Статистика канала Железобетонный замес. Telegram Analytics
Российский бизнес в Казахстане: есть ли угроза?Те, кто вчера проголосовал в нашем опросе за вероятный ввод войск в Казахстан, оказались правы: утром в Алматы приземлился первый борт с российскими десантниками. Должны прибыть военные и из других стран ОДКБ.
Счет погибшим — и протестующих, и силовиков — идет на десятки. В стране не работают банки и биржа, интернет — с перебоями, многие предприятия остановились. Причем предприятия — так или иначе связанные с Россией. Есть стойкое ощущение, что российские войска едут не только «охранять стратегические объекты», но и наши, российские, инвестиции.
❗Россия — главный внешнеторговый партнер Казахстана с оборотом в 2020м году 17,2 млрд долл. Евразийский банк развития (ЕАБР) сообщает, что в стране действует более 7 тысяч совместных предприятий, в которые инвестировано 11,2 млрд долларов только в 2020. Интересы в республике есть у «Лукойла», «АвтоВАЗа», «Билайна», «Газпрома», «Интер РАО ЕЭС», «Росатома», «Русала», «Еврохима», «Полиметалла», РЕСО и других крупных российских компаний.
📍Даже пресловутый газ, из-за которого начались протесты, производят в Оренбурге на заводе «Газпрома». В середине нулевых отказ Казахстана от планов строительства собственного газоперерабатывающего завода был частью личных договоренностей Путина и Назарбаева. «Национальное достояние» добывает газ в рамках СП «КазМунайГаз», 90% которой у государственного фонда Samruk-Kazyna.
📍Около трети российских инвестиций в Казахстане – свыше $3 млрд – на счету «Лукойла», работающего в стране еще с 90-х. Компания Вагита Алекперова участвует в Каспийском трубопроводном консорциуме, владеющим магистральным трубопроводом от Тенгиза до Новороссийска. В КТК 24% у «Транснефти» во главе с Игорем Сечиным, 19% имеет «КазМунайГаза», остальное распределено у акционеров поменьше, включая иностранные компании. Кроме того, российские нефтяники разрабатывают несколько месторождений.
📍«Росатом» владеет долями в ряде крупных уранодобывающих проектов страны.Казахский уран добывать дешево, а залежи разведаны весьма крупные: около 41% мирового производства.
📍Rusal Олега Дерипаски владеет 50% казахстанской угольной компании «Богатырь Комир». Вторая половина — у фонда Samruk. «Еврохим» инвестировал в Казахстан около $200 млн.
📍IT-сектор также заинтересован в казахском рынке. «Билайн» («Вымпелком» Михаила Фридмана) — второй провайдер сотовой связи в стране, владелец местного оператора «Кар-Тел», он же K-Mobile.
📍Кроме того, российские банки, в числе которых Альфа-банк, ВТБ, Хоум Кредит и другие, активно работают в стране на розничном рынке. На начало 2020 года банки с российским капиталом составили 11% всего банковского рынка республики. Массовый отток вкладчиков, неизбежный при таких событиях, может привести к кризису ликвидности и ударить по «большим» брендам за пределами республики.
Впрочем, даже если элиты займутся переделом своих долей, вряд ли кто-то рискнет отнимать активы у ключевых игроков российского рынка. И даже в случае падения президента Токаева и смены геополитического вектора «отжать» бизнес у россиян будет практически нереально. @nebrexnya
статистика аудитории телеграмм канала Железобетонный замес
Российский бизнес в Казахстане: есть ли угроза? Те, кто вчера проголосовал в нашем опросе за вероятный ввод войск в Казахстан, оказались правы: утром в Алматы приземлился первый борт с российскими десантниками. Должны прибыть военные и из других стран ОДКБ. Счет погибшим — и протестующих, и силовиков — идет на десятки. В стране не работают банки и биржа, интернет — с перебоями, многие предприятия остановились. Причем предприятия — так или иначе связанные с Россией. Есть стойкое ощущение, что российские войска едут не только «охранять стратегические объекты», но и наши, российские, инвестиции. ❗Россия — главный внешнеторговый партнер Казахстана с оборотом в 2020м году 17,2 млрд долл. Евразийский банк развития (ЕАБР) сообщает, что в стране действует более 7 тысяч совместных предприятий, в которые инвестировано 11,2 млрд долларов только в 2020.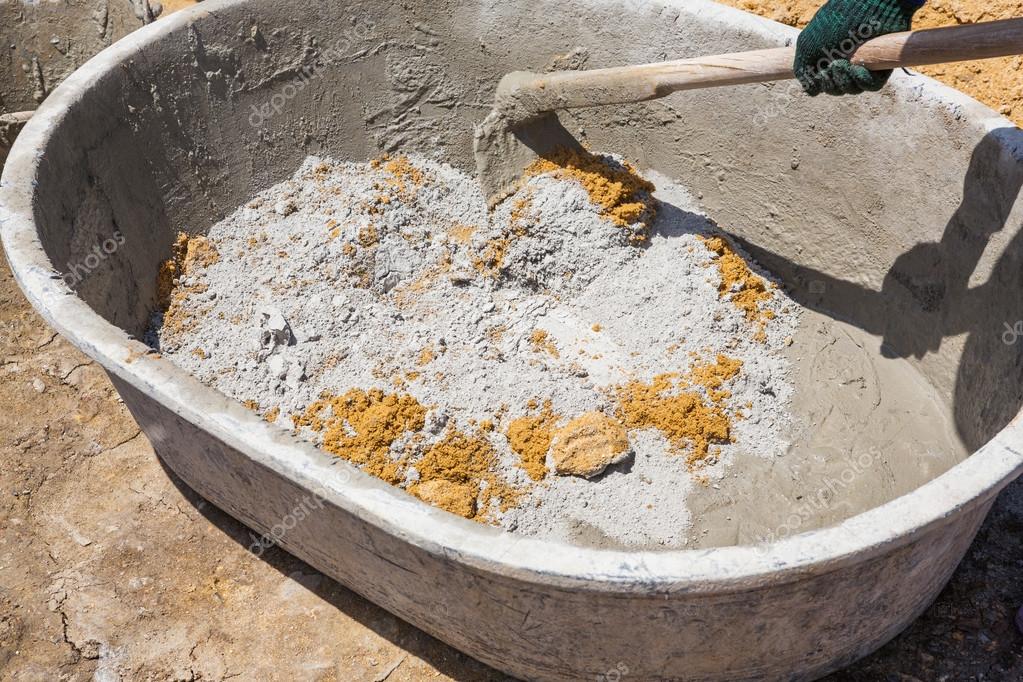
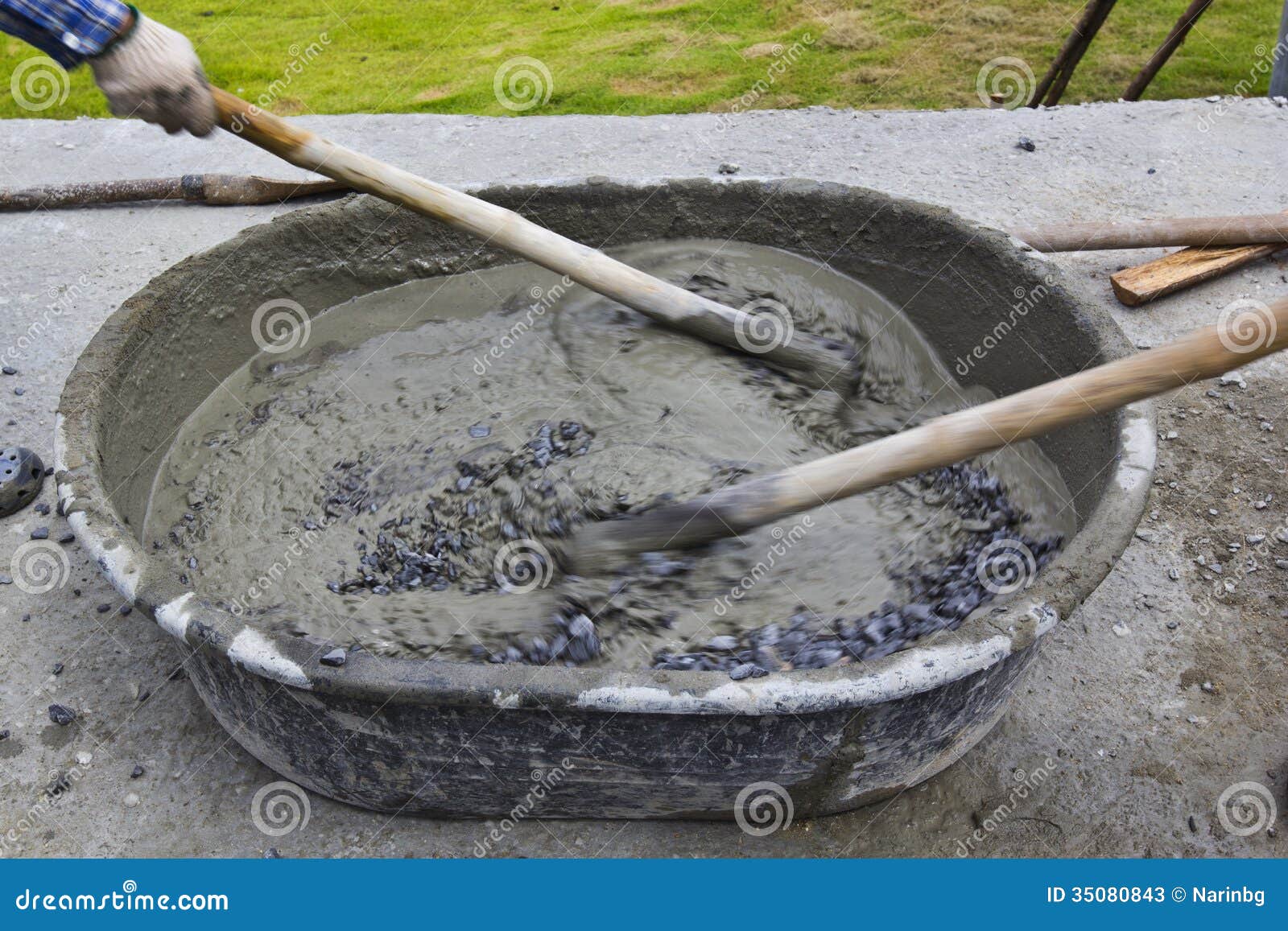

Показать полностью …
Блогер Варламов: «Похоже, сахалинские водители считают пешеходов врагами» — Новости Сахалинской области
«Боюсь, что если в развитии Южно-Сахалинска опираться исключительно на хотелки водителей, это тоже ни к чему хорошему не приведёт», — написал в своём блоге известный российский общественник Илья Варламов. Таким образом он поддержал позицию руководителя центра развития городской среды областной столицы Василия Вишневского, выступающего за безопасность пешеходов.
Поводом для публикации в Telegram-канале @gradovod стало массовое недовольство островных водителей предложением перекрыть сквозной проезд по улице Хабаровской. По результатам опросов подавляющее большинство проголосовало оставить удобный для них проезд.
Вместе с тем, отметил Вишневский, за ликвидацию пешеходных переходов проголосовало от 51% до 70% принявших участие в опросе. В этом, по его словам, проявляется готтентотская мораль — двойные стандарты автомобилистов: «Когда забирают у меня — это плохо, когда мы забираем у других — это хорошо».
Глава центра развития городской среды Южно-Сахалинска привел несколько высказываний горожан:
— Проезд закрывать ради безопасности — глупо, клиника и идиотизм.
— Ликвидировать переход ради безопасности — можно. Безопасность в приоритете.
— Ликвидировать парковки нельзя, а то будет социальный взрыв и поэтому надо провести опрос.
— Ликвидировать переход можно, опросы проводить не надо, просто меняем проект.
— Когда сбивают на нерегулируемом переходе — это зло перехода.
— Когда сбивают на регулируемом переходе — ну так бывает.
«Но на самом деле той же логикой отсталых африканских племён руководствуются автомобилисты по всей России.
Опрос
Что для вас является большим приоритетом?
Железобетонный замес. | ЦСЗО города Москвы
На днях телеграмм-канал «Железобетонный» замес обратил внимание на ситуацию приостановки и возобновления регистрационных действий по договорам долевого участия в одном из жилых комплексов на западе Москвы. Как утверждает ТКЖЗ выявлено несоответствие проектной документацией требованиям действующего законодательства, а именно застройщик внес изменения в проект строительства, связанные с радикальным уменьшением количества машиномест и уменьшением площади нежилых помещений. Исходя их публикации можно сделать вывод, что на изменения в проектную документацию не было получено положительное заключение экспертизы. В любом случае у дольщиков возникли сложности с оформлением прав собственности, например, при переуступки или продажи.
Читая этот пост вспомнил как ко мне обратился друг с просьбой посмотреть документы на строительство в одном из строящихся жилых комплексов рядом на улице Лобачевского в Москве. Изучая документы на строительство высотного жилого комплекса переменной этажностью высотой 140 метров обратил внимание на корректировку разрешения на строительство, итак количество мест на хранение уменьшилось с 1393 до 785, количество квартир увеличилось с 1473 до 1756, исчез детский сад на 400-450 мест. Обеспеченность стала 0,4 машиноместа на 1 квартиру. Мосгостройнадзор на запрос пояснил, что изменения в разрешение на строительство внесены на основании положительного заключение экспертизы, а «…технико-экономические показатели объекта по откорректированной проектной документации не превышают показатели, нормируемые ГПЗУ».
То есть покупатели квартир неожиданного получили жилье где проблема с парковкой машин и поиском мест в ближайших детских садиках. Конечно практика внесения изменений в РнС имеет широкое распространение, но несет с собой и правовые риски, в том числе со стороны регистрационного органа. Но у потребители кроме того рискуют получить жилье другого качества чем планировали изначально.
Друзья, осуществляя покупки недвижимости внимательно подходите к изучение правовой и фактической ситуации, чтобы в последующем не получать разочарование.
Замес теста для слоеных дрожжевых изделий
Тесто для слоеных дрожжевых изделий необходимо хорошо промешивать.
Интенсивное тестомесильное оборудование (200-220 оборотов/мин).
Для приготовления теста для слоеных дрожжевых изделий мы рекомендуем использовать интенсивный замес. На сегодняшний день – это классический вариант тестомесильного оборудования. Скорость вращения тестомесильного органа на таком оборудовании составляет 200-220 оборотов в мин. Продолжительность замеса, как правило, составляет 3 мин на медленной скорости и 4-6 мин на второй скорости. Эти параметры варьируются в зависимости от степени загрузки тестомесильной машины и от качества проработки теста.
Сверхинтенсивные тестомесильное оборудование (280 оборотов/мин и более)
Сверхинтенсивные машины встречаются на предприятиях реже. На этом типе оборудования продолжительность замеса более короткая, потому что клейковинный каркас, необходимый для газоудержания, формируется быстрее.
Медленное тестомесильное оборудование (40-60 оборотов/мин)
На ряде предприятий установлены медленные тестомесильные машины, где есть только первая скорость и качество проработки теста недостаточное, чтобы получить хорошую структуру слоистости и объем готовых изделий. Но не нужно отчаиваться! Если мы пользуемся медленным замесом или у нас горизонтальные машины для пряничного теста, т.е. наше тесто недостаточно хорошо проработано: невозможно растянуть тесто до прозрачной эластичной пленки, то мы можем проработать тесто с помощью тестораскаточной машины. Мы рекомендуем сделать 1-2 раскатки на тестораскаточной машине со сложением в четверку и увеличить продолжительность отлежки теста между раскатками. С помощью сложения теста и его раскатки мы сможем получить развитую структуру теста: по качеству механической обработки и степени развития клейковины оно не будет уступать тесту, которое мы возьмем после замеса на специализированных машинах интенсивного или сверхинтенсивного действия.
Сколько бетона получится из 50 кг цемента: как расчитывается
Производить расчеты о том, какое количество бетона получится из одного мешка цемента весом 50 кг, следует перед началом процесса строительства. Для получения качественной и прочной конструкции обязательно учитывается марка бетонного раствора, используемого в определенных работах, и правильно рассчитываются пропорции остальных составляющих, исходя из их индивидуальных характеристик.
Перед строительством заранее просчитывается количество материалов, которые потребуются. Это особенно важно перед проведением масштабных работ.
Состав бетона: что включено?
Для изготовления бетонного раствора применяются следующие компоненты:
- Щебенка, гравий. Добавляются для наполнения наибольшего объема опалубки. Чем меньше фракция камней, тем плотнее они ложатся.
- Песок. Зернистый материал, заполняющий свободные промежутки между камнями.
- Цемент. Выступает в роли связующего составляющего.
Как «клей» соединяет в едином монолите крупные и мелко-фракционные минеральные наполнители.
- Вода.
Соразмерности входящих в состав бетонного раствора стройматериалов зависимы от специфики и предназначения возводимых конструкций. Для различных видов подбирается соответствующая марка бетона. Информация о классификации бетонных растворов, применяемых в индивидуальном жилищном строительстве, представлена в таблице:
Марка | Области использования |
М100 | Подушки под фундаменты |
М150 | Стяжки полов, отмостки, основания под небольшие сооружения, дорожки |
Заборы, столбы, бордюры | |
М200 | Стены, плиты перекрытий, монолитные фундаменты, колонны |
Как рассчитывается количество компонентов?
Количество добавляемого цемента зависит от его марки, и чем она выше, тем меньше материала израсходуется.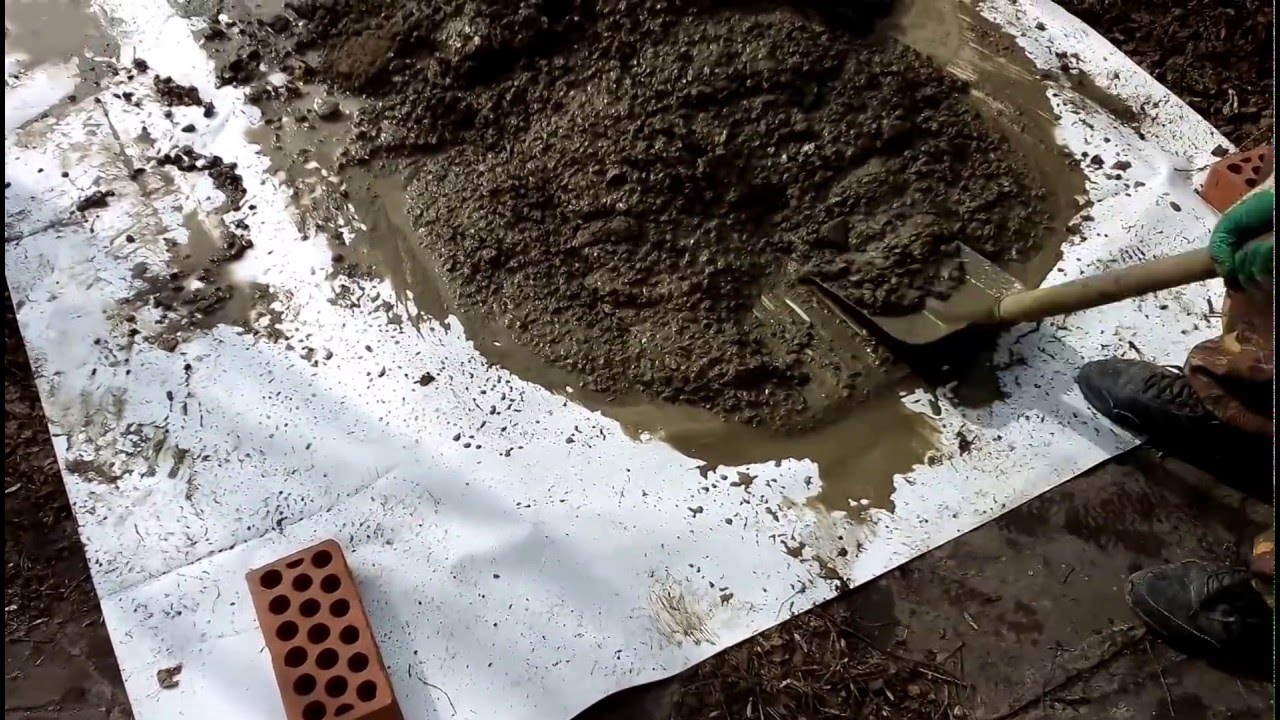
Для всех перечисленных марок бетонного состава существуют пропорции используемых компонентов, требующие соблюдения. В процессе практики приготовления разных составов определились точные весовые соотношения частей смеси, определяющие свойства искусственного камня. Марка бетона задана количеством сухого цемента в растворе по отношению к щебенке и песку. При выборе связующего составляющего учитывается основная характеристика, определяющая его прочность, а именно: марка. Чем выше ее значение, тем тратится меньше материала. Так, портландцемент М200 и М300 применяется при отделочных работах, а М400 и М500 — при возведении монолитных стен и фундаментов.
При замесе бетонного раствора для основания фундамента оптимальным принято считать соотношение сухого цемента к песку и щебенке 1:3:5. Для определения точных пропорций строительных материалов при изготовлении бетона необходимы их подробные характеристики, например, размеры фракций камня, модуль упругости песка, свежесть связующего, а также особенности планируемых работ. Расчет осуществляется исходя из СНиП 82—02—95.
Специалисты сферы строения настоятельно рекомендуют соблюдать следующее требование при выборе цемента: марка связующего компонента обязана превышать аналогичную характеристику бетонного раствора в 1,5—2 раза. Например, бетону М100 отвечает марка цемента М200.
Посмотреть «СНиП 82-02-95» или cкачать в PDF (3.9 MB)
Выход бетона из 50 кг цемента
При заливке сооружения с армированным каркасом, согласно нормам используется 220 кг/м3 вяжущего компонента.Строительными нормами и правилами регламентируется следующий объем вяжущего компонента при затвердевании бетонных конструкций в природных условиях:
- неармированные — 200 кг/м3;
- армированные — 220 кг/м3.
Нужное количество сухого цемента определяется путем умножения типового значения на коэффициенты, зависящие от фракции заполнителей. Для расчета объема смеси для неармированной конструкции, содержащей мешок цемента, нужно выполнить следующее действие: 50/200=0,250 м3, если параметры камешков 20 мм, а модуль упругости песка 1,5. Для армированного бетона выход составляет 50/220=0,227 м3. Рекомендуемая масса портландцемента М500 для наиболее используемого бетона М300—250 кг. Мешка связующего компонента марки М500 достаточно, чтобы приготовить 50/250=0,2 м3 раствора.
Сборные ленточные и столбчатые фундаменты из ж/б блоков и легких бетонов
Читайте в статье:
Как известно, сооружение фундамента — одна из самых продолжительных и трудоемких строительных операций. Но если расчетные нагрузки позволяют, можно и сократить, и упростить этот процесс, сложив основание дома из блочных материалов
Блочное основание подходит для возведения как многоэтажных зданий, так и частных домов из разных стеновых материалов, а также легких построек типа сарая, беседки, гаража и т. п. Сооружение фундаментов четко регламентируется СНиП, где приводятся сырьевой состав, технические характеристики и размеры блоков, рассчитанных на ту или иную нагрузку. С этой целью могут быть использованы изделия из тяжелого бетона (цементно-песчаные и шлакоблоки), керамзитобетона, пено- и газобетона.
Блоки из тяжелых и легких бетонов
Бетон. Фундаментные бетонные блоки ГОСТ подразделяет на три типа: монолитные сплошные (ФБС), сплошные с выемкой — для устройства перемычек и прокладки коммуникаций с последующей заливкой бетоном (ФБВ) и пустотелые (ФБП).
Первые — наиболее прочные (величина данного показателя зависит от марки бетона — от М 100 до М 200), могут иметь арматурный каркас и выпускаются в широкой линейке типоразмеров. Максимальная масса изделий составляет 2 т, плотность — 2500 кг/м³. Чем крупнее габариты бетонных камней, тем выше их прочность и тем большую нагрузку они выдерживают. Самый «ходовой» размер блоков, применяемых в частном домостроении, — 40 × 20 × 20 см, а вес — около 32 кг, что позволяет вести кладку без привлечения тяжелой строительной техники.
Вторая разновидность блоков, как правило, идет на возведение цоколей, на уровне которых делают разводку инженерных сетей. И наконец, облегченные пустотелые блоки, за счет заполненных воздухом полостей, обеспечивают улучшенную теплоизоляцию, но из-за невысоких несущих способностей могут лежать в основании только небольших и нетяжелых построек, например каркасных дачных домов, садовых павильонов, теплиц и т. п.
Отдельную категорию ФБС составляют блоки трапециевидного сечения, маркируемые ФЛ и предназначенные для создания подложки (ее еще называют «подушкой») под первый ряд фундаментной кладки: расширенная нижняя плоскость блоков формирует увеличенную площадь опоры, на которую распределяется нагрузка. В силу особой роли в конструкции, такие изделия производят из бетона прочностью не менее В12,5 и обязательно армируют.
Фундаментные блоки изготавливают на заводах ЖБИ из качественных компонентов (в частности, без всякой примеси глины), с точным соблюдением их пропорций, механическим замешиванием и глубинным вибропрессованием массы. Изделия строго соответствуют заявленным параметрам прочности, морозостойкости и др. , имеют правильную геометрию и ровные поверхности
Шлакоблоки. Их делают на основе цементного вяжущего и наполнителей из отходов производств — кирпичного и стеклянного боя, продуктов сгорания топлива, каменного отсева и др. Причем выпуск материала можно наладить и без промышленного оборудования, используя малые вибропрессовальные машины. Изделия тяжелые, не отличаются точностью размеров и сложны в обработке, но зато привлекают застройщиков своей дешевизной. Для сооружения фундаментов пригодны только полнотелые блоки, но и они не в состоянии нести нагрузку свыше 100 т. Следует учитывать, что шлакоблоки не относятся к разряду экологически чистых материалов (могут включать в себя небезопасные компоненты и примеси) и потому не рекомендуются для использования при возведении жилых домов, основная сфера их применения — хозяйственные постройки.
Керамзитобетон. Это пористый материал с мелкофракционным минеральным наполнителем (вспененные глиняные гранулы, пемзовый гравий), который может быть изготовлен как на производстве, так в условиях стройплощадки. Он легок (вес малогабаритных блоков — 10–25 кг), обладает сравнительно низкой теплопроводностью и водопоглощением, но крошится при резке и из-за своей хрупкости менее «вынослив», чем тяжелый бетон. Конструкционные керамзитоблоки плотностью от 1000 кг/м³, как правило, применяют при возведении фундаментов для небольших одноэтажных домов, бань, хозпостроек, гаражей и пр.
Газо- и пенобетон. Оба материала относятся к разряду легких ячеистых бетонов. Первый производится автоклавным методом на заводах, что обеспечивает точность размеров блоков и гарантирует их качество. Второй, не требующий автоклавной обработки, часто выпускается полукустарным способом, и соответствие таких изделий заявленным характеристикам можно поставить под сомнение. И газо-, и пенобетон отличаются низким коэффициентом теплопроводности, легко режутся обычным ручным инструментом, обладают небольшим весом (масса блока 30 кг). При этом они гигроскопичны, а значит, нуждаются в усиленной изоляции от влаги и в силу своей структуры имеют недостаточную для опорных конструкций несущую способность. Тем не менее, при использовании материала высоких марок прочности и обязательном армировании кладки в каждом ряду, из ячеистых бетонов можно закладывать фундаменты под нетяжелые постройки.
Фундамент из керамзитобетонных блоков
Фундамент из керамзитобетонных блоков
Фундамент из пеноблоков
Сборный ленточный фундамент
Самый надежный вариант блочного основания для капитального загородного дома — ленточный фундамент из ФБС.
Устройство монолитной ленты — процесс продолжительный и трудоемкий (необходима вязка мощного арматурного каркаса, замес бетона в большом объеме), а кладка из крупноформатных блоков ведется значительно быстрее, причем при любой погоде. Кроме того, технические перерывы в ходе работ, способные повлиять на качество заливаемой ленты, никак не сказываются на прочностных свойствах блочной конструкции.
Как и в случае с любым фундаментом, перед его закладкой на участке проводят геологические изыскания и берут пробы грунта на анализ для выяснения его состава, плотности слоев и пр. Полученные данные ложатся в основу проекта, в котором также должны быть учтены глубина промерзания грунта, уровень залегания подземных вод, рельеф местности и другие факторы.
При проектировании фундамента из ФБС его геометрические параметры по возможности нужно привязать к стандартным размерам блоков. Это позволит минимизировать их подрезку (а точнее, раскалывание с применением подъемной техники или трудоемкий ручной крой) для выполнения технологических проемов в ленте и закладки промежутков в углах
Как правило, специалисты рекомендуют блочные фундаменты для участков с плотными песчаными, гравийными или скальными грунтами и УГВ не менее 3 м. Такие условия являются идеальными для сборной ленты. Но в принципе, ее можно устроить и на проблемных грунтах — глинистых и суглинистых — с близко стоящими подземными водами. Другое дело, что в этом случае придется принимать серьезные меры по защите фундамента от воздействия сил пучения и влаги, заметно удорожающие строительство (усиленная гидро- и теплоизоляция, создание системы дренажа). При этом существует мнение, что сборная лента из ФБС — более надежный вариант для пучинистых грунтов, чем монолитная, так как наличие швов между блоками придает конструкции определенную гибкость, позволяя ей справляться с подвижками тогда, когда сплошной ленте грозят разрывы.
Неподходящими для блочных оснований являются пылевато-глинистые и лёссовые грунты, для которых характерна сильная просадка и набухание под воздействием влаги. Общее же правило таково: чем хуже несущая способность грунта, тем большую площадь должна иметь подошва фундамента.
Чтобы повысить прочность и стабильность фундамента, используют комбинированные конструкции, в которых блочные стенки опираются не на основание из ФЛ, а на отлитую бетонную подошву
Первым этапом закладки фундамента является его разметка с помощью натянутой веревки и колышков, особое внимание при этом следует уделить правильности углов. Далее выкапывают траншею расчетной ширины и глубины, выравнивают ее дно и стенки и засыпают щебнем (при высоком УГВ) или крупнозернистым песком слоем 10–20 см. Подушку проливают водой и тщательно трамбуют. Если грунт на участке песчаный или гравийный, в такой засыпке нет необходимости, если же на нем залегают глины, то она обязательна. Кроме того, в подстилающем слое нужно будет предусмотреть систему дрен для отвода воды от подошвы фундамента.
Уплотненное основание застилают рулонной гидроизоляцией, а после установки ФЛ ее края загибают и наплавляют на поверхности блоков. (Важно. Чтобы удешевить конструкцию, ФЛ можно поставить не вплотную друг к другу, а на расчетном расстоянии — так, чтобы блоки первого ряда ФБС опирались на них не всей плоскостью, а только частично, по краям. Промежутки либо засыпают песком или щебнем и утрамбовывают, либо заливают бетоном. И в этом случае прочности ЖБИ будет более чем достаточно даже для массивных построек.)
Опорные блоки обрабатывают битумной мастикой, делают опалубку и заливают нижний армопояс. Когда бетон наберет прочность, приступают к установке крупноформатных ФБС, при этом работу начинают с углов и мест примыкания внутренних несущих стен, то есть с узлов, где выполняется перевязка элементов. Кладку ведут на раствор, а также заполняют им швы между торцами блоков. Последние располагают так, чтобы верхний ряд перекрывал стыки в нижнем — это повышает жесткость и устойчивость конструкции к вертикальным нагрузкам. По ходу сборки ленты ее геометрию постоянно контролируют с помощью уровня и отвеса. При устройстве в теле фундамента отверстий для ввода коммуникаций и создания продухов используют специальные бетонные изделия (так называемые пломбы) либо формируют проемы из фрагментов блоков, закладывая лишние пустоты кирпичом или заливая бетоном.
Когда проектное число рядов уложено, опять монтируют опалубку и отливают верхний армопояс. Заключительные этапы работ — вертикальная гидроизоляция фундамента обмазочными, оклеечными или напыляемыми материалами либо штукатурными составами со специальными добавками, его наружное утепление и обратная засыпка смесью песка и грунта с обязательной трамбовкой.
Чтобы помочь фундаменту эффективнее противостоять силам морозного пучения и разрушительному воздействию влаги, вокруг него нужно соорудить утепленную отмостку. Сделав это сразу по готовности конструкции, можно сократить объем земляных работ.
За счет добавления в бетонную смесь специальных присадок, ЖБИ приобретают повышенную устойчивость к коррозии, образованию плесени и грибка, а наличие в составе щебня делает их невосприимчивыми к агрессивному воздействию кислот, содержащихся в почвах
В углах и местах примыкания стен блоки укладывают с перевязкой
Фундамент из ж/б блоков с отлитым верхним армопоясом
Безусловные достоинства фундаментов из крупноформатных бетонных блоков — высокая несущая способность и долгий срок службы, в среднем не менее 50–75 лет. Но есть у них и серьезные недостатки. Во-первых, более низкая (на 20–30%) по сравнению с монолитными лентами прочность, в частности — из-за наличия в конструкции швов; впрочем, пазы в торцах блоков, заполняемые раствором, снижают их влияние на стабильность кладки. Во-вторых, те же швы, хоть их число, учитывая размеры блоков, и невелико, являются потенциальными зонами промерзания и требуют особо качественной гидро- и теплоизоляции фундамента. В-третьих, сами ЖБИ стоят совсем недорого, но для их установки необходимо привлечение тяжелой техники, что становится крупной статьей расходов и заметно удорожает строительство. Кстати, сэкономить путем применения дешевых шлакоблоков не удастся по той же причине: опирают их, как и ЖБИ, на трапециевидные бетонные «подушки», да и рядовые элементы слишком тяжелы для ручного монтажа, так что без крана все равно не обойтись.
Чтобы снизить затраты, мощный фундамент из крупноформатных блоков иногда сооружают только под ограждающие стены, а несущие перегородки опирают, например, на столбчатые основания. Если же проектные нагрузки позволяют, имеет смысл сложить ленточный фундамент из ФБС малого размера (40 × 20 × 20 см). Сделать это можно своими силами, сэкономив таким образом как минимум на аренде крана. К тому же в данном случае не понадобится подложка в виде ФЛ — фундаментные блоки ставятся на сплошную бетонную отливку толщиной, как правило, 30 см, служащую нижним армопоясом для повышения жесткости конструкции, а также для равномерного распределения нагрузки на основание. Подготовительные работы идентичны описанным ранее. Стенки фундамента выводят в один или два ряда. Первый вариант — облегченный и представляет собой классическую кирпичную кладку со смещением на половину элемента; второй — усиленный, при котором нижний ряд блоков располагают поперек тела ленты, следующий — вдоль и т. д. попеременно. Блоки скрепляют 10–12-миллиметровым слоем раствора по арматурной сетке в каждом ряду. Для устойчивости к вертикальным нагрузкам и стабильности стенок поверх готовой кладки заливают еще один армопояс (30 см).
«Штамповка» или handmade?
При наличии соответствующего оборудования можно организовать изготовление бетонных, а также керамзитных или шлакоблоков непосредственно на стройплощадке. Однако такие изделия однозначно будут уступать по качеству заводской продукции. То же касается и самостоятельной заливки ленточного фундамента. Если нет условий или возможности соблюсти все требования технологии по приготовлению раствора и его уплотнению (точная дозировка ингредиентов, отсутствие примесей, трамбовка с помощью виброплиты и др. ), то лучше собрать основание из готовых штучных элементов, чем отливать монолит сомнительного качества.
По тому же принципу возводят сборные ленточные фундаменты из керамзитобетонных и ячеистых блоков под легкие постройки. Работать с ними несложно: такие камни весят немного, их проще подогнать под нужный размер, но, учитывая пористую структуру материалов, важно обеспечить усиленную гидроизоляцию подошвы фундамента, для чего ее делают здесь в два слоя. Особенно это актуально для ячеистых бетонов, гигроскопичность которых достигает 22% (для сравнения: у керамзитоблоков она составляет 3%, у тяжелого бетона — до 15%, а у кирпича — до 10%). Кроме того, защита от влаги существенно улучшает морозостойкость изделий из легких бетонов.
Как и любая конструкция из мелкоштучных элементов, кладка из газо-, пено- и керамзитоблоков плохо сопротивляется нагрузкам на изгиб, то есть очень чувствительна к подвижкам основания. По этой причине такие фундаменты лучше не закладывать на влагонасыщенных пучинистых грунтах. Предотвратить возможные деформации позволяют те же меры по упрочнению кладки, что рекомендованы для строительства из малоформатных ЖБИ. Обратите внимание: в сортименте керамзитобетонных блоков есть трапециевидные изделия, служащие, подобно железобетонным ФЛ, для более равномерной передачи нагрузки на основание.
Стоит добавить, что особенностью работы с газо- и пенобетоном является монтаж первого ряда камней на цементный раствор, а последующих — на специальный клеевой состав. Он наносится тонким слоем 3–5 мм, что предотвращает возникновение в швах мостиков холода и улучшает теплоизолирующие свойства конструкции.
Требования к проектированию и сооружению фундаментов, а также критерии оценки их качества содержатся в СП 63.13330.2012 «Бетонные и железобетонные конструкции» и СП 70.13330.2012 «Несущие и ограждающие конструкции»
Сборный столбчатый фундамент
Для таких построек, как одноэтажный деревянный дом, баня и т. п., сборный ленточный фундамент, даже возведенный самостоятельно из малоразмерных блоков, зачастую является избыточным — и по своим несущим способностям, и по затраченным на него силам и средствам. Сэкономить на земляных работах, строительных и изоляционных материалах и обеспечить при этом дому надежное основание можно, сложив из тех же блоков столбчатый фундамент.
На основании данных о составе грунта на участке, уровне подземных вод и предполагаемых нагрузок специалисты производят расчет глубины заложения опор и их размера в сечении. Как правило, столбы делают заглубленными или малозаглубленными, при этом разница между ними выражается лишь в количестве рядов блоков. Главное, чтобы они возвышались над землей не менее чем на 40 см. Если территория подтопляемая, имеет сильно выраженный рельеф или высота снежного покрова в данном регионе значительно больше этой величины, опоры «наращивают» до нужной отметки.
Столбы закладывают по углам здания, в местах пересечения стен, а также по их длине с расчетным шагом, что позволяет исключить перекосы и деформации будущей постройки. Сначала выкапывают ямы конической формы, создают на выровненном дне подушку из щебня и песка, проливают ее водой и утрамбовывают. Далее подстилают кусок гидроизолирующего материала (так, чтобы он на 10–15 см выступал за пределы кладки со всех сторон) и устанавливают ряды блоков на бетонный раствор по арматурной сетке, следя за тем, чтобы все опоры выводились в одной плоскости. Блоки в верхнем ряду скрепляют стяжкой.
Чем большее сечение имеет столб, тем он прочнее. Обычно делают кладку в два камня, ставя их в каждом последующем ряду поперек предыдущему. При использовании блоков из легких бетонов, чтобы увеличить площадь опоры и равномернее распределить давление на грунт, под столбами отливают армированную бетонную подошву либо расширяют их основание, выкладывая здесь одну, а иногда и несколько сходящихся ступенек.
Готовые опоры гидроизолируют со всех сторон (при этом влагозащитный контур герметично соединяют с загнутыми краями подстилающей изоляции), выполняют обратную засыпку и монтируют нижнюю обвязку дома в виде деревянного или металлического ростверка.
Опорные столбы должны быть обязательно гидроизолированы со всех сторон
Бетон, армированный фиброй | Строительные материалы — CEMEX США
Использование армирования волокном в жилых проектах представляет собой экономичный способ воспользоваться преимуществами лучших технологий бетона.

Волокна использовались в строительных материалах на протяжении сотен лет. В прошлом натуральные волокна, такие как солома или шерсть животных, использовались для получения «армированного волокном» бетона. За последние несколько десятилетий волокна изменились как по форме, так и по назначению.
Описание продукта
Бетонная смесь, включающая волокнистые материалы в качестве альтернативы сварной металлической сетке для вторичного армирования.
Волокна в бетоне обычно рассматриваются как микро- или макроволокна в зависимости от относительного размера волокна. Микроволокно имеет диаметр менее 0,3 мм (0,012 дюйма), а макроволокно имеет диаметр, равный или превышающий 0,3 мм (0,012 дюйма). Существует четыре основных категории фибробетона в зависимости от материала, используемого для производства волокна.
- Тип I: армированный сталью фибробетон — волокна из нержавеющей стали, легированной стали или углеродистой стали в соответствии с ASTM A820
- Тип II: Бетон, армированный стекловолокном — щелочестойкое стекловолокно в соответствии с ASTM C1666
- Тип III: Бетон, армированный синтетическим волокном — искусственные волокна, такие как углерод, нейлон, полиэстер и полиолефины
- Тип IV: Бетон, армированный натуральными волокнами, целлюлозные волокна из различных растений
Использование/Применение
Обычно используется в плитах перекрытий, приподнятых металлических панелях и плоских работах.Также используется в изолированных бетонных формах (ICF) для жилищного строительства.
Техническая информация о продукте
Некоррозионный, улучшенный ударопрочный, устойчивый к ударам и истиранию; многомерное армирование; всегда позиционируется в соответствии с кодами.
Преимущества продукта
Армирование по всему бетонному сечению: добавление миллионов волокон в бетонную смесь обеспечивает трехмерное армирование бетона.
Увеличение скорости строительства: за счет добавления армирования в бетонную смесь строительство идет быстрее, а трудозатраты снижаются.
Специальное оборудование не требуется: добавление волокнистой арматуры в широко используемые составы бетонных смесей и обычные бетононасосы не требует дополнительных затрат на оборудование.
Армирование волокном также препятствует образованию трещин при пластической усадке, уменьшает растрескивание при пластической усадке, повышает прочность в сыром состоянии и улучшает сцепление смеси, что позволяет получить прочный бетон, не требующий особого ухода.
улучшают свойства как свежего, так и затвердевшего бетона.В свежем бетоне волокна помогают уменьшить кровотечение, усадку и растрескивание, связанное с усадкой. Волокна также помогают свести к минимуму развитие пластических усадочных трещин, которые имеют тенденцию образовываться при неблагоприятных погодных условиях, таких как жаркие, сухие и ветреные условия.
В затвердевшем бетоне основным преимуществом фибры является их способность улучшать несущую способность бетона после появления трещины или ударную вязкость при изгибе.
Дополнительная информация
http://www.nrmca.org/aboutconcrete/cips/24p.pdf
Бетон, армированный фиброй — Ozinga
Обзор фибробетона
Универсальная смесь, армированный волокном бетон, может использоваться для цокольных полов и тротуаров, а также для строительных элементов, таких как балки и колонны, без увеличения стоимости использования арматуры. Эта универсальность обусловлена широким спектром волокон, доступных в различных формах, размерах, длинах и составах.
Добавление фибры в бетонную смесь (например, в нашу серию OzFlat) может уменьшить трещины, повысить ударопрочность и в целом повысить прочность бетона.Благодаря широкому выбору волокон железобетон хорошо подойдет для любых целей, от жилых двориков и подъездных дорог до коммерческих парковок.
Типы волокон
Волокнамогут играть важную роль в армировании бетона. Однако не все волокна одинаковы. Хотя многие волокна не могут заменить прочность, полученную за счет стального армирования, большинство из них все же может продлить срок службы бетона, а иногда даже придать ему особый вид.
Микросинтетика (невидимое волокно)
В тех случаях, когда важен внешний вид бетона, микросинтетические или невидимые волокна могут быть лучшим выбором для вашего проекта.С этим типом волокна вы можете получить те же преимущества, что и с традиционным волокном, сохраняя при этом чистую, почти невидимую поверхность
Макросинтетика (традиционное волокно)
Макросинтетические волокна обладают теми же преимуществами, что и стальные волокна, но без риска коррозии, иногда связанного со сталью. Макроволокна повышают ударную вязкость и долговечность бетона, и их можно добавлять в гораздо больших количествах на единицу объема, чем традиционные стальные волокна.
Стальные волокна
Стальная фибра отлично подходит для тяжелых условий эксплуатации и промышленного применения, где необходимы превосходная защита от трещин и ударопрочность.Стальная фибра спроектирована так, чтобы придать бетону долгосрочные характеристики в зонах интенсивного использования.
Различные типы волокон обеспечивают различные преимущества. В то время как стальные волокна могут помочь улучшить общую прочность конструкции и уменьшить потребность в стальной арматуре, другие, такие как волокна на основе нейлона, могут улучшить устойчивость бетона к усадке при отверждении. Большинство волокон также улучшают морозостойкость.
Какое волокно лучше всего подходит для вашего проекта? Свяжитесь с нашей компетентной службой поддержки клиентов, чтобы узнать больше.
Что происходит с фибробетоном?
Добавление фибры в бетон делает его прочнее или что?
Бетон, армированный сталью, — основа нашего современного общества. Армирование внутри бетона создает композитный материал, при этом бетон обеспечивает прочность против напряжения сжатия, а армирование обеспечивает прочность против напряжения растяжения. Но, в то время как стальная арматура решает одну из самых больших проблем бетона, она создает совершенно новую проблему: коррозия встроенной стальной арматуры является наиболее распространенной формой износа бетона.Итак, что мы делаем по этому поводу?
Привет, я Грейди, а это Практическая инженерия. В сегодняшнем выпуске мы тестируем некоторые инновации в армировании бетона.
Хотя незащищенная сталь естественным образом подвержена коррозии или ржавчине, когда она внедряется в бетон, определенные факторы обычно защищают ее. Во-первых, это очевидная защита от внешней среды относительно непроницаемым и прочным материалом. Вода и загрязняющие вещества обычно не могут проникнуть через бетон в сталь.
Вторая форма защиты – щелочная среда. Высокий pH обычного бетона создает на стали тонкий оксидный слой, обеспечивающий защиту от коррозии.
Но в некоторых случаях этой защиты недостаточно. Одним из основных источников коррозии арматуры является соль. Будь то воздействие соленой воды в морской среде или применение противогололедных солей для повышения безопасности дорог зимой, эти ионы хлорида могут проникать сквозь бетон, вызывая коррозию стальной арматуры.А когда сталь подвергается коррозии, образуется оксид железа, который расширяется внутри бетона. Это расширение создает напряжение, иногда называемое оксидным домкратом, и является одной из основных причин разрушения бетона.
Трещины в крышке
Итак, как предотвратить попадание ионов хлорида и других загрязняющих веществ в сталь и вызвать коррозию? Первая линия обороны — прикрытие.
Защитный слой — это минимальное расстояние между внешней поверхностью бетона и арматурной сталью.
И, в зависимости от воздействия и применения, некоторые коды определяют различное количество бетонного покрытия, как правило, от 25 до 75 миллиметров или от 1 до 3 дюймов. Покрытие является одной из причин, по которой хорошая бетонная работа требует так много усилий, прежде чем бетон появится на рабочей площадке. Установка прочной опалубки и много-много проволоки, связывающей всю арматуру вместе, помогают быть абсолютно уверенными в том, что, несмотря на все толчки, ходьбу и общий хаос, который возникает, когда приходит время фактической укладки бетона, арматура остается там, где она должна быть. внедрены в конечный продукт.Пренебрежение этими шагами может привести к тому, что арматура опустится на дно плиты или окажется слишком близко к внешней поверхности до того, как бетон затвердеет, что в конечном итоге приведет к преждевременной коррозии арматуры из-за отсутствия покрытия.
Но даже при соответствующем покрытии любая трещина в бетоне может привести к прямому контакту загрязняющих веществ и воды с арматурой. И вы не удивитесь, узнав, что трещины в бетоне не так уж и редки. Большинство бетонов дает усадку по мере затвердевания, что может привести к трещинам. Изменения температуры также вызывают расширение и сжатие, что может привести к растрескиванию. Бетон также может растрескиваться при нормальных ожидаемых условиях нагрузки из-за того, как сталь воспринимает напряжения внутри материала.
Одним из способов решения этой проблемы является предварительное натяжение арматурного стержня. Эту тему я кратко обсуждал в предыдущем видео, и в будущем я хотел бы углубиться в эту тему. Но сегодня я хочу показать еще один вариант уменьшения этих трещин.
Бетон, армированный волокном
Бетон, армированный волокнами, в значительной степени соответствует вашим ожиданиям.Это ни в коем случае не новая идея, но наше понимание и использование различных видов волокон в бетонной смеси продолжает расти. Добавление в бетон стеклянных, стальных или синтетических волокон может дать много преимуществ, но одним из наиболее важных является контроль над трещинами .
Я построил три почти одинаковые железобетонные балки, чтобы показать, как это работает, и дал им высохнуть около недели. Первый имеет только стальную арматуру в качестве арматуры. Я использую свой гидравлический пресс, чтобы проверить прочность каждой балки и посмотреть, как она работает до отказа.И я использую тонны как меру силы на этих балках, просто потому, что это то, что говорит датчик, но единицы измерения совершенно произвольны для демонстрации. (Если вы предпочитаете SI [Système Internationale или метрическую систему], просто представьте, что это метрические тонны.)
Когда я увеличиваю нагрузку на балку, вы видите трещины, начиная всего с 3 тонн. Эти трещины образуются из-за того, что сталь немного растягивается, воспринимая растягивающее напряжение в бетоне. Балка прекрасно держит нагрузку и даже не близка к разрушению, но бетон не может растягиваться вместе со сталью, поэтому он должен треснуть. Вы можете себе представить, как эти трещины могли привести к контакту воды и воздуха с арматурой и, в конечном итоге, к разрушению бетона.
(Эти трещины являются важной частью этой демонстрации, но я пошел дальше и увеличил нагрузку до тех пор, пока балка не разрушилась, потому что, эй, для этого годятся гидравлические прессы, верно?)
Для следующих двух балок я добавил в бетонную смесь волокна: одна балка содержит стальное волокно, а другая — стекловолокно. Стальная арматура и волокна объединяются, чтобы противостоять растягивающим напряжениям в балках.Арматурный стержень обеспечивает крупномасштабное армирование, чтобы противостоять растяжению по всему элементу конструкции, а волокна обеспечивают мелкомасштабное армирование, чтобы противостоять локализованному напряжению, вызывающему растрескивание.
Когда я нагружаю эти балки до 3 тонн, то не видно ни одной трещины. На самом деле, для обеих этих балок я не видел образования трещин почти в два раза больше. и даже тогда трещины были намного меньше. Обе балки вышли из строя примерно при той же нагрузке, что и первая, которую я и ожидал. Как я уже сказал, волокна на самом деле не добавляют большой общей прочности балке, но вы можете легко видеть, что они могут иметь большое значение для предотвращения коррозии стальной арматуры.
Альтернативы стальной арматуре
Вам может быть интересно, почему мы вообще используем сталь для армирования? Сталь относительно недорогая, хорошо испытанная и прочная, но есть много других материалов с отличными механическими свойствами, которые не сталкиваются с проблемой коррозии. Для очень агрессивных сред мы иногда используем арматуру с эпоксидным покрытием или даже нержавеющую сталь, но есть некоторые новые альтернативы, такие как полимеры, армированные волокном, или стержни из стеклопластика. Это армирование из базальта, переплавленной вулканической породы, пропускаемой через крошечные сопла для создания чрезвычайно прочных волокон.
Подобные варианты часто стоят больше, чем стальная арматура, а в некоторых случаях намного дороже. Но основным препятствием для использования этих новых, более инновационных типов армирования является не только стоимость. Легко видеть, что эти дополнительные затраты могут быть компенсированы увеличением срока службы бетона. Другое торможение происходит просто из-за отсутствия широкого использования. Инновации в гражданском строительстве происходят медленно, потому что последствия неудачи очень велики. Обретение уверенности в конструкции имеет столько же общего с инженерной теорией, сколько и простое наблюдение за тем, насколько хорошо аналогичные конструкции работали в прошлом.
Но многие инженерные катастрофы происходят не из-за плохой конструкции, а из-за плохого обслуживания, поэтому долгосрочная долговечность может быть столь же важна для общественной безопасности, как и другие критерии проектирования. В будущем мы обязательно увидим более инновационные способы армирования бетона, в том числе варианты, которые я упомянул в этом видео.
Спасибо за просмотр, и дайте мне знать, что вы думаете!
— Это видео взято с YouTube-канала «Практическая инженерия», на котором есть гораздо больше обучающих видео по инженерным вопросам.
Бетон, армированный фиброй – типы, свойства и преимущества
🕑 Время прочтения: 1 минута
Бетон, армированный фиброй, можно определить как композитный материал, состоящий из смесей цемента, раствора или бетона и прерывистых, дискретных, равномерно диспергированных подходящих волокон. Фибробетон бывает разных типов и свойств со многими преимуществами.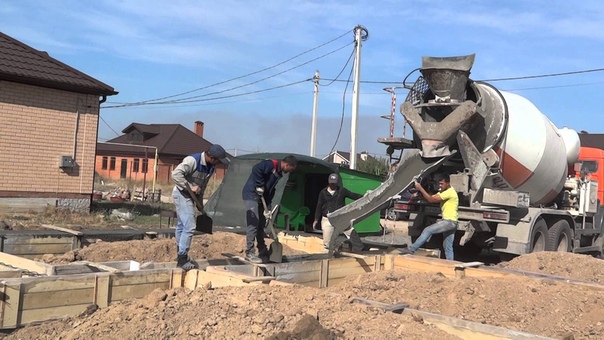

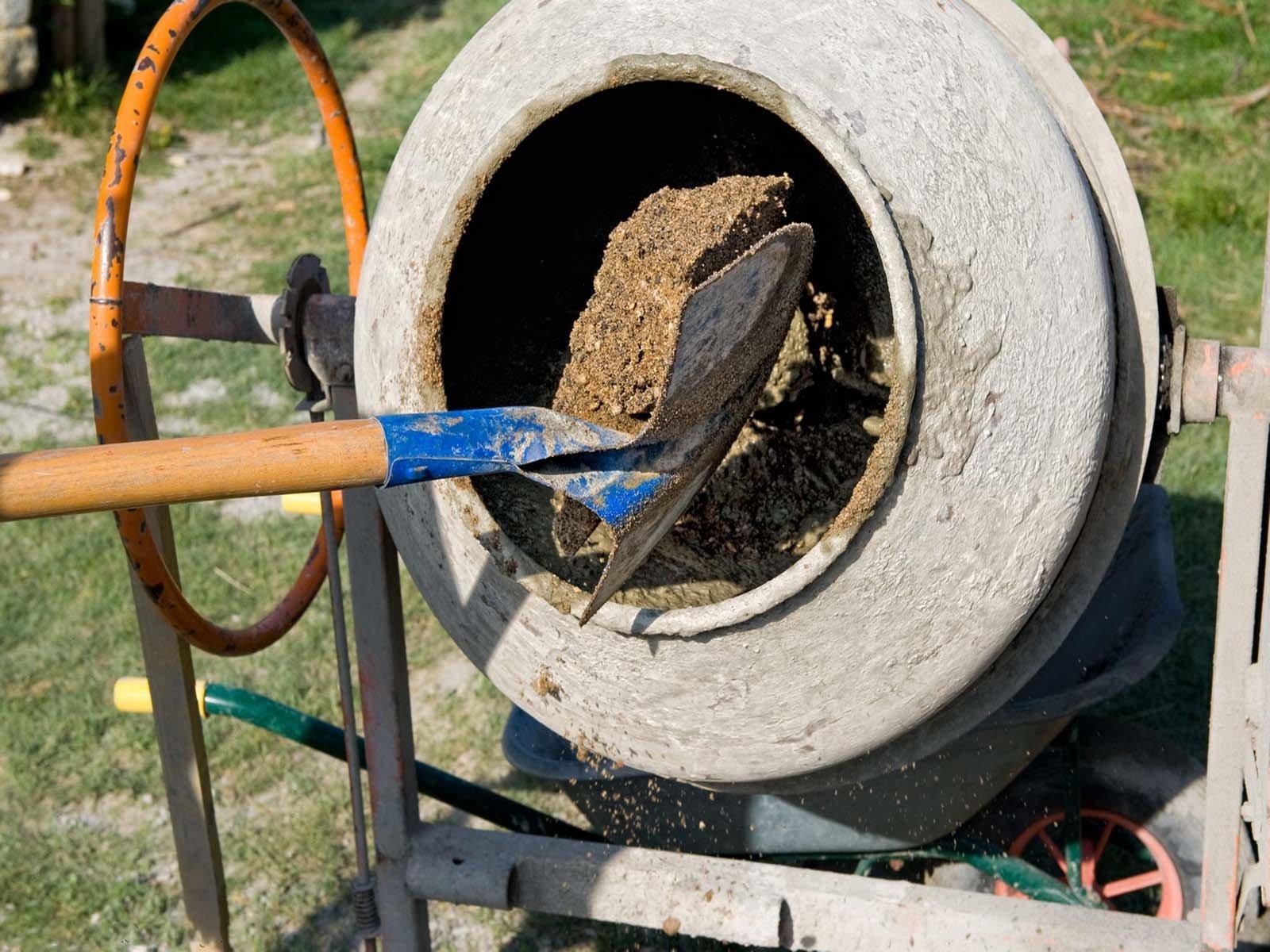

- Повышает прочность бетона на растяжение.
- Уменьшает воздушные и водяные пустоты, присущую гелю пористость.
- Повышает прочность бетона.
- Волокна, такие как графит и стекло, обладают отличной устойчивостью к ползучести, чего нельзя сказать о большинстве смол. Таким образом, ориентация и объем волокон оказывают значительное влияние на характеристики ползучести арматурных стержней/напрягающих элементов .
- Железобетон сам по себе представляет собой композитный материал, в котором арматура выступает в качестве усиливающего волокна, а бетон — в качестве матрицы.
Поэтому крайне важно, чтобы поведение двух материалов при термических напряжениях было одинаковым, чтобы свести к минимуму дифференциальные деформации бетона и арматуры.
- Было признано, что добавление в бетон небольших, близко расположенных и равномерно распределенных волокон будет действовать как гаситель трещин и существенно улучшит его статические и динамические свойства.
Факторы, влияющие на свойства фибробетона
Бетон, армированный фиброй, представляет собой композитный материал, содержащий волокна в цементной матрице в упорядоченном или случайном порядке.Его свойства, очевидно, будут зависеть от эффективной передачи напряжения между матрицей и волокнами. Факторы кратко обсуждаются ниже: 1. Относительная жесткость волоконной матрицы Модуль упругости матрицы должен быть намного ниже модуля упругости волокна для эффективной передачи напряжения. Таким образом, волокна с низким модулем упругости, такие как найлоны и полипропилены, вряд ли дадут улучшение прочности, но помогут в поглощении большой энергии и, следовательно, придадут большую степень ударной вязкости и сопротивления приданию.
Рис. 1: Влияние объема волокон на изгиб
Рис. 2: Влияние объема волокон при растяжении
3. Соотношение сторон волокна Еще одним важным фактором, влияющим на свойства и поведение композита, является соотношение сторон волокна.
Тип бетона | Соотношение сторон | Относительная прочность | Относительная ударная вязкость |
Гладкий бетон | 0 | 1 | 1 |
С | 25 | 1.5 | 2,0 |
Случайно | 50 | 1,6 | 8,0 |
Дисперсные волокна | 75 | 1,7 | 10,5 |
100 | 1,5 | 8,5 |



- Бетон, армированный стальным волокном
- Цементный раствор и бетон, армированный полипропиленовым волокном (PFR)
- Армированный стекловолокном бетон GFRC
- Асбестовые волокна
- Углеродное волокно
- Органические волокна


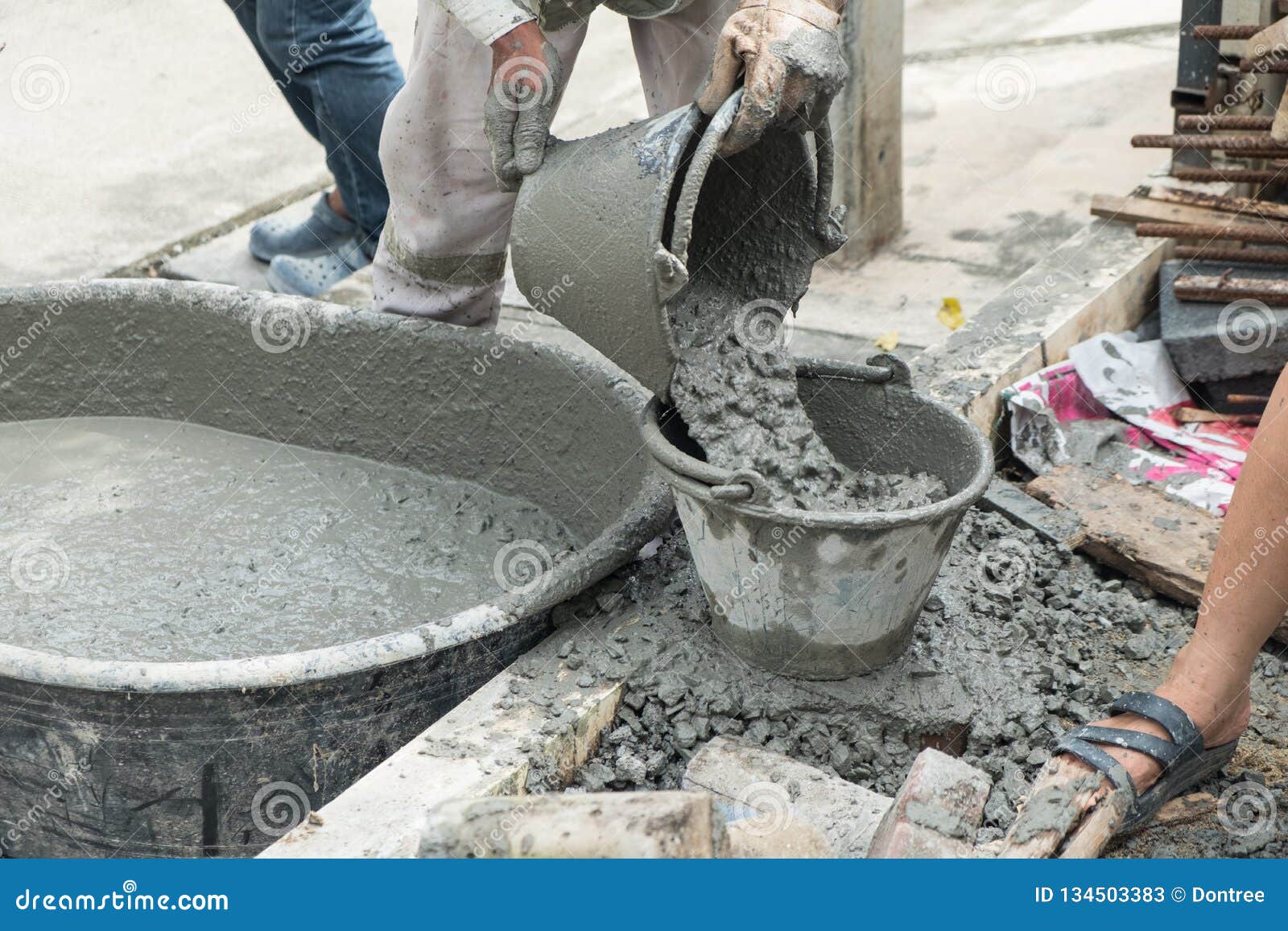
Рис. 3: Цементный раствор и бетон, армированный полипропиленовым волокном
3. GFRC — Бетон, армированный стекловолокном Стекловолокно состоит из 200-400 отдельных нитей, которые слегка связаны между собой, образуя основу.Эти подставки можно нарезать на кусочки разной длины или объединить в тканевые коврики или ленты. Используя обычные методы смешивания обычного бетона, невозможно смешать более 2% (по объему) волокон длиной 25 мм. Основное применение стекловолокна заключалось в армировании цементных или растворных матриц, используемых при производстве тонколистовых изделий. Обычно используемыми истинами стекловолокна являются электронное стекло. В армированном пластике и AR-стекле E-стекло имеет недостаточную устойчивость к щелочам, присутствующим в портландцементе, в то время как AR-стекло имеет улучшенные щелочестойкие характеристики.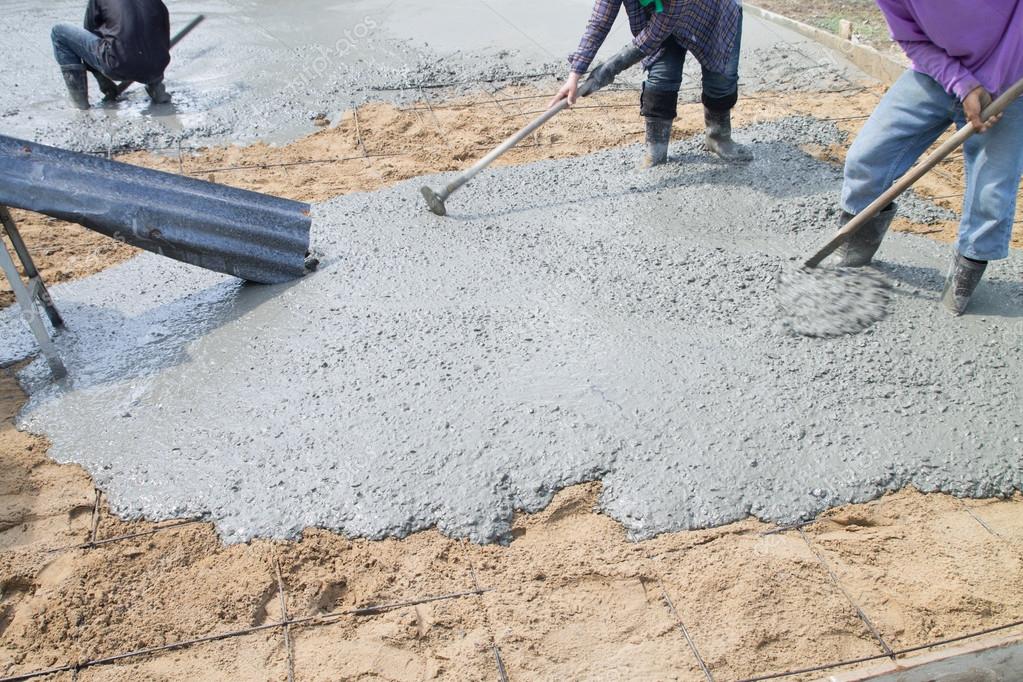
Рис. 4: Бетон, армированный стекловолокном
4. Асбестовые волокна Доступное в природе недорогое минеральное волокно, асбест, было успешно объединено с портландцементной пастой для получения широко используемого продукта, называемого асбестоцементом. Асбестовые волокна обладают термомеханической и химической стойкостью, что делает их пригодными для изготовления листовых труб, черепицы и гофрированных кровельных элементов.Асбестоцементная плита примерно в два-четыре раза больше, чем неармированная матрица. Однако из-за относительно небольшой длины (10 мм) волокна обладают низкой ударной вязкостью.Рис. 5: Асбестовое волокно
5. Углеродное волокно Углеродное волокно из самого последнего и, вероятно, наиболее впечатляющего дополнения к ассортименту волокна, доступного для коммерческого использования.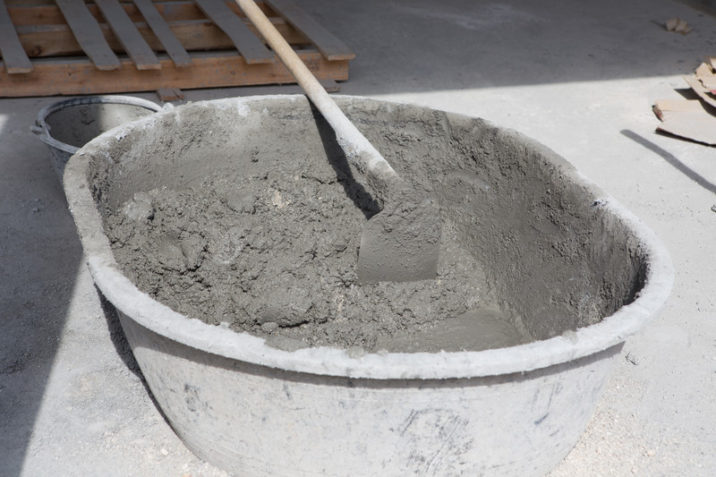
Рис. 6: Углеродное волокно
Читайте также: Бетон, армированный стекловолокном (GFRC) – свойства и применение в строительных работах 6. Органические волокна Органическое волокно, такое как полипропилен или натуральное волокно, может быть химически более инертным, чем стальное или стекловолокно.Они и дешевле, особенно если натуральные. Для получения композита многократного крекинга можно использовать большой объем растительного волокна. Проблема смешивания и равномерного диспергирования может быть решена путем добавления суперпластификатора.Рис. 7: Органическое волокно
Подробнее: Факторы, влияющие на долговечность фибробетона (FRC) Бетон, армированный волокном, в дорожном покрытииОбзор армированного волокном бетона
ЧТО ТАКОЕ ФИБРОБЕТОН И ПОЧЕМУ ОН ПОЛЕЗЕН?
Поставщики товарного бетона обсуждают преимущества использования фибробетона
Мы и раньше слышали о армировании бетона материалами, но для чего это нужно? Это что-то, что мы недавно разработали, или оно существует уже давно?
Проще говоря, этот процесс укрепляет бетон, обеспечивая целостность и безопасность конструкции — в основном то, что удерживает небоскребы от падения.
Чтобы узнать больше о фибробетоне, ознакомьтесь с его назначением, типами, применением и многочисленными преимуществами.
Подробнее: Проблема с железобетоном
ЧТО ТАКОЕ ФИБРОБЕТОН?
Бетон, армированный волокнами (FRC) — это бетон, в который добавлены волокнистые материалы для повышения прочности и структурной целостности бетона. FRC имеет маленькие, короткие и незаметные волокна, которые ориентированы случайным образом, но равномерно распределены по всему бетону.
Волокна могут быть круглыми или плоскими и часто составляют от одного до трех процентов от общего объема бетонной смеси.
Обычные волокна, используемые в железобетоне, включают стальные, стеклянные, синтетические и натуральные волокна.
ПОЧЕМУ ЭТО ИСПОЛЬЗУЕТСЯ?
Сам по себе бетон не обладает прочностью на растяжение и склонен к растрескиванию. Но бетон, армированный волокнами, может улучшить прочность на растяжение и контролировать растрескивание бетонных конструкций, которое часто вызывается пластической усадкой и усадкой при высыхании.
Волокна в бетоне также могут снижать проницаемость бетона, что ограничивает количество просачивающейся воды, дополнительно уменьшая растрескивание при усадке во время отверждения.
Некоторые типы волокон также используются для придания бетону большей стойкости к истиранию, ударам и разрушению.
Бетон, армированный волокнами, часто используется для:
- Применение на уровне земли, например, тротуары и полы зданий
- Подвальные фундаменты
- Строительные столбы
- Опорные балки
- Мосты
- Усыпальницы
- Автодороги
- Черепица и черепица
- Набрызг-бетон, например бассейны, бассейны, сельскохозяйственные водотоки и каменные стены
- Дренажные трубы
- Септики
- Канализационные системы
- Сборные и готовые формы, такие как композитные настилы и тонкие цементные листы и панели
- Хранилища и сейфы
ТИПЫ ВОЛОКНО, ИСПОЛЬЗУЕМЫЕ В БЕТОНЕ
Вот некоторые из наиболее распространенных волокон, используемых в железобетоне:
Сталь Сталь является одним из наиболее часто используемых материалов для фибробетона. Круглые стальные волокна изготавливаются путем разрезания круглой проволоки на короткие отрезки. А плоские прямоугольные стальные волокна создаются путем просеивания стальных листов.
Стальные волокна повышают прочность бетонных смесей за счет распределения локализованных напряжений. Армирование стальным волокном также уменьшает количество необходимой конструкционной стали, такой как арматура и сетка. Он также может уменьшить повреждения от замерзания и растрескивания, вызванные пластиковой усадкой, при одновременном повышении ударопрочности.
Полипропилен (ПФР) В бетоне, армированном полипропиленовым волокном (PRF), используется дешевый и широко доступный полипропиленовый полимер.Полипропиленовые волокна устойчивы к большинству химических веществ и имеют высокую температуру плавления 165˚C. Таким образом, он может выдерживать рабочую температуру 100˚C в течение коротких периодов времени.
Поскольку эти волокна являются гидрофобными, их можно легко смешивать и равномерно распределять в бетоне без образования комков.
Бетон, армированный стекловолокном (GFRC), является еще одним распространенным типом. Чаще всего используется при производстве изделий из тонколистового бетона.
АсбестМинеральные волокна асбеста естественно доступны и недороги.Асбестовые волокна термически и химически стойкие, поэтому подходят для листовых изделий, труб, черепицы, гофрированных кровельных элементов. Но поскольку существует риск для здоровья, связанный с асбестом, поставщики бетона в наши дни используют более безопасные материалы.
УглеродУглеродные волокна обладают высокой эластичностью и прочностью на изгиб, при этом их прочность сравнима или даже превосходит стальные волокна. Но углеродные волокна более уязвимы к повреждениям, чем даже стекловолокна, поэтому их необходимо обрабатывать смоляным покрытием.
Органический Натуральные волокна, такие как растительные волокна, дешевле, чем другие виды волокон. Однако для предотвращения растрескивания часто требуется большой объем натуральных волокон. А натуральные волокна, как правило, труднее смешивать и равномерно распределять по бетону. Таким образом, может потребоваться суперпластификатор, чтобы избежать проблем со смешиванием и обеспечить равномерное распределение волокон.
Пластиковые волокна относительно новы в мире армирования бетона.Но эти волокна дают возможность перерабатывать изобилие пластика в мире для получения более экологически чистого железобетона.
Нейлон Нейлоновые волокнаво многом схожи с полипропиленовыми волокнами. Нейлоновые волокна также прочнее, чем сварная проволочная ткань при использовании в бетоне.
ФАКТОРЫ, ВЛИЯЮЩИЕ НА СВОЙСТВА ФИБРОБЕТОНА
При использовании фибробетона на его характеристики и удобоукладываемость влияют многие факторы, например:
Относительная жесткость матрицы волокна Чтобы обеспечить эффективную передачу напряжения в бетоне, модуль упругости бетонной матрицы должен быть ниже, чем модуль упругости волокна.
Например, нейлоновые и полипропиленовые волокна имеют низкий модуль упругости. Таким образом, хотя они вряд ли улучшат общую прочность, они помогут поглотить большое количество энергии напряжения, сделав бетон более прочным и устойчивым к нагрузкам.
С другой стороны, сталь, стекло и углеродные волокна создают более прочный и жесткий бетон.
Объем волоконКоличество (объем) волокон, используемых в бетоне, влияет на прочность и ударную вязкость бетона.Прочность на растяжение и ударная вязкость будут увеличиваться по мере увеличения объема волокон.
Соотношение сторон волокнаПо мере увеличения соотношения сторон волокна увеличивается прочность и ударная вязкость бетона, но только до определенного момента — отношения размеров 75. Если общий объем волокон превышает это максимальное соотношение размеров, то волокна могут на самом деле уменьшить долговечность бетона, а не укрепить его.
Ориентация волокна Хотя волокна в железобетоне ориентированы случайным образом, их ориентация может повлиять на прочность бетона. Волокна, расположенные параллельно нагрузке, обеспечивают большую прочность на растяжение и долговечность, чем волокна, расположенные перпендикулярно или произвольно.
Стальные волокна снижают удобоукладываемость бетона и затрудняют уплотнение бетона. Длина и диаметр стальных волокон также влияют на обрабатываемость и легкость уплотнения.
Кроме того, неравномерное распределение волокон в бетоне снижает удобоукладываемость и уплотнение.Для улучшения удобоукладываемости и уплотнения поставщики бетона могут увеличить соотношение вода/цемент или использовать добавки, уменьшающие количество воды.
При смешивании фибробетона максимальный размер крупных заполнителей должен составлять 10 мм во избежание снижения прочности бетона. Добавки, уменьшающие трение, и добавки, повышающие сцепление смеси, могут помочь улучшить смесь.
СмешиваниеПри смешивании фибробетона необходимо учитывать указанные выше факторы, чтобы избежать:
- Слипшиеся волокна;
- Сегрегация волокон; и,
- Неравномерное распределение волокон.
Добавление фибры в бетон перед добавлением воды может помочь обеспечить равномерное распределение фибры по всей бетонной смеси.
ПРЕИМУЩЕСТВА ФИБРОБЕТОНА
Все волокна уменьшают потребность бетона в стальной арматуре. А поскольку армирование волокном, как правило, дешевле, чем стальная арматура (и менее подвержено коррозии), оно делает бетон более рентабельным.
Волокна также могут улучшить характеристики бетона:
- Удобоукладываемость
- Гибкость
- Прочность на растяжение
- Долговечность — за счет контроля и уменьшения ширины трещин
- Пластичность
- Сплоченность
- Морозостойкость
- Стойкость к истиранию и ударам
- Стойкость к пластической усадке при отверждении
- Стойкость к растрескиванию
- Усыхание в раннем возрасте
- Огнестойкость
- Однородность
С таким большим выбором вариантов и всеми этими преимуществами рассмотрите возможность использования фибробетона для своего следующего проекта. Вы даже можете комбинировать типы волокон, чтобы получить превосходный бетон с комбинированными преимуществами каждого волокна.
Область применения джутового волокна для армирования бетонного материала | Текстиль и одежда Экологичность
Материалы
Местное необработанное джутовое волокно, показанное на рис. 1, использовалось без какой-либо обработки. Это джутовое волокно с четырьмя различными длинами нарезки (10, 15, 20 и 25 мм), также показанное на рис. 2, наносили на бетонную смесь в различных объемных процентах.В качестве вяжущего применялся обычный портландцемент; нормальная консистенция которого составляла 30 %, время начального схватывания 132 мин, время окончательного схватывания 07:00 ч. В качестве крупного заполнителя использовали песок (модуль крупности = 2,5) и хорошо отсортированный кирпичный щебень 25 мм вниз.
Рис. 1 Рис. 2Отрезанные куски необработанного джутового волокна
Бетонная смесь
Состав смеси – это подбор ингредиентов смеси и их пропорций, необходимых в бетонной смеси. Состав смеси предполагает наличие количества цемента, мелкого и крупного заполнителя (кирпичная крошка, показанная на рис. 3), а также необходимо знать соотношение между водоцементным отношением и заданной прочностью. Поскольку целью исследования является изучение влияния включения джутового волокна на механические свойства бетона, расчет состава смеси с заданной прочностью в исследовании не проводился. Вместо этого использовалось общепринятое соотношение компонентов смеси, используемое в Бангладеш и других соседних странах, таких как части Индии и Пакистана.С этой целью в настоящем исследовании использовались два различных соотношения смеси: цемент/песок/кирпичная крошка (по объему) = 1:2:4 и 1:1,5:3 и соотношение вода/цемент (по весу) 0,60 и 0,55. осторожно поддерживается. При приготовлении бетонной смеси первоначально в бетонную смесь добавляли джутовое волокно разной длины и объемного содержания и наблюдали за эффективностью смешивания для получения лучшего расположения джута. И, наконец, было выбрано джутовое волокно длиной 10, 15, 20 и 25 мм с объемной дозировкой 0, 0,1, 0,25, 0,50 и 0,75%; и, наконец, образцы были подготовлены для определенного набора параметров.
В таблице 1 показано расчетное количество материалов для одной переменной, тогда как другие могут быть получены с помощью той же процедуры.
Подготовка образца для испытаний
Были использованы различные параметры бетонных композитов, длина и объемная доля содержания джутового волокна. Разная длина волокна 10, 15, 20 и 25 мм и содержание 0, 0.1, 0,25, 0,50 и 0,75 %. Три разных образца: кубы (150 мм × 150 мм × 150 мм), призмы (450 мм × 150 мм × 150 мм) и цилиндры (150 мм × 300 мм) были отлиты для определения прочности на сжатие, изгиб и растяжение композиты соответственно. Волокна обрезали до указанной длины вручную ручными ножницами. Смешивание ингредиентов производилось с помощью тарельчатого миксера, и джутовые волокна медленно и равномерно добавлялись в бетонную смесь, чтобы можно было подтвердить равномерное распределение нитей по всему бетону. В смеситель добавляли цемент и проводили перемешивание с последующим добавлением воды до достижения однородности. Такой способ перемешивания бетона продолжался около 3 мин. Затем свежезамешанный бетон заливали в формы куба, призмы и цилиндра. После этого образцы оставляли на 24 ч для расформовки. Затем их выдерживали в воде не менее 28 дней. По окончании периода отверждения образцы высушивали на воздухе в течение 24 часов перед испытанием.
Экспериментальная программа
Настоящее исследование состоит из определения прочности на изгиб, сжатие и растяжение бетонных композитов с джутовым волокном и сравнивалось с аналогичными показателями простого бетона.Универсальная испытательная машина (модель-UTN-100, Индия, грузоподъемность 980 кН) для испытания на растяжение и автоматическая испытательная машина на сжатие (MATEST srl, Италия, грузоподъемность 3000 кН), показанные на рис. 4, для испытания на сжатие и автоматический изгиб Для испытаний на изгиб использовалась машина для испытаний на прочность (MATEST srl, Италия, грузоподъемность 150 кН). Кроме того, анализировались микроскопические изображения испытуемых образцов.
Автоматическая машина для испытаний на сжатие (MATEST s.r.l.)
Испытание на прочность при сжатии
Прочность бетона на сжатие является мерой его способности противостоять статической нагрузке, когда последняя стремится его раздавить.Испытание прочности на сжатие является наиболее распространенным; многие желательные характеристики бетона связаны с его прочностью, и, следовательно, прочность бетона на сжатие при проектировании конструкций имеет первостепенное значение. Кроме того, прочность на сжатие дает хорошее и четкое представление о том, как на прочность влияет увеличение объемной дозировки волокна в испытуемых образцах. В AS 1012 упоминается, что образцы для прочности на сжатие должны иметь диаметр 150 мм и высоту 300 мм, но это относится только к максимальному размеру заполнителя более 20 мм, в то время как кубический образец со стороной 150 мм (AS 1012 2002 г. ), а интенсивность нагрузки качественно определяется в мегапаскалях.Процедура испытания на сжатие проводилась в соответствии с методом испытаний AS 1012.9.
Испытание на прочность при изгибе
Прочность бетона на изгиб является мерой его способности сопротивляться изгибу и может быть выражена в терминах модуля разрыва. Таким образом, при проведении испытаний бетона на прочность при изгибе с использованием несущих блоков использовался метод двухточечной нагрузки, который гарантировал, что силы, приложенные к балке, были перпендикулярны поверхности образца и прикладывались без эксцентриситета.Во время испытания реакция всегда была параллельна направлению приложенной силы. Процедура испытаний проводилась в соответствии с методом испытаний ASTM C 78-00. Расстояние до точки нагрузки (l) составляет 133 мм, а до точки опоры (L) – 400 мм, при этом нагрузка прикладывалась непрерывно и без какого-либо удара с постоянной скоростью до точки разрыва. Прикладывайте нагрузку со скоростью, которая постоянно увеличивает предельное напряжение волокна 1,21 МПа/мин. Наконец, были получены результаты в виде полной нагрузки в килоньютонах и интенсивности нагрузки в мегапаскалях.
Испытание на прочность при растяжении
Исследование механических свойств бетона может быть обоснованно представлено посредством анализа прочности на растяжение. Хрупкость и малая прочность бетона на растяжение делают бесперспективной борьбу с прямым напряжением. Следовательно, измерение прочности на растяжение является обязательным для определения нагрузки, при которой бетонные элементы могут треснуть; следовательно, растрескивание происходит из-за нарушения натяжения. Испытания на расщепление (иногда называемые испытаниями на растяжение при расщеплении) являются хорошо известными косвенными испытаниями, используемыми для определения прочности бетона на растяжение.Процедура испытания состоит в приложении сжимающей линейной нагрузки вдоль противоположных образующих бетонного цилиндра, расположенного с горизонтальной осью между сжимающими плоскостями. Испытание на прочность на растяжение при раскалывании проводили в соответствии с методом испытаний ASTM C 496/M496.
Конструкция сверхвысокоэффективной бетонной смеси, армированной фиброй, в центральной Канаде
Цитируется по
1. Использование сверхвысококачественного бетона для производства стандартных крупных заполнителей
2. Уменьшение усадки сверхвысококачественного бетона, подвергнутого воздействию различных условий смешивания и отверждения
3. Характеристика сверхвысококачественных бетонных материалов для применения в модульных конструкциях
4. Исследование ограничений применения теста ускоренной миграции до UHPFRC со стальными волокнами
5. Баллистическая стойкость панелей UHPFRC при воздействии бронебойных снарядов
6. Новая технология смешивания бетона со сверхвысокими характеристиками с предварительной сухой принудительной укладкой
7. Реакция на изгиб гибридных соединений настила сверхвысокого качества бетона (UHPC), изготовленных из местных материалов
8. Численное моделирование бетона Прочность сцепления с UHPC
9. Влияние высокой дозировки пластификатора на сверхвысококачественный фибробетон (UHPFRC)
10. Механические свойства сверхвысококачественного фибробетона, содержащего синтетические и минеральные волокна
11. Дозирование экономичных смесей UHPC
12. Теоретическое исследование термомеханического поведения облицовки тоннелей во время пожарной разработки RABT
13. Модифицированные испытания ускоренной миграции хлоридов для UHPC и UHPFRC с PVA и PVA.
14. Длина арматурных стержней, залитых в реактивный порошковый бетон (RPC) Состав смеси и реакция на изгиб сверхвысококачественного фибробетона (UHPFRC)
17. Использование упаковки частиц и статистического подхода для оптимизации экологически эффективного сверхвысококачественного бетона
18. Исследование термического отверждения в полевых условиях сверхвысокопрочного бетона с использованием теплоты гидратации
19. Методы производства для надежного строительства конструкций из сверхвысокопрочного бетона (UHPC)
20. Разработка бетона со сверхвысокими характеристиками с использованием местных материалов
21. Циклическое поведение соединений внахлестку, усиленных фибробетоном со сверхвысокими характеристиками
22. Реакция тонких мишеней UHPFRC с различной объемной долей волокна на деформируемый снаряд Воздействие
23. Влияние длины волокна на энергию разрушения СВПФУ
24. Экспериментальное исследование испытания на сжатие куба и цилиндра СВВПФ при повышенной температуре
25. Экспериментальное исследование поведения при продавливании высокопрочных сталефибробетонных плит с учетом направлений заливки
26. Экспериментальное исследование распределения напряжения сцепления и прочности соединения в неограниченных соединениях внахлест UHPFRC при прямом растяжении
27. Производство ультра — бетон с высокими эксплуатационными характеристиками с использованием обычных материалов и методов производства
28. Термогравиметрический анализ полиоксиметиленовой фибры, используемой для модификации цементного бетона: Термогравиметрический анализ полиоксиметиленовой фибры, используемой для модификации цементного бетона
29. Железобетонные бетонные барьеры из сборных волокна с интегрированным тротуаром
30. Прочность на основе облигации образцов сращиваний на коленях в UHPFRC
31. древесина-бетонные композитные системы с пластичными соединениями
32. Сращивание натяжения Бетон со сверхвысокими характеристиками, армированный фиброй
33. Проблемы, связанные с характеристикой межфазной связи в бетоне со сверхвысокими характеристиками с последствиями для практики восстановления мостов
34. Состав смеси UHPFRC и его реакция на удар снаряда
35. Поведение различных типов бетона при ударе и квазистатической нагрузке
36. Сборные мостовые парапеты из фибробетона со сверхвысокими характеристиками
37.