей компании также можно купить матрицу Graf из налиичия, для этого нужно связаться с нами по телефону + 7 (831) 211-94-85 или заполнить форму заказа.
Гранулятор для комбикорма своими руками
Все больше владельцев частных птицеферм и животноводческих хозяйств задумываются о покупке или создании гранулятора. Это устройство экономит затраты на кормление, а также обеспечивает животных более сбалансированным кормом.
Гранулятор можно сделать своими руками из мясорубки — такая модель довольно проста в использовании и пригодная для небольших хозяйств и частных подворий.
Польза гранулятора
Рыночная цена на гранулированный комбикорм всегда выше, чем на рассыпной даже с аналогичным составом. Это объясняется тем, что гранулированный корм лучше храниться и легче транспортируется, не боится перепадов температуры, повышения влажности и может находится под прямыми солнечными лучами.
Гранулированный корм также позволяет снизить себестоимость содержания птиц и животных и удешевить статью расходов на кормление.
Корма, пропущенные через гранулятор, консервируются, что позволяет снизить угрозу попадания в пищу опасных бактерий. Животные и птицы получают сбалансированный корм и не имеют возможности выбрать только то, что им нравится, каждая гранула содержит сразу несколько компонентов. А витамины, стимулирующие вещества и микроэлементы, которые можно добавить к составу комбикорма, позволяют увеличить продуктивность фермы на 20 – 30 процентов.
Грануляторы для комбикорма можно купить в специализированном магазине, но все больше частных фермеров отдают предпочтение самодельным конструкциям. Производство гранулированного комбикорма также является неплохим бизнесом – излишек кормов можно продавать по рыночным ценам или же заниматься производством гранулированного корма по своему собственному рецепту.
Такой корм пользуется большим спросом, поскольку является более натуральным и чистым.
Гранулятор с матрицей, изготовленной самостоятельно
Гранулятор для комбикорма бытовой своими руками можно изготовить и с самодельной матрицей.
Для изготовления потребуется:
- Двигатель,
- Вал,
- Диск, толщиной примерно 2 см,
- Жестяные листы,
- Металлические углы,
- Болты для крепежа деталей,
- Сварочный аппарат,
- Линейка,
- Штангенциркуль,
- Набор гаечных ключей,
- Перфоратор и болгарка,
- Фломастеры,
- Редуктор,
- Металлический диск.
Изготовление матрицы
Для изготовления матрицы берется металлический диск, толщиной большей, чем 2 см. Чем больше площадь диска, тем выше производительность устройства.
В центре диска высверливаются отверстия с пазами. Для этого можно использовать дрель или токарный станок. Пазы обеспечат более плотную посадку матрицы. На матрице также просверливают конусовидные отверстия для выхода гранул.
Корпус устройства
Корпус устройства изготавливается из отрезка трубы или жестяного ведра без дна. В верхнюю часть насыпаются составляющие комбикорма. В нижнюю часть корпуса после прохождения через матрицу поступает уже спрессованный готовый корм. Диаметр корпуса должен быть больше диаметра матрицы для более свободного вращения. В нижней части корпуса проделывается квадратное отверстие и под него помещается лоток для сбора готового корма.
Сборка гранулятора
Редуктор крепится внизу конструкции при помощи подшипников или муфты. Две части корпуса свариваются между собой с помощью ушек и специальных болтов. Шестеренки и ролики матрицы монтируются в корпус. Раму корпуса изготавливают из уголков или швеллеров и устанавливают на гранулятор. Устройство крепится к станине. Последним устанавливается электродвигатель. После завершения работы гранулятор снаружи красится краской для металла для предотвращения ржавления.
Гранулятор комбикорма бытовой своими руками изготовленный по данной схеме функционирует за счет вращения матрицы. Вращение обеспечивается прочным креплением и приводом редуктора.
Гранулятор из мясорубки
Инструкция по изготовлению
Изготовление гранулятора комбикорма своими руками начинается с чертежей конструкции. Сделанные своими руками чертежи позволят не только сэкономить время, но и понять принцип работы гранулятора. Для примера можно использовать:
Как сделать гранулятор:
Гранулятор для комбикорма своими руками из мясорубки – одна из простейших моделей. Свой собственный небольшой гранулятор хорошо иметь даже частным подворьям с небольшим поголовьем скота и птицы. Это сэкономит затраты на корма и сделает кормление более сбалансированным и полезным.
Чтобы сделать гранулятор, понадобятся:
- Устойчивая ровная поверхность,
- Механическая мясорубка,
- Токарный станок,
- Сверла,
- Два шкива, для снижения оборотов двигателя и увеличения мощности,
- Тонкая болванка для изготовления матрицы. Рекомендуемая толщина не более семи сантиметров,
- Ремень,
- Электродвигатель. Можно использовать двигатели от бытовых приборов.
Работа начинается с крепления ножей мясорубки к столу. Для этого в ножах проделываются отверстия и закрепляются болтами. Матрица — плотный диск с отверстиями, она изготавливается того же диаметра, что и решетка мясорубки. Для более плотного примыкания матрицы можно сточить ребра. Крышку делают с небольшим допуском на случай, если понадобится более толстая матрица. На крышке нарезаются канавки или привариваются кусочки проволоки для более легкого прикручивания. С наружной стороны матрицы крепятся ножи для нарезки готовых гранул. Последними монтируются два шкива, двигатель и ремень. Ремень натягивается не слишком прочно, чтобы уберечь двигатель от перегрева и сгорания. Устройство готово к работе.
как сделать своими руками, принцип работы устройства
В удаленных загородных поселках газа обычно нет. И жители самостоятельно решают проблему отопления и горячего водоснабжения. Для этого требуется источник энергии. И газ в этом плане – самый дешевый вариант. Его отсутствие толкает людей на использование других видов энергоносителей. Один из современных – пеллеты, изготовленные из отходов древесины или сельскохозяйственной продукции.
Содержание статьи
Что такое гранулятор
Гранулятор для пеллет, он же пеллетайзер, – станок, с помощью которого изготавливают пеллеты. Принцип его работы очень похож на мясорубку. Только вместо шнека в нем используются тяжелые ролики, с помощью которых древесная мука проталкивается через матрицу. Матрица – это стальной блин со сквозными отверстиями. В мясорубке ее называют сеточкой.
Какое оборудование нужно для производства пеллет
Сегодня производители предлагают две разновидности пеллетайзеров:
- Матрица в виде блина, расположенная горизонтально на дне станка. По ней прокатывается два или три ролика, выдавливающие пеллеты вниз.
- Матрица изготовлена в виде кольца определенной шириной, и установлена вертикально. Ролики вращаются в вертикальной плоскости. Пеллеты выталкиваются во всей длине матрицы.
Из какого сырья производят пеллеты
Нет особых ограничений в использовании сырьевого материала для изготовления пеллет. Главное – они должны быть природного происхождения, плюс – горючими.
Но к сырьевому материалу есть свои требования:
- Зольность. Это несгораемые остатки, которые остаются после сжигания топлива.
У пеллет этот показатель не должен превышать 3%.
- Влажность – 8-15%.
- Минимальное количество химических компонентов, таких как сера, хлор, азот и прочее.
- Свежесть материала, потому что старое сырье теряет свою энергетическую ценность.
- Возможность его гранулировать. Не все природные горючие материалы имеют невысокую прочность. А чем прочнее сырье, тем слабее пеллеты в плане твердости. Потому что их сложнее прессовать.
Переработка опилок, жмыха, шелухи, кожуры семян
К сожалению, отходы агропромышленного комплекса соответствуют не всем параметрам. У них высокая зольность, невысокая энергетическая ценность, плюс – большое содержание химических элементов. Единственный плюс, который перебивает недостатки, минимальная цена. Это снижает себестоимость пеллет.
Гранулированное топливо из сельскохозяйственных растительных отходов обладают достаточно неплохой энергетической ценностью – до 5 кВт/кг. Но у них по сравнению с древесиной повышенная зольность – 1,5-3%. Поэтому пеллеты из такого сырья относятся к третьему сорту. Отсюда и невысокая цена.
Изготовление пеллет из древесины, сены и соломы
Пеллеты из древесины без коры – первый сорт. Зольность такого топлива не превышает 0,5%, тепловая мощность – 5,4 кВт/кг. Это самый дорогой вариант.
Древесина с корой относится ко второму сорту. Сюда же можно причислить пеллеты из соломы и сена. Здесь зольность – 1-1,5%, мощность сгорания 5,2 кВт/кг.
Технология изготовления пеллет из древесины
Способ изготовления прост. Включает несколько технологических операций:
- Сортировка древесины по размерам: на опилки и стружку, а также на щепу, ветки и горбыль.
- Дробление крупных элементов.
- Дробление мелких элементов до получения размеров длины до 4 мм, толщины до 1,5 мм.
- Сушка. На выходе влажность не должна превышать 12%.
- Грануляция. Здесь и используется гранулятор опилок.
- Вторичная сушка готового материала.
В процессе прессования из древесины выделяется лигнин. Это природное полимерное соединение, которое содержится в клетках растений. Именно он и связывает между собой частички древесины, то есть склеивает их.
Принцип работы гранулятора для пеллет
Принцип работы основан на выпрессовке сырьевого материала сквозь матрицу. Поэтому пеллетайзер представляет собой пресс, в котором основная деталь – матрица. Она должна быть прочной, выдерживать большие нагрузки. Поэтому ее изготавливают из стали.
Сам процесс происходит в следующей последовательности:
- измельченное сырье попадает в станок;
- заполняет пространство;
- вращающиеся ролики большой массы вдавливают его в отверстия матрицы;
- здесь происходит резкое уменьшение объема опилок и увеличение их плотности, в результате чего из древесины выделяется лигнин;
- формируются гранулы, проходящие сквозь матрицу, падая в бункер сбора готового изделия.
Некоторые виды станков комплектуются ножами, которые режут выдавливаемые гранулы под необходимую длину. Гранулятор можно автоматизировать, если установить до и после него систему подачи сырья и отвода готовой продукции. Для этого используют конвейеры: ленточный или шнековый.
Как сделать гранулятор для пеллет своими руками
Грануляторы для пеллет своими руками многие умельцы изготавливают без проблем. Но собирается он не из расходного бросового материала. Матрицу, ролики и другие элементы конструкции придется или заказывать для изготовления, или покупать готовые.
Просто в самом начале надо выбрать тип конструкции станка. То есть это или подвижная матрица и неподвижные ролики, или наоборот: матрица статична, валки двигаются. Оба варианта требуют инженерного подхода. И здесь нельзя сказать, какое из предложений проще и дешевле. Но оба варианта работают эффективно.
Кроме выше обозначенных деталей потребуется электродвигатель, редуктор, два шкива разного диаметра и ремень клиновой.
Тип редуктора выбирается с учетом того, в какой плоскости будет располагаться ведомый вал: горизонтально или вертикально. Если вертикально, то электродвигатель и редуктор собираются на раме в последовательном порядке. То есть один за другим. При этом их валы располагаются в одном направлении. И соединяются эти два элемента вертикально и напрямую без промежуточных деталей. В данном случае без шкивов и ремня.
Такую же конструкцию можно использовать, установив мотор и редуктор горизонтально. Но в таком случае надо выбрать последний с двумя выходящими из него валами, расположенными перпендикулярно друг другу.
Третий вариант – с использованием промежуточных деталей. Здесь двигатель и редуктор устанавливаются на раме рядом друг с другом вертикально. Передача вращения производится посредством ремня и шкивов. Последние можно заменить звездочками, то есть создать цепную передачу. Этот вариант удобен тем, что если грамотно рассчитать передаточное число промежуточных элементов, можно не устанавливать редуктор.
Внимание! Оптимальное передаточное число равно «6». Не меньше.
В качестве редуктора подойдет задний мост от автомобиля. Чем последний больше, тем мощнее устройство передачи оборотов от электродвигателя.
Теперь о матрице и роликах. Своими руками их не сделать. Придется обращаться к токарю. Или приобретать готовые детали. Чем толще матрица, тем она прочнее, будет выдерживать большие нагрузки и дольше прослужит. Оно дорогое, плюс – большой вес.
Ролики должны быть по ширине такими, чтобы они помещались на поверхности матрицы, свободно перемещаясь по ней. Для них подбирается поперечина, которая соединяется с валом редуктора. Она должна быть прочной, потому что основные нагрузки ложатся именно на нее.
Последний элемент гранулятора – корпус. Самый простой вариант – труба с толстой стенкой. Ее внутренний диаметр и будет внешним диаметром матрицы. То есть заказывать у токаря надо будет с указанием этого размера. То же самое касается валиков.
Собрать грануляторы для опилок своими руками можно, учитывая не сложность конструкции, а стоимость деталей и узлов. И если какие-то можно найти на свалке, то такие как матрица, придется покупать дорого. Но в любом случае это обойдется дешевле, чем заводской станок. Правда, гарантии надежности и качества здесь никто не даст.
Гранулирование — обзор | ScienceDirect Topics
4.2.5.2.1 Гранулирование
Гранулирование является наиболее широко используемым процессом для измельчения многих термопластичных материалов, включая сырые полимеры и смешанные соединения. Процесс включает экструзию через головку. Экструдат охлаждают до затвердевания и затем разрезают на гранулы, или расплавленный экструдат разрезают, когда он выходит из экструзионной головки, и затем гранулы охлаждают. В последнем случае и резка, и охлаждение могут производиться на воздухе или в воде, либо резка может производиться на воздухе с последующей закалкой в воде [45].Резка термопластов в виде расплава, а не в виде твердого вещества, приводит к меньшему количеству мелких частиц и меньшему износу ножей [46].
Устройство для гранулирования, которое превращает продукт в гранулы различных форм и размеров, часто присоединяется к экструдеру или шестеренчатому насосу. Форма гранул предлагает несколько технологических преимуществ по сравнению с другими формами. Его можно легко взвесить, в нем используются простые системы кормления с меньшим количеством кормушек, и он позволяет получать однородный и однородный сыпучий корм для последующего конечного использования.
Вязкость продукта, тепловая история, однородность, требуемая производительность и другие факторы обычно определяют метод резки, который можно успешно использовать.Ниже приведены наиболее широко используемые машины для гранулирования термопластов.
Стренговые грануляторы были наиболее широко используемым оборудованием для гранулирования термопластичных полимеров и компаундов [47] в прошлом, но в настоящее время наблюдается тенденция к использованию подводных машин. Нити, выходящие из головки экструдера или шестеренчатого насоса, проходят через ванну с охлаждающей водой с желобчатыми роликами, которые удерживают их отдельно до тех пор, пока они не затвердеют. Затем они сушатся на воздухе и в прижимных валках подаются на многоножевой ротор, работающий против неподвижных лопастей. Поперечное сечение гранул может быть круглым, овальным или почти квадратным [48], с типичным диаметром 2–4 мм (0,08–0,16 дюйма) и длиной 1–5 мм (0,04–0,2 дюйма). Существует несколько методов охлаждения и сушки пеллет; они обсуждаются более подробно в Ref. [49]. Принципиальная схема стренгового гранулятора представлена на рис. 4.20.
Рисунок 4.20. Схематический чертеж ручьевого гранулятора.
Предоставлено Rieter-AutomatikГрануляторы с матрицей производят гранулы с помощью ножей, быстро вращающихся на матрице с множеством отверстий.Закалку окатышей проводят только на воздухе водяным туманом или последующим погружением в водяную баню [50]. Принципиальная схема гранулятора с горячей головкой представлена на рис. 4.21.
Рисунок 4.21. Принципиальная схема гранулятора с горячей головкой. (А) расплав полимера; (Б) Роторный нож; (C) Разгрузочный желоб.
Эксцентриковые грануляторы для сухой резки имеют эксцентрично установленный резак с несколькими рычагами, вращающимися со скоростью до 2500 об/мин.
Подводные грануляторы , вероятно, являются наиболее универсальным оборудованием для широкого диапазона вязкости, более высокой производительности и размеров гранул.Они работают с торцевой матрицей и вращающимся резцом, полностью погруженными в воду. Полученные окатыши уносятся в виде взвеси в воде для дальнейшего охлаждения в пути к оборудованию для обезвоживания, сортировки и сушки [51]. Пример подводной головки для гранулирования показан на рис. 4 22(A), а детали режущих ножей показаны на рис. 4.22 (B).
Рисунок 4.22. (A) Схематический рисунок подводной грануляторной головки. а) водяная камера; б) гранулы; с) держатель ножа; (г) матрица пластины; (e) Шнек подачи экструдера.(B) Деталь режущей головки подводного гранулятора.
Предоставлено: Помини; Davis-Standard LLC, Black Clawson Converting Machinery В грануляторе с водяным кольцом расплавленные нити, выходящие из головки, разрезаются установленным в центре резаком. Свеженарезанные гранулы бросают в спирально вращающуюся воду на глубину около 20 мм (0,8 дюйма). Гранулы охлаждают в воде, затем просеивают и сушат. Схема этого типа гранулятора представлена на рис. 4.23(А), а пример расположения фильерных ножей в таком устройстве – на рис.4.23(В).
Рисунок 4.23. (A) Схематический рисунок гранулятора с водяным кольцом. а) водокольцевая камера; б) гранулы; с) держатель ножа; (г) матрица пластины; e) подающий шнек экструдера; (е) Двигатель. (B) Деталь режущей головки гранулятора с водяным кольцом. (C) Типичная схема системы гранулирования термопластичных эластомеров.
Предоставлено: Помини; Экструзия Ксалой; Davis-Standard LLC, Black Clawson Converting Machinery В центробежных грануляторах расплав подается во вращающуюся головную камеру при атмосферном давлении.Давление для выдавливания полимера через отверстия матрицы создается центробежной силой внутри головки, а не экструдером или шестеренчатым насосом. Появляющиеся пряди срезаются одним стационарным ножом [51]. Этот тип машин когда-то предлагался, но больше не производится.
Грануляторы с вращающимся ножом работают с головкой, аналогичной головке для стренги, но с вращающимся ножом, работающим в непосредственной близости от формирующихся прядей. Резак полностью закрыт [52].
Термопластичные эластомеры можно перерабатывать практически на любой из этих машин; выбор зависит главным образом от кажущейся вязкости расплава данного материала. Схема типичной системы гранулирования большинства термопластичных эластомеров представлена на рис. 4.23(C).
Малый завод по производству древесных гранул, чертежи самодельного завода по производству пеллет
Бытовой гранулятор также называют небольшим гранулятором, самодельным гранулятором, домашним гранулятором, самодельным гранулятором или прессом для гранул для домашнего использования.Небольшой гранулятор GEMCO для продажи спроектирован с плоской матрицей. Ряд роликов находится над горизонтальной матрицей гранулятора, которая называется плоской матрицей. При изготовлении гранул матрица неподвижна, в то время как ролики вращаются для сжатия порошков сырья в небольшие отверстия в плоской матрице для формирования гранул. А серия ножей с другой стороны плоской матрицы сразу же нарежет образовавшиеся гранулы на одинаковую длину. Бытовой гранулятор обычно используется для мелкосерийного производства древесины или кормовых гранул, как правило, дома или на ферме для индивидуального использования.
Бытовой гранулятор обладает очевидными преимуществами, такими как: небольшой размер, легкий вес, компактная конструкция, легкая мобильность, низкий уровень шума и низкое энергопотребление.
Пресс-гранулятор GEMCO для домашнего использования может производить гранулы биомассы из широкого спектра сырья, такого как: опилки, рисовая шелуха, древесная стружка, сосновая древесина, растительные остатки, такие как пшеничная солома, рисовая солома и стебли кукурузы, трава, такая как мискантус и тростник. , просо, люцерна, EFB (пустые фруктовые бранчи), бамбук, багасса, скорлупа арахиса, опавшие листья и ветки деревьев и т. д.
Более того, эти небольшие грануляторы также можно использовать для производства кормовых гранул из жмыха, агроостатков, таких как ростки арахиса, трава, солома кукурузы, солома пшеницы, зерно, пшеничные отруби и т. д., побочные продукты муки, злаки и патока, а также скоро.
Пеллеты из биомассы, производимые гранулятором с плоской матрицей GEMCO, в основном предназначены для индивидуального или домашнего использования, например, для отопления и сжигания или подстилки для лошадей. Пеллеты, изготовленные на небольшой мельнице, могут в полной мере использовать опавшие листья, отходы травы на вашем газоне, скорлупу от арахиса, макулатуру и т. д.Производство пеллет из биомассы в домашних условиях, безусловно, является беспроигрышной стратегией. Вы действительно можете превратить отходы в сокровища.
Небольшая грануляционная мельница GEMCO для домашнего использования может приводиться в действие 4 различными двигателями: электрическим двигателем, дизельным двигателем, бензиновым двигателем и ВОМ. Гранулятор GEMCO с плоской матрицей имеет большую производительность гранул (500-800 кг/ч для гранул из опилок). По сравнению с гранулятором с кольцевой матрицей, который обычно известен своей большой производительностью, этот гранулятор легче заменить матрицу и ролики, когда это необходимо.
Эти самодельные машины позволяют любому перерабатывать пластик в новые продукты
Большая часть из 300 миллионов тонн пластика, производимого каждый год, не перерабатывается, а переработка, которая происходит, обычно происходит в промышленных масштабах на заводах с использованием оборудования, которое может стоить десятки тысячи долларов. Но все большее число дизайнеров используют набор простых в сборке инструментов с открытым исходным кодом для переработки пластика и самостоятельного производства новых пластиковых изделий.
Посмотрите, как это работает:
«Мы хотим сделать мелкомасштабную переработку пластика доступной для всех, поскольку это может иметь экспоненциальный эффект на количество перерабатываемой пластмассы — в конечном итоге снижая спрос на новую первичную пластмассу — и обучать миллионы людей используют пластик, переработку пластика и способы обращения с ним до того, как он попадет в окружающую среду», — говорит Дэйв Хаккенс, голландский основатель Precious Plastic, организации, разработавшей машины, которые сейчас используются дизайнерами в Таиланде и Украина и более 200 других.
«Мы хотим сделать мелкую переработку пластика доступной для всех». [Фото: Precious Plastic] В одном наборе инструкций объясняется, как построить недорогую машину, которая измельчает пластик в хлопья. Другая модульная машина экструдирует пластик, который можно использовать для 3D-печати; машина для литья под давлением и машина для сжатия могут формовать пластик в формы. Серия видеороликов объясняет, как построить машины, используя основные материалы и универсальные детали.
Дизайнеры по всему миру начали использовать машины для производства изделий из переработанного пластика в 2016 году, и теперь организация делится новыми инструкциями по созданию мастерских по полной переработке внутри транспортных контейнеров.Они также создали новую карту, чтобы объединить людей в сообществе по переработке отходов DIY.
«Это может оказать экспоненциальное влияние на количество переработанного пластика, что в конечном итоге снизит спрос на новый первичный пластик». [Фото: Precious Plastic] «Карта предназначена для содействия местному сотрудничеству между людьми, чтобы помочь создать сотни дополнительных рабочих мест по переработке пластика по всему миру, а также предоставить людям совместный инструмент для совместной борьбы с пластиковыми отходами творческими способами — кампания за переход законы, бойкот предприятий, организация акций протеста или любые другие действия, направленные на прекращение загрязнения пластиком», — говорит Хаккенс.
Новый онлайн-рынок под названием Bazar продает товары, изготовленные с помощью машин, в попытке помочь большему количеству людей начать зарабатывать на жизнь переработкой пластика.
Хотя Хаккенс говорит, что команда заинтересована в создании инструментов для переработки и использования других материалов, пластик является их приоритетом. «Пластик — одна из самых насущных проблем, стоящих перед планетой, — говорит он. «Я думаю, что это будет нашим приоритетом на многие годы вперед».
Самодельный гранулятор, Создайте свой собственный гранулятор
С ростом знаний людей об охране окружающей среды и энергосбережении растет и потребность в древесных гранулах для отопления дома.Это пеллетное топливо не только является источником возобновляемой энергии, но и может удовлетворить многие современные требования к возобновляемым источникам энергии. А делать пеллеты в домашних условиях очень здорово!
Здесь я хотел бы показать некоторые основные процедуры гранулирования на самодельной грануляторной мельнице , основной процесс относится к следующим словам:
Прежде всего, вам нужна машина для производства древесных гранул. После этого, используя правильные материалы и правильные инструкции, которые вы можете узнать из руководства по эксплуатации или другими способами, вы, естественно, получите свои собственные пеллеты прямо у себя дома.
1. Дробление
Прежде всего, с помощью дробильной машины измельчают сырье прямо на мелкие предметы, затем все эти предметы при необходимости следует измельчать в древесный порошок молотковыми мельницами.
2. Сушка
Что касается гранулирования, то для правильной работы самодельных грануляторов требуется максимальное содержание влаги в материалах. По этой причине сушка сырья до нужного уровня влажности перед помещением его в машину является отличным выбором.Как правило, 13-15% — это максимальное содержание влаги для этой машины.
3. Гранулирование
После сушки до идеального содержания влаги материал следует поместить в мельницы для гранулирования. Существует много таких машин, в том числе дизельные, небольшие грануляторы, грануляторы с кольцевой и плоской матрицей и т. д. Вы можете выбрать любой из них в зависимости от ваших потребностей в самодельной грануляторной мельнице.
4. Охлаждение
На этом этапе температура гранул составляет около 60-80 градусов, а содержание влаги около 15%.В таких случаях содержание влаги необходимо уменьшить на 3-4%, используя охладители для целей хранения.
5.Упаковка
Если ваши гранулы не предназначены для непосредственного употребления в пищу или вы просто хотите хранить их некоторое время, процесс упаковки в пакеты необходим, поскольку он может предотвратить отсыревание гранул.
Создайте свой собственный гранулятор , грануляторы для домашнего использования
Самодельный гранулятор | С дизельным двигателем | С электродвигателем |
Плоская матрица гранулятора | Матрицы и ролики грануляторов | Электрический шкаф управления |
Производственный процесс | Готовые пеллеты | Сжигание Древесные пеллеты |
Домашний гранулятор ВОМ
Коробка отбора мощности (ВОМ) представляет собой шлицевой карданный вал, обычно на тракторе или грузовике, который может использоваться для подачи мощности на навесное оборудование или отдельную машину. ВОМ для домашнего гранулятора спроектирован таким образом, чтобы его можно было легко подключать и отключать. Коробка отбора мощности (ВОМ) позволяет навесному оборудованию получать энергию от двигателя трактора
Узнайте больше об этом Пресс-гранулятор с плоской матрицей
Как использовать дисковый гранулятор
В мире оборудования для перемешивания и агломерации дисковый гранулятор (иногда также называемый тарельчатым гранулятором) часто выбирают за его способность создавать очищенный продукт.Он широко используется для обработки всего: от химических порошков, летучей золы и почвенных добавок до минералов и руд, удобрений и многого другого.
Часть того, что делает дисковые грануляторы настолько успешными, заключается в том, что они позволяют операторам регулировать несколько переменных во время производства, чтобы точно настроить размер и качество продукта, будь то реакция на изменения в сырье или внесение корректировок в характеристики продукта. сброс с диска.
Этот высокий уровень гибкости привел к некоторой путанице в отношении того, как работают эти машины.Далее следует объяснение того, как использовать дисковый гранулятор.
Конструкция дискового гранулятора
Механическая конструкция дискового гранулятора
На изображении выше показана механическая конструкция дискового гранулятора. Устройство состоит из вращающегося диска, расположенного на неподвижном стальном основании. Распылительная система установлена над дисковым гранулятором для распределения связующего и жидких добавок. Плуги или скребки помогают направлять самоклассифицирующиеся потоки гранул при вращении диска.
Приподнятая рама вокруг вращающегося диска служит разгрузочным желобом. Более подробный обзор конструкции и компонентов дискового гранулятора см. в нашей статье «Анатомия гранулятора ».
Основы дискового гранулятора Дисковые грануляторы представляют собой устройство для агломерации с перемешиванием или перемешиванием, что означает, что они полагаются на жидкое связующее и движение для формирования и измельчения агломератов. Дисковый гранулятор можно использовать отдельно или в сочетании со смесителем, чаще всего со штифтовым смесителем.
Материал непрерывно подается на диск/лоток, где он захватывается вращением. Распылительная система, установленная поверх диска, имеет несколько подвижных распылительных форсунок (количество которых определяется на этапе проектирования), которые распыляют связующее вещество на материал, делая его липким.
Эта липкость и непрерывное прохождение материала через поток сырья при вращении диска приводит к агрегации частиц. По мере того, как агрегированные частицы продолжают вращаться вокруг диска, они захватывают дополнительные слои в модели роста, известной как коалесценция.При этом гранулы становятся более плотными и мелкими, так как промежутки, или промежутки между собравшимися частицами, заполняются более мелкими частицами, а промежутки между ними – еще более мелкими частицами и т.д.
Когда перед дисковым гранулятором стоит смеситель, действие такое же, но вместо этого в гранулятор подаются «зародышевые гранулы» или исходные ядра, на которые добавляются дополнительные слои мелочи.
Из-за центробежной силы на диске гранулы самоклассифицируются на потоки в зависимости от их размера; маленькие гранулы семян попадают на правую сторону диска и по мере роста продвигаются влево, откуда они в конечном итоге выбрасываются, когда достигают желаемого размера (см. диаграмму ниже).
Как работать с дисковым гранулятором Работа дискового гранулятора
сравнивается с сочетанием науки и искусства. В процессе производства операторы могут использовать несколько переменных для управления образованием и ростом гранул на диске, а также характеристиками продукта. Процесс эксплуатации дискового гранулятора включает в себя внимание к условиям предшествующей обработки и знание того, как взаимодействуют различные переменные, влияющие на продукт, выходящий из диска.По этой причине обучение операторов дискового гранулятора имеет важное значение.
Переменные дискового гранулятора
Операторы могут использовать следующие переменные в сочетании друг с другом для управления характеристиками продукта и реагирования на изменения в производстве.
Скорость диска
Скорость диска означает число оборотов в минуту или скорость, с которой вращается диск. Скорость регулируется с помощью частотно-регулируемого привода (VFD), который дает операторам больший контроль над регулировкой скорости во время запуска и остановки или во время колебаний.Скорость является наименее важной переменной и используется только вместе с регулировкой угла для получения оптимального покрытия материала гранулятора (когда система распыления выключена, материал должен покрывать весь поддон).
Угловой диск
Угол наклона рештака регулируется ручным домкратным винтом. До некоторой степени регулировки угла и скорости дополняют друг друга. Чем круче угол панорамирования, тем выше требуемая скорость.
Более высокий угол приведет к меньшему времени пребывания на сковороде, что приведет к более мелким гранулам, а меньший угол приведет к большему времени удерживания на сковороде, что приведет к более крупным гранулам, потому что у пеллет больше времени, чтобы пройти вокруг сковороды и собраться. больше частиц.
Скорость подачи и положение
Скорость подачи и положение также регулируются. Однако, чтобы сохранить размер и качество продукта, скорость подачи в лоток должна быть постоянной. Любое нарушение подачи приведет к нарушению продукта.
Скорость и место распыления связующего
Скорость распыления связующего, а также расположение распылителей связующего также регулируются. Операторы могут использовать скорость и место распыления вяжущего, чтобы реагировать на изменения в корме и стимулировать гранулы большего или меньшего размера.
Расположение плуга/скребка
Когда жидкость распыляется на диск и смешивается с подачей порошка, на дне и боковой стенке чаши могут начать образовываться отложения. Это накопление необходимо удалить, иначе процесс не будет работать правильно. Плуги или скребки удаляют эти отложения и создают гладкую поверхность. Как уже упоминалось, они также помогают направлять гранулы в отдельные потоки, поскольку они самоклассифицируются.
Заключение
Гранулятор — невероятно полезный инструмент в области агломерации.Возможность корректировки и настройки позволяет выполнять тонкую настройку и настройку, что может привести к получению продукта чрезвычайно высокого качества.
FEECO является лидером в агломерационной отрасли с 1951 года, производя дисковые грануляторы на заказ для широкого спектра материалов. Мы предлагаем уникальную испытательную установку, где мы можем проверить возможность гранулирования вашего материала как в серийном, так и в пилотном масштабе. Для получения дополнительной информации свяжитесь с нами сегодня!
Как сделать пробки хмеля или гранулы хмеля | Homebrew Talk
Небольшая тема про зомби, но она всплывает в сезон, когда люди начинают об этом думать.PelletComp, вы правы, но это не только это. Мы узнали гораздо больше с тех пор, как этот пост появился 2 года назад.
Грануляторы с плоской матрицей… китайского или другого производства… не работают. Масла и другие липкие вещества в хмеле очень быстро забивают их. Чтобы они продолжали работать, скорость подачи должна быть снижена НАМНОГО. Итак, вы говорите об очень дорогом грануляторе с кольцевой матрицей.
Использование стандартного кольцевого штампа также не работает. Нам потребовалось много экспериментов, чтобы получить правильные характеристики отверстия.
НЕЛЬЗЯ сжимать их при сильном нагревании, например, дерево или сельскохозяйственную пищу. В хмеле нет лигнина. Они держатся вместе благодаря собственной липкости. Высокая температура разрушает альфа-кислоты, выпаривает масла и превращает гранулы в восковые мелки. Что я имею в виду под высокой температурой? Все, что выше 100F.
Так как же нам этого добиться? Мы используем жидкий азот, чтобы держать кристалл около -40F. Это дает нам довольно хорошую пеллету, которая не показывает никаких признаков деградации по сравнению с исходным конусом. Любой, кто использует «холодный воздух» либо в штампе, либо охлаждает его сразу после выхода из штампа, пострадает. Если вы не нагнетаете огромное количество воздуха -50F в кристалл, у вас не будет такой же охлаждающей способности. Точно так же быстрое охлаждение пеллет после сжатия не принесет вам пользы. Все повреждения готовы.
Другим преимуществом использования азота является то, что мы можем обеспечить газовую подушку над молотковой мельницей, конвейером, гранулятором, следующим конвейером и затем упаковкой. Это означает, что с того момента, как мы разобьем конус, он будет защищен от кислорода. Это немного анальный ретеншн? Ну, наш химик так не думает.
Вы также правы насчет переменной скорости. У нас есть VFD на всем, так как мы обнаружили, что скорость даже гранулятора должна варьироваться в зависимости от типа и размера конуса.
Это была попытка сделать все правильно… но интересно.
О, чуть не забыл упомянуть. Как только мы наладили этот процесс, штат Висконсин изменил правила, и мы подверглись проверке Министерства сельского хозяйства США и критериям GMP. Поэтому нам пришлось перенести всю операцию на объект, который мы могли бы промывать, модернизировать все до нержавеющей стали или пищевых продуктов, настроить отслеживание запасов и тысячу других вещей. Мы близки к получению гранта Министерства сельского хозяйства США, чтобы мы могли записать часть этой информации для «мелкомасштабных» переработчиков хмеля и распространить ее. Поэтому, если вы думаете о продаже своего хмеля, проверьте, требуется ли в вашем штате лицензия, иначе у вас могут быть большие проблемы. Я знаю, что Висконсин и Нью-Йорк недавно добавили требования, как и другие штаты, которые ускользнули от меня.
Решение общих проблем при подводном гранулировании
Компаундеры сегодня сталкиваются со многими проблемами. Поддержание стабильного качества продукции имеет решающее значение для успеха.Одной из наиболее распространенных проблем при подводном гранулировании является неоднородность гранул. Несоответствие гранул может быть вызвано неправильным выбором или размером матрицы или колебаниями производительности.
В этой статье мы рассмотрим несколько проблем, которые способствуют несогласованности гранул, и предложим пути их решения.
НЕПРАВИЛЬНЫЙ РАЗМЕР МАТРИЦЫ
В большинстве случаев подводного гранулирования неправильный размер головки может привести к плохой однородности потока полимера по поперечному сечению отверстия головки и фактическому затвердеванию полимера в отверстии головки (иногда называемому замерзанием).Чтобы предотвратить замерзание матрицы, необходимо поддерживать минимальную скорость полимера через экструзионное отверстие и правильную температуру матрицы.
В большинстве случаев рекомендуется скорость от 2,5 до 3 фут/сек через отверстие матрицы, чтобы предотвратить затвердевание экструдата в отверстии. Чтобы поддерживать правильную скорость на отверстие, вы должны иметь правильное количество отверстий в матричной пластине для желаемой производительности.
Давайте рассмотрим размер штампа с диаметром отверстия 0,125 дюйма (3,2 мм). Для достижения рекомендуемой скорости вам потребуется от 50 до 60 фунтов/час на отверстие матрицы (V=0. 0002122/R2 x скорость за отверстие в фунтах/час). Имейте в виду, что это основано на материале с удельным весом 1. Во многих случаях, когда имеется значительное количество наполнителя или пигментов, материал будет иметь гораздо более высокий удельный вес. Это необходимо учитывать при выборе размера штампа.
Например, если материал имеет удельный вес 1,8, вам потребуется 1,8-кратная производительность от 50 до 60 фунтов/час на отверстие в штампе. Это может быть очень обманчиво. Вы можете подумать, что необходимо добавить больше отверстий в матрицу, чтобы уменьшить падение давления на ней, когда на самом деле требуется меньше отверстий, чтобы все они оставались «открытыми» во время работы.Существует расчет, чтобы определить, открыты ли все отверстия матрицы во время работы. Это так:
X = R × 7,6 /(Ш × Ш × Н), где:
X = количество открытых отверстий
R = производительность в фунтах/ч
W = вес в граммах на гранулу
S = скорость гранулятора в об/мин
N = количество лезвий на ступице фрезы
Вообще говоря, скорость полимера, в дополнение к теплу, которое он выделяет на матрице, должна регулироваться должным образом, чтобы обеспечить чисто разрезанную гранулу. Без такого контроля или понимания немногие технологические настройки или инженерные устройства могут обеспечить полное решение определенных технологических проблем, вызывающих несогласованность гранул.
НЕПРАВИЛЬНАЯ ТЕМПЕРАТУРА МАТРИЦЫ
Это также может способствовать замораживанию кристаллов. В большинстве случаев температура головки должна быть на 25°F выше, чем температура расплава полимера. Это может немного отличаться от продукта к продукту, но это хорошая отправная точка. На температуру кристалла также может влиять изоляция.Большинство штампов в той или иной форме изолированы. Это необходимо, чтобы изолировать все, кроме режущей поверхности, от контакта с технологической водой, чтобы предотвратить потерю тепла штампом.
Эта изоляция обычно герметизируется высокотемпературным силиконом, вулканизирующимся при комнатной температуре (RTV), и вам необходимо знать номинальные температуры. Герметик разлагается со временем и при повышенных температурах, что позволяет воде просачиваться в изоляцию и снижать температуру штампа. Например, предположим, что температура кристалла значительно падает по сравнению с заданным значением при запуске, и система управления запрашивает нагрев, но кристалл с трудом или никогда не возвращается к исходному заданному значению нагрева штампа.Это очень хороший признак того, что изоляция матричной пластины ухудшилась, отсутствует или неправильно установлена.
Проверьте количество энергии, потребляемой кристаллом. Многие системы управления оснащены амперметром в каждой зоне нагрева штампа. Рассчитайте потребляемый ток, необходимый для каждой зоны нагрева, затем сравните с фактическими показаниями. Если показание меньше оптимального, вероятно, один или несколько нагревателей вышли из строя.
БЛОКИРОВКА ОТВЕРСТИЯ
Неоднородные гранулы могут быть вызваны физической закупоркой отверстий матрицы загрязняющими веществами в материале или минеральными наполнителями, плохо диспергированными в матрице.В большинстве случаев желательна смена экрана или какой-либо тип фильтрации перед головкой. В небольших системах этот тип засорения можно удалить из отверстия матрицы с помощью специального инструмента для ручной очистки. В более крупных системах матрица обычно снимается для очистки. Также рекомендуется снижать температурные профили, в том числе в зоне нагрева штампа, при длительных периодах простоя.
До этого момента мы говорили о причинах и следствиях самого подводного гранулятора, но в процессе может быть несколько факторов, которые могут привести к несоответствию размеров гранул.Слипание сырья в бункере может уменьшить поток материала в экструдер. В зависимости от перерабатываемого продукта это может привести к получению неоднородных гранул или к замораживанию.
Неправильные настройки температуры экструдера могут вызвать пульсацию в экструдере, что приведет к изменению размеров гранул. Это также может привести к слишком высокой температуре расплава, что не обязательно приведет к несоответствию размера гранул, но может вызвать деформацию гранул.
МЕЛКА И ХВОСТИ НА ОКРУЖАЮЩИХ
Эта проблема может быть связана с рядом факторов; однако обычно это вызвано износом матрицы и/или лезвия. Если режущая поверхность штампа становится рифленой, даже новое и острое лезвие не сможет аккуратно разрезать полимер. В месте разреза небольшое количество материала протягивается через эту канавку, в результате чего на грануле образуется хвост. То же самое можно сказать и о лезвии с нарезами, работающем на новой поверхности штампа. Это подчеркивает важность выбора правильных и совместимых материалов для изготовления поверхности матрицы и лезвий. Использование слишком твердого лезвия может немного увеличить срок службы лезвия в краткосрочной перспективе, но может ускорить износ поверхности штампа.
Другими возможными причинами хвостов являются чрезмерная температура расплава, выравнивание матрицы вне допуска, проблемы механического износа подшипников гранулятора, приводящие к чрезмерному биению вала, или слишком горячая технологическая вода.
Следует также подчеркнуть, что без поддержания надлежащей скорости полимера через экструзионные отверстия экструзионной пластины в экструзионном отверстии экструзионной пластины существует преувеличенный градиент потока внутри отверстия экструзионной головки, вызывающий эффект рукава. Это создает нежелательное полимерное плечо, с которым лезвие будет бороться за чистый срез.
Когда гранулы проходят через центробежную сушилку, хвост отламывается, что приводит к образованию мелких частиц. Это может вызвать проблемы в системах обработки материалов, а также высокую остаточную влажность пеллет. Мелкие частицы могут прилипать к сеткам сушилки, уменьшая открытую площадь и поток воздуха через сетки.
Мелкие частицы не являются единственной возможной причиной более высокого, чем желаемое, содержания остаточной влаги в готовых гранулах. Другие причины включают растрескивание расплава (или «снятие акульей шкуры»), пористость окатышей из-за высокого содержания наполнителя или волокнистого материала, неправильную форму окатышей, а также рабочие параметры или параметры окружающей среды.
Разрушение расплава создает очень шероховатую поверхность на гранулах, обеспечивая множество мест для улавливания воды, когда гранулы проходят через центробежную сушилку. Эта шероховатая поверхность находится на боковой стенке гранулы, а не на обрезанных концах. Один из способов свести к минимуму разрушение расплава состоит в том, чтобы сделать гранулу немного тоньше, тем самым уменьшив площадь боковых стенок. Имейте в виду, что это увеличивает общую площадь поверхности. Еще один способ свести к минимуму разрушение расплава — это уменьшить скорость прохождения через отверстия матрицы в дополнение к полировке или хонингованию штампов экструзией.
Высокое содержание минерального наполнителя может привести к образованию пористых гранул, которые очень трудно высушить. Эта пористость позволяет воде проникать в пустоты, которые очень трудно удалить одним только центробежным действием. Волокнистые наполнители, такие как стекло или древесина, действуют как фитиль, втягивая влагу в гранулы, что делает практически невозможной механическую сушку, поэтому может потребоваться дополнительная сушка.
Поскольку центробежные осушители работают по трем основным принципам: остаточное тепло в гранулах, центробежное действие и противоток окружающего воздуха, необходимо установить надлежащие рабочие параметры. Например, если температура технологической воды слишком низкая, результирующая температура гранул будет слишком низкой для испарения достаточного количества поверхностной влаги. С другой стороны, если температура воды слишком высока, могут образовываться хвосты. Противоточный поток воздуха через сушилку очень важен для снижения уровня поверхностной влажности. Его следует проверить и отрегулировать в соответствии со спецификациями производителя.
Условия окружающей среды могут играть значительную роль в снижении влажности поверхности пеллет.Для технологической линии, расположенной в очень влажной зоне и обрабатывающей окатыши с трещинами расплава или пористые, можно было бы ожидать, что будет трудно получить очень низкий уровень влажности окатышей. Кроме того, при работе с продуктом, который очень липкий и требует очень холодной воды, а гранулы выходят из осушителя при температуре ниже текущей точки росы, даже если гранулы могут быть сухими на выходе из сушилки, образуется конденсат, что приводит к с более высоким содержанием влаги, когда он упакован.
Вот некоторые из распространенных проблем, с которыми сталкиваются операторы подводных систем гранулирования.Правильное понимание причины и следствия может в большинстве случаев устранить эти проблемы. Если вы столкнулись с некоторыми из этих проблем, обратитесь к производителю подводного гранулятора, чтобы он помог улучшить ваш процесс.
Об авторе: Марк Тейт
Марк Тейт — технический менеджер в Gala Industries, Inc., Игл-Рок, Вирджиния. Он работает в Gala с 1990 года, работая с клиентами по всему миру, помогая с вводом в эксплуатацию технологических линий, обучая заводской персонал и предоставляя технологические решения для новых и сложных приложений. .В качестве технического менеджера он координирует и контролирует демонстрационные испытания оборудования, а также предоставляет рекомендации и техническую помощь сотрудникам по продажам и обслуживанию по новым и существующим приложениям. Телефон: (540) 884-2589; электронная почта: mtate@gala-industries.