Как класть керамзитобетонные блоки: правила и нюансы
Инновации в строительстве
Современное строительство претерпело значительные изменения. Это связано в первую очередь с использованием новых строительных технологий и материалов. Революционные изменения позволили улучшить качество возводимых строений и уменьшить трудовые затраты. Немаловажную роль в этом сыграло использование блоков, вместо кирпичей. Блоки производят по различным технологиям из цемента, керамзитобетона и прочих материалов.
Характеристики керамзитобетонных блоков
Внешне керамзитобетонные блоки представляют собой легкие строительные камни из особо прочного керамзитобетонного состава.
Основной особенностью керамзитобетонных блоков есть их большая влагоустойчивость. При полном погружении в воду керамзитобетон на 200% меньше впитывает воду, нежели поризованный бетон. Такой коэффициент влагопоглощения свидетельствует о том, что материал имеет хорошие теплосберегающие свойства.
Расчеты показали, что теплопроводность кладки из керамзитобетонных блоков в 1,5 раз меньше теплопроводности фасада из дырчатого клинкерного кирпича такого же сечения. Керамзитобетон огнестойкий, экологичный и имеет отличную несущую способность. Имея такие характеристики, керамзитобетонные блоки получили большую популярность в таких государствах, как Швеция, Нидерланды, Чехия, Финляндия, Германия, Норвегия. 40% индивидуального строительства в этих странах выполнено с использованием керамзитобетона.
Правила и нюансы кладки блоков из керамзитобетона
Если посмотреть, как кладут керамзитобетонные блоки, то создается впечатление, что собирается детский конструктор «LEGO». Благодаря тому, что блоки по размеру больше чем кирпичи и легче, то процесс кладки происходит значительно быстрее.
Процесс кладки во многом идентичен с кладкой кирпича. Для работы используют кладочный цементный раствор, блоки смачивают для улучшения сцепления с веществом в процессе кладки.
Перед тем, как класть керамзитобетонные блоки обязательно выполняют выравнивание.В качестве гидроизоляции выкладывают рубероид в два слоя.
Начинать кладку блоков надлежит с углов строения, последовательно продолжая ее по всему периметру. Для увеличения прочности швы желательно укрепить стальной армирующей сеткой.
Последовательность работ:
- Нанесите цементный раствор на блок равномерным слоем;
- Положите блок на раствор к краю ранее уложенного блока, отступив от него около 5 см;
- Скользящим движением придвиньте блок к уже уложенному так, чтобы между ними образовался вертикальный шов толщиной около 1 см.
Как класть керамзитобетонные блоки, чтобы исполнить кладку с высочайшим качеством? Во-первых, очень важно правильно уложить первый ряд. Перед этим обязательно выполнить гидроизоляцию между кладкой и фундаментом и выровнять поверхность с помощью цементного раствора. Во-вторых, при кладке керамзитобетона используется меньшее количество цементного раствора. Эта особенность позволяет достигнуть значительной экономии. Это же можно сказать и о расчете стоимости керамзитобетонных блоков по сравнению с традиционным кирпичом. Блоки использовать дешевле.
Отделка
Поверхность керамзитобетонных блоков совместима с большинством способов конечной отделки. Их разрешено штукатурить, облицовывать декоративной плиткой либо кирпичом. Иногда для повышения энергетической эффективности и понижения тепловых потерь сооружений комбинируются разные методы. Одна из таких методов – это вентилируемый фасад. Возможен вариант отделки внутренних поверхностей стен как «мокрым» этак и «сухим» методом.
Стены из керамзитобетонных блоков — кладка, возведение, строительство
Среди видов высококачественного строительного материала для возведения стен особого внимания заслуживают керамзитобетонные блоки – доступный, легкий, прочный, долговечный и поддающийся обработке стройматериал. Возведением зданий различного назначения из керамзитобетонных блоков и занимается компания «Проект». Мы оказываем профессиональные строительно-монтажные услуги по невысоким ценам жителям Москвы и Подмосковья.
Керамзитобетонные блоки: общие сведения и характеристики
Керамзитобетон относится к классу легких бетонов, хотя если сравнивать вес изделий из него с изделиями из газобетона, полистиролбетона или пенобетона, то он будет в 1,5 – 2,5 раза больше. Вес стандартного изделия 16 -17 кг.
Изготавливают стеновые блоки в соответствии с нормативами ГОСТ исключительно из природных материалов: керамзит, вода, наполнители, песок и цемент. Первый компонент в составе – это пористый материал, получаемый при помощи обжига глинистого сланца или глины.
Производятся керамзитобетонные блоки из цемента марки М 50 – М 500, щебня (гравия) самых различных фракций (от 5 мм до 40мм) по технологии вибропрессования. Смешенные с водой, песком и цементом щебневые шарики «склеиваются» друг с другом, образуя очень прочный, экологически безопасный и достаточно легкий стройматериал. В зависимости от того, какие виды компонентов были использованы при изготовлении керамзитобетонных блоков, проявляются и их физико-технические качества:
- Плотность – от 350 до 1800 кг/м3.
- Паропроницаемость (нормальные условия) – от 0,1 до 0,3 мг/мчПа.
- Морозостойкость – от 25 до 500 (для перегородочных блоков не определяется).
- Испытанная эксплуатационная влажность материала – от 5 до 7%.
- Прочность на сжатие – от 0,5 до 15 мПа.
- Огнестойкость: изделия сохраняют свои качества под воздействием открытого огня до 10 часов.
- Теплопроводность (расчетная) кладки – от 0,11 до 0,7 Вт/м2.
- Процент усадки стены керамзитобетонных блоков – 0%.
- Процент водопоглощения – до 50%.
- Время остывания стены – от 65 до 90 часов.
Применение керамзитобетонных блоков и их разновидности
Физико-технические качества определяются процентным содержанием керамзита и его фракцией в составе материала. Чем выше процент содержания, тем меньше характеристики теплопроводности и прочности. При этом свойства изделий подразделяют данный вид стройматериала на типы, от которых зависит область применения данного материала. Наши специалисты рекомендуют использовать керамзитобетонные блоки по назначению:
- Теплоизоляционные.
Наименее прочный и механически стойкий вид материала, плотность которого не превышает 700 кг/м3, а прочность – до 25 мПа. Используются в качестве надежного теплоизоляционного материала, для возведения межкомнатных перегородок.
- Конструктивные. Наиболее прочный материал, имеющий плотность от 1200 до 1800 кг/м3 при прочности – от 10 до 15 мПа. Эти блоки имеют максимальный коэффициент морозостойкости и используются для возведения несущих стен.
- Конструктивно-теплоизоляционные. Блоки используются для возведения однослойных стеновых панелей, перегородок, и прочего. Плотность этого материала составляет 800- 1200кг/м3 при прочности – до 10 мПа.
Также различают монолитные и пустотелые блоки. Пустотелые изделия позволяют строить теплые стены конструкций любого назначения, а монолитные применяют для кладки каминов, печей или дымоходов.
Стены из керамзитобетонных блоков: особенности
Для создания оптимально комфортного теплового режима в доме в условиях центрального региона необходимо возводить стены толщиной не менее 0,65 метров с обязательным утеплением.
Дом со стенами из керамзитобетонных блоков будет обладать:
- значительными теплотехническими и звукоизоляционными качествами;
- значительной воздухопроницаемостью. Способность стен сохранять в комнатах оптимальный температурный режим;
- значительной влагостойкостью, сопротивляемостью агрессивным средам;
- высокими показателями огнестойкости;
- экологической безопасностью.
Строительство стен из керамзитобетонных блоков
Возведение стен из керамзитобетонных блоков требует некоторых специальных знаний и нередко принятия конструктивных решений. Эту работу лучше доверить профессионалам. Специалисты нашей компании оказывают доступные профессиональные услуги по строительству сооружений в Москве и Подмосковье.
Начинают кладку стен из керамзитобетонных блоков с углов и продолжают рядами по периметру. Однако прежде чем положить первый ряд, стоит позаботиться о качественной гидроизоляции. Для этого на фундамент укладывается двойной слой рубероида или других изоляционных материалов.
Также стоит помнить, что:
- использовать обычный молоток каменщика при работе с керамзитобетонными блоками нельзя. Лучше приобрести специальный резиновый молоток;
- армировать стены необходимо специальной арматурой. Ее укладывают на завершенный ряд по периметру во всю стеновую длину. Кладка следующего ряда осуществляется по арматуре, которую укладывают через каждые 3-5 рядов;
- кладку каждого ряда из блоков необходимо проверять уровнем, поскольку для этого стройматериала свойственна незначительная конусность;
- кладку наружных и внутренних стен стоит проводить одновременно, не забывая об арматуре;
- осуществляя кладку, нельзя забывать о цепной перевязке швов по вертикали;
- последний ряд завершает армопояс.
При четком соблюдении правил, учете особенностей работы с этим видом стенового материала, возведенная конструкция прослужит долгие годы.
Как правильно класть керамзитобетонные блоки
Керамзитовые бетонные блоки – одни из первых в ряде стеновых блоков появились как альтернатива кирпичу в малоэтажном строительстве. У них прочность на сжатие и плотность почти такая, как у кирпича. Но из-за рыхлости керамзита эти блоки более хрупкие.
Поэтому несущие стены из керамзитобетона можно выполнять только до трех этажей. Их теплопроводность ниже в два раза, чем у кирпича, но более высокая гигроскопичность. Качественные керамзитобетонные блоки Рязань можно заказать на сайте компании ooo-bloki.ru.
Поэтому для стен из керамзитобетона требуется наружная отделка. Керамзитобетонные блоки производятся полнотелые и пустотелые. Для перегородок используют блоки с пазовым гребневым соединением.
Фундаменты под керамзитобетонные стены
Под такие тяжелые стены необходимо выполнять ленточный фундамент из бетона по стальному каркасу, или из фундаментных бетонных блоков ФБС (не керамзитовых), с глубиной залегания ниже глубины промерзания в регионе.
Ширина фундамента должна быть больше ширины стены на 5 см и более.
После полного созревания бетона (около 28 дней) выполняется обмазочная гидроизоляция фундамента, а по верхней его части – рулонная в виде рубероида.
Кладка стен из керамзитобетонного блока
Ширина стен жилого здания по проекту чаще всего выбирается в один блок – 0,4 м, с последующим утеплением по фасаду, или с параллельной облицовкой снаружи в полкирпича.
Реже, хоть это и лучше, но дороже, кладут стены в полтора блока.В пол блока кладут только летние не отапливаемые хозяйственные здания и помещения, или более поздние надстройки и мансарды по армирующему поясу с дополнительным утеплением.
Первый ряд кладки начинается с самого высокого угла в периметре.
Тогда общая горизонталь в ряду выровняется, и дальше можно будет поддерживать строгую горизонтальность каждого ряда.
Все перегородки, которые заложены в проекте, лучше выкладывать одновременно со стенами – для общей перевязки ряда по периметру.
Кладка каждого последующего ряда начинается с углов, а дальше по уровню заполняется ряд между углами.
Через 3 – 4 ряда проводится армирование по периметру или двумя рядами арматуры 6 – 10 мм, или кладочной сеткой.
Над дверными и оконными проемами заливаются в опалубке бетонные перемычки по стальному каркасу, или монтируются готовые стандартные перемычки.
В составе керамзитобетонных блоков
Могут поставляться заготовки перемычек с полостями под каркас и заливку бетона.
Каждый этаж стен из керамзитобетона должен обвязываться монолитным бетонным армирующим поясом по ширине стены. Высота его рассчитывается по проекту и обычно равна 0,2- 0,3 м.
Армирующий пояс служит основой для монтажа перекрытий, для кладки следующего этажа, или для монтажа мауэрлата и стропильной системы кровли.
характеристика, достоинства и недостатки.

Керамзитобетонные блоки по праву считаются биоблоками. Они состоят из глины, цемента, песка и гравия. Их используют при возведении зданий и сооружений, каркасов и гаражей. По характеристикам и ценовой политике они представляют тесную конкуренцию кирпичу.
Характеристика керамзитобетонных блоков
Современное общество постоянно сооружает новые здания и сооружения под свои нужды. На поиск оптимального варианта стройматериалов потрачены годы. Для них задана высокая планка: надежность и долговечность, доступность и простота использования.
Так, для кирпича, альтернативным аналогом приходятся керамзитобетонные блоки. Они широко используются в Европе. В таких странах, как Австрия, Германия, Дания.
Материал изготавливается из экологически чистого сырья. Основными элементами керамзитобетона является обожженная глина, вода и бетон. При замешивании последнего добавляют песок и/или щебень для прочности. В результате получается жесткий и долговечный материал. Но который характеризуется большим уровнем теплопроводности. А значит, он не способен удерживать тепло внутри помещения. Поэтому используется дополнительный материал для облицовки и получаются утепленные керамзитобетонные блоки.
Керамзит производят в специальных крутящихся печах. Он отличается способностью быстро впитывать влагу. Что актуально для строительства теплиц, для выращивания сельскохозяйственных культур. А твердость конструкции достигается методом полусухого пресса и следующего за ним пропаривания. Каждая гранула вещества покрывается коркой и приобретает вид застывшей пены.
Так, средняя плотность итогового блока варьируется от 450 до 1750 кг/м³.
Керамзитобетонные блоки применяются для следующих целей:
- возведение наружных и внутренних стен зданий,
- закладка фундамента,
- организация вентиляционных шахт,
- сооружение межкомнатных перегородок,
- заполнение каркаса при монолитном строительстве.
Свойства данных блоков регламентируются ГОСТом 6133-99 «Камни бетонные стеновые. Технические условия».
Стандарт указывает, что поверхность материала бывает рифленая, колотая, шлифованная и гладкая.
А по назначению камни делятся на рядовые и лицевые. Первые требуют обработки дополнительным облицовочным материалом. Вторые – изготавливают с одной или двумя гранями, которые выполняют декоративную функцию.
Керамзитобетонные блоки обычно выпускаются в форме прямоугольного параллелепипеда. Но по согласованию с заказчиком, возможно выполнение других вариантов.
Вне зависимости от размера керамзитобетонного блока, его вес не превышает 31 кг.
Размеры керамзитобетонных блоков
Согласно ГОСТа 6133-99 для строительства изготавливают блоки определенных размеров. Стеновые керамзитобетонные блоки производят, ориентируясь на следующие параметры:
- высота 13,8 см,
- ширина от 1,4 до 2,9 см,
- длина от 0,9 до 2,9 см.
А для сооружения перегородок используют керамзитобетонные блоки со следующими размерами:
- высота 18,8 см,
- ширина 9 см,
- длина от 1,9 до 5,9 см.
Углы блоков делают прямыми или закругляют.
Расчет керамзитобетонных блоков проводится на этапе составления проекта строительства.
Сам материал бывает полнотелый и пустотелый. Последний вид формируется с вертикальными сквозными или не сквозными полостями, которые равномерно распределяются по площади блока. Полнотелые керамзитобетонные блоки характеризуются плотной структурой. Они без пустот и отверстий. Обычно их используют для укладки фундамента.
Производитель делает маркировку материала, где приняты обозначения:
- К – камень,
- С – сфера применения для кладки стен,
- П – использование для внутренних перегородок,
- Л и Р – лицевой или рядовой тип блока,
- ПС – пустотелость материала.
По прочности марки из тяжелого бетона делятся по убыванию твердости от маркера 300 до 50. А из легкого аналога – от 100 до 25.
Также указывается уровень морозостойкости, где F200 – максимальный показатель, а F15 – минимальный.
Прежде чем купить керамзитобетонные блоки, необходимо проверять соответствие условного обозначения на них нормам и фактическим параметрам материала.
Преимущества керамзитобетонного материала
Любой строительный элемент имеет свои плюсы и минусы. Исходя из них, необходимо выбрать оптимальный вариант для заданного вида работ.
Специалисты определяют ряд достоинств керамзитобетонные блоков. Вот основные из них:
- Воздухопроницаемость материала через гранулы.
- Экологически чистый строительный материал.
- Теплоизоляция сохраняет до 70% тепла внутри помещений, по сравнению с бетонным аналогом.
- Влагоустойчивость, в отличие от цементного материала.
- Минимальное количество кладочного раствора для возведения стен.
- Экономия на почасовой оплате труда рабочих. Поскольку кладка данным материалом происходит в 4 — 5 раз быстрее, чем при использовании кирпича.
- Дома из керамзитобетона отличаются долговечностью. Они не подвержены коррозии, гниению и не горят при пожаре.
- Материал отличается большим уровнем шумоизоляции, по сравнению с бетонными аналогами.
- Керамзитобетон отличается химической стойкостью к щелочам и сульфатам.
- Относительно невысокая цена керамзитобетонных блоков при их большом объеме: одна единица заменяет 5 – 7 кирпичей.
- В отличие от пено-газобетона, керамзитобетон хорошо держит дюбели без специальных крепежей.
- Простота производства доступна для самостоятельного выполнения.
- Кладка поддается легкой облицовке и обшивке другими материалами.
- Прочность до 1800 кг/м³ и морозоустойчивость до -40 °С.
- В силу своей прочности, в процессе работы материал не деформируется и не дает трещин.
К технологии изготовления керамзитобетонных блоков выставлены высокие требования. Так как из них возводят несущие стены. Поэтому они характеризуются качеством и надежностью.
По праву считается хорошим строительным материалом. На его долю приходит 7% сооружений в постсоветских странах и до 40 % за рубежом.
В целом, отечественные мастера оставляют одобрительные отзывы о керамзитобетонных блоках. Делая акцент на том, что потребуется еще лет 10 – 15, чтобы они закрепили свои позиции в строительном деле.
Преимущества керамзитобетонных блоков позволяют снизить цену и сэкономить время строительства. При этом получив надежную и долговечную постройку.
Недостатки керамзитобетонных блоков
При положительных сторонах керамзитобетону свойственны и относительные недостатки:
- Повышенная пористость, по сравнению с твердым монолитным бетоном. В силу чего снижаются физико-механические характеристики материала. В том числе и плотность. Поэтому при закладке фундамента и строительстве высокоэтажных домов, предпочтительней использование чистого бетона.
- Необходимость внешней теплоизоляции для сохранения комфорта в холодную пору.
- Недобросовестность изготовления блоков. Иногда производители используют некачественное сырье и не выдерживают требований ГОСТа. А в открытом доступе нет полной технологии самостоятельного изготовления.
- Несмотря на относительно малый вес материала, здания из керамзитобетона требует прочного фундамента. А значит, не получится сэкономить на несущей конструкции.
Керамзитобетонные блоки своими руками
Для экономии средств, умельцы изготавливают керамзитобатонные блоки самостоятельно. Также на этом можно хорошо заработать. Процесс не сложный, но требует соблюдение пропорций и инструкций.
Для самостоятельного приготовления потребуется следующий материал:
- песок 35 кг,
- деревянные доски для опалубки,
- керамзит с фракциями 5 – 7 мм весом 70,85 кг,
- цемент 12 кг,
- вода 11,7 л,
- металлическая пластина для выкладывания материала,
- емкость на 150 л и инструмент для замешивания смеси.
Обратите внимание, что приведено соотношение сырья для изготовления 12 – 13 пустотелых блоков. Произведите соответствующие расчеты для необходимого вам количества итогового материала.
Сначала сделайте форму под блоки из дерева или металла толщиной 4 – 5 мм. Для формирования внутренних полостей достаточно материала в 3 мм.
Замесите смесь керамзитобетона до состояния пластилина. Это можно сделать самостоятельно в емкости при помощи лопаты. Для большого производства лучше арендовать станок для керамзитобетонных блоков, представленный на фото.
Залейте форму смесью.
Для высыхания блоки размещаются на металлическую основу. В течение недели на них не должна попадать влага и прямой солнечный свет. В жару их необходимо смачивать водой и покрыть сверху полиэтиленом.
По факту материал сохнет за 48 часов. Но мастера утверждают, что лишь через 3 – 4 недели керамзитобетон приобретает максимальную прочность.
Как класть керамзитобетонные блоки
Процесс кладки керамзитобетонных блоков во многом схож с кладкой кирпича. Но отличается рядом особенностей. Например, необходимостью перевязки швов.
Для укладки потребуется следующие инструменты и материал:
- мерная рулетка,
- емкость и инструмент для замешивания клея, к примеру: ведро и лопата,
- уровень для выравнивания блоков,
- отвес,
- деревянные рейки,
- керамзитобетонные блоки,
- рубероид,
- бичевая веревка,
- резиновый или деревянный молоток для укладки,
- вода,
- клей,
- пила для резьбы по стройматериалу.
- Фундамент выравнивается при помощи нивелира и цементной смеси. После не него стелется рубероид в два слоя. Он будет выполнять функцию гидроизоляции. Поверхность вторично выравнивается при помощи нивелира или уровня.
- Начинать укладку необходимо с углов строения. В них размещаются уровневые рейки с привязанной к ним бечевкой, которая будет служить направляющей для следующих рядов блоков.
- Блоки обрабатываются водой, после чего на них наносится клеящий раствор.
Достаточно слоя в 2 см вещества. Это делается для того, чтобы пористый материал минимально впитывал в себя кладочный раствор.
- Очередной керамзитобетонный блок укладывается на расстоянии 4 – 5 см от торца предыдущего. После надавливанием вниз и по направлению к стыку блоки выравниваются. Придать прочности их крепежа осуществляется при помощи простукивания поверхности молотком.
- Каждые 4 – 5 рядов крепится арматурная сетка для придания конструкции большей прочности.
- При необходимости уменьшить размер материала используют специальную пилу.
Специалисты рекомендуют параллельно возводить внутреннюю и внешнюю стены.
После укладки каждого ряда нивелиром проверяется его параллельность относительно земли.
Рекомендации при проектировании каменных конструкций из блоков
- При возведении невысоких зданий, необходимо использовать крупнопористые керамзитобетонные блоки. Для внешних стен их морозостойкость должна быть не ниже F50.
При строительстве дополнительного внутреннего ряда подобного требования нет.
- Для скрепления блоков используют тонкослойные кладочные растворы. При этом толщина швов выдерживается в размере 1 – 2,5 мм.
- Возможно также применение тяжелых клеящих смесей. Толщина швов между керамзитобетонных блоков в таком случае достигает 1 – 1,2 см.
- Стены шириной в 30 см, необходимо проектировать в один ряд камня. При большем размере – в один или два блока.
- Выполнение двухуровневой кладки бывает плашкового и тычкового типа перевязки. Размер первого вида должен составлять не менее 1/5 толщины стены.
- Примыкание стен друг к другу необходимо производить встык с жесткими или скользящими соединениями. Например, при помощи металлических направляющих и профилей.
- Для обеспечения требуемого уровня тишины в помещении, используйте специальный звукоизолирующий материал.
- В зависимости от величины нагрузки на конструкцию, оснастите ее обычной или жесткой арматурой.
- Проектирование и возведение сооружения лучше предоставить специалисту. А для качественного и своевременного выполнения контролировать процесс.
- Убедитесь, что техническая документация составлена правильно, с учетом норм безопасного строительства.
- При проектировании и строительстве каменных конструкций, обратитесь к видео-обзорам по укладке керамзитобетонных блоков.
Калькулятор керамзитобетонных блоков | сколько керамзитобетонных блоков 1м3 1м2
Дополнительная информация для расчёта строительных блоков
Онлайн калькулятор керамзитобетонных блоков помогает рассчитать количество блоков для строительства дома, дачи, бани, гаража достаточно точно, сколько керамзитобетонных блоков 1м3 1м2. Строительный калькулятор будет полезен как специалисту по строительству, так и обычному обывателю без опыта. Вы можете мгновенно рассчитать необходимое количество блоков, раствора и кладочной сетки, тем самым не покупать лишнего материала и сэкономить деньги и время.
Пояснение расчёта керамзитобетонных блоков
Калькулятор блоков прост в использовании, и поможет рассчитать смету строительных материалов, следуя данной инструкции.
Расчёт периметра строительных блоков — периметр рассчитывается сложением всех стен дома, в случае прямоугольной формы дома: A+D+A+D, вводим получившийся результат, единица измерения метр.
Высота стены по углам — с помощью измерения высоты стены по углам или имеющихся данных, вводим высоту в соответствующее поле, единица измерения метр.
Выбираем толщину стен кладки — в зависимости от толщины стен, в блок или полблока, отмечаем необходимое значение. Толщина раствора в кладке — Толщина раствора в кладке выбрана по умолчанию 12 мм согласно ГОСТ 6133-99, и этот пункт можно не трогать, расчёт будет по умолчанию.
Кладочная сетка — при кладке керамзитобетонных блоков рекомендуется класть сетку для придания стены дополнительной прочности и устойчивости. По умолчанию сетку кладут через два ряда, но также возможны другие варианты. Сетка рассчитывается в погонных метрах и её количество зависит от толщины стены, учтите это при покупке сетки.
Фронтоны — при необходимости, вы можете добавить размеры фронтонов (в метрах), для этого нужно ввести высоту, ширину и количество фронтонов, это потребуется для более точного расчёта материалов.
Вычет пространства под окна и двери — любой дом состоит из окон и дверей и их учёт снижает количество керамзитобетонных блоков и других строительных материалов, тем самым экономит ваши деньги. Вводите размеры и их количество, единица измерения метр.
Рассчитать количество керамзитобетонных блоков — при нажатии кнопки рассчитать, появиться информация: общая площадь кладки блоков в м3, количество кладочной сетки в метрах погонных, объём раствора на всю кладку и общее количество керамзитобетонных блоков. При дополнительном изменении данных, вам потребуется ещё раз нажать кнопку рассчитать, и вы получите новые результаты.
Размерный эффект в испытаниях на прочность при сжатии образцов с сердечником из легких заполнителей материалов
(Базель). 2020 март; 13(5): 1187.
Факультет гражданского строительства Краковского технического университета, 31-155 Краков, Польша; lp.ude.kp@alagamodlПоступила в редакцию 15 января 2020 г.; Принято 3 марта 2020 г.
Лицензиат MDPI, Базель, Швейцария. Эта статья находится в открытом доступе и распространяется на условиях лицензии Creative Commons Attribution (CC BY) (http://creativecommons.org/licenses/by/4.0/).Эта статья была процитирована другими статьями в PMC.Abstract
Целью данной статьи является обсуждение непризнанной проблемы масштабного эффекта при испытаниях на прочность при сжатии образцов из легкого заполнителя (LWAC) с сердцевиной на фоне имеющихся данных о влиянии для нормального бетона (NWAC) ). При анализе масштабного эффекта учитывали влияние гибкости ( λ = 1,0, 1,5, 2,0) и диаметра (d = 80, 100, 125 и 150 мм) образцов с керном, а также типа легкого заполнителя. (керамзит и агломерат) и тип цементной матрицы (в/ц = 0.55 и 0,37). Анализ результатов для четырех бетонов с легким заполнителем не выявил масштабного эффекта в испытаниях на прочность при сжатии, определенных на образцах с сердечником. Ни гибкость, ни диаметр сердцевины, казалось, не влияли на результаты прочности. Этот факт следует объяснить значительно лучшей структурной однородностью испытанных легких бетонов по сравнению с обычными. Тем не менее, были четкие различия между результатами, полученными на формованных образцах и образцах с сердечником одинаковой формы и размера.
Ключевые слова: эффект масштаба, размер образца, легкий бетон, легкий заполнитель, керамзит, спекшаяся зольная пыль, прочность на сжатие материалов в мире на протяжении десятилетий. Важнейшими преимуществами его применения по сравнению с обычным бетоном (НББ) того же класса прочности являются:
Более высокая теплоизоляция и лучшее звукопоглощение [1,2,3];
Возможность строительства конструкций с большими пролетами и/или большей высотой и/или меньшими сечениями конструктивных элементов [4,5,6];
Возможность устранения аутогенной усадки [7,8,9];
Повышенная износостойкость: более высокая огнестойкость, возможно более высокая морозостойкость, возможно более низкая карбонизация и, возможно, более низкая водопроницаемость [10,11,12,13,14,15,16];
Меньшая вероятность растрескивания в результате усадки, ползучести, термической деформации или нагрузок [17,18,19,20].
Лучшая долговечность и меньшая вероятность растрескивания LWAC в основном являются результатом лучшей однородности структуры LWAC.
Тем не менее, легкий заполнитель редко используется в качестве конструкционного материала по сравнению с наиболее популярным вариантом — обычным бетоном. Важнейшими причинами такой ситуации являются некоторые технологические проблемы при выполнении конструкции ЛВБК, т.е. повышенный риск потери удобоукладываемости и расслоения бетона, а также, как правило, более высокая цена за единицу объема, а главное отсутствие разносторонних процедур проектирования, исполнения, тестирование и оценка.Между тем, использование конструкционных легких бетонов, изготовленных из промышленных или переработанных заполнителей, в ближайшем будущем должно получить широкое распространение в связи с истощением запасов природного заполнителя и упором на устойчивые, менее энергозатратные конструкции.
Влияние размера и формы испытуемых образцов на оценку свойств LWAC является одной из менее признанных в качественном и количественном отношении проблем. Как правило, согласно теории Гриффита и Вейбулла [3, 21], разрушение начинается с любого критического дефекта («наиболее слабой цепи»), содержащегося в материале.Поэтому образцы большего объема обнаруживают большую вероятность наличия такого дефекта и, как следствие, характеризуются меньшей прочностью. Более того, хорошо известно, что эффект масштаба более выражен, если материал менее однороден [3,21,22]. Однородность бетона в основном зависит от распределения включений (заполнителя) в цементной матрице, размера и формы заполнителя, разности прочности и модуля упругости заполнителя и цементной матрицы, а также связи между этими двумя компонентами.Масштабный эффект определяется также геометрическими характеристиками самих образцов. Из-за значительных различий жесткостей бетонного образца и плит машины для испытаний на сжатие в зоне их контакта одноосное напряженное состояние нарушается трением и давлением. В результате образцы с большей площадью поперечного сечения обладают меньшей прочностью.
В то же время форма поперечного сечения образца и его гибкость ( λ = высота ( h ) / размер поперечного сечения ( d )) не имеют значения.Круглое поперечное сечение обеспечивает более равномерное распределение напряжений по сравнению с квадратным, поскольку на его разрушение меньше влияет торцевое закрепление образца. При этом на прочность цилиндров меньше влияют свойства крупного заполнителя из-за более однородного состава бетона по круглой кромке по сравнению с образцами квадратного сечения, обнаруживающего более высокое содержание цементного теста в углах. Следовательно, при одинаковой гибкости и площади поперечного сечения цилиндрические образцы могут обладать большей прочностью, чем кубические [3].Уменьшение гибкости образца также способствует повышению прочности. Для обычного бетона типичное отношение прочности, определенное на формованных цилиндрах λ = 2,0 и 1,0, составляет ок. 0,85–0,95 и ниже для бетона меньшей прочности. Масштабный эффект в случае нормальных бетонов разных типов — простых, рядовых, самоуплотняющихся, высокопрочных и сверхвысокопрочных (реактивные порошковые бетоны), фибробетонов — доказан многочисленными исследованиями, например [23, 24,25,26,27,28,29,30,31,32,33,34].
Есть два общих вывода, вытекающие из этого исследования относительно нормального бетона: (1) чем выше прочность бетона, тем меньше эффект масштаба; (2) гибкость образца является решающим параметром, определяющим масштабный эффект.
В целом следует ожидать, что эффект масштаба LWAC будет менее выраженным по сравнению с NWAC, поскольку структура бетона с легким заполнителем обычно более однородна по сравнению с бетоном с нормальным весом. Основными причинами лучшей однородности ЛВАК являются:
Более правильная форма и размеры изготавливаемых заполнителей;
Меньшая разница между значениями прочности и модуля упругости пористого заполнителя и цементной матрицы;
Лучшее сцепление между пористым заполнителем и цементным тестом в результате лучшей адгезии, поглощения воды затворения пористым заполнителем и, в некоторых случаях, пуццолановой реакции.
Подтверждение менее выраженного масштабного эффекта LWAC было найдено в некоторых исследованиях [3,13,35,36,37]. Меньшая значимость масштабного эффекта в испытаниях на прочность на сжатие легких бетонов отражена также в классификации прочности по европейскому стандарту EN 206 [38]. Соотношение характеристической прочности LWAC, определенное на стандартных цилиндрических и кубических образцах ( f ck , cyl / f ck , cube ), полученное в классах прочности EN

Основное различие в масштабном эффекте, определяемом для формованных образцов и образцов с сердечником, заключается в отсутствии в этом последнем случае «стеночного эффекта». Кроме того, образцы, взятые из конструкции, обычно имеют другие, менее благоприятные условия уплотнения и твердения по сравнению с формованными образцами. Кроме того, процесс сверления образцов сам по себе может вызвать микротрещины в образцах с керном. В результате в EN 13791 [41] предполагается, что для всех типов конструкционных бетонов образцы с заполнителем показывают ок.Прочность на 15% ниже, чем у формованных. Между тем, благодаря лучшей структурной однородности по сравнению с обычным бетоном, LWAC в конструкции, даже если она массивная, может быть менее подвержена растрескиванию в результате как процесса бурения, так и повышения температуры при гидратации цемента. Как было показано в [17, 18], LWAC за счет лучшей структурной однородности обнаруживал меньшую концентрацию напряжений под нагрузкой и был менее подвержен растрескиванию по сравнению с обычным бетоном.В работе [19], посвященной исследованию соотношения начального и стабилизированного секущих модулей упругости, используемых в качестве показателя склонности бетона к микротрещинованию, доказана более высокая стойкость конструкционного легкого бетона к микротрещинованию или микротрещинованию под напряжением.
растрескивание, вызванное сверлением, по сравнению с конструкционным нормальным бетоном. С другой стороны, есть многочисленные отчеты об испытаниях, показывающие, что при высокой температуре LWAC работает лучше, чем NWAC. Например, результаты исследований, представленные в [15,16], показали, что LWAC при температурах до 200 °С и даже до 300 °С соответственно не показали развития микротрещин и снижения прочности.Поэтому более высокая температура (до 90 °С), развивающаяся при гидратации цемента в конструкции из ЛВАЦ, обычно не способна вызвать образование микротрещин. Более того, из-за внутреннего отверждения водой, находящейся в пористом заполнителе, LWAC в конструкции обычно проявляет меньшую чувствительность к внешним условиям отверждения по сравнению с обычным бетоном. Таким образом, структура легкого заполнителя в отвержденных в лабораторных условиях формованных образцах и в конструкции может быть менее разнообразной, чем в случае обычного бетона.Таким образом, можно ожидать, что разница между прочностными характеристиками, определенными для формованных образцов LWAC и образцов с сердечником, будет меньше, чем предполагается в EN 13791 [41] для всех типов бетона.
Хотя европейский стандарт EN 13791 [41] содержит принципы и рекомендации по оценке прочности бетона на сжатие на месте в конструкциях и сборных железобетонных элементах, он, скорее, ориентирован на бетон с нормальным весом, и некоторые конкретные данные, полученные в результате эффект масштаба приведен только для NWAC.Обычно считается, что диаметр сердцевины от 75 до 150 мм не влияет на результат испытания на прочность. Однако гибкость сердцевины влияет на достигнутое значение. В случае обычного и тяжелого бетона отношение прочности, определенное на полых цилиндрах λ = 2,0 и 1,0, можно принять равным 0,82, а для легкого бетона соответствующей информации нет. Для LWAC стандарт EN 13791 [41] рекомендует применять положения, действующие в месте использования, или подтверждать некоторые взаимосвязи путем испытаний.Такая ситуация вызвана отсутствием достаточных достоверных данных о масштабном эффекте образцов с керном LWAC, что подтверждается отсутствием литературных сообщений по этому вопросу. Между тем есть предпосылки, свидетельствующие о том, что, как и в случае литых образцов, масштабный эффект при испытаниях на прочность образцов с сердечником из НВАК менее значителен, чем в случае НВАК.
Поскольку не существует конкретных руководств по испытаниям и оценке прочности легкого бетона в конструкциях или сборных элементах, основной целью исследования была оценка непризнанного масштабного эффекта в испытаниях на прочность при сжатии, проведенных на образцах LWAC с сердечником.Дополнительной целью исследования было проверить, действительно ли предполагаемое снижение прочности на 15 % для образцов с сердечником по сравнению с формованными также для LWAC. Для этих целей были приготовлены четыре серии легкого заполнителя с замкнутой структурой разного состава, и для каждой серии бетона были испытаны как стандартные формованные образцы, так и 12 типов пустотелых цилиндров для определения прочности на сжатие. Выполненная программа исследований позволила провести количественную и качественную оценку эффекта масштаба образцов LWAC с сердечником на фоне имеющихся данных о влиянии для бетона нормальной массы. В нем также дана некоторая информация о выборе типов образцов с сердечником для получения надежных результатов прочности на сжатие легкого бетона, встроенного в конструкцию или сборный элемент. Такая информация может иметь практическое значение в случае оценки прочности на сжатие для структурной оценки существующей конструкции или оценки класса прочности на сжатие LWAC в случае сомнения.
2. Материалы и методы
Составы приготовленных ЛБК отличались типом легкого заполнителя (ЛЗА) и прочностью цементной матрицы, а также их объемной долей.Были выбраны два типа крупного легкого заполнителя: керамзит (EC) и спекшаяся зола-унос (SFA) (). Эти типы являются наиболее популярными в мире пористыми заполнителями, используемыми для конструкционного легкого бетона. Однако керамзит, использованный в этом исследовании, характеризовался гораздо меньшей плотностью частиц и более пористой внешней оболочкой по сравнению с спекшейся золой-уносом. Поэтому на практике такой заполнитель используют скорее для изготовления сборных элементов из теплоизоляционно-конструкционного бетона, чем для типовых конструктивных целей. В этом исследовании применение слабого заполнителя из керамзита было в основном направлено на то, чтобы показать эффект масштаба также в случае LWAC с более низкой прочностью и меньшей однородностью по сравнению с бетоном из спеченной золы-уноса. Основные свойства применяемых легких заполнителей представлены в . Заполнители перед нанесением на бетон предварительно увлажняли до уровня, соответствующего их впитыванию после погружения в воду на 1 ч. Такая влажность — 34,4 % и 17,0 % соответственно для керамзита и спекшейся золы-уноса, с одной стороны, предохраняла свежий бетон от потери удобоукладываемости, а с другой — обеспечивала хорошую адгезию цементного теста.
Легкие заполнители, используемые для испытуемого бетона: ( a ) спекшаяся зольная пыль и ( b ) керамзит.
Таблица 1
Свойства крупных легких заполнителей.
Агрегатный тип | фракция, мм | плотность частиц, кг / м 3 | водопоглощение,% | Сопротивление дробления, MPA | ||
---|---|---|---|---|---|---|
4/8 | 550 | 41.![]() | 1.4 | 1.4 | ||
Спеченная летающая зола | 4/8 | 1350 | 1350 | 24.3 | 8.0 |
Остальные из составных материалов для бетонных смесей были следующими: Портленд Цемент CEM I 42,5 R, природный песок 0/2 мм в качестве мелкого заполнителя, водопроводная вода, суперпластификатор. Цементные растворы, являющиеся цементными матрицами для приготовленных легких бетонов, характеризовались существенно отличающимся водоцементным отношением (В/Ц), равным 0. 55 и 0,37. Доля крупного легкого заполнителя в готовых бетонах колебалась от 52 до 55 % соответственно при В/Ц = 0,37 и 0,55. Составы бетонов представлены в .
Таблица 2
Составы растворов и легких бетонов. LWA, легкий заполнитель; ЭК, керамзит; SFA, спеченная летучая зола.
Серия | LWA Тип | Номинальная в/ц | Цемент, кг/м 3 | Вода, кг/м 3 | 4, кг / м 3 9LWA 1 , кг / м 3 | песок, кг / м 3 | |||
---|---|---|---|---|---|---|---|---|---|
9 | — | 0.![]() | 415 | 415 | 0.0 | — | 906 | ||
II Минометный | — | 0.37 | 912 | 335 912 | 335 | 18.4 | — | 937 | |
I EC | Exp.![]() | 0.55 | 338 | 186 | 0,0 | 308 | 406 | ||
II EC | Расшир. глина | 0,37 | 446 | 164 | 9,0 | 287 | 458 | ||
I SFA 9,0int 9,0149 зольная пыль | 0,55 | 338 | 186 | 0,0 | 749 | 406 | II SFA int летучая зола | 0,37 | 446 | 164 | 9.![]() | 699 | 458 |
Из каждой серии бетона были отлиты 6 стандартных кубов (d = 150 мм) и 6 цилиндров (d = 150 мм и h = 300 мм) в качестве эталонных образцов. Дополнительно для сравнения были отлиты стандартные кубы с растворами составов, соответствующих используемым в бетонах. Кроме того, были отлиты 4 больших бетонных блока размерами 400 × 600 × 1000 мм для сверления образцов с керном (). Образцы после извлечения из формы хранили до дня испытаний в условиях Т = 20 ± 2 °С, относительной влажности = 100 ± 5 %, соответствующих требованиям EN 12390-2 [42].В то же время большие блоки сбрызгивали водой, чтобы обеспечить одинаковые условия отверждения. Тем не менее в первые дни твердения температура блоков была значительно выше температуры стандартных формованных образцов. На верхней поверхности блоков она достигала 50 °С и 70 °С соответственно для бетонов I и II серий, что связано с большими размерами элементов. Внутренняя температура была, конечно, еще выше.
Подготовка бетонных блоков для колонкового бурения.
После 28 дней отверждения из блоков были высверлены керны и нарезаны на образцы в соответствии с EN 12504-1 [43].Были применены четыре буровые установки диаметром d = 80, 100, 125 и 150 мм (). Этот диапазон диаметров наиболее часто используется для оценки прочности конструкций на сжатие на месте. Ядра были разрезаны на образцы с гибкостью 1,0 и 2,0, обычно используемые для оценки прочности на сжатие на месте, и дополнительно 1,5. Типы и количество образцов, подготовленных для испытаний, представлены в и . Из каждой серии бетона вырезали по семь образцов с сердечником определенного типа (диаметра и гибкости): 6 в качестве базового набора для испытаний на масштабный эффект в условиях естественной влажности (в состоянии поставки) и 1 для контрольного испытания в сухом состоянии.Образцы в высушенном состоянии в основном применялись для испытания на плотность в высушенном состоянии (базового для легкого бетона), а затем их дополнительно использовали для дополнительной оценки эффекта масштаба. На практике образцы с керном, высверленные из конструкции, испытывали во влажном состоянии или, если это требовалось, в насыщенном состоянии. В случае этого исследования состояние образцов было при получении, но оно было очень близко к состоянию насыщения из-за отверждения.Температура сушки образцов составляла всего 50 °С, чтобы избежать риска образования микротрещин в бетоне.
Типы используемых буровых установок (d = 80, 100, 125, 150 мм) и вырезание керна из бетонного блока.
12 типов образцов с сердечником различного диаметра d и гибкости λ , подлежащих испытаниям на прочность при сжатии.
Таблица 3
Типы и количество образцов, подготовленных для испытаний каждой серии бетона.
образцы типа | диаметр / сторона D , мм | высота ч , мм | Slandness λ = h / d | образцы номера | |
---|---|---|---|---|---|
Литой | |||||
куб | 150 | 150 | 1.![]() | 6 | |
цилиндр | 150 | 300 | 2.0 | 6 | |
С сердечником | |||||
цилиндр 150 | 150 | 1.![]() | |||
цилиндр 150 | 225 | 1,5 | |||
цилиндр 150 | 300 | 2.0 | 7 | ||
цилиндр | 125 | 125 | 1,0 | 7 | |
цилиндр | 125 | 187,5 | 1,5 | 7 | |
цилиндр | 125 | 250 | 2.![]() | 7 | 7 |
цилиндр | 100 | 100 | 1.0 | 7 | |
Цилиндр | 100 | 150 | 1.5 | 7 | 7 |
цилиндр | 100 | 200 | 20 | 7 | 7 | 9 |
80 | 1.![]() | 7 | |||
Chillinder | 80 | 120 | 1.5 | 7 | |
Цилиндр | 80 | 160 | 160 | 2,0 | 7 |
Общее количество экземпляров, которые должны быть проверены 336. Плотность и прочность на сжатие влажных формованных образцов и образцов с сердечником были испытаны в возрасте 28 дней в соответствии с EN 12390-7 [44] и EN 12390-3 [45] соответственно. Высушенные образцы испытывали по тем же методикам, но в возрасте 35 дней, когда они достигли высушенного состояния.
3. Результаты
Результаты испытаний формованных образцов представлены в . Результаты испытаний плотности во влажном и сухом состоянии, а также испытаний на влагосодержание образцов с сердечником представлены в .Приведенные значения являются средними значениями, определенными для данного бетона на целом наборе из 72 и 12 образцов с сердечником соответственно во влажном и высушенном состоянии.
Таблица 4
Средние значения прочности на сжатие и плотности, определенные на формованных образцах.
серии | LWA типа | Номинал W / C | 33 Плотность 8 1 D M , W , KG / M 3Прочность на компрессию, см , , , MPA , MPA | 3 Прочность на компрессию, F см , CYL , CYL , MPA , MPA|||||
---|---|---|---|---|---|---|---|---|
I MOTAR | — | 0.![]() | 2080 | 2080 | 45.0 | — | — | |
II Минометный | — | 0,37 | 2200 | 65.2 | — | — | ||
I EC | Exp.![]() | 0,55 | 1290 | 14,5 | 13,8 | |||
II EC | Exp. глина | 0,37 | 1410 | 18,1 | 16,9 | |||
I SFA | Синт. летучая зола | 0.55 | 1800 | 1800 | 37.![]() | 37.1 | 37.1 | 97.1 |
II SFA | II SFA | 0.37 | 1890 | 49.090 | 49.6 |
Таблица 5
Средние значения бетонной плотности и содержания влаги на стержневых образцах.
серии | серии | NWA типа | Номинальная W / C | W / C 433 M , W , KG / M 3Плотность 2 D m m , d , кг / м 3 | содержание влаги, мк м ,% | ,%
---|---|---|---|---|---|
I EC | EXP.![]() | 0,55 | 1300 | 1140 | 14,0 |
II EC | Exp. глина | 0,37 | 1410 | 1250 | 12,8 |
I SFA | Синт. летучая зола | 0,55 | 1790 | 1570 | 14,0 |
II SFA | Синт.![]() | 0,37 | 1880 | 1680 | 11,9 |
Результаты испытаний на прочность при сжатии образцов с сердечником представлены соответственно во влажном и сухом состоянии.Следует отметить, что средние значения прочности ( f см ), рассчитанные как средние значения шести однотипных стержней, представлены в . Глобальное среднее значение прочности ( f CM ) рассчитывалось как среднее средних значений всех типов сердцевины. Между тем, результаты прочности, представленные в, были определены на отдельных образцах, высушенных в печи. Поэтому эти результаты можно рассматривать только как дополнительные, и они не могут быть положены в основу количественного анализа эффекта масштаба.
Средние значения прочности на сжатие, определенные для образцов с влажным керном различного диаметра d и гибкости λ .
Индивидуальные результаты испытаний прочности на сжатие, определенных для сухих образцов с наполнителем различных диаметров d и гибкости λ .
4. Обсуждение
Анализ результатов показал, как и предполагалось, существенно различающиеся уровни прочности на сжатие и плотности четырех серий бетона.Прочность бетона составила от 14,5 до 49,5 МПа при определении формованных образцов-кубов и от 13,8 до 47,6 МПа для формованных цилиндров. Плотность бетона в высушенном состоянии колебалась от 1140 до 1680 кг/м 3 , а во влажном состоянии соответствующий диапазон составлял 1290–1880 кг/м 3 . «Эффект стены» оказывает незначительное влияние на плотность бетона; поэтому практически не было различий между результатами, полученными для формованных и стержневых образцов. Кроме того, аналогичные результаты испытаний на плотность, проведенных на формованных образцах, отвержденных в воде, и образцах с сердечником, показали, что состояние стержней было похоже на состояние насыщения из-за внешнего отверждения, но в основном за счет внутреннего отверждения с водой, размещенной в пористом заполнителе. Особый интерес представляли значения влажности бетонов. Несмотря на то, что керамзит характеризуется почти в два раза более высоким водопоглощением, чем спекшаяся зола-унос, влагосодержание испытанных легких бетонов, по-видимому, зависело в основном от герметичности цементных матриц. Если бы заполнители использовались изначально насыщенными, их водопоглощение, безусловно, повлияло бы на водопоглощение/влагосодержание композитов. В случае испытанных бетонов заполнители лишь предварительно увлажнялись до влажности, что обеспечивало хорошее сцепление и герметизацию структуры заполнителя цементным тестом.Такой эффект был доказан в [46].
Как правило, бетоны, изготовленные с более прочным спеченным зольным заполнителем (I SFA и II SFA), достигают более высокой плотности и прочности на сжатие (почти в три раза), чем бетоны, изготовленные из керамзита (I EC и II EC). Повышение прочности за счет применения более прочного раствора (II в/ц = 0,37) в качестве цементной матрицы также было намного более эффективным в случае бетонов SFA, чем для бетонов EC (). В случае последних бетонов применение столь слабого заполнителя ограничивало возможность увеличения прочности бетона за счет увеличения прочности цементной матрицы в значительной степени.Следует отметить, что прочность всех легких бетонов была ниже прочности цементных растворов, использованных в качестве их матриц, что характерно для ЛВБК с закрытой конструкцией.
Влияние применения различных цементных растворов в качестве матриц для легких бетонов с заполнителями из спеченной золы-уноса (SFA) и керамзита (EC) на их плотность и прочность (во влажном состоянии).
Соотношение прочности, определенное на стандартных кубиках и цилиндрах ( F см , CYL / F см , CUBE ) зависели от конкретной однородности: чем меньше прочность заполнителя и цементной матрицы, тем выше соотношение.Средние значения отношения были 0,95, 0,93, 0,99 и 0,96, соответственно, для бетонов I EC, II EC, I SFA и II SFA. Следовательно, эти значения были явно выше, чем значения, полученные в соответствии с EN 206 [38], и подтвердили гораздо менее выраженный эффект масштаба и формы испытанных легких бетонов по сравнению с обычными бетонами. Особо следует отметить, что бетон II ЭК с наименьшим значением коэффициента вообще не должен применяться на практике по материальным и экономическим причинам. Для целей данного исследования была приготовлена высокопрочная цементная матрица и очень слабый легкий заполнитель для получения легкого композита плохой однородности.Из полученных значений соотношения f см , цил / f см , куб : оценка легкого заполнителя привести к более высокому классу, чем в случае, когда он определяется для стандартных кубов.
В случае образцов с сердечником размерный эффект оказался практически незаметным (). Эту тенденцию можно наблюдать даже в случае результатов одиночных сухих образцов с керном (). Тем не менее, по очевидным причинам, результаты, полученные на отдельных образцах в сухом состоянии, не следует учитывать при дальнейшем количественном анализе масштабного эффекта. При анализе средних значений прочности, представленных в , казалось, что тип образцов с сердечником не влияет на результат прочности независимо от типа бетона. Как предполагалось в EN 13791 [41], диаметр сердечника в испытательном диапазоне 80–150 мм при заданной гибкости не оказал заметного влияния на результаты прочности. Более того, в отличие от NWAC, гибкость протестированных LWAC, по-видимому, также не оказала заметного влияния на результаты.Однако в случае менее однородных, более слабых бетонов, изготовленных из керамзита, разброс значений средней прочности ( f см ) был немного больше по сравнению с бетонами с агломерированной золой. Для подтверждения этих наблюдений был проведен более подробный анализ. Анализ охватывал разброс результатов для конкретного типа образцов с сердечником, а также соотношение значений средней прочности, определенных для эталонного цилиндра с сердечником (d = 150 мм, h = 300 мм) и конкретного типа образцов с сердечником.
Исследования дисперсии результатов прочности показали, что для всех испытанных бетонов значения стандартного отклонения ( σ f ) и коэффициента вариации (v f = σ f /f c ) практически не зависят от объема и гибкости образцов с керном. Правило большего разброса результатов испытаний на прочность образцов меньшего объема здесь не подтвердилось. Коэффициенты вариации для конкретного типа образцов с сердечником представлены в .Значения v f варьировались от 0,01 до 0,15, а их средние значения составляли 0,07, 0,08, 0,05 и 0,03 соответственно для бетонов I ЭК, II EC, I SFA и II SFA. Значения σ f для конкретного типа образцов с сердечником колебались от 0,3 до 2,2 МПа, а их средние значения составили 1,1 МПа, 0,9 МПа, 1,5 МПа и 1,2 МПа соответственно для бетонов I ЭК, II ЭК. , I СФА и II СФА. Эти значения были почти такими же, как и стандартные отклонения значений средней силы ( f см ) по отношению к общемировому среднему ( f см ), представленным в . Такая дисперсионная сходимость предполагала, что различия в представленных результатах были вызваны скорее разбросом результатов, чем каким-либо эффектом масштаба. Очень низкие значения v f подтвердили превосходную структурную однородность испытанных легких бетонов, особенно композитов с заполнителем из спеченной золы-уноса. Результаты также показали возможность использования даже самых маленьких образцов керна (в пределах рассматриваемого диапазона) для оценки прочности конструкции из легкого бетона без увеличения количества образцов.
Соотношение между объемом образца с сердцевиной ( V ) и коэффициентом вариации прочности, определенным для конкретных типов образцов ( V f ) (во влажном состоянии).
Результаты анализа соотношений значений средней прочности, определенных на эталонном стержневом цилиндре (d = 150 мм и h = 300 мм) и на стержневых образцах определенного типа (R = f см, 300:150 стержень /f см, h:d core ) представлены в . Они подтвердили гораздо лучшую структурную однородность испытанных легких бетонов, особенно изготовленных из спеченного зольного заполнителя, по сравнению с обычными или тяжелыми бетонами.Для всех LWAC стандартный коэффициент длины сердечника ( f см 300:150 сердечник /f см 150:150 сердечник ) был значительно выше (в среднем 0,98), чем 0,82, принятый EN 13791 [41] для нормального -тяжелые и тяжелые бетоны. Для обеих серий спеченных зольных бетонов (I FSA и II FSA) среднее значение коэффициента прочности R равнялось точно 1,00, и не наблюдалось влияния гибкости или диаметра сердцевины. Это означает, что в случае таких бетонов можно предположить, что тип образцов с сердечником не имеет отношения к результатам прочности на месте.Однако в случае керамзитобетонов интерпретация результатов отношения прочности была не столь однозначной. Среднее значение отношения составило 1,06 и 0,94 для бетонов I EC и II EC соответственно, и в целом разброс значений отношения был намного больше по сравнению с бетонами с SFA.
Для определения достоверного значения коэффициента прочности для таких слабых бетонов следует провести дополнительные проверочные испытания.
Соотношение R = f см, 300:150 сердцевина /f см, h:d сердцевина (мокрое состояние).
Следует отметить, что состояние образца с сердечником, которое не указано в EN 12504-1 [43] и не учитывается в EN 13791 [41], может в некоторой степени повлиять на оцениваемый класс прочности бетона. Между тем, исследования также показали, что образцы с сердечником, высушенным в печи, показали более высокую прочность на 5% и прибл. 8% соответственно для бетонов SFA и EC, чем у испытанных во влажном состоянии. Снижение прочности влажных образцов, вероятно, было вызвано в большей степени значительным содержанием влаги, чем более ранним возрастом испытаний (сухим образцам для высыхания требовалось дополнительно семь дней к нормативному возрасту в 28 дней).
Несмотря на продемонстрированное отсутствие влияния размера и формы в испытаниях на прочность при сжатии легких бетонов, были явные различия между результатами, полученными для формованных образцов и образцов с сердечником. Соотношение ценностей прочности, определенные на клеолых и формованных цилиндрах F см , Core , / F см , CYL составляло 0,91, 0,75, 0,88 и 0,91 соответственно для бетонов I EC, II EC, I SFA и II SFA.Наименьшее значение коэффициента в случае бетона II EC может быть результатом его наименьшей однородности по сравнению с другими бетонами. Как упоминалось ранее, такой бетон, изготовленный из очень слабого заполнителя и прочной цементной матрицы, использовался в этом исследовании только для сравнительных целей и не должен применяться на практике. Другие бетоны (I EC, I SFA и II SFA), которые были примерами типичных LWAC, используемых для изготовления сборных элементов или строительства, показали более высокое соотношение см , цил (в среднем 0.90), чем принято в стандарте (0,85). В целом, в связи с различными технологиями производства LWAC и различными типами конструкции легких заполнителей, применяемых в мире, значение коэффициента 0,85 может быть сохранено в общих методических рекомендациях по оценке прочности бетона в конструкции или сборном элементе.
Тем не менее, в случае легкого заполнителя бетона более однородной структуры следует учитывать завышение класса прочности ЛБК, встроенных в конструкцию или сборные элементы.Поэтому стандартная рекомендация сформировать положения, действующие в месте применения LWAC, была полностью оправдана. Для испытанных LWAC, за исключением бетона II EC, «стеночный эффект» и различная температура отверждения, по-видимому, были доминирующими факторами, определяющими разницу между прочностными характеристиками, указанными для образцов с сердечником и формованных образцов. Влажность бетона (из-за внутреннего твердения) и подверженность микротрещинам в результате процесса сверления или высокой температуры, вероятно, имели здесь меньшее значение, чем в случае NWAC.
5. Выводы
Выполненная программа исследований и анализ полученных результатов не выявили масштабного эффекта в испытаниях на прочность при сжатии, определяемых на образцах с сердечником из четырех типов легких заполнителей с закрытой структурой. Ни гибкость, ни диаметр сердцевины, казалось, не влияли на результаты прочности. Этот факт следует объяснить несравненно лучшей структурной однородностью испытанных легких бетонов по сравнению с обычными.При этом правило большего разброса результатов испытаний на прочность образцов меньшего объема здесь не подтвердилось. Это означает, что, в отличие от NWAC, можно было надежно оценить прочность на сжатие таких типов LWAC, встроенных в конструкцию или сборные элементы, с использованием даже самых маленьких сердечников (в пределах рассматриваемого диапазона) без увеличения количества образцов. Кроме того, в случае таких бетонов оказалось достаточным использовать стержни с гибкостью 1,0 вместо требуемых 2.0, если результаты испытаний на прочность относятся к цилиндрам, формованным в пропорции 2:1. Тем не менее следует предположить, что в случае легкого бетона, приготовленного с изначально насыщенным заполнителем или с частицами заполнителя более плотного и/или более гладкого внешнего сланца, размерный эффект может быть более выраженным.
Поэтому количественные результаты этого исследования не могут быть обобщены для всех типов LWAC.
Несмотря на продемонстрированное отсутствие масштабного эффекта при испытаниях на прочность при сжатии легких бетонов, были явные различия между результатами, полученными на формованных и заполненных образцах.Однако для испытанных LWAC, за исключением бетона II ЭК, соотношение f см , сердечник /f см , цил было несколько выше среднего (5,0 на ). предполагается в стандартах. В результате применение стандартного соотношения для оценки прочности на сжатие существующей конструкции из таких типов LWAC может привести к ее завышению. Поэтому стандартная рекомендация сформировать положения, действующие в месте применения LWAC, была полностью оправдана.
Анализ зависимости прочности, заданной на стандартных формованных образцах, показал, что из-за гораздо менее выраженного масштабного эффекта LWAC по отношению к NWAC оценка прочности бетона с легким заполнителем, определенная на стандартных цилиндрах, может привести к более высокому классу прочности, чем в случае, когда она определяется на стандартных кубах.
Благодарности
Автор благодарен инж. Ян Шпак и инж. Мацею Райтару за техническую поддержку в проведении исследования.
Финансирование
Это исследование не получило внешнего финансирования.
Конфликт интересов
Автор заявляет об отсутствии конфликта интересов.
Литература
1. Валоре Р. Расчет теплопроводности пустотелых бетонных кладок. Конкр. Междунар. 1980; 2:40–63. [Google Академия]2. АКИ 213 Р-03. Руководство по конструкционным легким бетонным заполнителям. АКИ; Фармингтон-Хиллз, Мичиган, США: 2003. [Google Scholar]3. Невилл А. Свойства бетона. 5-е изд. Пирсон Эдьюкейшн Лимитед; Лондон, Великобритания: 2011.[Google Академия]4. Spitzner J. Обзор разработки легких заполнителей — история и фактический обзор; Материалы Конгресса по конструкционному легкому бетону; Саннефьорд, Норвегия. 20–24 июня 1995 г.; стр. 13–21. [Google Академия]5. Чандра С., Бернтссон Л. Бетон с легким заполнителем. Публикации Нойеса; Нью-Йорк, штат Нью-Йорк, США: 2003.
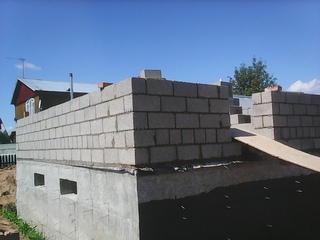
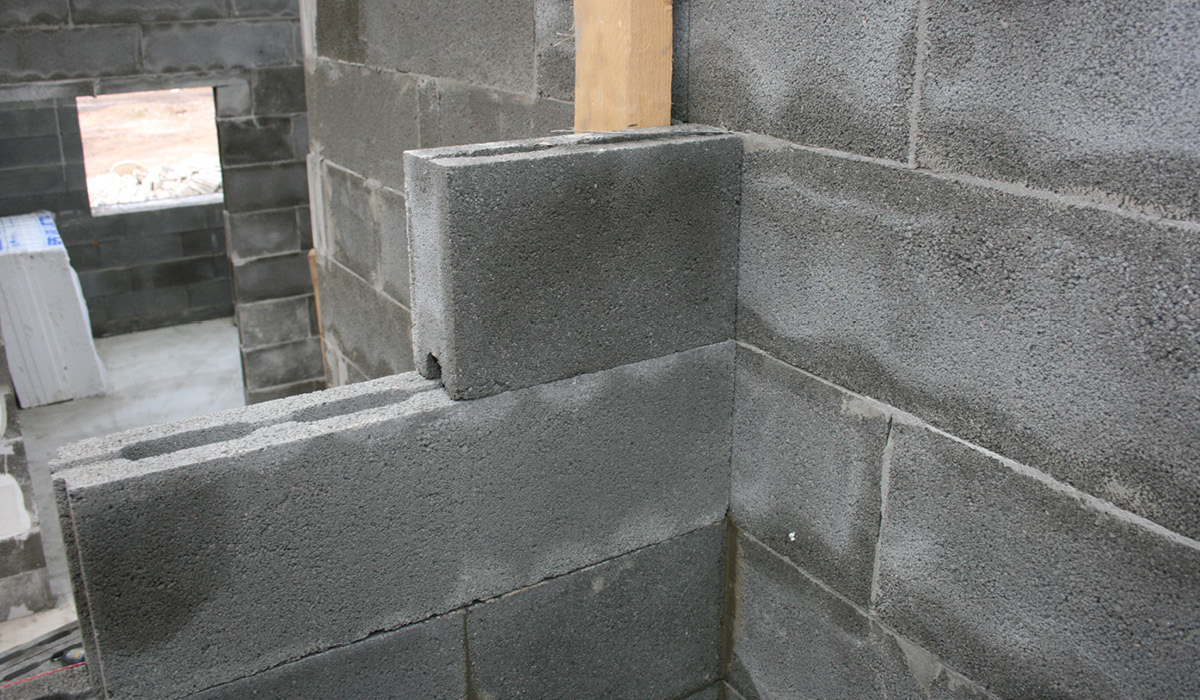

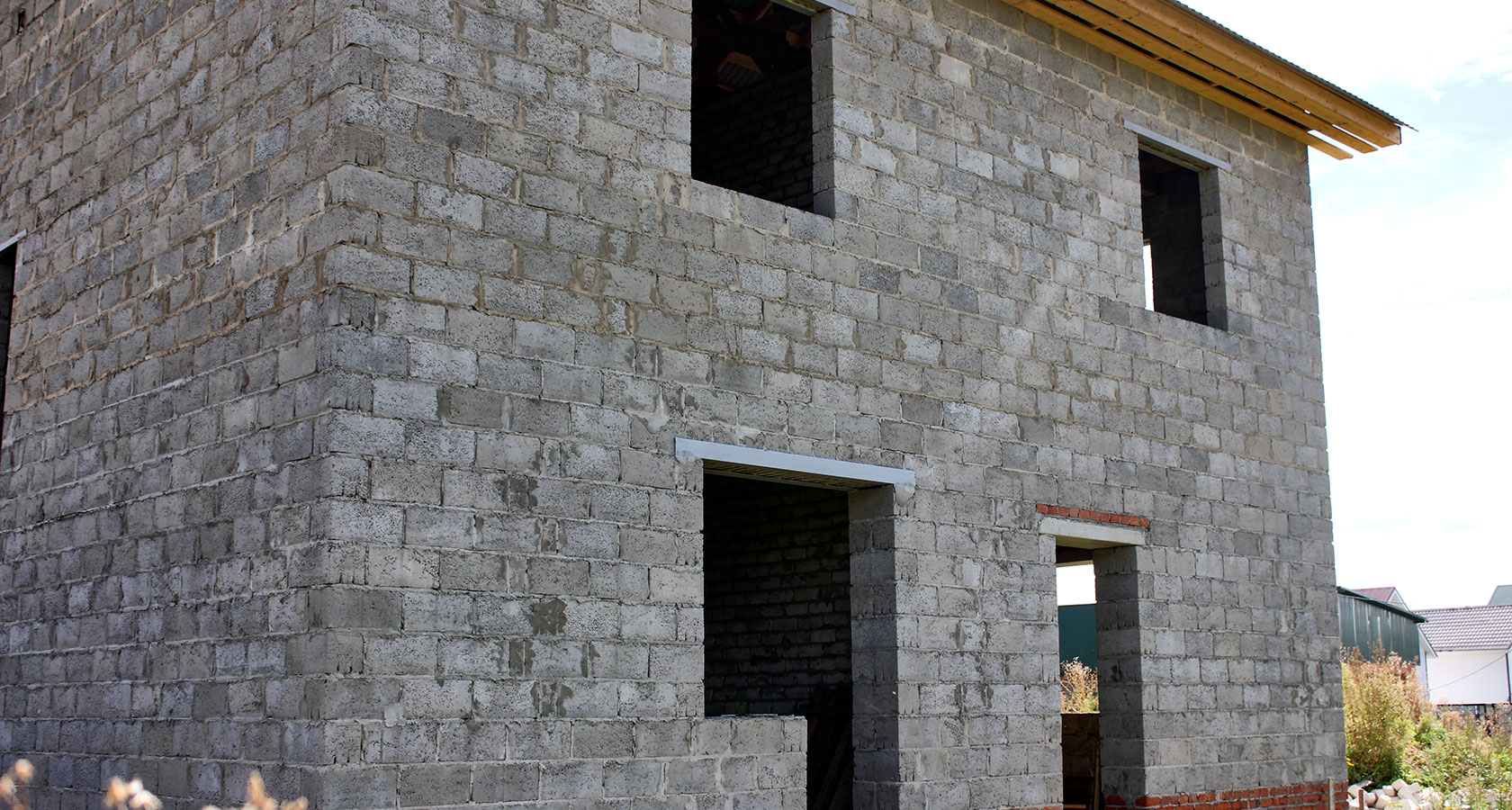



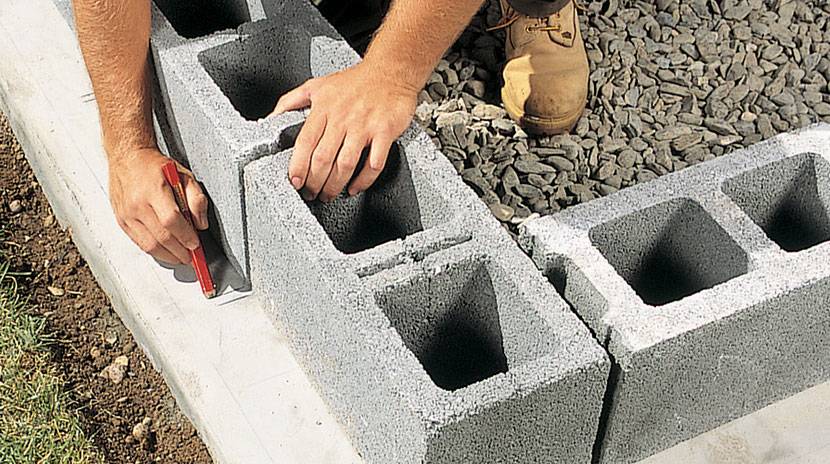
Что такое керамзитобетон?
Что означает керамзитовый заполнитель?
Вспученный или расширяемый глиняный заполнитель является широко используемой гидропонной средой для выращивания.Это легкий заполнитель, который нагревают в печи до температуры 2910 градусов по Фаренгейту (1200 градусов по Цельсию). Когда заполнитель нагревается, он выделяет газы, которые создают маленькие пузырьки, образующие сотовую структуру внутри заполнителя.
Движение печи придает агрегату круглую форму. Круглые формы керамзита различаются по размеру. Вспенивающаяся глина стала популярной средой для выращивания в гидропонике и аквапонике, потому что она защищает корни и удерживает воду.Глина имеет нейтральный pH, что также снижает вероятность роста плесени и грибка.
Максимальная доходность объясняет заполнитель керамзита
Вспучивающаяся глина часто используется в бетонных блоках, бетонных плитах, аквапонике, очистке воды, гидропонике и гидрокультуре. При использовании в гидропонном садоводстве керамзит считается беспочвенной средой для выращивания. Его также можно добавить в почву для улучшения дренажа.
При добавлении в почву керамзит помогает почве удерживать воду в периоды засухи. Вспенивающаяся глина действует как идеальный изолятор для корней при использовании в районах с частыми морозами.
Использование керамзита в качестве удобрения для почвы идеально подходит для увеличения количества кислорода в почве, что способствует энергичному росту растений. При смешивании с тяжелой почвой керамзит улучшает потенциал аэрации почвы, а также увеличивает дренаж.
Керамзит также иногда называют Гидротоном, глиняной галькой, легким керамзитовым заполнителем (LECA) или простой глиной.Напоминает коричневые камешки. Эту среду для выращивания можно промывать и использовать повторно, что делает ее популярным и экономичным выбором. Его часто сочетают с сетчатыми горшками или сетчатыми горшками, которые аккуратно удерживают среду в системе.
Блоки из керамзитобетона
Продукт также называют Leca Haydite или ex-clay. В Европе LECA началась в Дании, Германии, Голландии (Нидерланды), Великобритании и на Ближнем Востоке. В мире есть несколько производителей и поставщиков легкого керамзитового заполнителя (LECA) и керамзитового заполнителя (ECA). Обычно ECA используется в бетонных блоках, бетонных плитах, геотехнических засыпках, легком бетоне, очистке воды, гидропонике, аквапонике и гидрокультуре. ECA или LECA — это универсальный материал, который используется во все большем количестве приложений. В строительной отрасли он широко используется при производстве легкого бетона, блоков и сборных или литых конструктивных элементов (панелей, перегородок, кирпича и легкой черепицы). ECA используется для структурной обратной засыпки фундаментов, подпорных стен, устоев мостов.ECA может дренировать поверхностные и грунтовые воды, чтобы контролировать давление грунтовых вод. Затирка LECA может применяться для полов (отделки) и кровли с тепло- и звукоизоляцией. ECA или LECA также используются в водоочистных сооружениях для фильтрации и очистки муниципальных сточных вод и питьевой воды, а также в других процессах фильтрации, в том числе при работе с промышленными сточными водами и рыбными хозяйствами. ЭКА используется в сельском хозяйстве и в ландшафтном дизайне.
Это может изменить механику почвы. Он используется в качестве среды для выращивания в гидропонных системах и смешивается с другими средами для выращивания, такими как почва и торф, для улучшения дренажа, удержания воды в периоды засухи, изоляции корней во время заморозков и обеспечения корней повышенным уровнем кислорода, что способствует очень энергичному росту.ЭКА можно смешивать с тяжелой почвой для улучшения ее аэрации и дренажа. ECA полезен для ландшафтного дизайна, нефтехимии — нефти и газа, теплоизоляции крыш, звуко- или акустической изоляции, дорог и мостов, плавучих мостов на водоемах, плавучих солнечных электростанций или панелей, предотвращения оползней, гидроизоляции, открытых спортивных площадок, железных дорог и Проекты железных дорог метро, высокопрочный конструкционный бетон, сегменты сборного железобетона, поверхностные или сточные воды, очистка сточных вод и водосбережение.Компания Rivashaa Eco Design Solutions Private Limited уже создала для себя нишу в производстве качественного легкого керамзитового заполнителя (LECA) и керамзитового заполнителя (ECA), своевременных поставок и предоставления клиентам рекомендаций по эффективному использованию керамзитового заполнителя (ECA) или легкого заполнитель керамзита (LECA) для достижения наилучших результатов.
Керамзитовый заполнитель является предпочтительным легким заполнителем, используемым вместо обычного древесного угля, кокосового торфа, диатомовой земли, растущих камней, лаварока, минеральной ваты, перлита, пемзы, рисовой шелухи, песка, вермикулита и древесного волокна, строительства, керамики
Шлакоблок | Размер, вес, стоимость, преимущества и недостатки
В этой статье мы обсудим шлакоблок.
1. Введение
Шлакоблоки можно определить как полые конструкции прямоугольной формы, обычно изготавливаемые из бетона и угольных шлаков, которые используются для возведения стен на строительных площадках.
Зола используется в качестве заполнителя в шлакоблоке. Разница между бетонными блоками и шлаком заключается в том, что бетонные блоки готовятся с использованием цемента, заполнителя, песка, воды, но в шлаке вместо заполнителя используется зола.
2.Свойства шлакоблоков
а. Обычно изготавливается из бетона и шлака.
б. Он очень легкий по сравнению с последним из-за пропорции заполнителя
c. Он не очень силен, поэтому в нескольких местах им часто пренебрегают.
д. Они чаще гнутся, а коробление и ремонт в разы очень дороги, поэтому ими пренебрегают.
эл. Это самая старая мода, так как около 50% не производятся серийно.
ф. Он не имеет заметного количества прочности на растяжение.
3. Подготовка шлакоблоков
Обычный вес шлакоблока составляет около 26–33 фунтов (11,8–15,0 кг). Блоки из легкого бетона готовят путем удаления песка и гравия с керамзитом, сланцем или шифером. Керамзит, сланец и сланец изготавливаются путем измельчения сырья и нагревания его примерно до 2000°F (1093°C).
4.Типы шлакоблоков
Стандартные серые шлакоблоки
Этот формат отличается прочностью и долговечностью, огнестойкостью, отличными звукоизоляционными свойствами, энергосбережением и доступной ценой, соответствует спецификациям ASTM C-90.
Общий размер, например 8 дюймов x 8 дюймов x 16 дюймов;
Бетонный блок для настила
Это самый лучший и экономичный метод строительства настила. Этот тип блока сделан для клиентов DIY.Этот блок позволяет габаритную древесину. В этом блоке нет необходимости смешивать или насыпать огарки для общего размера, например, 7 «х 11» х 11 «.
Стандартный основной блок
Этот тип шлакоблока используется для возведения шлакоблоков для больших сооружений, таких как здания, школы и т. д. ;
Бетонный блок для настила Quikrete
Этот тип блока используется для поддержки настила и быстрой и прочной конструкции.Общий размер, например, 10 дюймов x 10 дюймов x 10 дюймов; Фактические: 625 дюймов x 9,625 дюймов x 9,625 дюймов
5. Размеры шлакоблоков
. Их нормальные размеры на 3 ⁄ 8 дюймов (9,5 мм) меньше формальных размеров (чтобы обеспечить 3 ⁄ 8 дюймов растворных швов между блоками в любой ориентации).
6.Стоимость шлакоблоков
Шлакоблоки больше не отличаются по стоимости в зависимости от типа. В то время как несколько замковых камней могут стоить 95 центов за штуку, нормальная стоимость шлакоблока составляет от до 3 долларов за штуку.
7. Преимущества шлакоблока
a. Перевязочные работы не требуются.
б. Он очень легкий по весу.
в. Требуется не так много навыков.
д. Он конструктивно прочнее кирпича.
эл. Возможны более тонкие стены, что обеспечивает большую площадь ковра.
ф. Он большой по размеру, а значит нет. суставов меньше.
г. Лучшая изоляция от тепла, звука и сырости.
ч. Он не нуждается в штукатурке.
я. Требуется меньше раствора, что экономит деньги.
8.

1. Возможность просачивания.
2. Материалы могут не подходить для разных мест.
9. Часто задаваемые вопросы
1. Сколько весит шлакоблок?
Вес шлакоблока составляет около 26–33 фунтов (11,8–15,0 кг).
2. Сколько стоят шлакоблоки?
Обычная стоимость шлакоблока составляет от 1 до 3 долларов за штуку.
3. Какой высоты шлакоблок?
Шлакоблоки имеют высоту 16 дюймов (410 мм).
4. Насколько велик шлакоблок?
Шлакоблоки имеют длину 16 дюймов (410 мм) и ширину 8 дюймов (200 мм).Они легкие, обладают прочностью, долговечностью, огнестойкостью, отличными звукоизоляционными свойствами, энергосбережением и доступной ценой
Инженер-строитель и генеральный директор Naba Buddha Group
Легкие бетонные блоки, здание IBS, модульное здание в Малайзии
Легкие сборные бетонные блоки обычно изготавливаются из керамзита, сланца или сланца, это может помочь уменьшить вес по сравнению с обычными бетонными заполнителями, где он может состоять из гранита, кварца, дробленого известняка и других; ключевым моментом здесь является пористость частиц заполнителя.
Хорошо известным продуктом является газобетон, также называемый в Малайзии автоклавным газобетоном. Ниже мы немного расскажем о газобетонном бетоне и о том, почему он так хорошо принят и пользуется высоким спросом в строительной отрасли Малайзии. Проконсультируйтесь с нами как с поставщиком газобетонных блоков в Малайзии, чтобы получить наилучшие рекомендации по спецификации, которая может потребоваться для вашего здания.
Автоклавный газобетон
В Малайзии есть много поставщиков газобетонных блоков, и они преуспевают, и общая проблема, с которой всегда сталкиваются строители, заключается в том, что им необходимо предварительно заказывать, а готового запаса всегда нет.AAC имеет много названий в строительной отрасли, таких как автоклавный бетон, автоклавный ячеистый бетон (ACC), ячеистый бетон, автоклавный легкий бетон (ALC), пористый бетон и многие другие. От стеновой панели, перекрытия или панели пола, крыши до перемычки и фасада (обшивки).
Поставщик блоков AAC из Малайзии также утверждает, что AAC может действовать как изолятор от звука, тепла, огня; устойчивый к плесени агент, вода рядом с ним может использоваться в качестве конструкционных строительных материалов для внутренней стены, внешней стены, крыши и пола.Легкий блок AAC в Малайзии также очень популярен, потому что он позволяет быстро и легко строить там, где неопытные рабочие или домовладелец могут сделать это самостоятельно (DIY) с соответствующей инструкцией.
Из-за сырья и процесса производства газобетонных блоков всеми производителями газобетонных блоков в Малайзии, он в основном имеет высокую теплоизоляцию. Процесс отверждения паром включает в себя высокое давление, и физические свойства этих газобетонных блоков состоят из более чем миллионов крошечных воздушных карманов, которые не связаны друг с другом.Материалами, используемыми для изготовления газобетона, являются песок, цемент, аэратор и известь. Эти смеси будут распределяться поставщиком газобетонных блоков в Малайзии для форм всех размеров, а затем для формирования легких кирпичей газобетонных блоков, блоков газобетонных блоков, панелей и перемычек газобетонных блоков в качестве результат автоклавной выдержки.
Легкий вес также означает, что вам нужно меньше структурных опор для строительства, а раствора для швов каждого блока также меньше из-за меньшего количества швов (больше размер каждого блока, чем у обычного кирпича).Это относится также к оштукатуриванию и штукатурке, где экономия средств может быть достигнута за счет стабильных по размерам и точных блоков, а также меньшей толщины штукатурки. Теплоизоляционный продукт от поставщика кирпича AAC в Малайзии экономит ваше время, усилия и затраты на установку дополнительных теплоизоляционных материалов.
Легкий железобетон (LRC)
Легкий конструкционный бетон. Бетон с легким заполнителем, поставляемый поставщиком легких блоков из Малайзии, может использоваться для строительных конструкций с прочностью, эквивалентной бетону с нормальным весом.Преимущества использования бетона с легким заполнителем включают: Уменьшение статической нагрузки, что позволяет экономить на фундаменте и армировании.
Поставщик легкого заполнителя в Малайзии производит легкие бетонные панели с использованием побочных продуктов промышленного производства, таких как летучая зола из котельной электростанции. Одним из самых популярных легких бетонных материалов является пенопласт, также известный как пенополистирол или пенополистирол (EPS).
Представляют собой смесь бетона и пены или изготавливаются из сэндвич-панелей.Сэндвич-панели из пенопласта также бывают разного формата: либо пена находится между двумя внешними слоями бетонных панелей, либо бетонный слой окружен двумя внешними слоями пены. Проконсультируйтесь с нами, как с ведущим поставщиком панелей из легкого бетона в Малайзии, который может предоставить вам решение по доставке и установке для вашего проекта.
Пенополистирол — сэндвич-панель из пенополистирола
Этот тип пенополистирола, пенополистиролбетонных панелей популярен также в Малайзии благодаря своей тепло- и звукоизоляции. или производителя сборных железобетонных панелей в Малайзии.
После этого поставщик сборных или сборных железобетонных панелей из Малайзии обработает пенопласт, чтобы разрезать его по размеру или смешать с бетонной смесью, в зависимости от замысла архитектора.
Смешанный пенопласт с бетоном легко смешивается со специальными добавками для обеспечения адгезии пенобетона и предварительно приготовленного бетона. или, в качестве альтернативы, подрядчиком на площадке.В противном случае поставщик премиксов зальет форму на своем заводе для вспенивания пенобетонных панелей для стен, плит, крыш или других компонентов инфраструктуры и отправит их после отверждения.
Промышленная строительная система IBS для легких блоков Малайзия
Последующие проекты, которые легкие бетонные блоки для этого типа зеленых строительных материалов (сертифицированы GBI) промышленной строительной системы, продукты IBS больше относятся к поставщику сборных и сборных железобетонных панелей. в Малайзии, тогда как, как упоминалось выше, различаются только слои полистирола и бетона внутри и снаружи. Если конструкция состоит из слоев пенопласта снаружи бетонной панели (также иногда называемых изолированными бетонными формами, ICF), обычно производитель бетонных панелей в Малайзии либо прикрепляет слой пены перед отправкой на стройплощадку, либо просто собирает на строительной площадке с помощью стартовых стержней. , поставщик сборного железобетона (поставщик сборного легкого армированного бетона, LRC) выполнит первый вариант, а поставщик сборных полистирольных панелей выполнит более поздний (монолитный).
И последнее, но не менее важное для другой конструкции, когда слои находятся между бетонными панелями. образуется после того, как подрядчик из Малайзии набрызгивает легкие блоки (торкретбетон) или заливает бетон в опалубку, в которой установлен пенополистирол.Этот тип легких бетонных блоков, поставщик Малайзии, конечно, будет выполнять механическую работу, которая заключается в прикреплении высокопрочной проволочной сетки BRC к пенополистиролу, чтобы обеспечить адгезию бетона и создать структурную целостность между пенопластом и слоями бетона.
Спрос на легкие конструкционные бетонные панели или блоки в Малайзии существует, потому что их можно использовать так же, как несущую стену и плиту, как и бетон с нормальным весом. Позвольте нам предоставить вам более подробную информацию о преимуществах регистрации легких поставщик заполнителя бетона в Малайзии для вашего строительства.Легкие бетонные блоки или панели из пенополистирола могут помочь уменьшить собственные нагрузки и, следовательно, снизить затраты при транспортировке, обработке, фундаментах, конструкционных и армирующих материалах. Помимо экономии опалубки, водонепроницаемости и огнестойкости можно добиться теплоизоляции и звукоизоляции.
Где купить легкие блоки и найти подрядчика в Малайзии
Группа ЛИДА поставляет и устанавливает изделия из легкого бетона, применимые для внутренних и наружных работ, конструкционные и ненесущие панели из легкого бетона (перегородки), лестницы, плавающие строительство, внутреннее и наружное, легкое и тяжелое промышленное использование, жилое, коммерческое, высотное, промышленное, магазин, дом, офисы, уединение, гостиница, кафе и другие настраиваемые спецификации.
особенности, этапы, отзывы владельцев
Если вы решили начать строительство, то дом из блоков Leca – это практически идеальный вариант. Материал качественный, сочетающий в себе как прочность, так и энергосберегающие свойства. Если обратить внимание на практику, то окажется, что эти параметры редко сочетаются. Обычно приходится выбирать между долговечностью и энергоэффективностью. А вот в керамзитобетонных блоках все эти характеристики удачно сочетаются настолько, что делают дома намного легче и теплее, чем кирпичные.По прочности уступают совсем немного.
Материал по стойкости к ударным нагрузкам немного лучше по этому параметру, чем газобетон. Хитрые европейцы, экономящие каждую копейку, давно оценили преимущества легкобетонных блоков. Построив дом из этого материала, впоследствии можно неплохо сэкономить на отоплении. Но это возможно только при соблюдении всех условий при строительстве. Об этом мы и поговорим в нашей статье.
Характеристики
В составе блоков есть три компонента:
- Обожженный и керамзит (керамзит).
- Кварцевый песок.
- Цемент.
Этот материал является экологически чистым, так как не содержит вредных компонентов. Бетонный блок – это легкий материал, но теплоизоляционные качества у него на высоком уровне. За счет цемента изделие отличается долговечностью и может применяться при строительстве частных домов.
Преимущества блоков
Теперь рассмотрим преимущества стен из керамобетонных блоков. И, судя по отзывам, довольно много:
- Низкая степень гигроскопичности – несмотря на наличие цемента, материал устойчив к влаге.
- Высокая морозостойкость. Но все зависит от типа агрегата – количество циклов оттаивания и замораживания может быть 15-200.
- Высокая прочность и плотность бетонного блока.
- Устойчив даже к открытому огню.
- Все вышеперечисленные преимущества порождают еще одно – долговечность. Можно сказать, что вы строите на века.
- Блоки не посягают на грызунов и различных насекомых, не подвержены ржавчине.
Блоки не гниют.
- Стены из керамзитобетона, не покрытые плесенью и грибками.
- Коэффициент теплопроводности довольно низкий, поэтому дома из этих блоков теплые.
- Материал дышит благодаря хорошей паропроницаемости.
- Строительство домов из легкобетонных блоков может быть выполнено без привлечения специалистов, все работы можно выполнить самостоятельно.
- Без усадки, малый вес материала.
- Вам нужно будет приготовить раствор, но его потребуется в два раза меньше, чем для кирпичных домов.
- Низкая стоимость строительства и материалов.
Недостатки керамоблоков
Но, судя по отзывам владельцев, дома из керамоблоков имеют ряд недостатков, на которые сложно закрыть глаза.
- Несмотря на то, что масса конструкции небольшая, экономить на возведении фундамента не стоит.
- При кладке в любом случае образуются швы (холодные швы), поэтому утепление делать обязательно.
- К сожалению, на рынке строительных материалов часто попадаются некачественные материалы, не соответствующие заявленным параметрам.
Но преимущества перевешивают, поэтому, если вы решаете, из какого материала строить дом, смело выбирайте легкие заполнители из блоков. Они прослужат многие десятилетия, верно.
Ящики отборные
Чтобы дом из газобетонных блоков прослужил долго, необходимо соблюдать несколько требований. В первую очередь необходимо выбрать тип материала, который будет использоваться при строительстве. В том случае, если планируется строительство малоэтажных домов, то лучше выбирать конструктивно-теплоизоляционные блочные типы, плотностью их 700-1200 кг/куб.м. Материалы с меньшей плотностью и массой лучше всего использовать для утепления. Тяжелые блоки идеально подходят для строительства жилых домов.
Обратите внимание, что чем меньше плотность материала, тем выше его изоляционные качества. Также необходимо с умом выбирать размер блоков. Если вы планируете построить теплый дом и сократить расходы на газ и электроэнергию, то вам необходимо, чтобы стены имели толщину 40 см. Один из самых популярных блоков – размер 190*188*390. Для изготовления самонесущих перегородок понадобится ставить секцию там, где толщина 90-120 мм.
Требования к фундаменту
Что касается фундамента под дом из заполнителя бетонных блоков, то он должен обладать повышенной прочностью. Желательно делать глубокой – этот вариант нужно выбирать исходя из типа грунта, промерзания грунта и водообеспеченности. Но в любом случае глубина не должна быть меньше одного метра. На дне находится слой песка высотой около 20 см. Он позволит фундаменту «играть» при движении грунта. Бетонные сетки должны иметь толщину 20 см, каркас делается из 6 стержней арматуры.Лучше всего использовать толстую арматуру – 12 или 18 мм. В этом случае вы обеспечите целостность дома даже при потере грунта.
Требования к утеплению и кладке
Что касается утепления и отделки, то лучше делать это одновременно. Поэтому облицовочные и теплоизоляционные материалы следует выбирать заранее и приобретать. Обшивка стен может быть выполнена блок-хаусом, сайдингом, кирпичом или штукатуркой. Идеальный утеплитель-пенопласт, ПЕНОПЛЭКС или минеральная вата. Для предотвращения образования холодных швов нужно использовать джут – его укладывают в кладку.За счет этого холод проникает внутрь здания через раствор.
Кладку блоков необходимо армировать через каждые 3-4 ряда. Для этого используются стержни из арматуры диаметром 12 мм. Но сначала на агрегатах необходимо сделать бороздки или борозды, которые впоследствии подлежат сушке феном. Необходимое армирование нужно сделать перед установкой потолочных панелей или кровли.
Выбрать ящики
Итак, теперь поговорим подробнее о том, как построить дом с нуля. Изучив различные отзывы о домах из легкобетонных блоков, можно понять, каких преимуществ у них гораздо больше, чем у других построек из подобных материалов.
Возможно разделение блоков по назначению:
- Утеплитель плотностью 500-700 кг/куб.м.
- Структурная плотность 1200-1800 кг/куб.
м.
- Конструкционно-теплоизоляционные, плотностью 700-1200 кг/куб. м.
Если вы планируете строительство коттеджа, то лучше всего выбрать второй тип блоков. Если вы хотите построить небольшой, но теплый дом, нам подойдет третий тип. Они обладают высокой прочностью и теплоизоляцией.Определив блоки, можно начинать строительство.
Чертеж
Проекты домов из керамзитобетонных блоков, как и любых других, лучше заказывать у специалистов. Конечно, если их самих нет. Ведь без проекта не только дом построить не получится, но и разрешения вам никто не даст. Архитектор составит не просто план строительства, а укажет все мелкие детали, составит подробную смету. В нем он укажет вид материала и количество, стоимость проведения всех этапов работы.Имея на руках все необходимые документы, можно приступать к строительству.
Строительство фундамента
В плане нужно уделить особое внимание стенам – в частности, их толщине. Дом из керамобетонных блоков будет тем теплее, чем толще стены. Этот параметр зависит от размера фундамента. Алгоритм строительства следующий:
- Очистить участок от растительности и мусора.
- Проект делает разметку. Для ориентира установите прутья и натяните между ними шпагат.Он определит границы траншей.
- Теперь, определив контуры, можно копать траншею. Ширину и глубину нужно выбирать при проектировании. Стены делают ровными, проверяют с помощью уровня и отвеса.
- На дно насыпают подушку из песка, поливают ее водой и заливают. Затем кладут сетку из арматуры.
- Изготавливают съемную опалубку из фанеры или досок. Закрепите опалубку, изнутри обтянутую пленкой.
- Комплект арматурной рамы для армирования бетона.Так вы обеспечите максимальную прочность фундамента, не позволите ему треснуть.
- Залить раствор и запечатать. Фундамент рекомендуется делать за один заход, чтобы бетон не затвердел.
- Выровняйте поверхность и дайте бетону остыть.
На просушку ленточной основы уйдет около месяца. Снимать опалубку разрешается не ранее чем через 10 дней после заливки. Если на улице жарко, то время от времени нужно поливать бетон водой, чтобы он не потрескался.
Стены
Теперь, когда фундамент полностью высох, можно приступать к возведению стен из заполнителя из бетонных блоков. Пошаговая инструкция по возведению:
- Не нужно рассчитывать на то, что поверхность фундамента должна быть ровной, т.к. уже месяц идет усадка. Итак, сначала нужно выровнять верхнюю часть фундамента. Ровность и качество проверяют уровнем.
- После застывания раствора необходимо уложить гидроизоляцию – идеальный для этого рубероид.Вам нужно будет уложить 3 слоя, обязательно промазав их битумной мастикой.
- Только после этого разрешается приступать к укладке блоков. Он мало чем отличается от работ, произведенных из кирпича. Необходимо иметь мастерки, нитки, гвозди, блоки, раствор, уровень, уголки. Сначала установите блоки по углам здания. В том случае, если стена 10 м, нам все равно придется поставить один блок посередине.
Цель – поставить ровно блоки и между ними натянуть нить как направляющую. Помните, что от этого зависит ровность всего дома.
- Необходимо, чтобы натянутая нить указывала на положение блоков. Его укладывают первым рядом по всему периметру. Как можно чаще проверяйте ровность, регулировку можно производить с помощью резинового молотка.
- После укладки первого ряда начинаем вторую аналогию. Единственная разница в том, что область исправлена. Соблюдайте толщину стен – около 40 см. В нужных местах сделайте разметку оконных и дверных проемов.
- Через каждые 3-4 ряда нужно делать арматуру по периметру, ряды дополняются стержнями арматуры, укладываемыми в пазы.
- Следите за кладкой до тех пор, пока не достигнете нужной высоты. Обязательно нужно армировать последний ряд, так как на него влияет большая нагрузка на крышу.
Как видите, технология строительства дома из керамзитобетонных блоков не очень сложная, достаточно соблюдать все требования.
Керамзитовый кирпич своими руками.
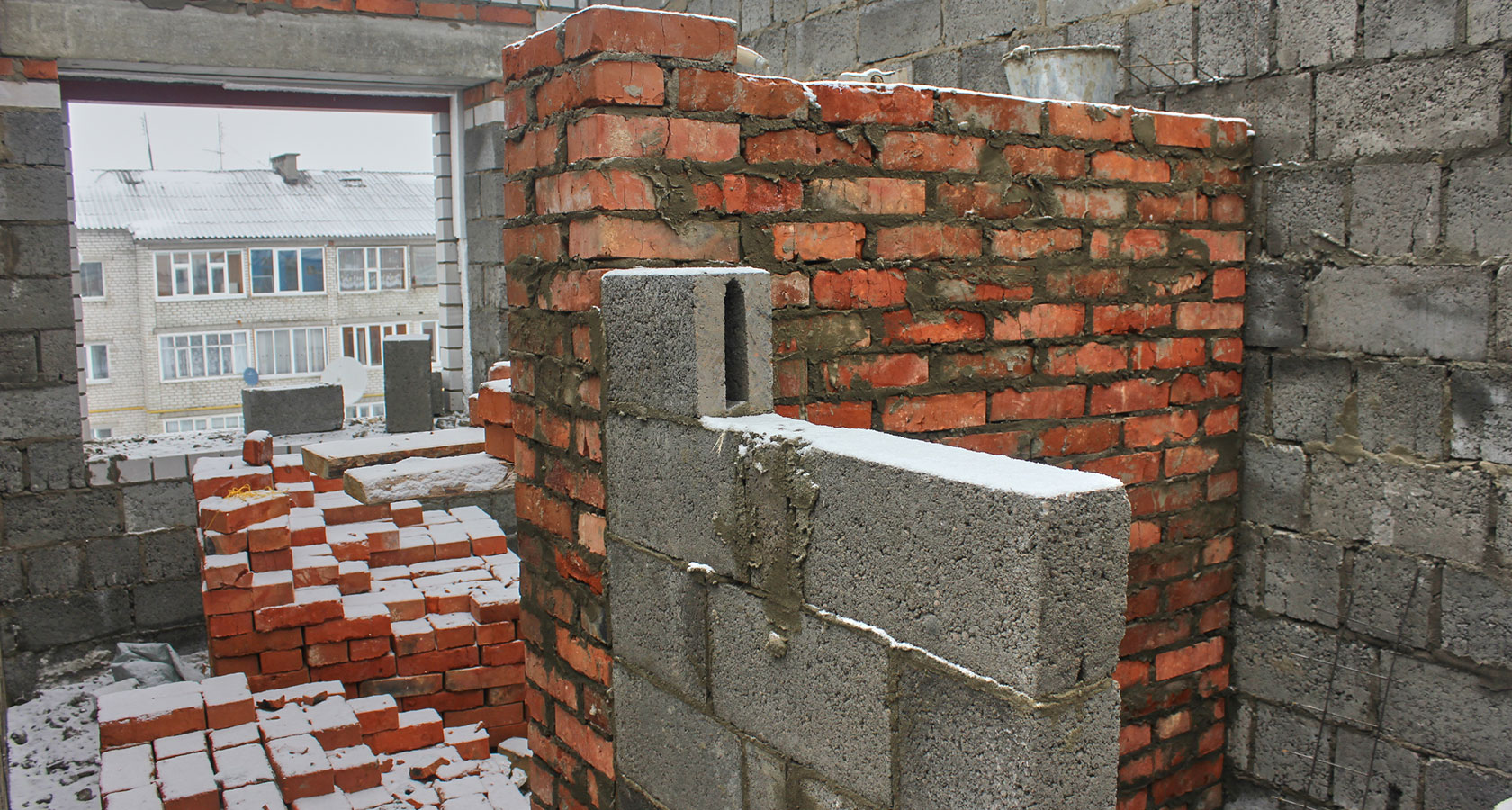
— легкие строительные материалы, которые применяются для кладки стен.Представленная на рынке продукция, как правило, производится тем или иным заводом керамзитобетонных изделий (в частности, Алексинским). Вы также можете приобрести продукцию и блоки Еврокам производства керамзитобетонно-гравийного завода (Винзили). Несмотря на то, что керамзитобетон имеет относительно небольшой вес, он обладает достаточной прочностью. Кроме того, керамзитобетонная поверхность не наносит вреда окружающей среде, и такой блок можно изготовить в домашних условиях. Технология производства продукции позволяет значительно снизить финансовые затраты.Качество будет высоким, если в их производстве используются хорошие материалы.
Технология изготовления
При строительстве малоэтажных домов специалисты часто возводят стены из легкого заполнителя бетонного блока. Использование этих стройматериалов сулит больше выгоды, чем покупка кирпича, так как блоки имеют ряд преимуществ. Во-первых, укладка керамзитоблоков займет меньше времени и меньше цементной смеси. Кроме того, теплопроводность блоков считается низкой, благодаря чему изделия обладают высокой теплоизоляцией.В то же время производство керамзитобетонных блоков – простой процесс. Технология создания легкозаполнительной бетонной смеси компании «Еврокам» аналогична способам изготовления аналогичных строительных материалов. Если есть такая необходимость, то можно сделать раствор своими руками или приобрести материалы производства Алексинских заводов или керамзитовый гравий (Винзили). Завод керамзитобетонных изделий выпускает качественную продукцию. Для этого нужно только соблюдать технологию и пропорции компонентов.Перед началом работ важно заранее узнать о преимуществах и недостатках керамзитобетона. Процесс делится на несколько этапов:
Укладка
Не заполняйте смесью отверстия внутри керамзитоблоков — блоки потеряют свои теплоизоляционные характеристики.
Так как первая линия кладки является основой здания, блоки нужно распределять особенно тщательно и аккуратно. После укладки каждых двух-трех керамзитоблоков нужно проверить, насколько ровна кладка.Для этого понадобится строительный уровень. Затем следует замазать щели цементным раствором. Таким же образом укладывается каждый последующий слой. Также важно помнить, что швы не должны слишком выделяться. При этом необходимо, чтобы они надежно удерживали остальные блоки. Так, ширина швов может быть около полутора сантиметров.
Специалисты отмечают, что заполнять смесью отверстия внутри керамзитоблоков нельзя. Во-первых, вы израсходуете на это большое количество цемента, во-вторых, блоки потеряют свои теплоизоляционные характеристики.Кроме того, стоит подумать, как вы будете украшать стену. Например, если вы планируете облицевать керамзитоблоки кирпичом, вам не придется заниматься дополнительной отделкой стен. А если вы не собираетесь облицовывать поверхности, то сделайте «расшивку».
очень часто используются в строительной сфере благодаря хорошим эксплуатационным характеристикам. Но для того, чтобы построить дом, необязательно покупать готовый материал, а можно сделать керамзитоблоки своими руками.Таким образом, вы сможете значительно сэкономить свой бюджет, так как для этого не нужно покупать дорогое сырье.
Необходимые материалы и инструменты
Для того чтобы сделать керамзитоблоки своими руками, необходимо, в первую очередь, подготовить инструменты и материалы. Лучше выбирать качественное сырье вне зависимости от цели использования – коммерческой или личной.
Для изготовления вам потребуются:
- Бетономешалка . Даже для строительства одного дома рекомендуется приобретать ее объемом от 120 литров.В среднем цена такого средства составляет 10 тысяч рублей.
- Вибропрессовый стол . Его можно приобрести в готовом виде в строительных магазинах за 7-10 тыс. руб. Преимуществом покупных моделей является уже встроенная форма для заливки блоков.
Но такой стол можно сделать самому из столешницы и электродвигателя.
Если у вас большое количество форм вместе, вы можете сделать до 150 блоков за один рабочий день. Купленная модель может производить от 1 до 4 готовых блоков за несколько минут.Конечно, им еще нужно дать время высохнуть. Если требуется небольшое количество материала, а бюджет на строительство ограничен, то сделать керамзитоблоки своими руками можно из самодельных приспособлений – емкостей для замеса бетона и форм для заливки.
Изготовление форм
Домашние формы могут быть изготовлены из картона, пластика или листового металла. Главное, чтобы он был ровным. Размер одного стандартного блока 39х19х19. Вы можете сделать одну форму с этими размерами или прямоугольник с несколькими отделениями для одновременного изготовления нескольких блоков.Форма изготовлена из двух частей, каждая из которых напоминает букву Г.
Деревянное изделие лучше соединить металлическими уголками, а с внутренней стороны обшить тонким листом стали. В противном случае древесина будет впитывать влагу, что отрицательно скажется на прочности блоков. Автомобильное масло можно использовать как альтернативу листовому металлу. Также он хорошо защитит изделие из дерева от влаги.
Керамзитобетонные блоки можно изготовить самостоятельно, как сплошные, так и с пустотой внутри.Делается это не только для того, чтобы сэкономить раствор, но и для того, чтобы стены имели лучшую теплоотдачу. Для этого нужно подготовить три цилиндра одинакового размера. Для того чтобы они крепко держались на своем месте, их сначала соединяют между собой, а затем прикручивают к боковой части формы саморезами.
Если вам нужно несколько блоков, то для создания пустот внутри изделия используются пластиковые или стеклянные бутылки. Но перед работой их необходимо залить водой, чтобы они были более устойчивыми.Вставлять их в форму нужно только после заполнения ее 60% раствором.
Приготовление раствора
Вторым этапом является приготовление раствора. Для того чтобы получить качественную продукцию, нужно смешать цемент, песок и керамзит в пропорциях 1:3:8. Добавить воду из расчета 200 литров на 1 кубометр раствора. Также необходимо учитывать начальную влажность цемента. , песок и керамзит.
Для приготовления раствора необходимо подготовить:
При производстве важно не только соблюдать правильные пропорции, но и добавлять каждый элемент в необходимой последовательности. Для начала необходимо рассчитать необходимое количество воды. После этого в бетономешалке тщательно перемешивают песок, керамзит и цемент, а затем добавляют жидкость. Полученный раствор по своей консистенции должен напоминать нагретый пластилин.
Бывают случаи, когда купить оборудование невозможно.Тогда керамзитобетонные блоки своими руками можно сделать с помощью обыкновенной лопаты. Размешивать раствор желательно небольшими порциями, это предотвратит его преждевременное застывание.
Блочное производство
Керамзит — материал с относительно небольшим весом , поэтому будет постоянно плавать в растворе. Для удобства производства по этой причине используется вибрационный станок. Если его нет, то блок придется подбивать деревянным брусом.
Использование вибростола позволяет изготавливать значительно больше изделий за короткое время. Раствор заливают в стальные формы, после чего на несколько минут включают мотор. В этом случае излишки удаляются. Чтобы достать блок из формы, его приподнимают за ручку.
После заливки блоки должны просохнуть в форме 1 сутки, а затем еще 1-2 суток на открытом воздухе. Для этого лучше использовать поддоны с воздушным зазором. Это позволит блокам высохнуть равномерно.
Для окончательной сушки блоков их необходимо поместить в закрытое помещение, где не будет ни влаги, ни прямых солнечных лучей. При очень высоких температурах их необходимо смочить водой и накрыть пленкой.
Через 7-10 дней можно использовать в работе керамзитоблоки. А вот сушить блоки мастера рекомендуют в течение месяца. Таким образом, они приобретут фирменные качества.
Комментарии:
Блоки из керамзитобетона своими руками изготовить несложно.Для их создания используется керамзитобетонная смесь, которая значительно снижает вес будущей конструкции.
Благодаря использованию натуральных материалов блоки экологически чистые.
Характеристики керамзитобетонных блоков
Керамзитовые блоки состоят из песка, цемента, воды и наполнителя, в качестве которого используется керамзит, поэтому изготовить их самостоятельно может любой мастер. При этом можно сэкономить значительные суммы денег. Понятно, что такие блоки нельзя использовать для строительства многоэтажного дома, но для строительства гаража, сарая или небольшого дома керамзитоблоки ручной работы – идеальное решение.
Если вы решили сделать керамзитоблоки своими руками, то вам следует знать, что по своим экологическим характеристикам они приравниваются к обычному кирпичу, так как изготавливаются из натуральных материалов.
Формы для изготовления керамзитобетонных блоков.
используется в качестве наполнителя при изготовлении этого строительного материала. Так как он легкий, вес блоков тоже небольшой. Если вас интересует вопрос, как сделать керамзитоблоки своими руками, и вы реализуете это решение, то сможете значительно удешевить строительные работы.При сравнении затрат при строительстве из обычного кирпича и таких блоков можно сэкономить около 30% своих денег. Тот факт, что один блок соответствует 7 кирпичам, позволяет ускорить процесс строительства.
Вы также можете приобрести указанный материал, но максимальная польза будет в том случае, когда вы делаете керамзитобетонные блоки своими руками.
Одним из недостатков этого строительного материала является низкая прочность, что объясняется высокой пористостью.Для того чтобы увеличить этот показатель, при изготовлении блоков в смесь необходимо добавлять кварц или обогащенный песок.
Если вы делаете строительные блоки своими руками и будете использовать их для создания внутренних перегородок, несущих незначительные нагрузки, то можно использовать керамзитобетон. В том случае, если вы будете возводить из этого материала несущие стены и укладывать на них железобетонные перекрытия, лучше использовать обогащенный песок.
В зависимости от пропорции компонентов, входящих в состав смеси для изготовления блоков, определяются конечные характеристики строительного материала.
Если вы хотите получить материал с высокими теплоизоляционными свойствами, то вам необходимо увеличить количество керамзита, но в этом случае прочностные характеристики блоков снизятся.
В зависимости от пропорций компонентов керамзитобетонные блоки станут прочнее или приобретут повышенные теплоизоляционные свойства.
Плотность такого строительного материала почти на 50% меньше, чем у керамического или силикатного кирпича, что позволяет снизить нагрузку на фундамент здания.На его строительстве можно сэкономить, так как его можно сделать менее мощным.
Если вы все же решили изготовить такие строительные блоки самостоятельно, то вам необходимо учитывать тот факт, что они, по сравнению с кирпичом, имеют более высокую пористость и поэтому хрупкие, менее прочные.
Еще одним недостатком этого стройматериала является низкая морозостойкость, поэтому отделка стен обязательна. Если сравнивать их с газобетоном, то этот материал обрабатывается хуже.
Вернуться к содержанию
Блоки самодельные
Изготовление блоков из легкого заполнителя своими руками – задача, которая под силу любому мастеру. Эту работу можно выполнить самостоятельно, а если работать вдвоем, то реально сделать 100-120 штук указанного строительного материала в день.
Если следовать инструкции и технологии, то можно самостоятельно подготовить материал, например, для строительства гаража, сарая, других подсобных помещений или небольшого домика.
Для начала вам понадобится форма, она может быть деревянной или металлической. Для изготовления формы проще и дешевле использовать доски. Для того чтобы облегчить вытягивание блоков, их рекомендуется обить жестью. Чтобы форма не изменила своих размеров в процессе эксплуатации, на концах двух ее половинок необходимо сделать специальные затворы.
Так как вы все делаете своими руками, размеры могут быть те, которые удобны в вашем случае. Все будет зависеть от размера подготовленной формы.
С помощью пресс-формы можно производить до 100 блоков из легкого заполнителя в день.
Для выполнения работы вам потребуется:
форма- ;
- Мастер в норме;
- лопата;
- готовая смесь; Металлический лист
- , на котором будут производиться работы;
- вибростол.
Для приготовления раствора лучше всего приобрести или арендовать бетономешалку, но если такой возможности нет и требуется небольшое количество стройматериала, то можно сделать раствор своими руками.
Для приготовления раствора вам понадобится:
- 1 часть цемента, необходимо использовать не менее М 400.
- 8 частей керамзита. Для упрощения расчетов нужно руководствоваться тем, что в ведро емкостью 10 литров поместится около 5 кг керамзита фракцией 5-20 мм.
Вам понадобится около 300-500 кг керамзита на кубометр раствора. Все будет зависеть от того, какая плотность сторон вам нужна.
- 1 часть воды.
- 3 части песка, он не должен содержать примесей глины.
- 1 часть обычного стирального порошка, это сделает смесь более пластичной.
Для получения более качественных блоков необходимо использовать вибростол. Его можно купить, сделать самому или просто арендовать. Если у вас нет такой возможности, то можно утрамбовать состав в форме и с помощью обыкновенной лопаты, но качество и прочность полученного стройматериала будут низкими.
После того, как раствор схватится, а это будет зависеть от погодных условий, форму снимают, а блоки оставляют еще на 2 дня. Теперь их можно складывать и использовать для строительства через 28 дней.
Частные строения с каждым годом становятся все более актуальными, ведь жить в собственном доме гораздо комфортнее, чем в многоэтажке. Но главным препятствием зачастую является высокая стоимость строительства, поэтому застройщики ищут способы сэкономить. Если делать керамзитобетонные блоки своими руками, то это не только сэкономит значительные средства, но и послужит гарантией того, что изделия изготовлены в соответствии с нормами прочности.
Что нужно для работы
Для изготовления самодельных керамзитоблоков необходимо приобрести все необходимые материалы. Их количество рассчитывается исходя из планового количества изделий, и рассчитывается в соответствии с пропорциями в объеме:
Цемент | Если взять за основу широко распространенную марку М400, то понадобится около 1/10 объема блоков, которые необходимо изготовить. В одном кубическом метре содержится 1300 килограммов цемента, именно на этот показатель следует ориентироваться при определении необходимого количества. |
Керамзит | Вам понадобится вариант плотностью от 350 до 500 кг/м3, оптимальная фракция от 5 до 20 мм. Так как в раствор нужно добавить 8 частей, то несложно догадаться, что этот материал будет основным.![]() |
Песок | Песок речной лучше всего приобрести среднезернистый или крупнозернистый без каких-либо примесей глины и чернозема.Подойдет и песок из карьеров, но его желательно хотя бы просеять, а лучше вообще промыть. Для приготовления требуется 2 части, исходя из этого, и объем рассчитан |
Вода | Для технологии требуется примерно 215-230 литров на м3. Правильная дозировка воды очень важна для прочности блоков. Недостаток его, как и избыток, приводит к снижению прочности и появлению трещин на поверхности в процессе высыхания. |
Добавки | Этот компонент используется по желанию, но следует учитывать, что различные добавки позволяют значительно улучшить свойства бетона и повысить его влагостойкость и морозостойкость. При их использовании вероятность появления трещин на изделиях намного меньше. |
Совет!
Для улучшения качества продукции и экономии средств лучше приобретать универсальные, улучшающие свойства смеси и повышающие ее пластичность.
Организация рабочего процесса
На самом деле процесс настолько прост, что для керамзитобетонных блоков практически не требуется никакого оборудования. Но некоторые из самых простых приспособлений все же необходимы.
Формы для блоков
Есть два варианта: либо приобрести готовые варианты, либо сделать их самостоятельно.
В первом случае следует руководствоваться следующими факторами:
- Новые формы довольно дорогие, но можно купить и бывшие в употреблении. . Их стоимость намного ниже, но важно тщательно проверять каждое изделие на наличие повреждений и соответствие геометрическим параметрам.
- Важно подобрать оптимальные размеры, чаще всего используется вариант 190х190х390 для стен и вариант 80х190х390 для установки внутренних перегородок. Параметры могут меняться в зависимости от специфики работы.
- Другой вариант – арендовать постройки. , в некоторых регионах предоставляется такая услуга, что позволяет существенно сэкономить.
Второй вариант — собрать формы своими руками.
Производственные инструкции:
- Можно собрать каркас из досок толщиной 25 мм, при этом их внутреннюю поверхность желательно обшить жестью или жестью. Параметры для блоков берутся те же, что и для стандартных форм или любых других.
На фото — один из вариантов конструкции из доски или фанеры
- Другим решением является изготовление каркаса из листового металла, усиленного металлическими уголками.Для фиксации формы могут использоваться либо защелки, либо болтовое соединение через приваренные проушины, либо стяжка со шпильками и барашковыми гайками.
- Для создания пустот можно использовать как специально подготовленные заготовки, так и просто бутылки. Все зависит от возможностей и пожеланий.
Еще один вариант — машина для блоков из легкого заполнителя, представляет собой комбинированный вибрационный агрегат и формы, в малых вариантах их 2-4 штуки, в более производительных их количество может быть значительно больше.
Изделия для формовки
Этот этап выполняется следующим образом:
- Раствор готовят в пропорциях, указанных выше.Важно контролировать, чтобы консистенция была оптимальной. Лучше всего использовать бетономешалку, это гарантирует высокое качество смешивания, что очень важно для прочности изделий.
Совет!
Проще всего проверить консистенцию следующим образом: небольшое количество состава сжимают в руке, должен получиться плотный комок, который разбивается при падении на землю.
- Дальнейшее рассмотрение вопроса, как самому сделать керамзитобетонные блоки, зависит от того, есть ли у вас виброустановка.Если есть, то формы заполняют и устанавливают на оборудование для удаления воздуха из состава. Если нет установки, то состав утрамбовывается булавкой или деревянной палочкой.
- Полученные самодельные керамзитобетонные блоки оставляют на сутки, после чего формы можно разобрать и аккуратно выложить изделия на ровную поверхность для дальнейшего высыхания.
Полную силу продукт набирает в течение четырех недель.
Если вы не умеете резать керамзитобетонные блоки, то лучше всего подойдет болгарка с алмазным диском по бетону и камню диаметром 230 мм, так как не у всех есть специальные пилы по кирпичу.
Заключение
Видео в этой статье поможет вам лучше понять этот процесс. Важно соблюдать все требования технологии, и вы получите отличный результат.
Популярный материал, включающий цемент, песок и керамзит. Простая технология производства керамзитобетона позволяет легко освоить производство изделий. Изучив техпроцесс, вы сможете изготовить качественные керамзитоблоки своими руками, а затем использовать готовый материал для гаража или дачи.При изготовлении блоков нет необходимости использовать специальное оборудование. Для замеса используйте бетономешалку, а размеры керамзитобетонных блоков обеспечит разборная опалубка, которую вы легко сможете изготовить из подручных материалов.
Керамзитовые блоки — состав, разновидности и эксплуатационные характеристики
Керамзитовые блокиочень популярны в строительной сфере благодаря своим теплоизоляционным свойствам, устойчивости к влаге, прочности и экологичности.
Керамический блок – популярный материал, в состав которого входит цемент, песок и керамзит.Собираясь изготовить керамзитоблоки своими руками, необходимо подготовить следующие ингредиенты, входящие в состав композиционного материала:
- Портландцемент марки М400 и выше, выполняющий роль вяжущего;
- песок просеянный и очищенный от посторонних примесей, используемый в качестве мелкого заполнителя;
- керамзит гранулированный, добавляемый в состав керамзитобетонной смеси, в качестве крупного наполнителя;
- модифицирующие компоненты, повышающие производительность составных блоков.
Также для изготовления блоков потребуется вода, которая небольшими порциями добавляется в бетономешалку при замесе. Технология также позволяет вводить волокнистые волокна, которые значительно повышают прочностные свойства блоков. Отличительной особенностью блоков является ячеистая структура, связанная с введением в рабочую смесь легких, пористых, прочных и экологически чистых гранул керамзита.
Изделия из керамзитобетона подразделяются на следующие типы:
- теплоизоляция, используемая в качестве изоляции;
- теплоизоляционные и конструкционные, применяемые для возведения стен;
- конструкционная, востребована в нагруженных строительных конструкциях.
Керамзитобетонные блоки классифицируются по следующим критериям:
- Области применения. Продукция используется для возведения стен и возведения перегородок;
- конструкции. Изготавливают полнотелые блоки, а также изделия с внутренними полостями;
- размер. Размеры стеновых и перегородочных элементов регламентируются требованиями действующего стандарта.
Керамзитовые блоки обладают высокими эксплуатационными характеристиками
Керамзитовые блоки обладают высокими эксплуатационными характеристиками, выгодно отличающими их от других строительных материалов.Основные свойства блочного композита:
- прочность. Блоки способны воспринимать усилия на каждый квадратный сантиметр площади от 5 кг для теплоизоляционных изделий до 500 кг для конструкционных изделий;
- теплопроводность. По этому показателю материал успешно конкурирует с деревом, бетоном и кирпичом. Использование пустотелых керамзитоблоков снижает потери тепла; Морозостойкость
- . Способность сохранять целостность при глубокой заморозке увеличивается с уменьшением пористости блока.Морозостойкость теплоизоляционных композитов не превышает 50 циклов, а для конструкционных изделий показатель увеличивается в десятки раз;
- способность поглощать шум. Звукоизоляционные свойства увеличиваются с увеличением пористости. Гранулы керамзита, входящие в состав блоков, обеспечивают повышенный уровень звукоизоляции;
- паропроницаемость.
Благодаря способности керамзитобетонного материала свободно пропускать пары воздуха, внутри помещения поддерживается комфортный уровень влажности;
- небольшая усадка.Керамзитовые блоки, изготовленные в соответствии с требованиями технологии, сохраняют свои первоначальные размеры. Усадка блочного материала на метр керамзитобетонной кладки не превышает 0,5 мм;
- экологическая чистота. В состав керамзитоблоков входит экологически чистое сырье. В процессе эксплуатации изделий не происходит выделения вредных для здоровья человека веществ.
К остальным достоинствам блоков также можно отнести:
- малый вес при увеличенных габаритах;
- способность воспринимать значительные усилия;
- малый коэффициент линейного расширения;
- простота;
- расширенный ассортимент продукции;
- доступный ценовой уровень.
С увеличением пористости повышаются звукоизоляционные свойства блоков.
За счет шероховатой поверхности блоков повышается сцепление с облицовочными составами, что ускоряет выполнение отделочных мероприятий. Наряду с комплексом достоинств блоки имеют один недостаток – их проблематично использовать для строительства многоэтажных домов из-за особенностей строения керамзитобетонного композита.
Блоки планируем делать самостоятельно — готовим материалы и инструменты
Приняв решение делать керамзитоблоки своими руками, подготовьте необходимые материалы, рабочие инструменты и оборудование для производства композитных блоков:
- ингредиенты для приготовления керамзитобетонного раствора;
- бетономешалка для смешивания компонентов;
- лопаты и ведра для загрузки сырья в бетономешалку; Вибростол
- для эффективного уплотнения смеси.
Вам также понадобится разборная опалубка для одиночной или групповой отливки изделий. Формы для керамзитобетонных блоков своими руками легко изготовить из листового металла, ламинированной фанеры или дерева.
Изготовление керамзитобетонных блоков своими руками – нюансы технологии
Производство керамзитобетонных блоков своими руками по следующему алгоритму:
Внутренние стенки необходимо смазать отработанным машинным маслом.

- Изготовление сборно-разборных форм для изготовления блоков.
- Приобрести материалы для приготовления рабочей смеси.
- Подготовить инструменты и оборудование.
- Определитесь с пропорциями керамзитобетонного раствора.
- Взвесьте сырье и приготовьте рабочую смесь.
- Сформировать изделия.
- Герметизируйте раствор, разлитый по формам.
- Демонтировать опалубку через день после заливки.
- Разложите готовые изделия для сушки.
Для ускоренного набора эксплуатационной прочности технология позволяет пропаривать блоки в специальных камерах. За счет использования пропарки сокращается продолжительность производственного цикла, что немаловажно при изготовлении блоков в повышенных объемах. Рассмотрим особенности основных этапов.
Подготовка формы для керамзитобетонных блоков
Формовочные емкости для изготовления керамзитоблоков в домашних условиях легко изготовить при минимальных затратах.
Возможны различные варианты формирования контейнеров:
Для изготовления керамзитоблоков форма может быть изготовлена самостоятельно
- деревянная, для изготовления которой используются строганные доски или ламинированная фанера. Древесина имеет ограниченный срок службы, однако надежно послужит для мелкосерийного производства блоков; Металл
- , для изготовления которого используется листовая сталь. Внутренние полости формируются с помощью трубчатых вставок.Стальные формы служат долгие годы при условии своевременной очистки и смазки.
Внутренние размеры формы выполнены в соответствии с размерами стандартного керамзитоблока. Перед началом производства следует разработать эскиз опалубки.
Дальнейшие работы по изготовлению литейной формы производить по следующему алгоритму:
- Перенесите размеры эскиза на материал.
- Вырежьте заготовки для опалубки.
- Подготовьте две L-образные стенки.
- Соедините заготовки с помощью металлических уголков.
- Прикрепите лист основания к нижней плоскости стен.
Важно тщательно продумать конструкцию пресс-формы, чтобы обеспечить возможность ее разборки. Нанесение отработанного масла на внутреннюю поверхность облегчит снятие готовых блоков.
Оптимальные пропорции керамзитобетонного раствора
Если вы хотите сделать блоки из керамзита своими руками, вам следует правильно приготовить рабочий раствор.
Основными вяжущими веществами являются песок, цемент и вода.
Для приготовления одного кубометра керамзитобетонной смеси плотностью 1,5 т/м3 потребуется:
- 430 кг портландцемента М400;
- Гранулы керамзита 720 кг;
- 420 кг просяного песка;
- 140 литров воды.
Пропорции компонентов для различных видов керамзитобетона, отличающихся удельным весом, легко найти на строительных сайтах или в специальной литературе.
Важно равномерно смешать ингредиенты и получить кремообразный раствор.
Отливаем керамзитоблоки своими руками
Для литья блоков формовочные емкости закрепляют на рабочем столе вибрационной машины и заливают керамзитобетонным раствором.
При выполнении работ важно придерживаться рекомендаций профессионалов:
- смазывать стенки формы с отработкой;
- заливать при температуре 16-19°С;
- выполнить формовку на плоской поверхности;
- защищают изделия от атмосферных осадков и солнечных лучей.
Раствор необходимо заливать в один прием до полного заполнения опалубки и затем выравнивать поверхность кельмой или шпателем.
Следует соблюдать осторожность при извлечении блоков из формы.
Уплотнение рабочей смеси
Правильное уплотнение раствора влияет на качество готового продукта. Для уплотнения керамзитобетонной смеси используйте:
- ручное устройство трамбовки;
- Вибростол с электроприводом.
Процесс виброуплотнения залитой в опалубку смеси прекращается при появлении на поверхности цементного молока.
Завершающие стадии производства блочных изделий из керамзита
В зависимости от конкретных условий процесс твердения в форме длится от одного до трех дней. Затем выполняются следующие операции:
- Керамзитовый блок извлекается из формы легким постукиванием по стенкам.При снятии керамзитоблоков своими руками следует соблюдать осторожность, чтобы избежать растрескивания блоков и не допустить образования сколов на углах изделия; Продукция
- раскладывается на поддоны и отправляется в закрытое помещение. Готовое изделие следует выкладывать в один слой и избегать ударных нагрузок.
Время высыхания готовых изделий 28 суток, после чего затвердевший керамзитобетонный композит используют для возведения стен и перегородок, а также для теплоизоляции.
Подведение итогов
Самостоятельно освоить производство керамзитобетонных блоков несложно, подготовив необходимые строительные материалы и внимательно изучив технологический процесс.