Стол и лавка из цельной доски
Сделанный на заказ обеденный комплект из ореховой доски с не обрезными краями, светодиодной подсветкой, стеклянными вставками и металлическими ножками.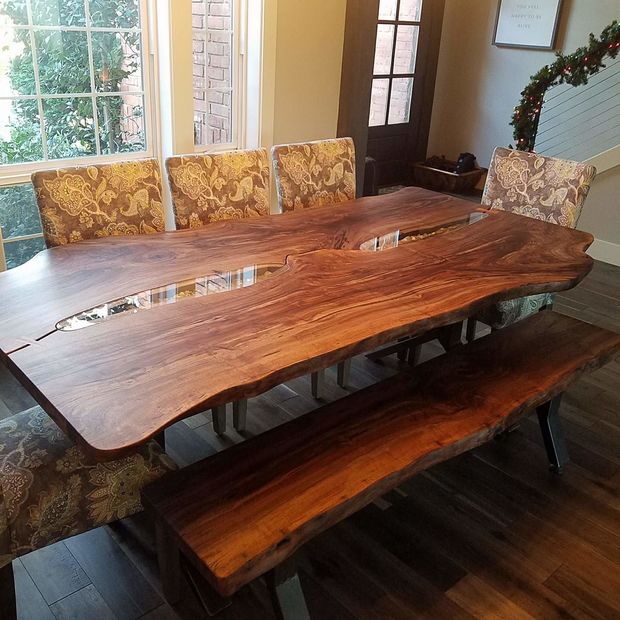

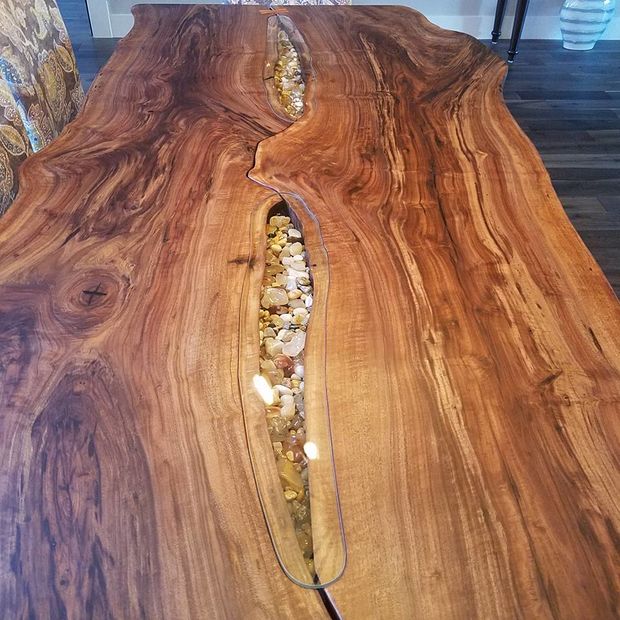
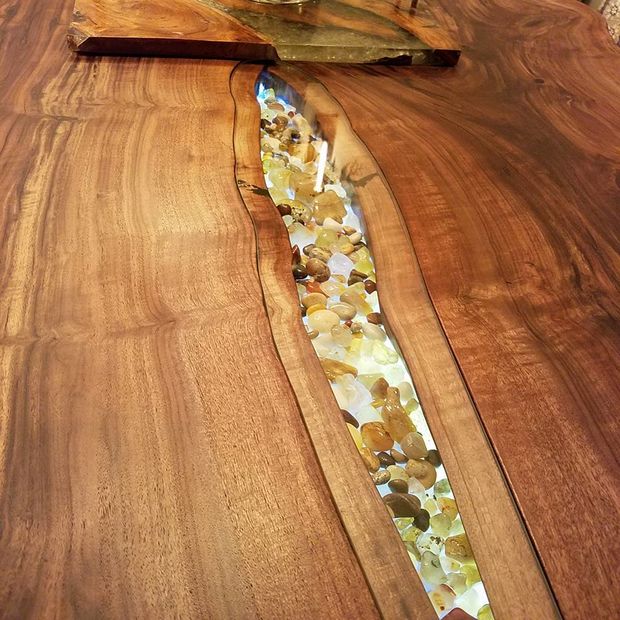
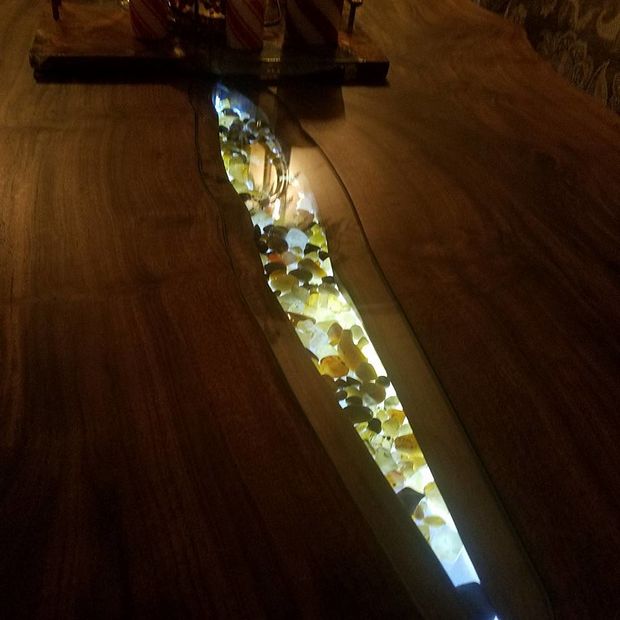
Работа над столом доставила массу удовольствия. Заказ у моей заказчицы был особенный (и интересный). А в качестве стимула – бюджет. Ее запрос включал такие пункты:
- — Столешница с не обрезными краями с двух сторон, состоящая из двух отдельных ореховых досок.
- — Множество узоров и контрастность.
- — Полости посередине для коллекции агатов.
- — Для освещения агатов в полости должна стоять светодиодная подсветка.
- — Полости накрываются съемными вставками из стекла.
- — Размеры столешницы 100 см в ширину и 210 см в длину.
- — Сделанные на заказ стальные ножки (затемненные).
- — Одна скамейка в похожем стиле.
- — Срок изготовления не более месяца.
Я постарался задокументировать каждый этап процесса, но сроки были довольно сжатыми, и иногда у меня не было возможности сделать фотоснимок. Простите за отсутствующие фотографии; эти шаги я постараюсь описать более подробно…
Поиск материала
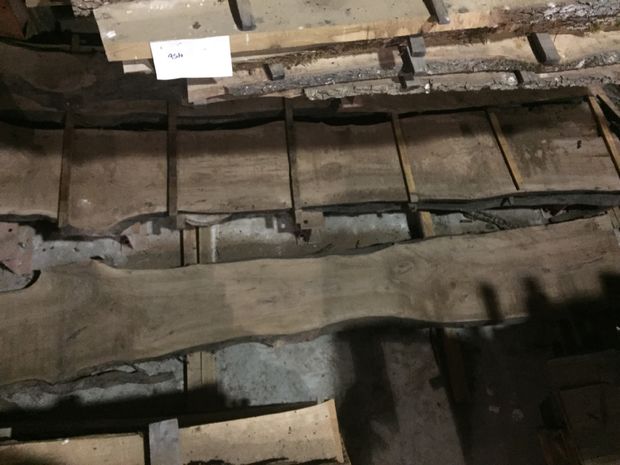
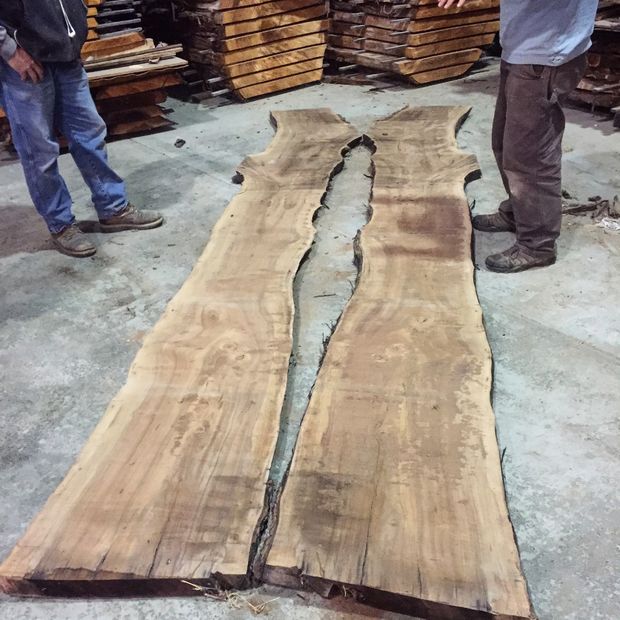
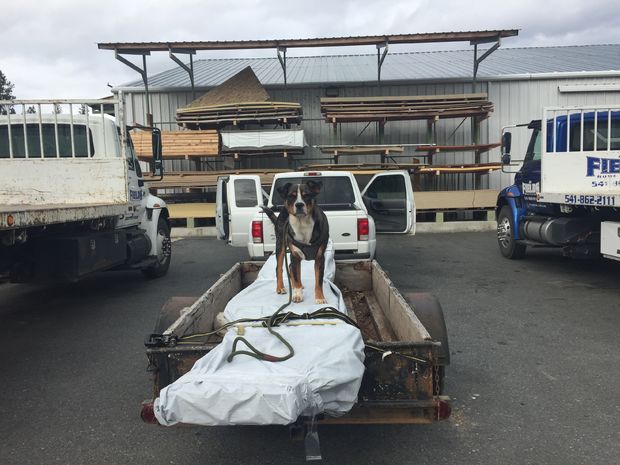
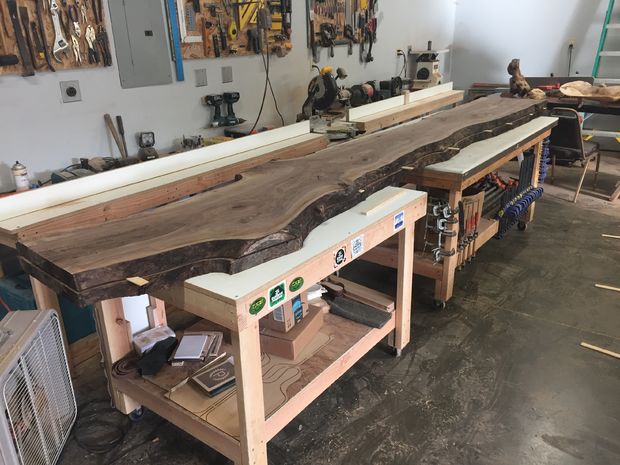
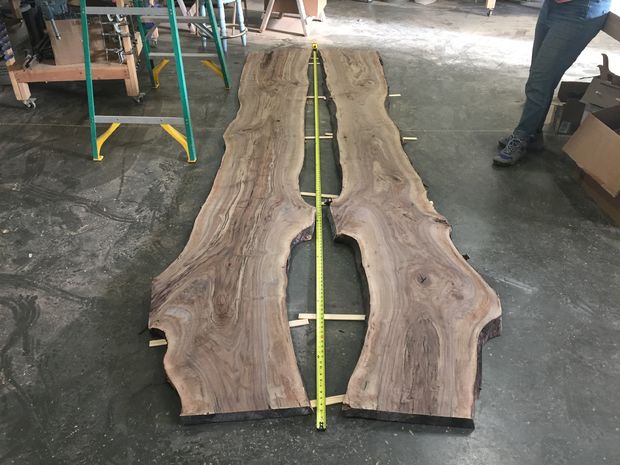
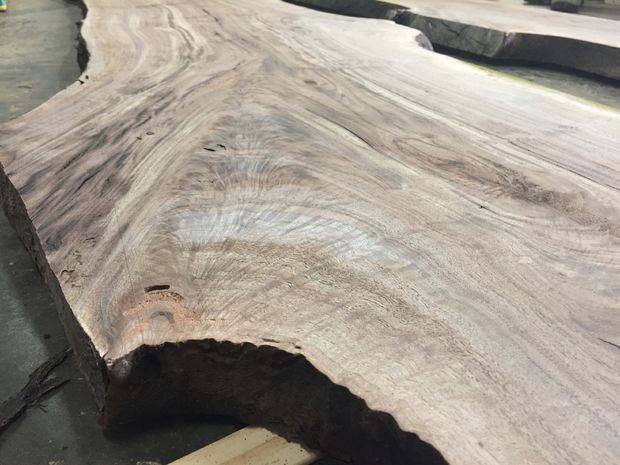
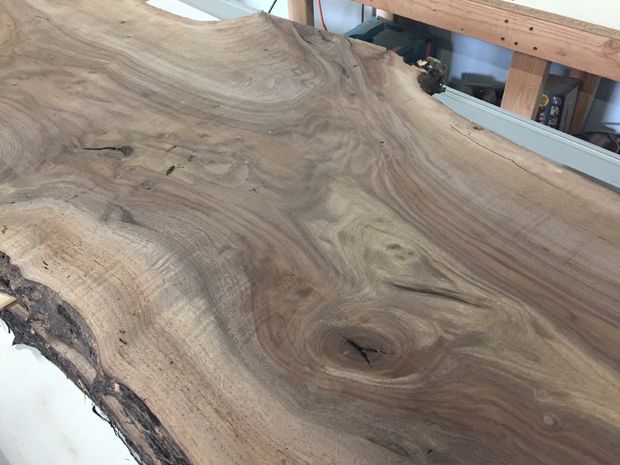
Не считаю этот этап основным, но он может длиться довольно долго. Значительная часть времени, энергии и бензина были потрачены на посещение различных лесопилок и складов с деревом в поисках подходящего материала. Это походило на подвиг, учитывая установленные требования по ширине. Мне нужно было найти две доски с необработанными краями, и, положив их рядом, суммарная ширина должна составлять необходимые 100 см. Их форма должна была образовывать пустоты для размещения коллекции агатов заказчицы. Доски должны иметь характерные выраженные узоры. Были еще стандартные требования: доски высушивались в печи или в течении пары лет на воздухе, имеют приятный вид, плоскость без лишних скручиваний, короблений, надрубов (всего, что потребует снятия слоя по толщине). И, конечно, стоимость должна быть разумной.
Поиск обычно начинается с сайтов электронных объявлений в разделе «строительные материалы». Часто местные мастера выставляют на продажу лишние доски по умеренным ценам. Объявления могут размещать и магазины, пытаясь таким образом привлечь больше клиентов. Я нашел несколько достойных вариантов поблизости, но не было ничего, что удовлетворяло бы всем требованиям. После этого я заглянул к некоторым местным лесорубам, которые распиливают бревна на доски. У этих ребят часто есть собственные пилорамы, и они продают доску по хорошей цене, потому что бревна им достаются дешево или бесплатно, и качество не всегда самое высокое. Но этот вариант тоже не сработал, поэтому мне пришлось двигаться дальше в магазины и склады. Очевидно, что здесь уже появился выбор, но по очень высокой цене.
Наконец я нашел то, что мне было нужно в местном магазине. Не совсем в магазине. Оказалось, что у его владельца есть собственная пилорама и склад, на котором полно досок с необрезными краями. У него было несколько штабелей ореха из которых можно было сделать выбор. Здесь я и нашел то, что искал. У досок была идеальная ширина, выпилены из одного бревна (сохранялась симметрия), сушились в правильных условиях на протяжении 3-х лет, красивые и плоские, а цена была относительно недорогой. К ним прилагался бонус. Так как их обработали широким рубанком, то мне не нужно было устранять шлифованием неровно выпиленную поверхность. У меня нет рубанка шириной в 60 см …
Во время поиска я отправлял фотографии заказчице, чтобы получить ее одобрение. Мы оба остановили выбор на этих двух. Наконец можно было приступать к следующему этапу проекта!
Разработка и утверждение дизайна
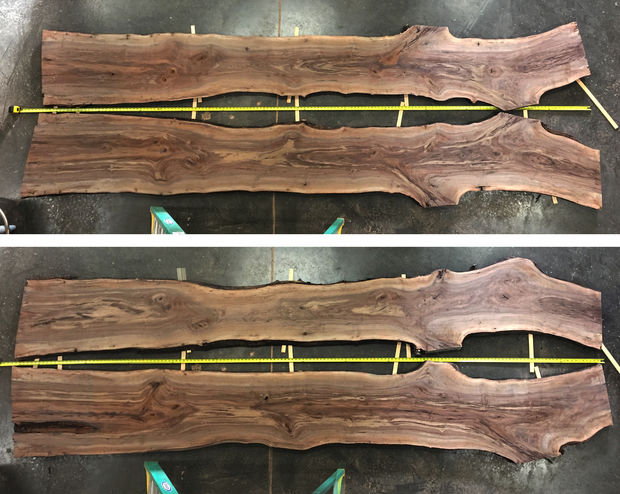
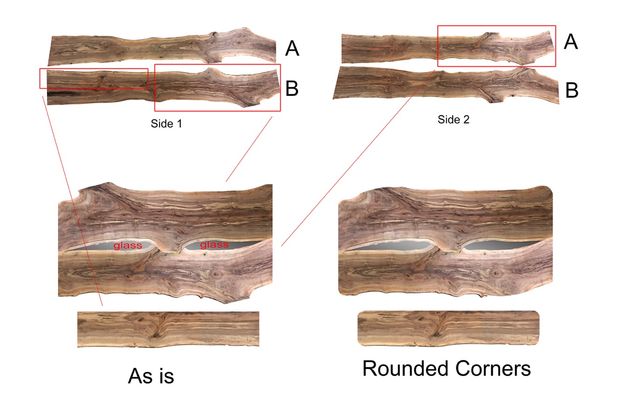
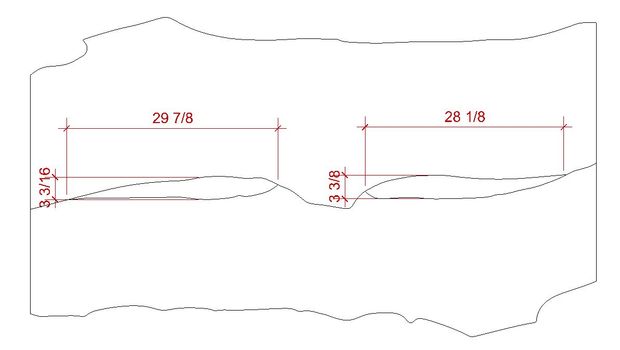
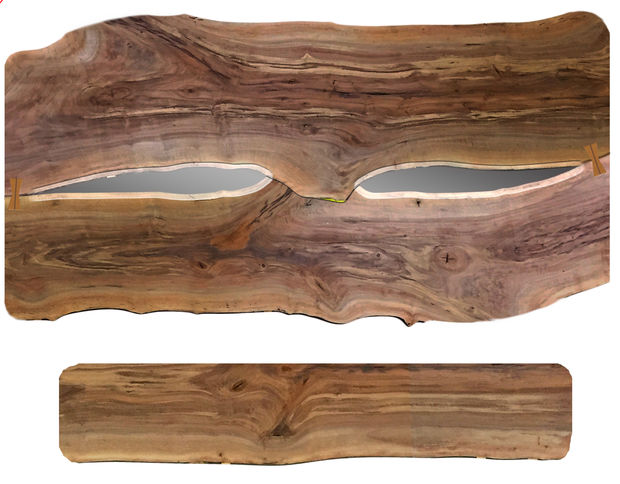
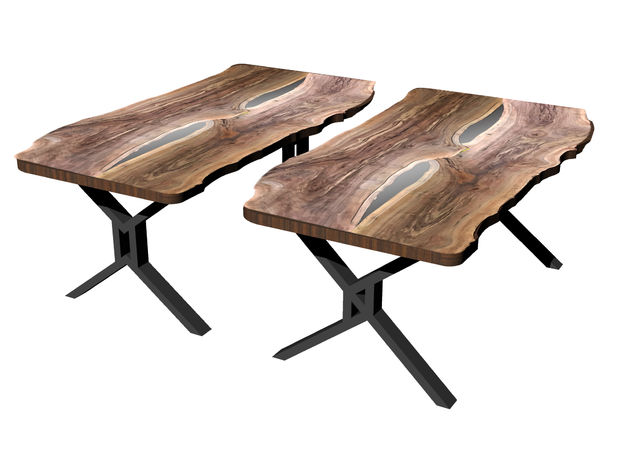
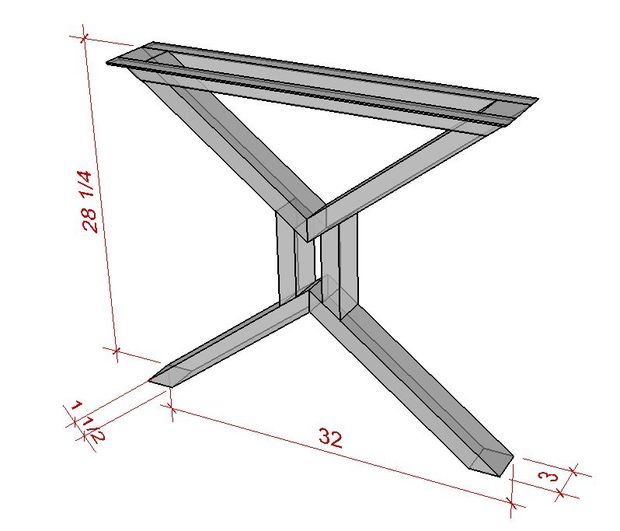
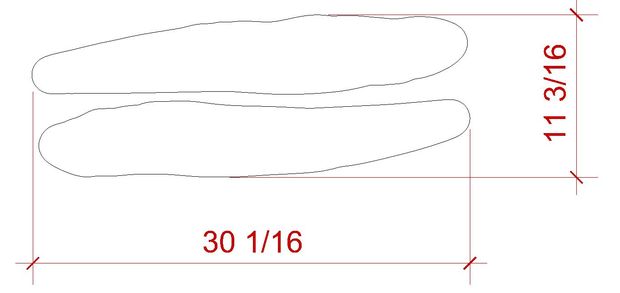
Прежде чем взяться за инструмент, почти каждый мой проект начинается с разработки дизайна в системе автоматизированного проектирования (САПР). С необработанными краями это сделать немного сложнее, так как трудно добиться их повторения в САПР. Я решил проблему поставив высокую лестницу и сделав фото досок по всей длине. Потом импортировал снимки в программу и обвел контуры. На фотографии была видна измерительная лента, чтобы более точно масштабировать графику.
После проектирования электронных моделей, я наложил на них реальный снимок поверхности досок, чтобы заказчице было проще представить, что я собираюсь делать. После того, как мы определились с дизайном, я спроектировал разные элементы, то как они будут взаимодействовать и крепиться друг к другу.
Для этого проекта я рисовал вектором разные проекции модели для всевозможных целей. Нарисовал очертания центральных полостей и экспортировал их в файл DXF, который затем отправил в стекольную компанию, чтобы они мне вырезали такие же формы. Этот же файл я использовал для изготовления шаблона с очертанием полости, по которому можно будет вырезать поликарбонатные пластины, которые будут крепится с нижней стороны столешницы. Шаблоны и поликарбонат я вырезал на своем самодельном фрезерном станке с ЧПУ. Еще я вырезал шаблон для фиксации частей металлических ножек, чтобы правильно их приварить. Я даже лазером вырезал профили различных металлических частей, которые мне будут помогать резать детали ножек под правильным углом. Спроектировав полную модель в САПР можно начинать работу, или по крайней мере с ней работать будет намного легче.
Подготовка досок (шпаклевка трещин, фиксация сучков, шлифовка)
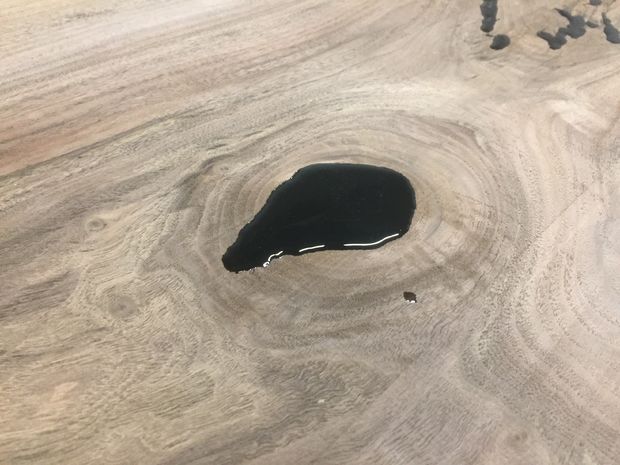
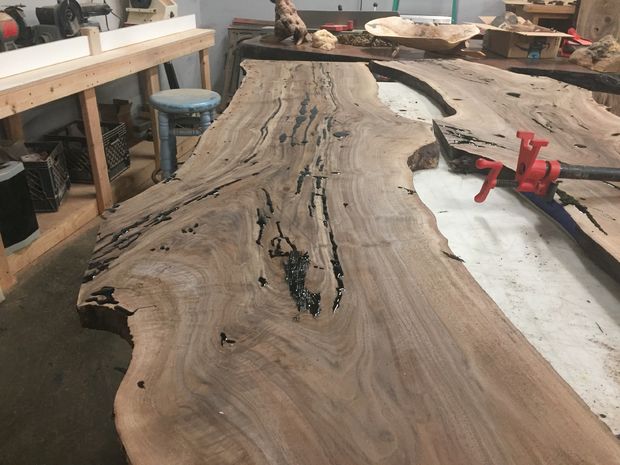
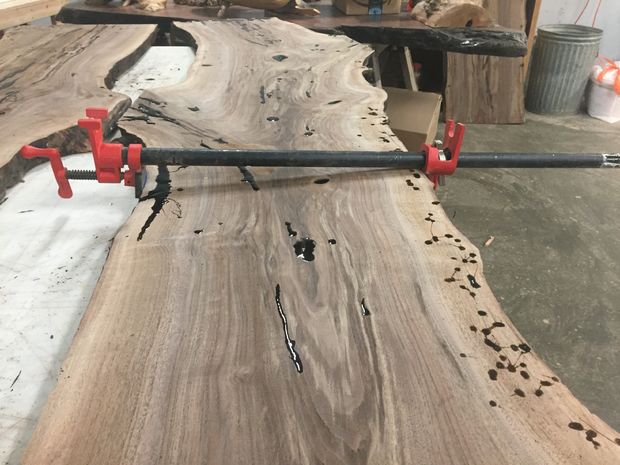
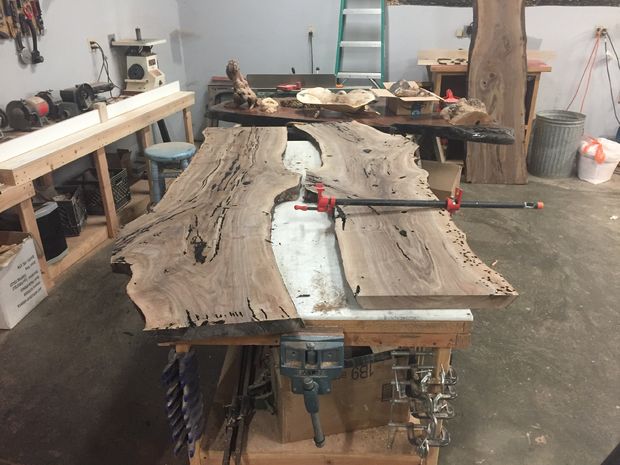
В большинстве случаев мне нравится, когда все сучки, трещины, пустоты фиксируются и заполняются черной эпоксидной смолой, особенно при работе с орехом. Черный цвет чаще всего выглядит естественно, а иногда придает контрастность. Так как в досках то тут, то там были довольно глубокие трещины, я использовал смолу с долгим временем застывания; это позволит ей хорошо впитаться и поможет действительно зафиксировать трещины, а не создать иллюзию заполнения. Недостаток этого метода в том, что почти всегда приходится снова наносить смолу второй, а бывает и третий раз. Иногда для повторной обработки я использую смолу с быстрым временем отвердения. Я заполнил все пустоты на обеих сторонах досок, чтобы их можно было надежно фиксировать. Наносить эпоксидную смолу лучше с «горочкой», чтобы при шлифовке не обнаружились пузыри (так они поднимутся выше плоскости доски).
После заполнения всех пустот я обработал выступающие части эпоксидной смолы абразивом с зерном P60.
Придание формы в местах соединения
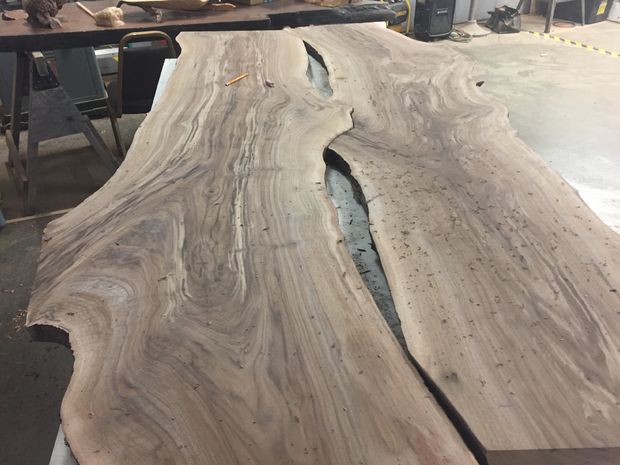
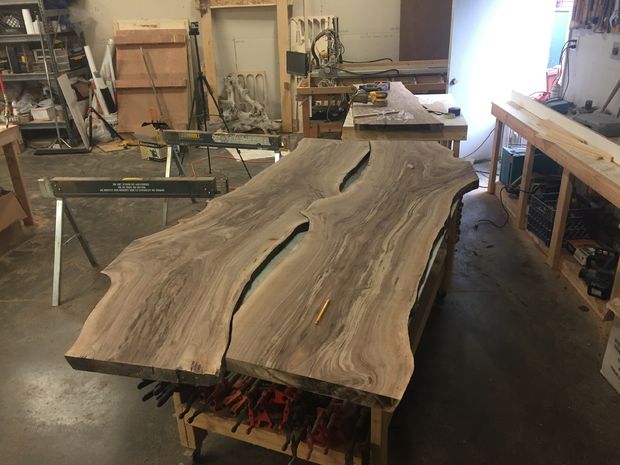
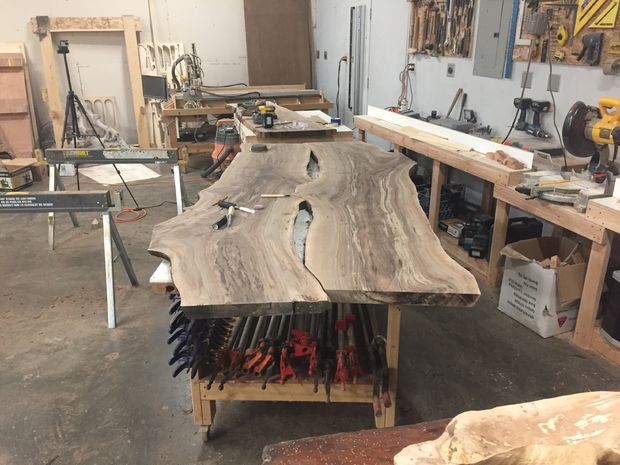
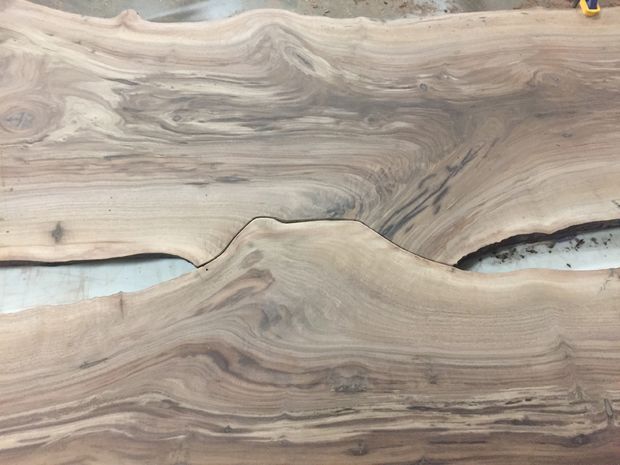
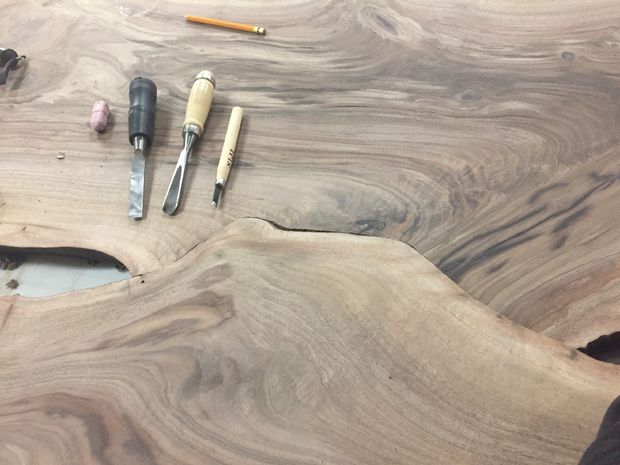
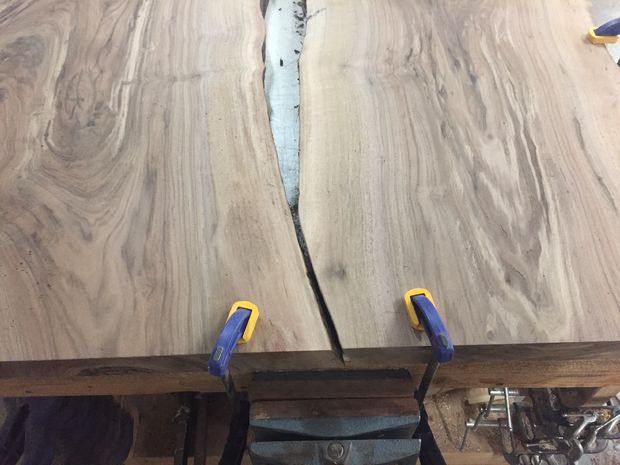
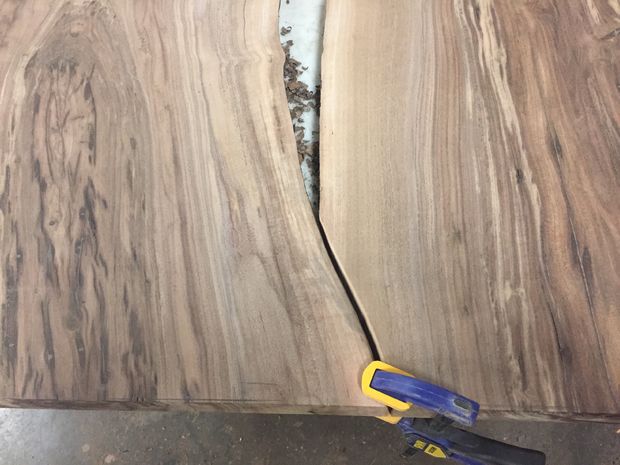
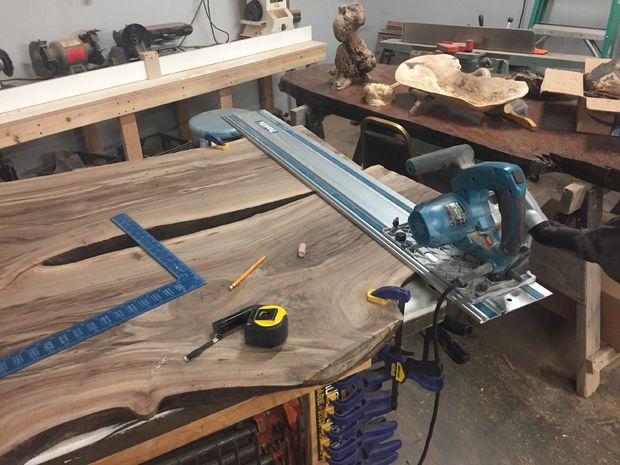
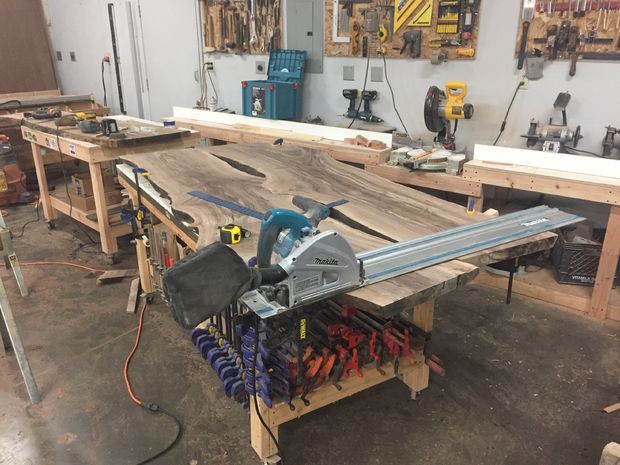
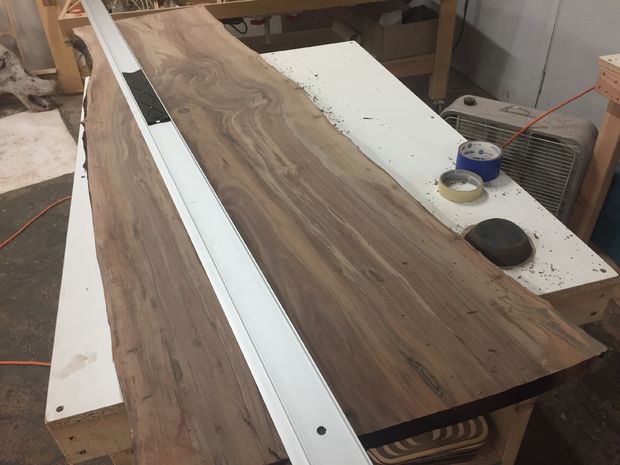
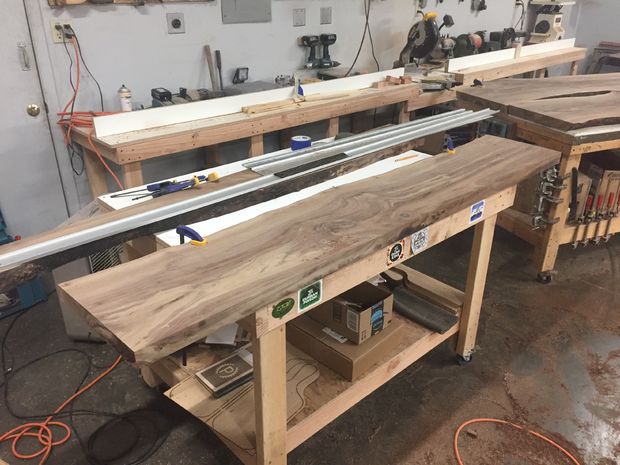
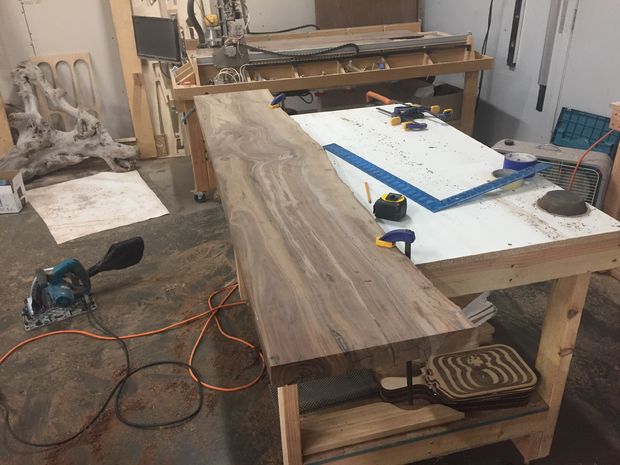
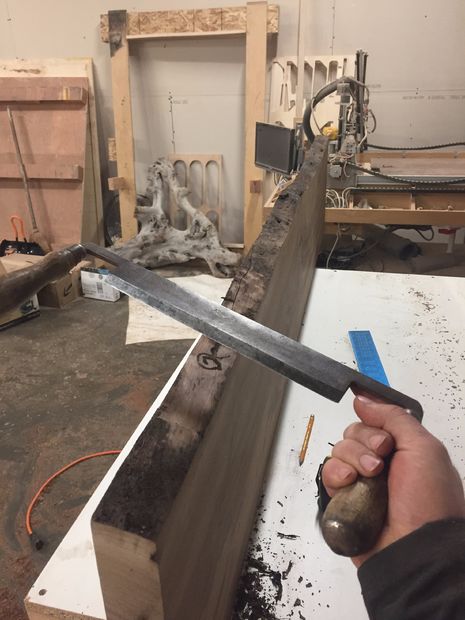
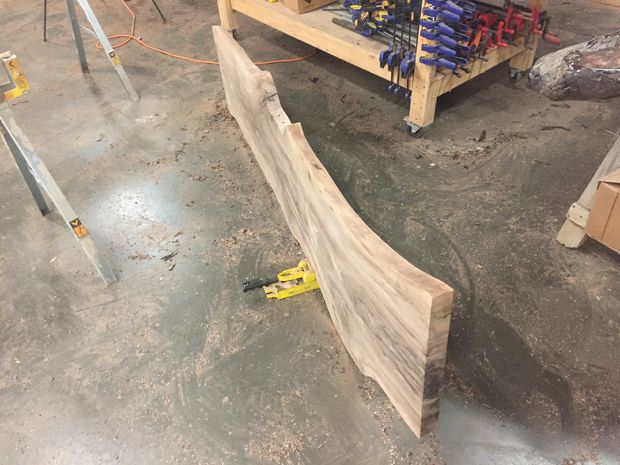
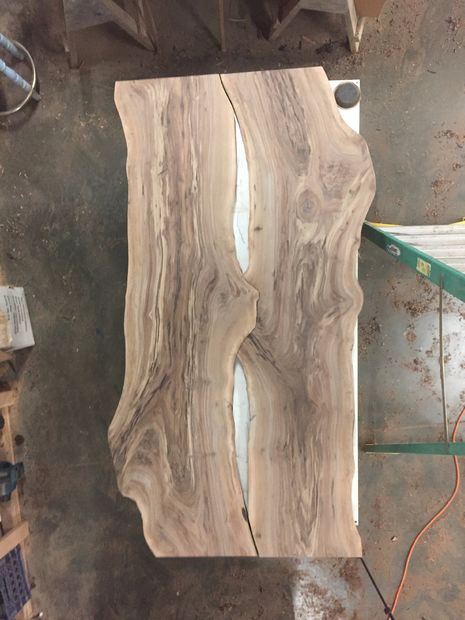
К сожалению этот этап я не особо задокументировал. По существу, я положил одну доску на другую в необходимом положении, и разметил область для удаления. Непосредственно для работы я использовал электролобзик, угловую щлифмашину (с диском-фрезой и лепестковым диском), и там, где необходимо, ручные инструменты для резьбы по дереву. На этом этапе было много тонкой работы и подгонки. По всей длине между досками я оставил шов толщиной примерно в 4 миллиметра. Я подумал, что так стол будет выглядеть более выразительно. С другой стороны, бесшовная подгонка оставляет углы, что не очень хорошо выглядит. Толщина шва будет сохранятся благодаря шпонке «ласточкин хвост». Затем я выровнял края стола с помощью дисковой пилы.
Во время этого этапа я скобелем очистил необработанные края от остатков коры как на столе, так и на скамейке. Затем я прошелся по ним еще угловой шлифовальной машиной с лепестковым диском, чтобы необрезные края стали более гладкими.
В скамейке одну необработанную сторону я обрезал дисковой пилой. Я согласовал с заказчицей, что у скамейки одна сторона будет прямой.
Соединение досок при помощи шкантов и шпонок
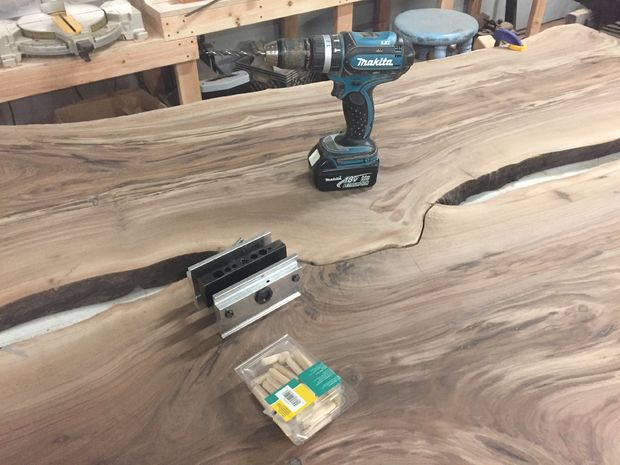
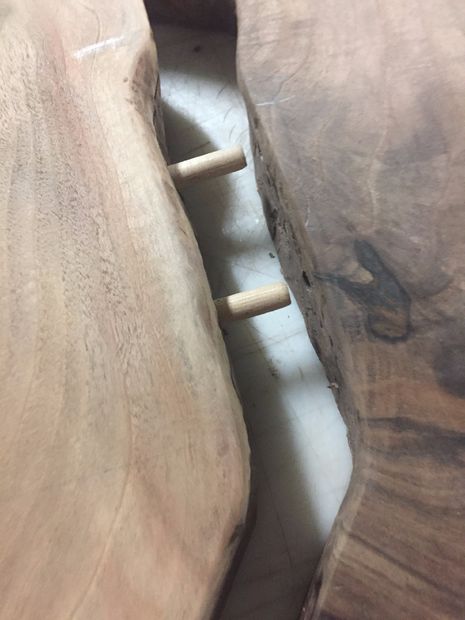
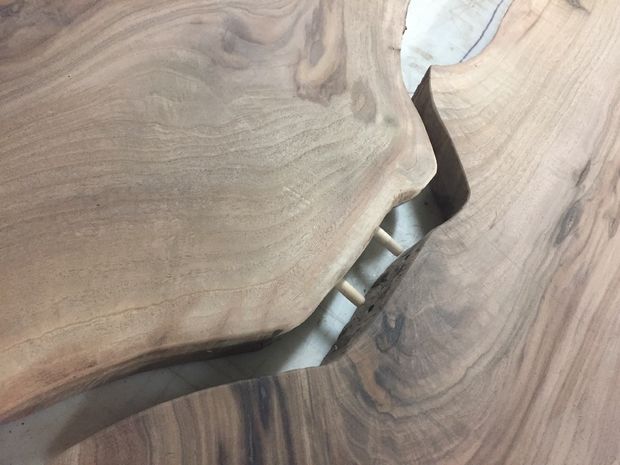
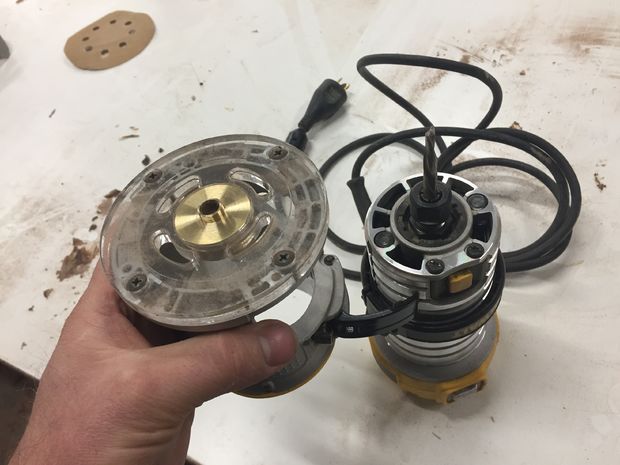
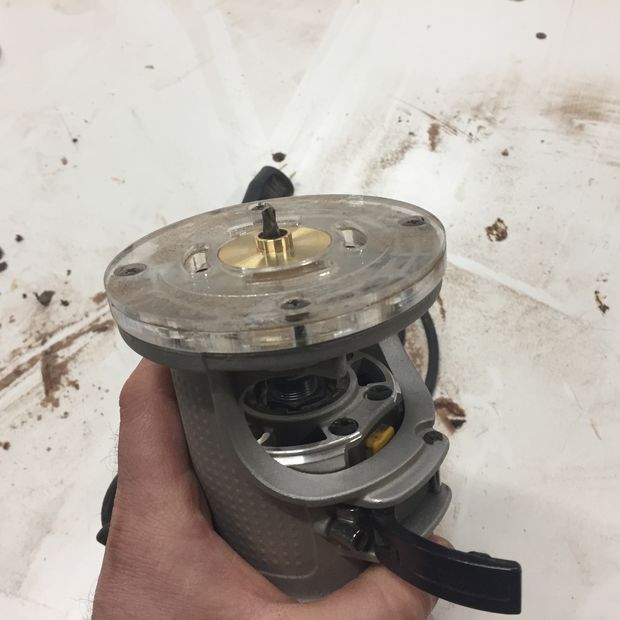
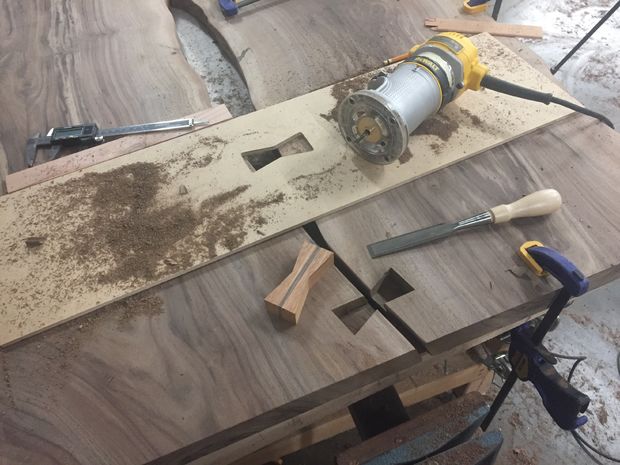
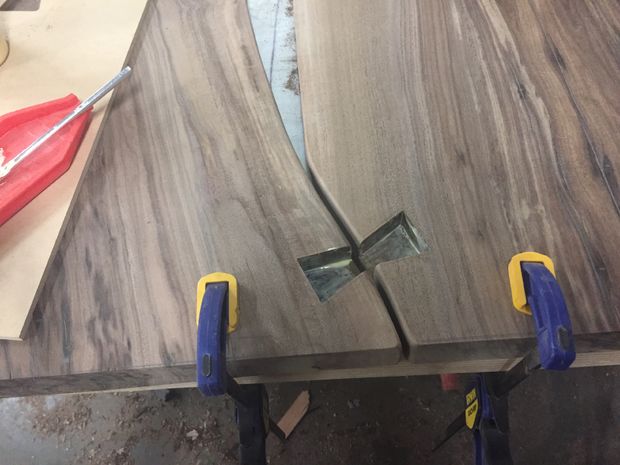
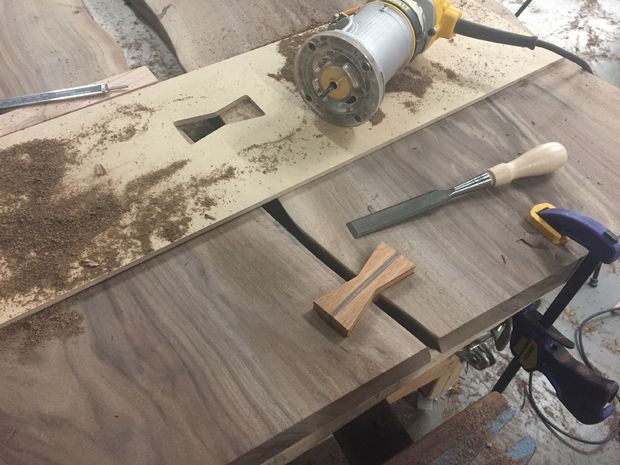
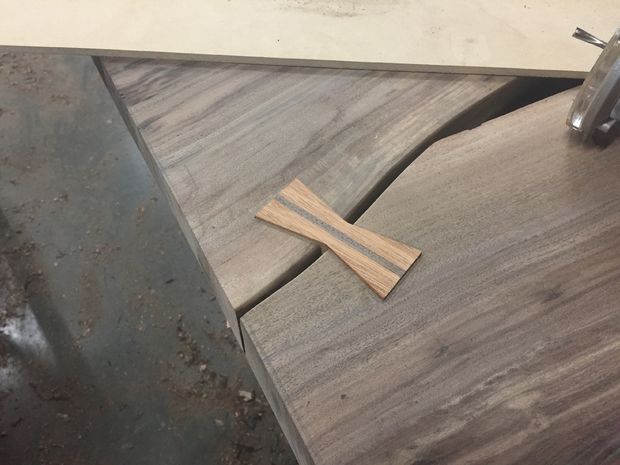
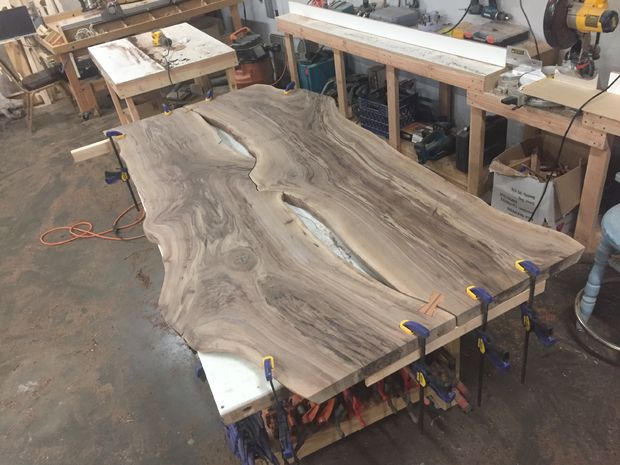
Для соединения центральных частей я использовал шканты. Они служат для фиксирования двух досок в одной плоскости (по отношению друг к другу). На шпонки и ножки стола ляжет основная нагрузка по фиксации столешницы. В отличии от шпонок, которые мне довелось встречать, эти я сделал толщиной почти равной толщине досок.
Материал для шпонок был сделан из склейки листа ореха между двумя листами махагони, а станок с ЧПУ вырезал форму. Еще я сделал шаблон, который поможет вырезать пазы для шпонки с помощью ручного фрезера.
После выравнивания шва между досками, я зафиксировал их к столу при помощи струбцин. Затем, используя шаблон, я фрезером вырезал пазы. Там, где фрезер оставил паз округлым мне пришлось поработать стамеской. Можно было сделать «ласточкин хвост» с округлением, но мне нравится вид ровных углов.
Когда пазы для шпонки были готовы, я осторожно попробовал вставить «ласточкин хвост» (чтобы убедиться, что он не застрянет!) и приступил к склеиванию. Шпонки были сделаны немного толще, чем пазы, поэтому были зашлифованы вровень со столешницей.
После того, как данный этап был закончен, я зашлифовал все поверхности переходя от зерна P60 к P180. Финальная шлифовка зерном P220 была проведена непосредственно перед полированием.
Вставка стекла, поликарбоната и LED-освещения
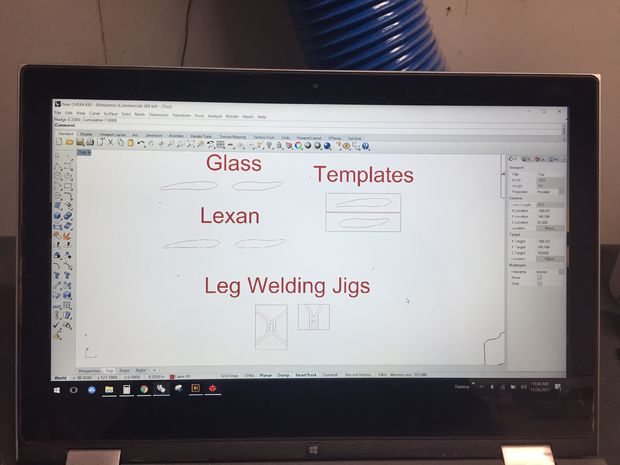
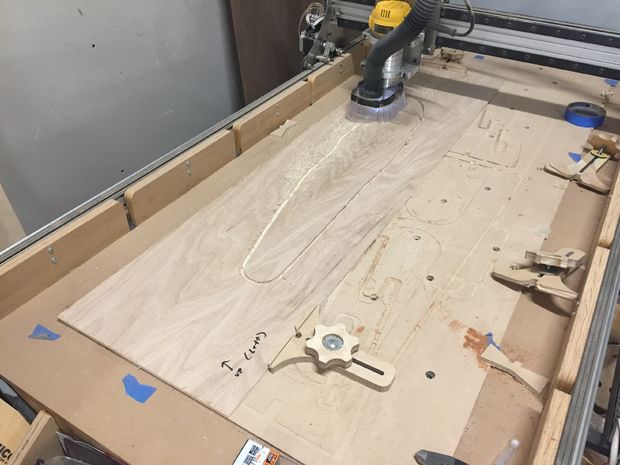
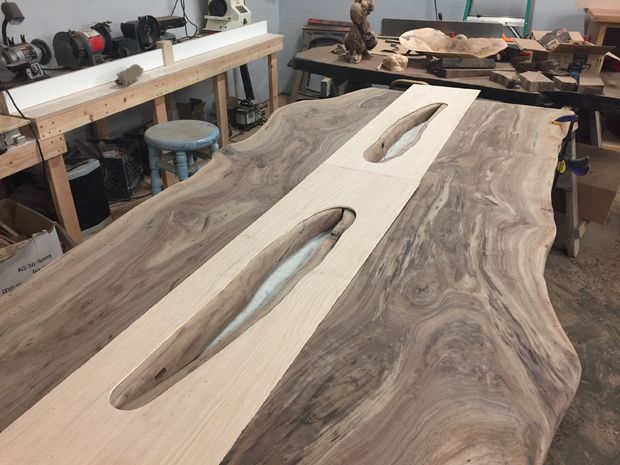
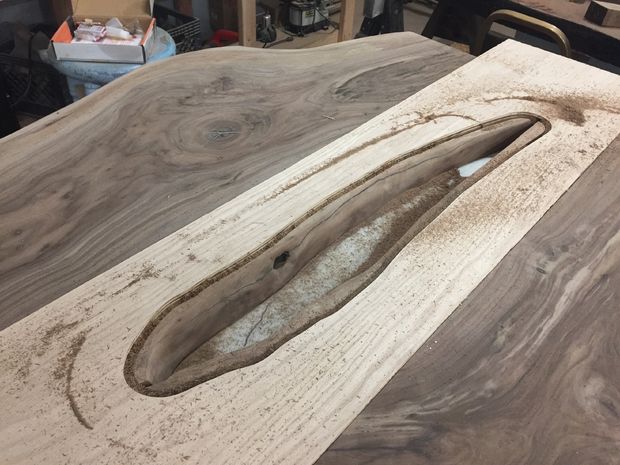
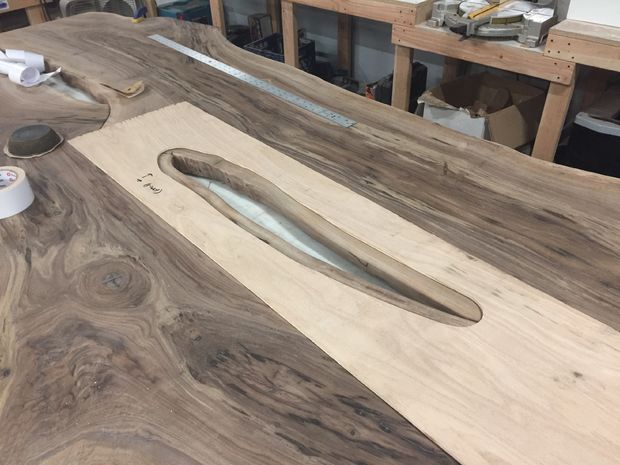
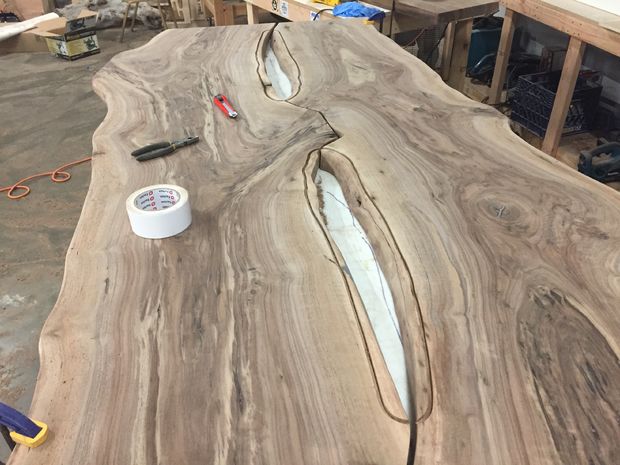
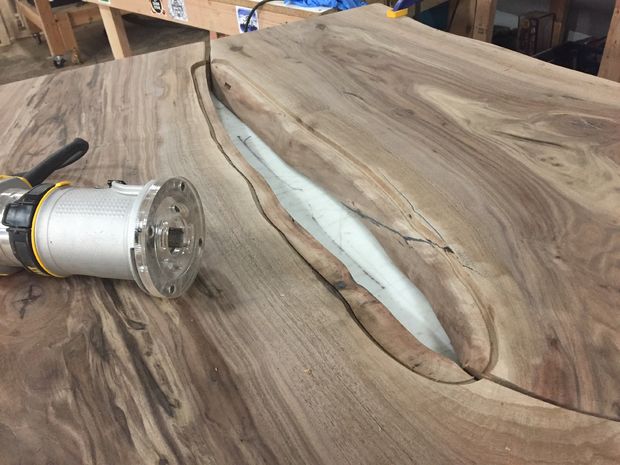
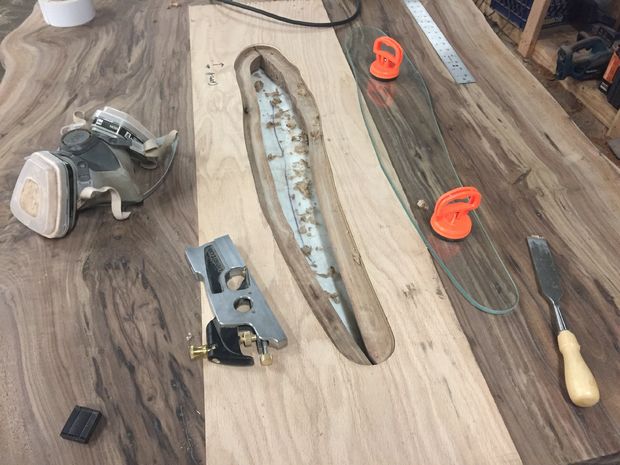
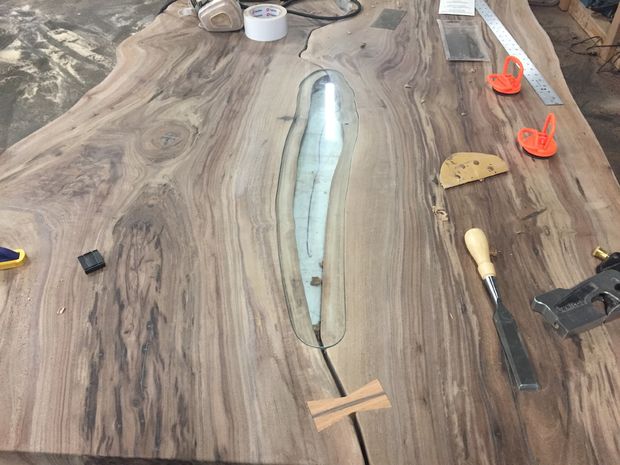
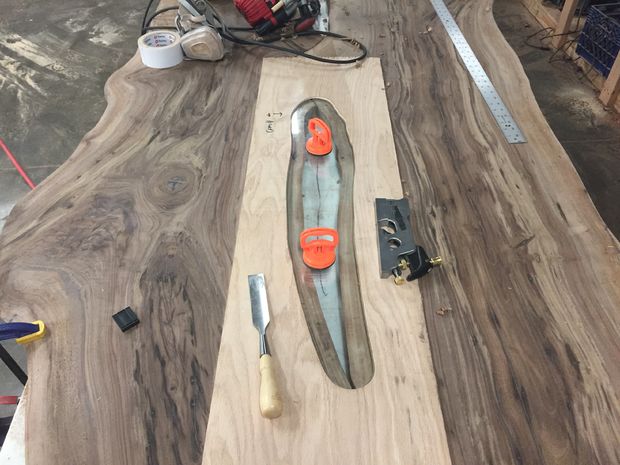
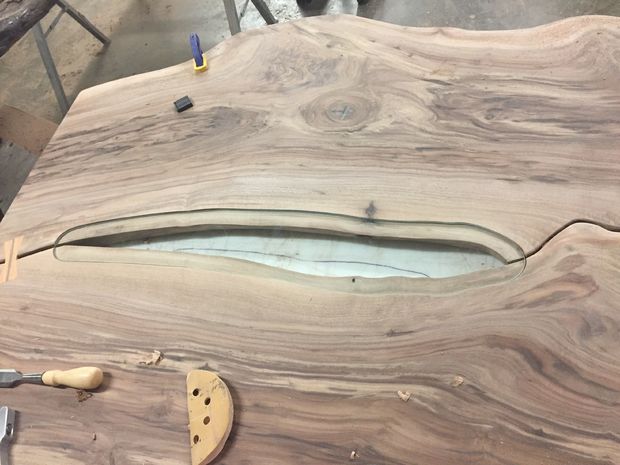
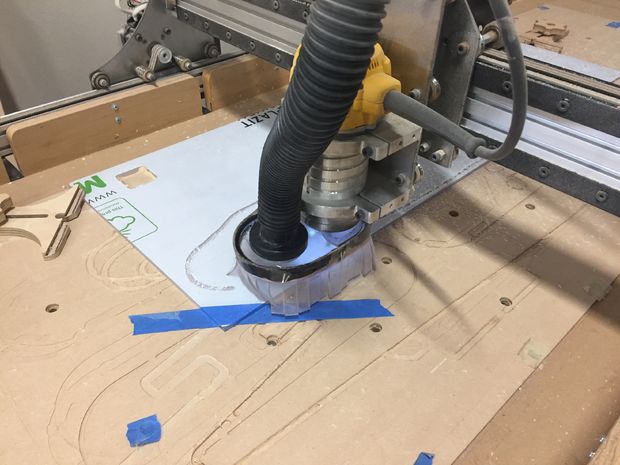
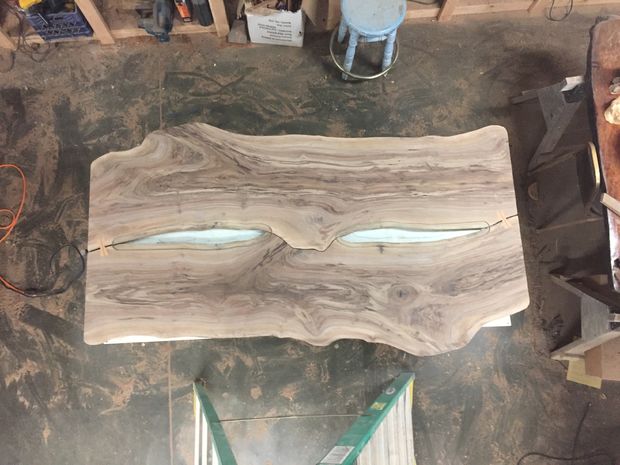
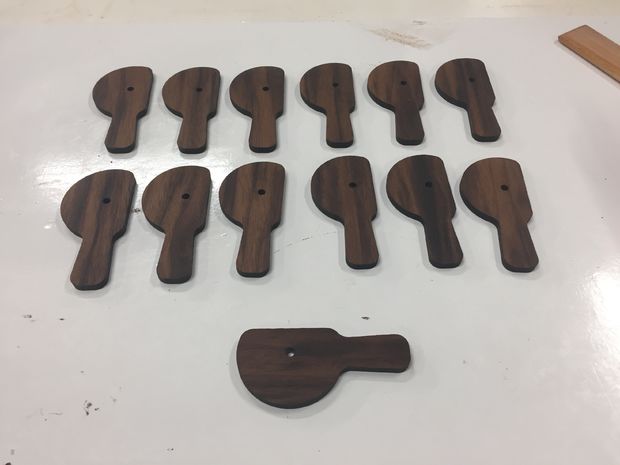
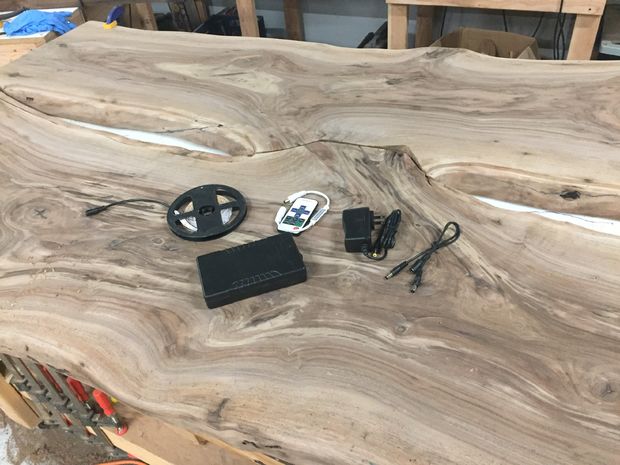
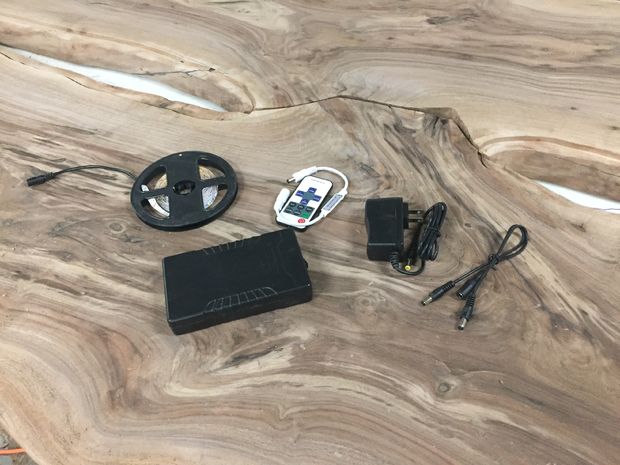

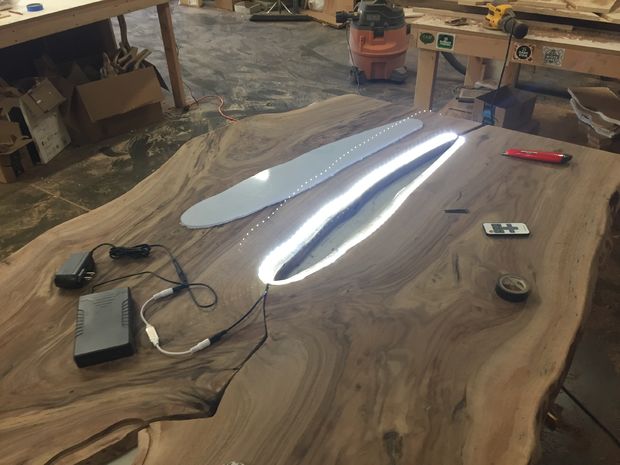
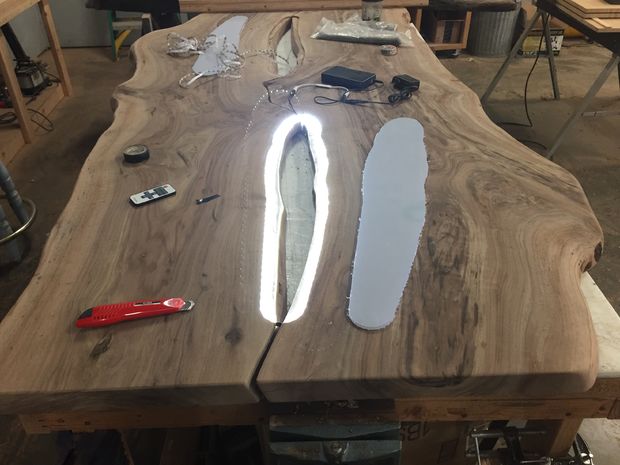
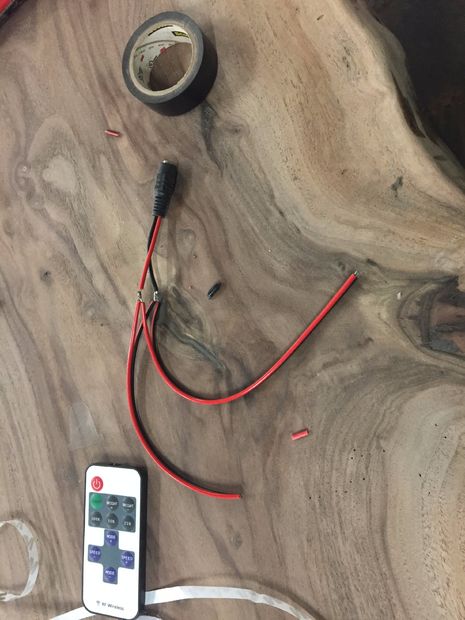
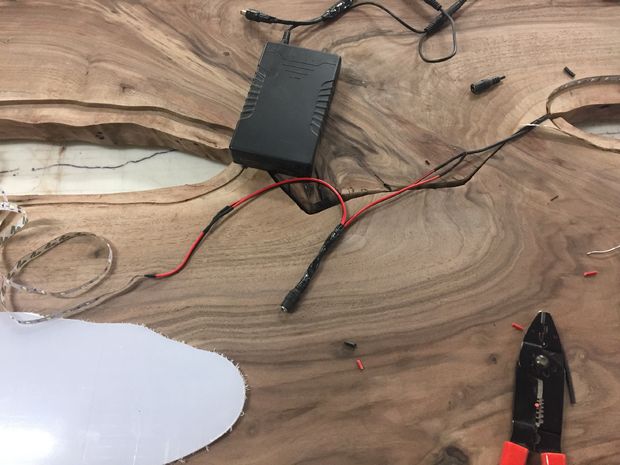
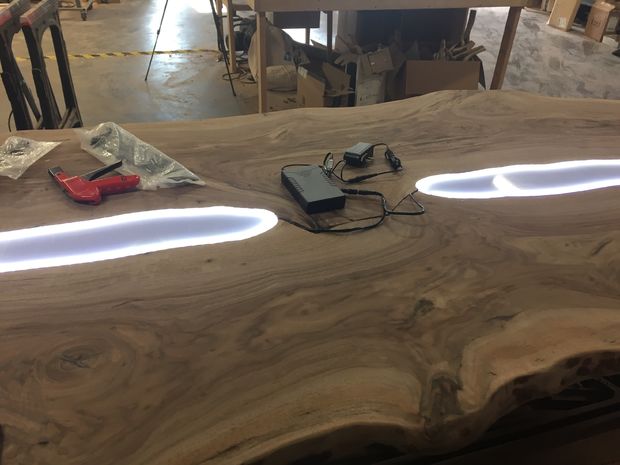
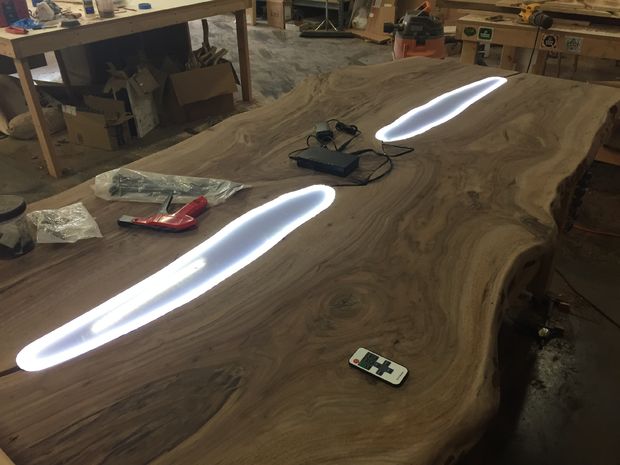
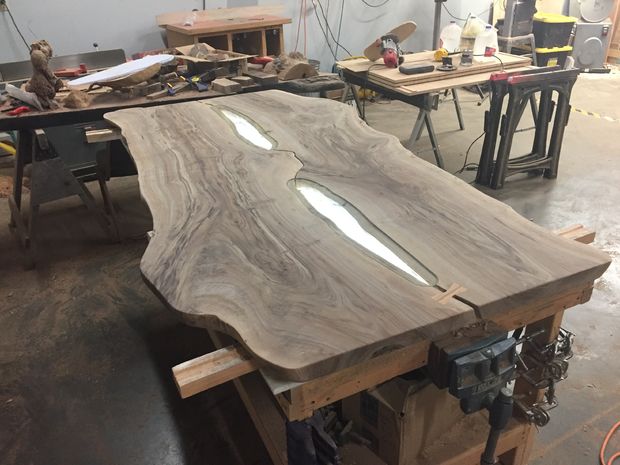
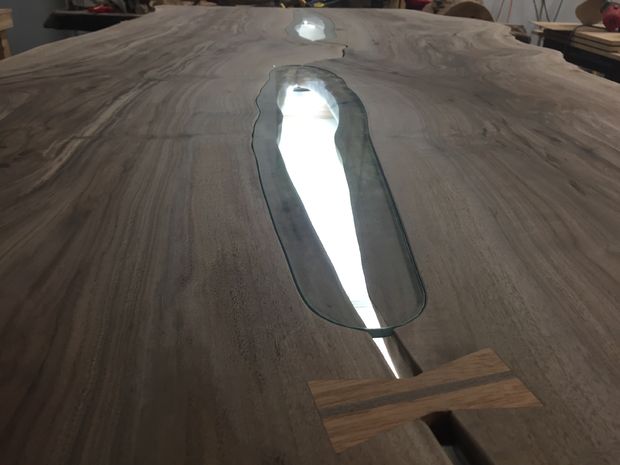
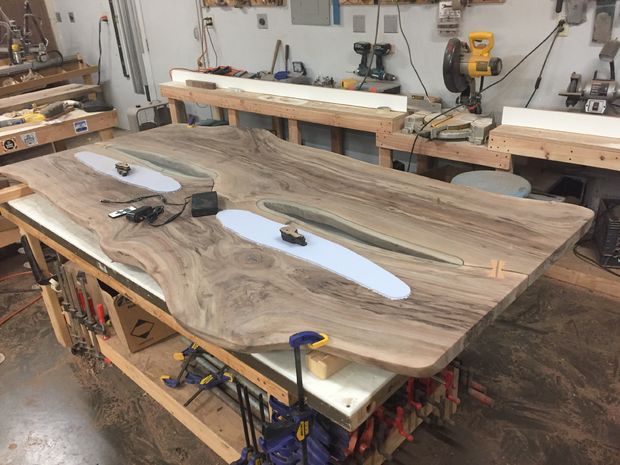
Я использовал модель САПР для создания вставок для стекла и поликарбонатной пластины. Двусторонний скотч отлично подошел для временной фиксации заготовок на поверхности стола. Затем я снова воспользовался ручным фрезером для создания пазов на обоих сторонах досок. Для более точной работы я использовал зензубель и стамеску, пока стекло не легло ровно и фиксировалось без колебаний. Стекло вынималось и вставлялось много раз, для этого я использовал присоски.
Вставки из поликарбонатного листа были подготовлены с помощью станка с ЧПУ и торцевой фрезы. Здесь мне нужно было принять решение, как более надежно зафиксировать пластиковые вставки на дне столешницы. Мне хотелось, чтобы их легко можно было снять, например, для замены из-за царапин. Я решил, что флажки-фиксаторы, выполненные из ореха, будут в самый раз. Поэтому я вырезал их лазерным резаком из имеющегося у меня материала.
Прежде чем вставлять пластик, мне нужно было разобраться со светодиодной подсветкой. Для более изысканного эффекта я решил разместить LED-освещение по периметру пластика. Этот прием еще поможет скрыть провода. Я приобрел тонкую светодиодную ленту с клеящейся стороной, которую можно легко приклеить по углублению, которое я делал ранее вокруг нижней части полости. Я должен был собрать две отдельные электрические цепи в виде Y, которые затем должны входить в отдельный диммер. Диммер с одной стороны соединяется с аккумуляторной батареей и с другой с 12-вольтовым блоком питания. Это позволяет лампам светиться как от батареек, так и от сети. Идея заключается в том, чтобы хозяева подсоединяли зарядное устройство, когда не пользуются столом, и можно было бы убирать провода, когда они им будут мешать. Провода и батарея были закреплены на дне столешницы при помощи хомутов и анкеров. Я рассматривал вариант встраивания батареи и проводов в дерево, но окончательно решил, что лучше не стоит, так как все эти компоненты когда-то придется заменять. В конце концов этот стол должен стать семейной ценностью, которая переживет меня, клиента и светодиодные лампы. Говорят, что LED-лампы могут служить довольно долго, но, если возникнет желание, их можно будет заменить на что-то подобное.
После примерки пластика и проверки работы освещения я отложил пластины в сторону. Запирающие флажки и пластик можно прикреплять после полировки.
Полировка
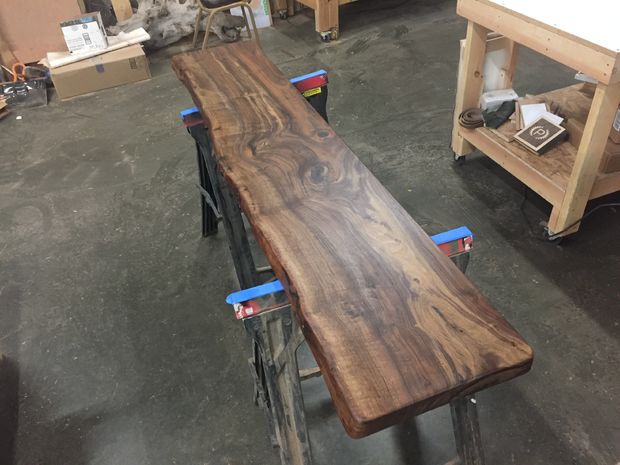
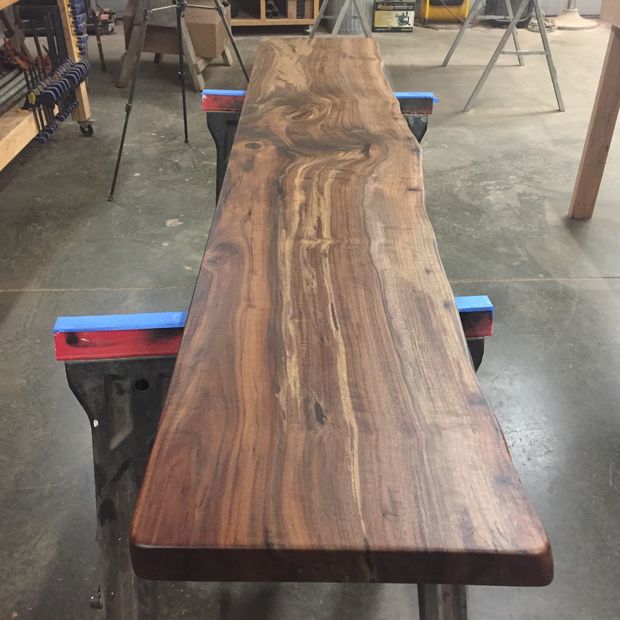
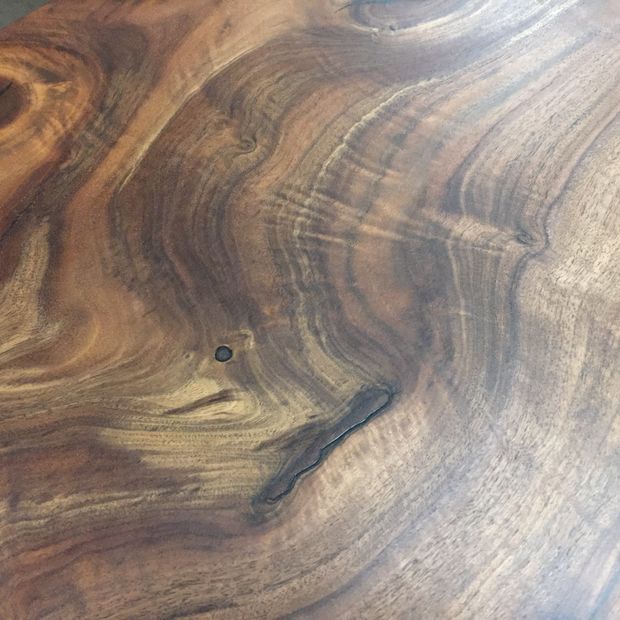
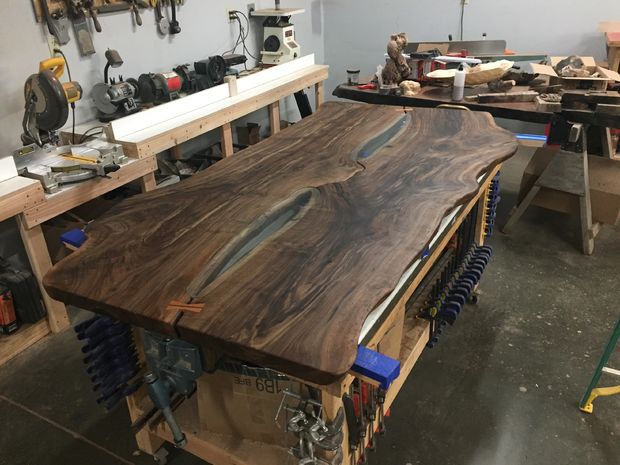
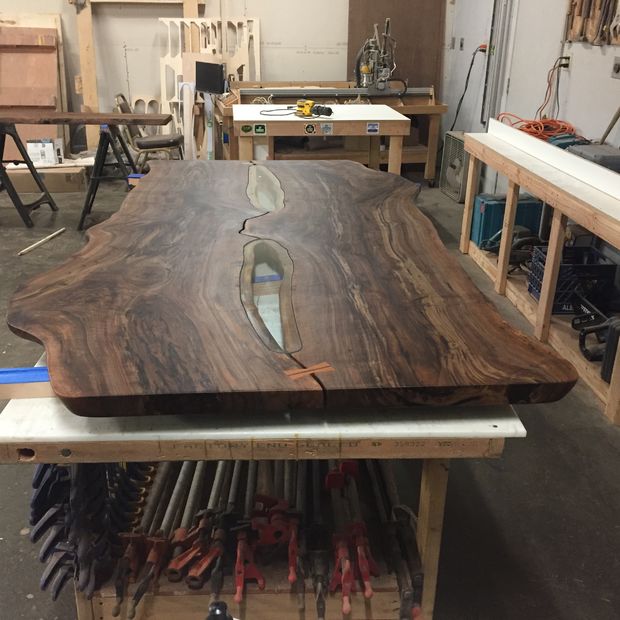

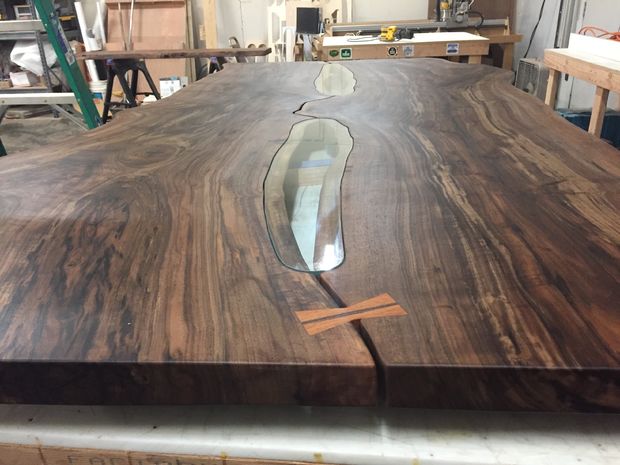
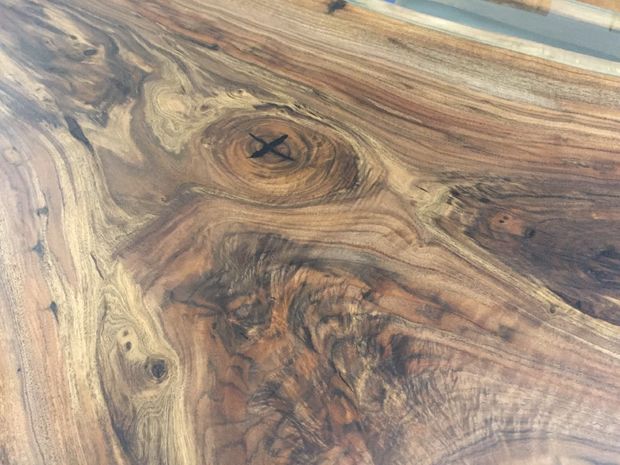
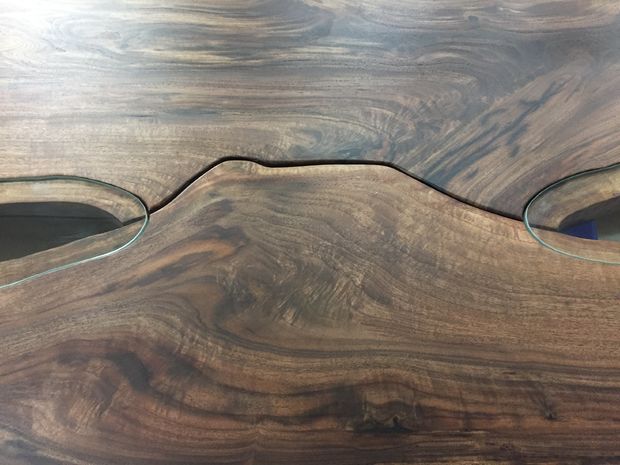
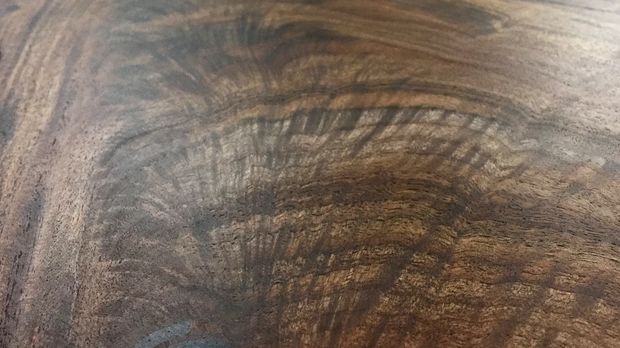
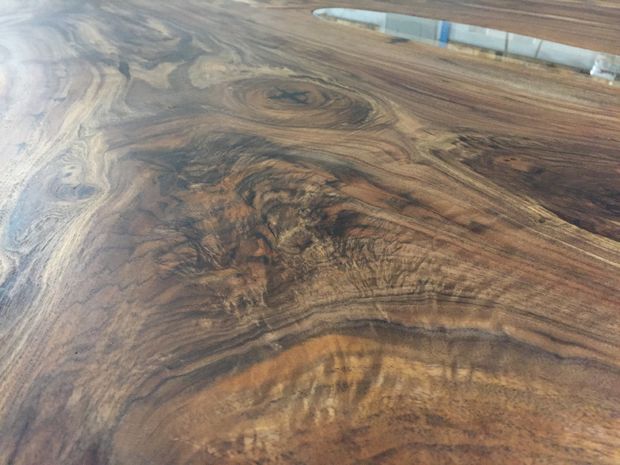
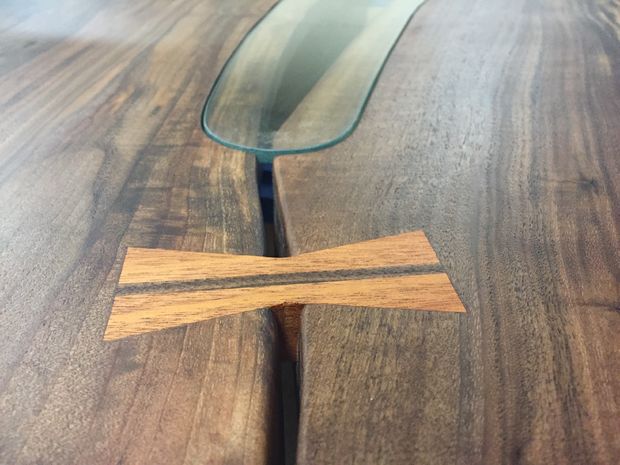
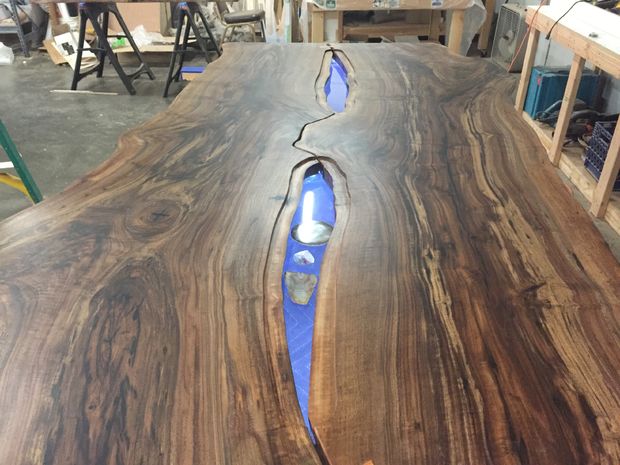
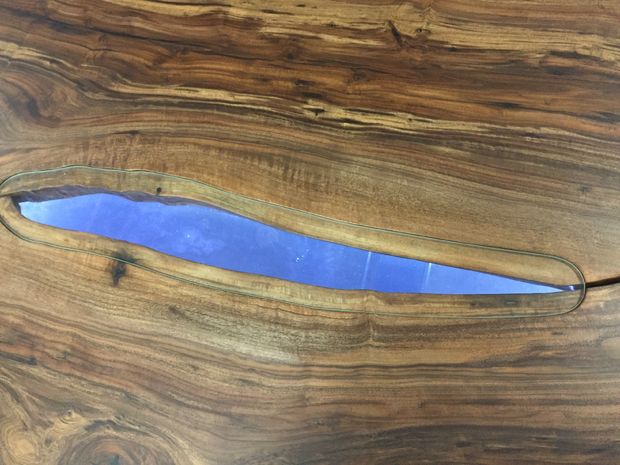
Заказчик пожелал использовать полировочный материал, который сохранит естественный вид дерева, сделает его стойким, но не будет выглядеть, как лак. Поэтому я остановился на OSMO PolyX. Этот продукт задуман для деревянного пола, но и для мебели он хорошо подходит. В нем низкое содержание летучих органических веществ, и высокое содержание твердых, так как в основном он состоит из воска и натуральных масел. Его легко применять. Для достижения хорошего результата достаточно двух слоев.
Я не делал фотографий этого процесса, так как на мне постоянно были резиновые перчатки, вымазанные в полировочную пасту. Прежде чем наносить слои, я еще раз прошелся по поверхностям и краям абразивом с зерном P220.
Чтобы равномерно нанести OSMO на поверхность я использовал шпатель. Им легко было полностью увлажнить дерево и пастой покрыть все мелкие неровности. На краях мне пришлось использовать ткань. После увлажнения я удалил остатки пасты безворсовой тканью. На этом этапе важно хорошенько проработать поверхности, но полностью удалить излишки. Я покрыл верх, низ и все края стола и скамейки, и дал им просохнуть день или два, затем проделал все еще раз. Достаточно только два слоя, и на самом деле, если нанести больше, это может привести к нежелательному глянцевому эффекту.
В итоге обработка деревянных частей была завершена, я уложил поликарбонатные пластины на свои места и закрепил их флажковыми фиксаторами.
Создание ножек и их установка
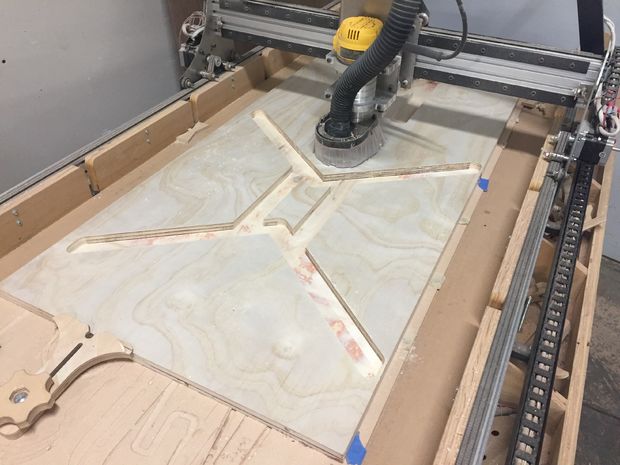
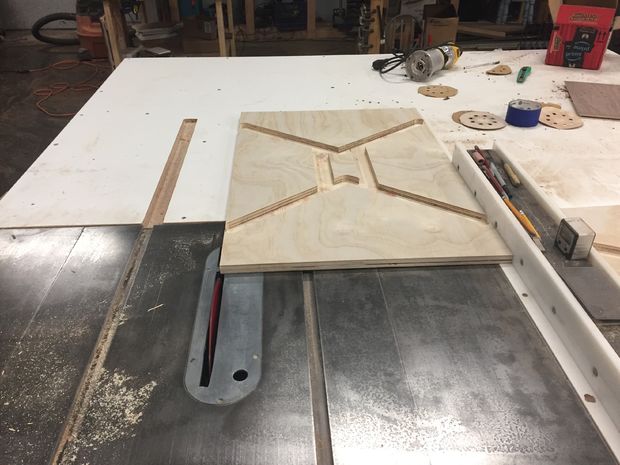
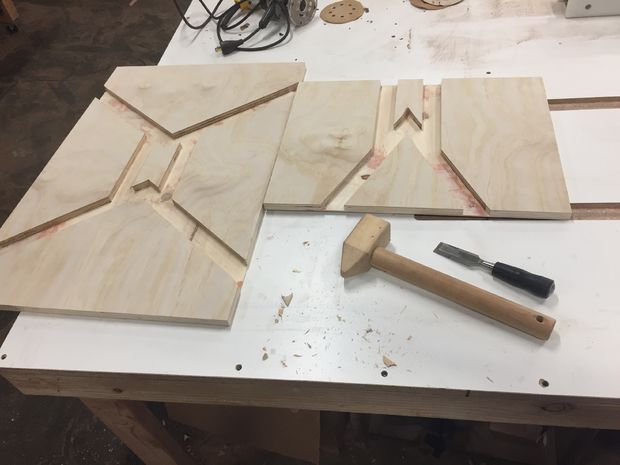
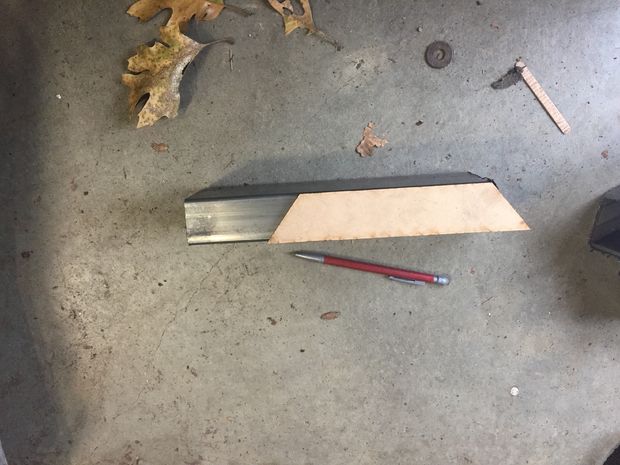
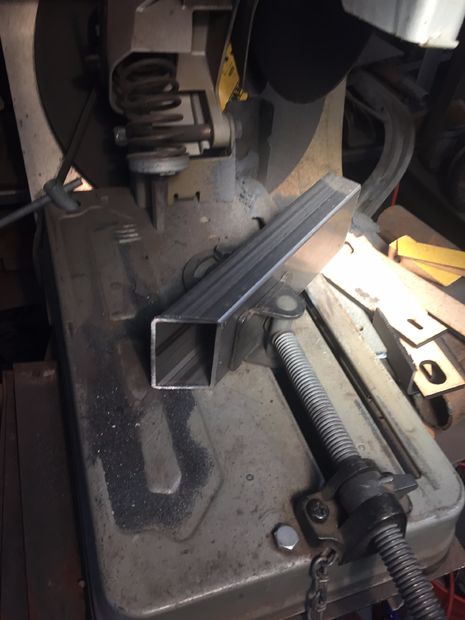
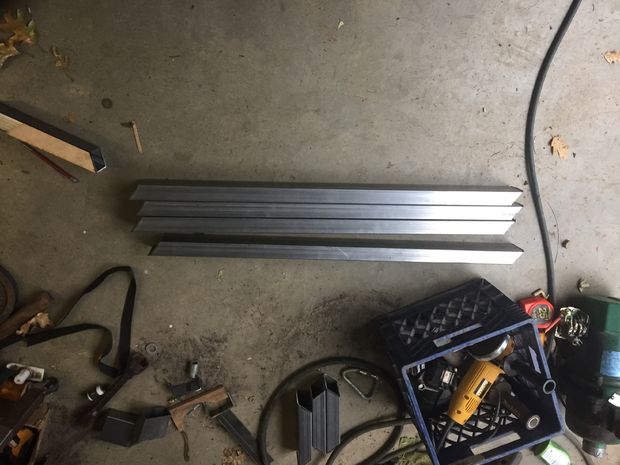
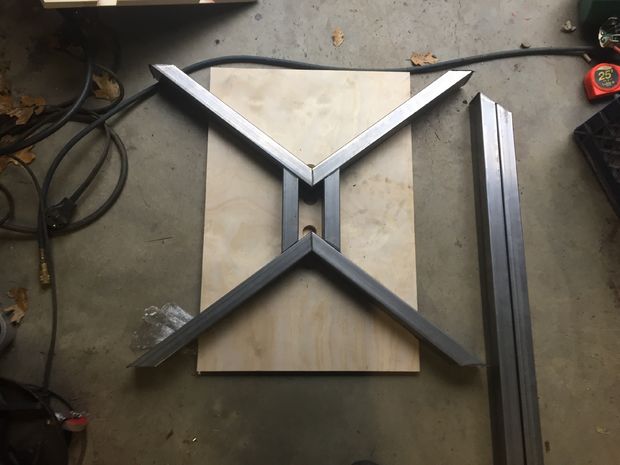
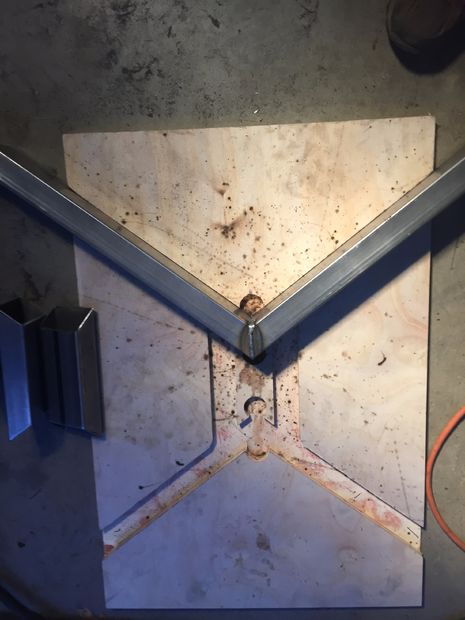
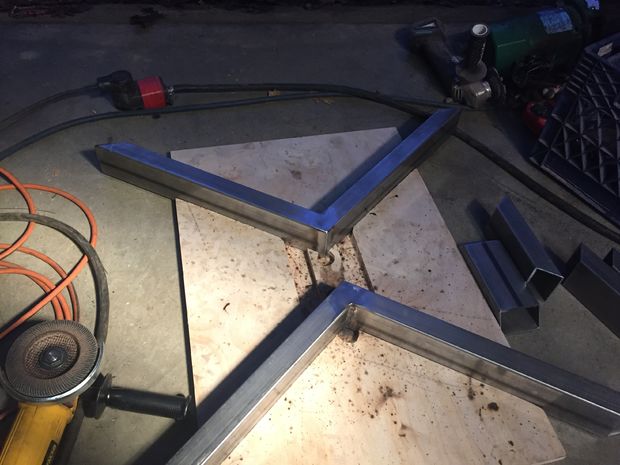

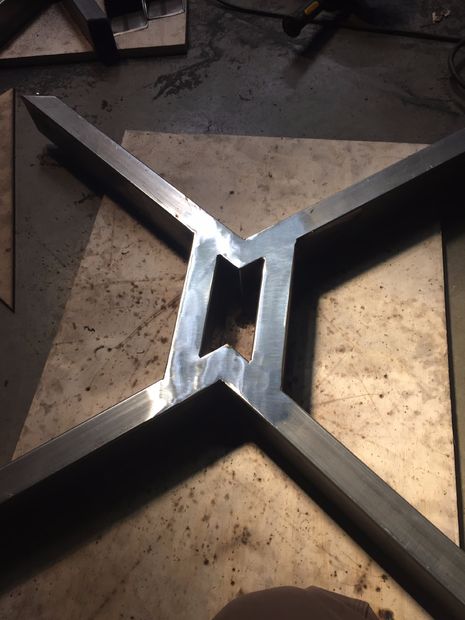
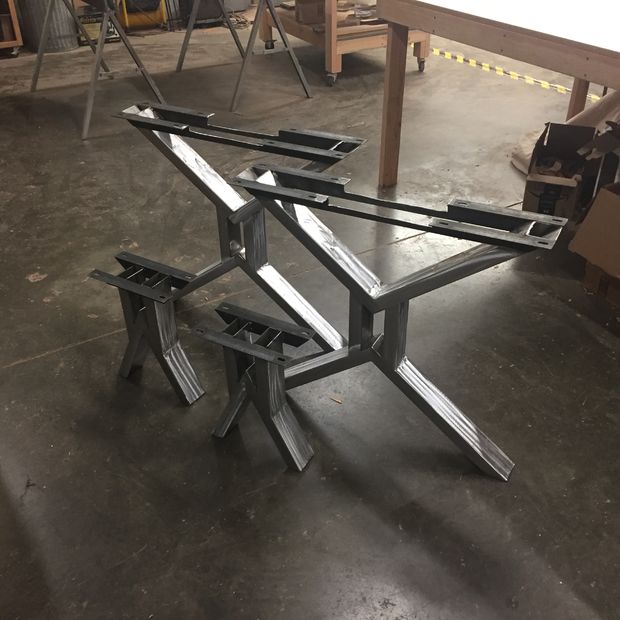
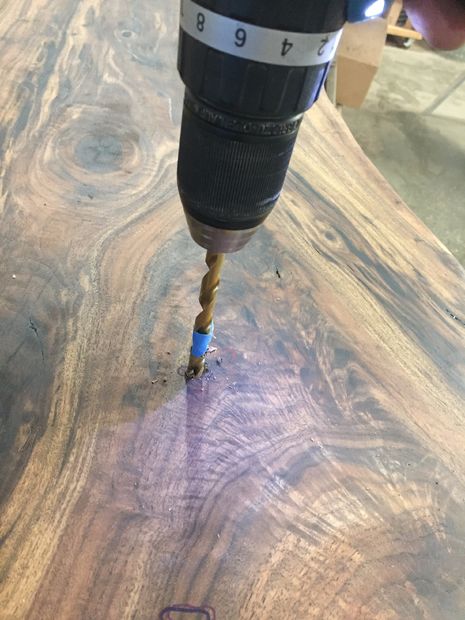
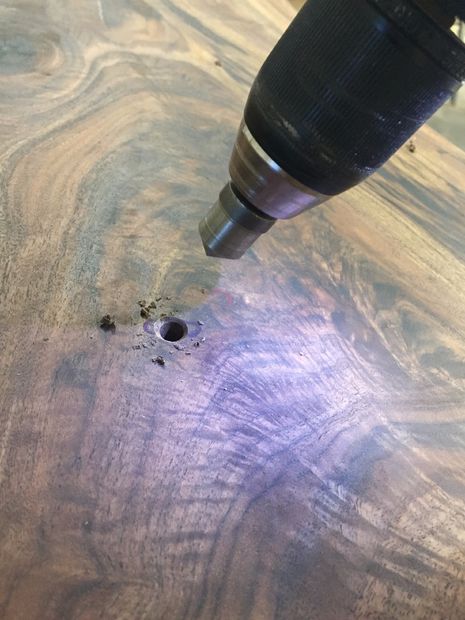
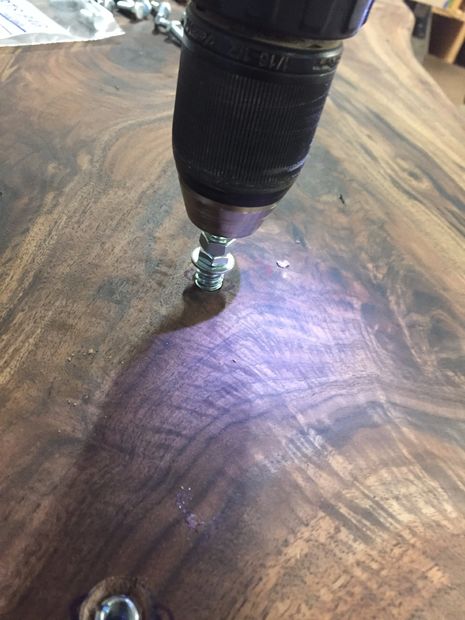
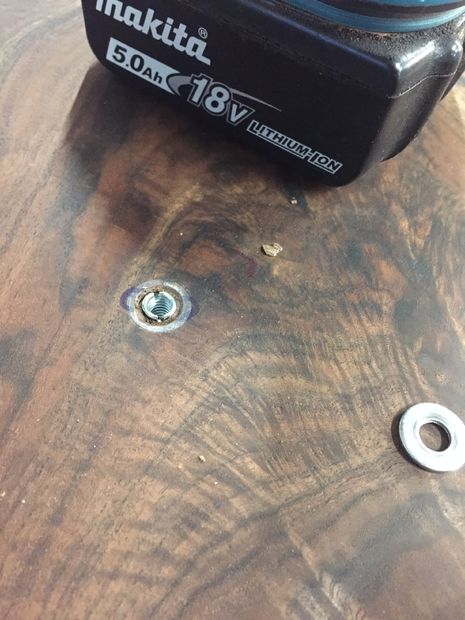

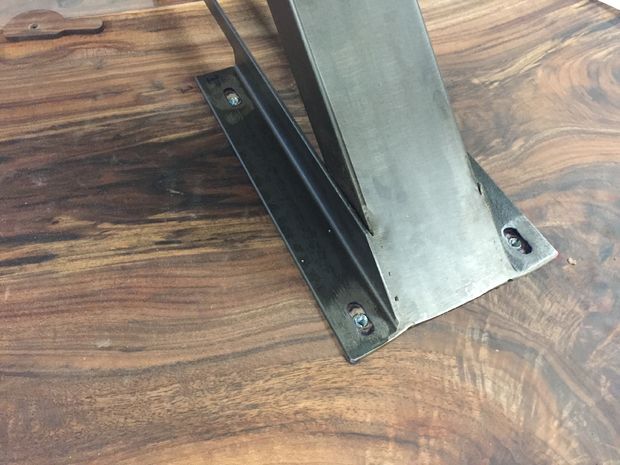
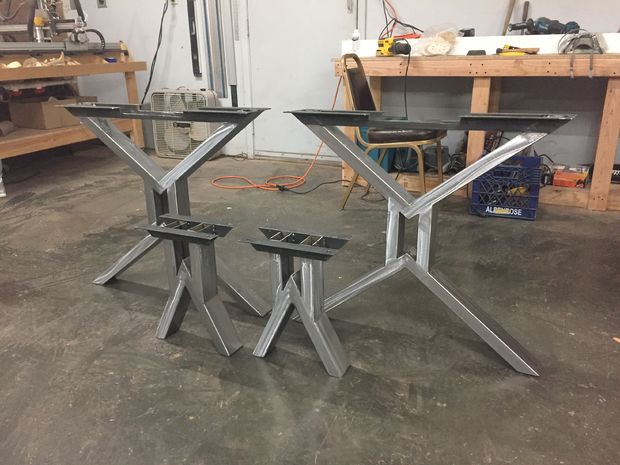
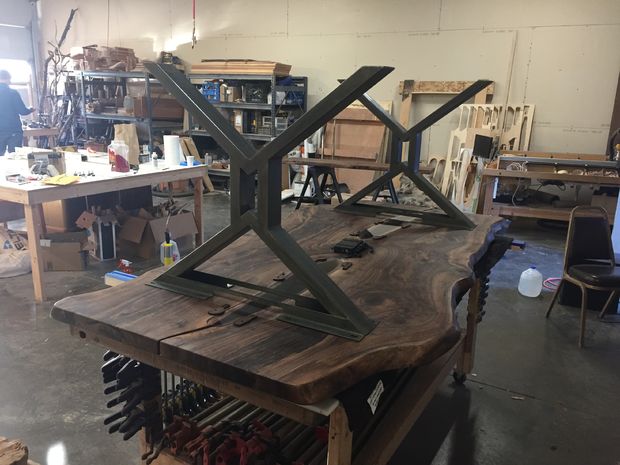
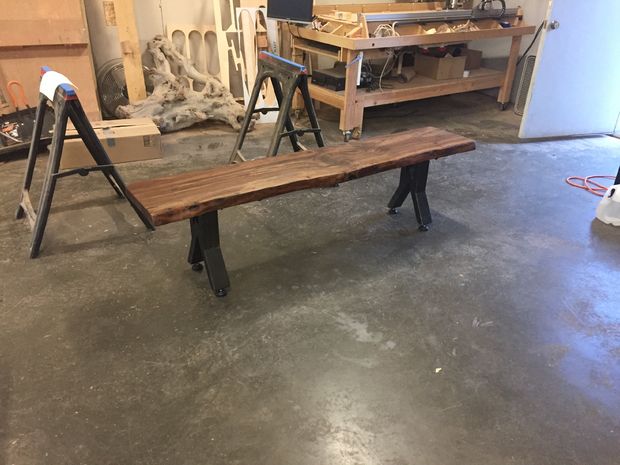
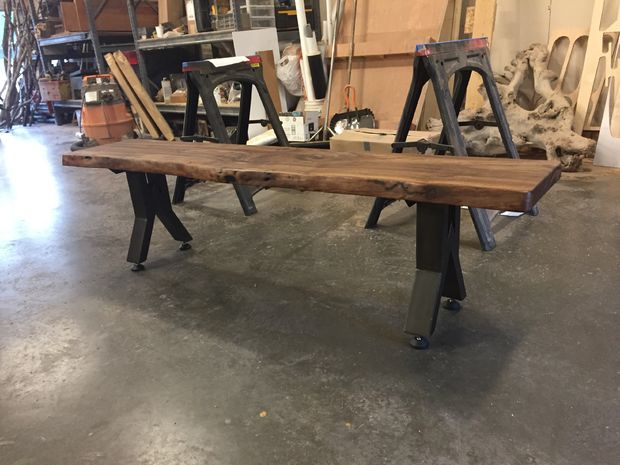
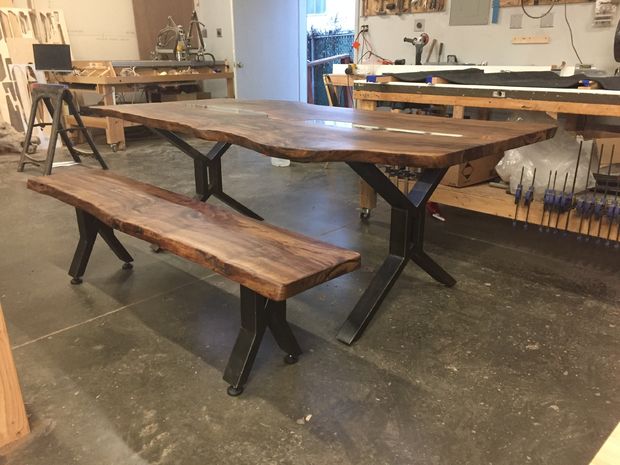
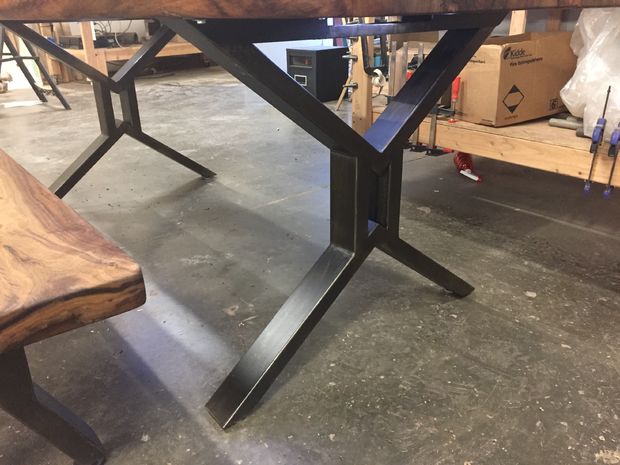
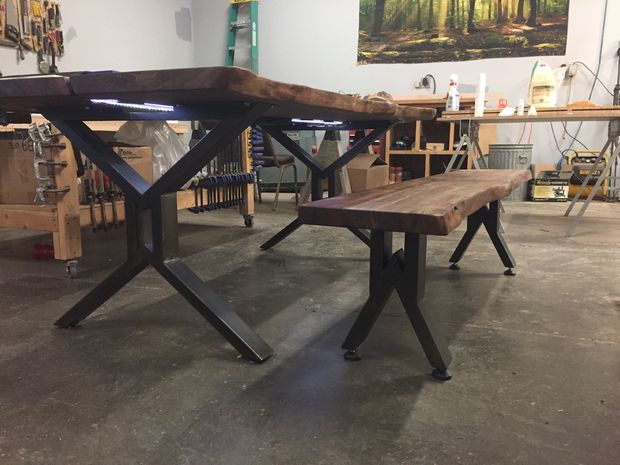
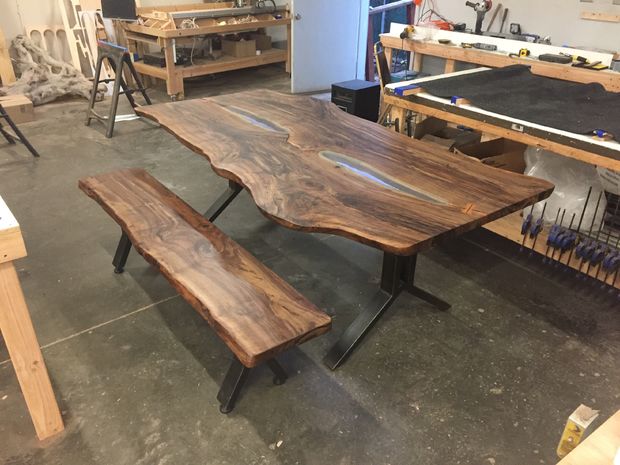
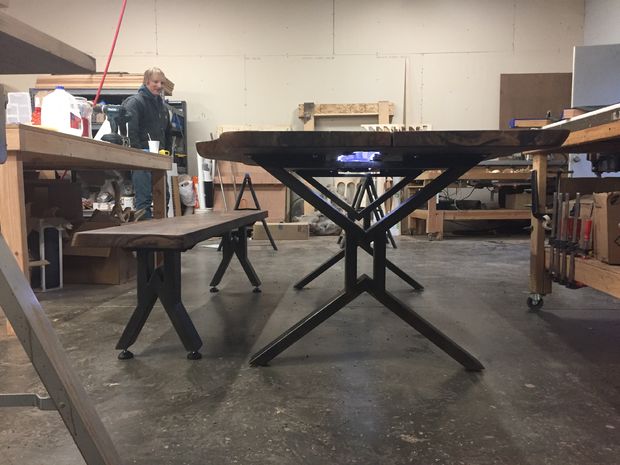
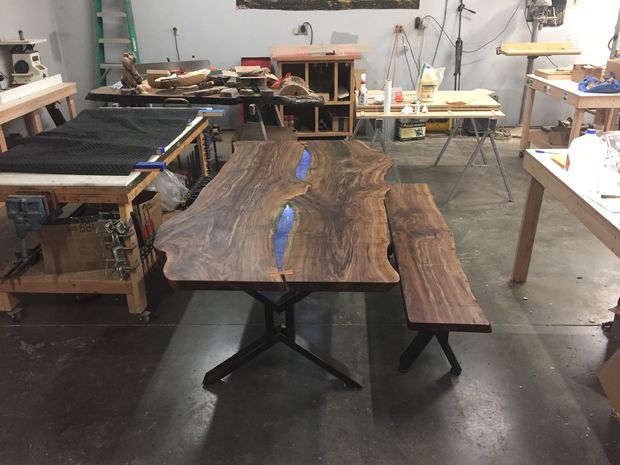
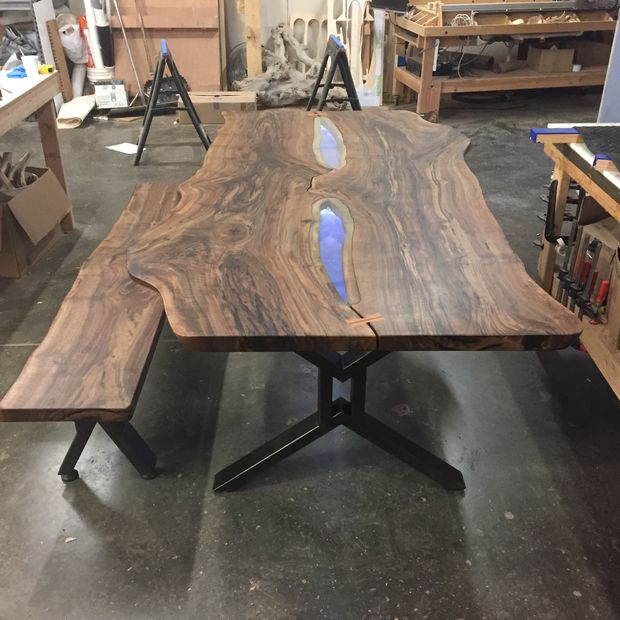
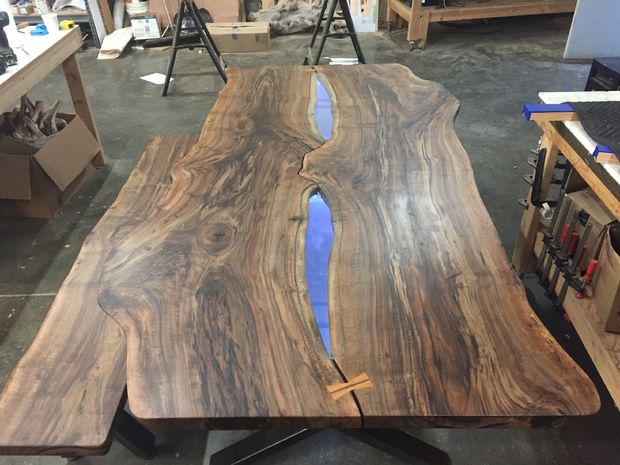
Ножки делались из прямоугольной стальной трубы размером 3,8 х 7,6 см и 3,8 х 3,8 см железного уголка. Чтобы облегчить процесс, я вырезал лазерным резаком шаблоны для фиксации необходимых компонентов и заготовки, которые помогут все сложить под правильным углом. Давным-давно я был прекрасным сварщиком, но шли годы и без достаточной практики у меня все еще остались функциональные навыки, но варить декоративными швами я разучился. Чтобы сгладить этот недостаток, я воспользовался угловой шлифовальной машиной, чтобы сточить излишки металла и придать поверхности более аккуратный вид.
По завершению сварочных работ, я обработал все металлические поверхности угловой шлифмашиной с лепестковым диском, чтобы у них была однородная фактура и блеск. В угловом металле я вырезал продолговатые отверстия для крепления столешницы, чтобы в случае сжатия или расширения древесины не возникло никаких проблем. Нижние части ножек я заварил железными пластинами, чтобы потом просверлить в них отверстия и установить механизм регулировки высоты.
Заказчица пожелала, чтобы ножки были черными. Мы немного поразмыслили над вопросом, как лучше это будет сделать. Вместо краски мы решили использовать средство для воронения стали, так результат будет более стойким и лучше скроет недостатки. Я использовал продукт с названием presto black. Нанесение производилось через распылитель, пока все поверхности не были покрыты веществом, а затем нейтрализовали его действие с помощью раствора пищевой соды, чтобы метал не начал окисляться (ржаветь). После удаления средства для воронения, я высушил метал при помощи компрессора, и покрыл поверхность матовым полиуретаном, чтобы он не ржавел по дороге.
Для присоединения ножек я использовал мебельные гайки и болты, что позволит снимать и устанавливать ножки снова и снова. В скамейке ножки я закрепил крупными шурупами по дереву, так как она не больших размеров и ее можно перемещать не снимая ножек.
Доставка и установка
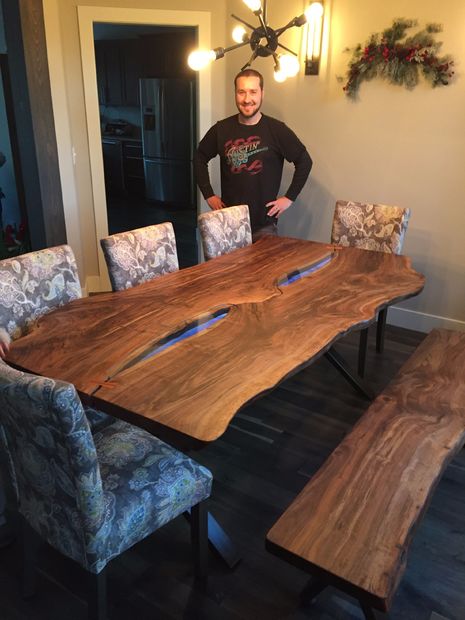
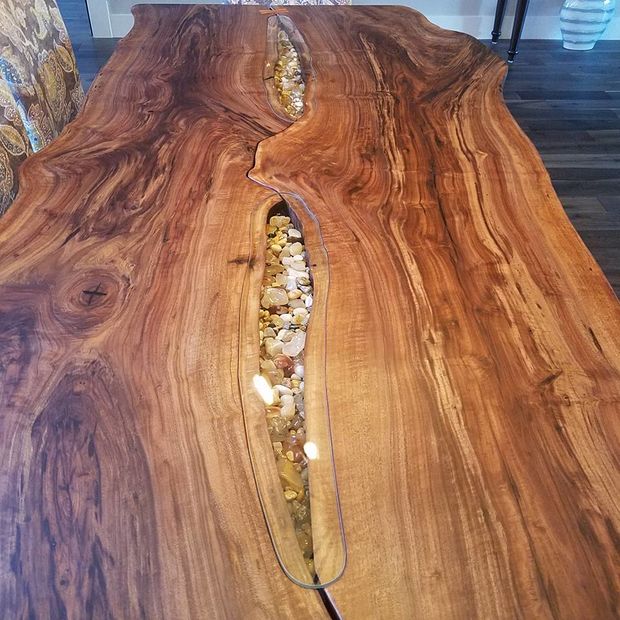
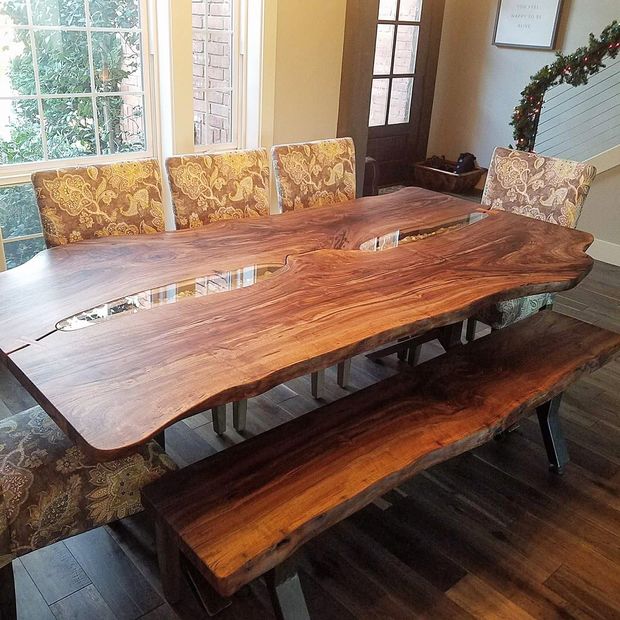

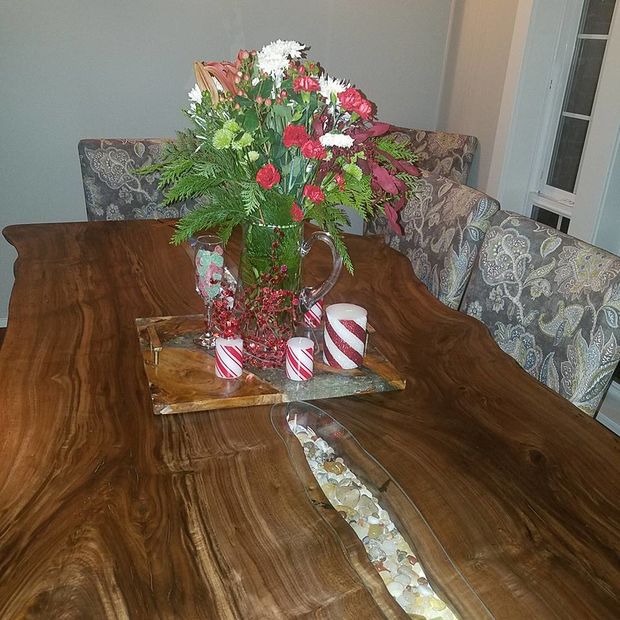
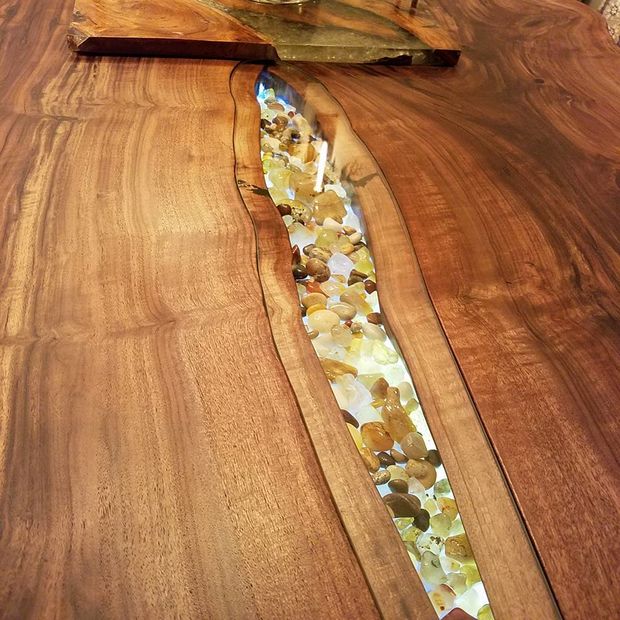
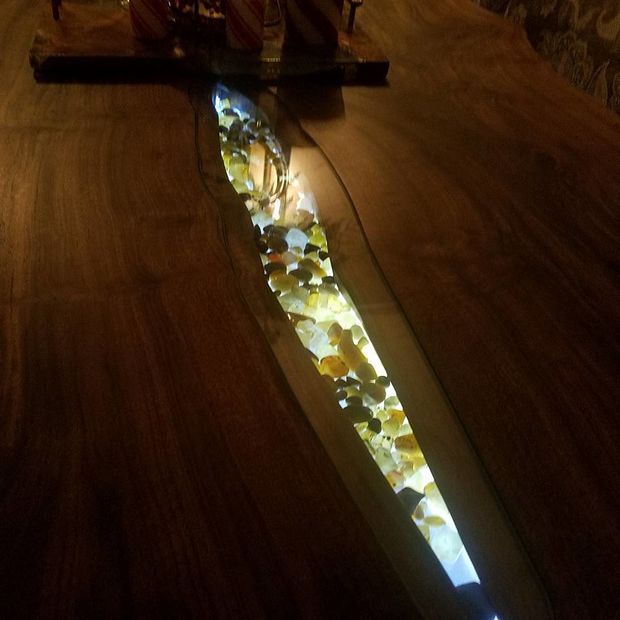
Заказчица живет в трех часах езды от меня, поэтому при перевозке стола было важно его правильно упаковать. Я отсоединил ножки от скамьи и стола, каждый компонент отдельно обернул и заклеил в пластиковый упаковочный материал. Важно оборачивать и упаковывать детали в порядке разборки, потому что потом, когда вы будете их обратно собирать, они будут находиться нужным образом. Так будет проще. Например, когда я доехал до дома, где жила клиентка, первым, что мне довелось сгрузить с фургона, была столешница. Я разместил ее в доме вверх ногами на полу. Следующими доступными деталями были ножки, которые я прикрепил к столешнице. Затем скамейка, ножки скамейки и так далее. Это может казаться здравым смыслом, но увлекшись упаковыванием можно легко обо всем забыть. Этот процесс я не снимал, но уверен, что его довольно просто представить.
Спасибо за внимание!
Original article in English
Новый дачный стол из старых досок
Лето – время дачного отдыха. А какой отдых без застолья? Можно конечно обзавестись приобретенным в супермаркете пластиковым столиком, легким, ажурным. Однако у такого стола, как у любой вещи, тоже есть недостатки. Например, он может колыхнуться от порыва ветра в самый неподходящий момент. Но все поправимо, если на даче имеется старый пиломатериал. Сделанный своими руками стол выглядит эффективнее и надежнее, служит дольше, он не лопнет от перепада температур и не треснет под высоким давлением груза. Стоимость такого столика – полчаса времени!Материалы для работы:
• Старый брус размером 10 х 15 – 4 высоты ножек стола;
• Доска толщиной 40 мм – 2 ширины + 2 длины столешницы;
• Обрезная доска – 1 шт. длиной 5 метров;
• Гвозди длиной 120 мм – 16 штук;
• Гвозди длиной 40 мм – 20 штук;
• Пила, молоток, кисточка, краски.
Этапы выполнения работы:
Первый этап: формируем основу.
Берем старый подоконник, брусок, пару толстых досок. Для придания устойчивости будущему столику в настоящем мастер-классе использованы брусок и старый подоконник. Подоконник удобен уже выпиленными выемками. Но его легко можно заменить брусом и использовать только его.
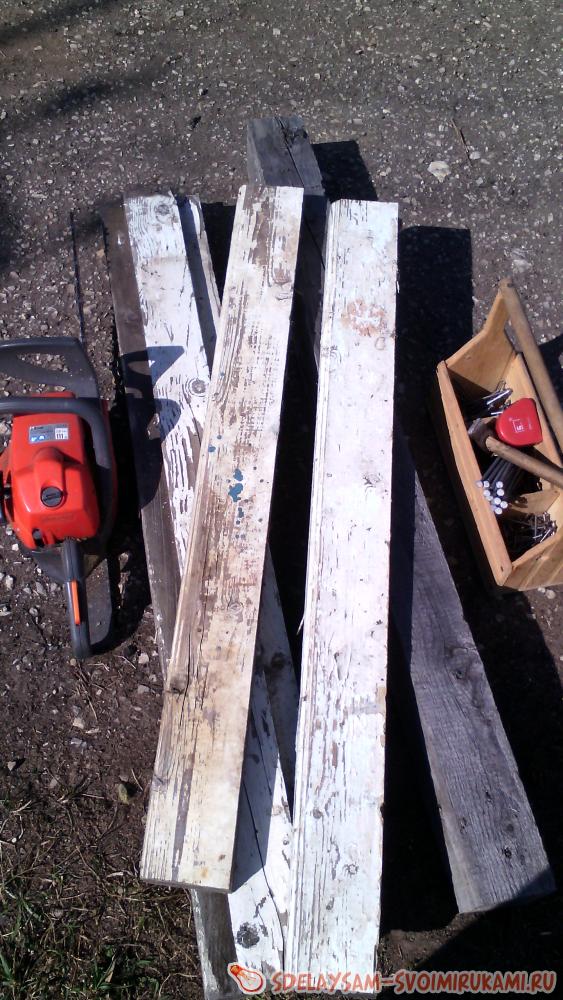
На подоконнике отмеряем 65 сантиметров.
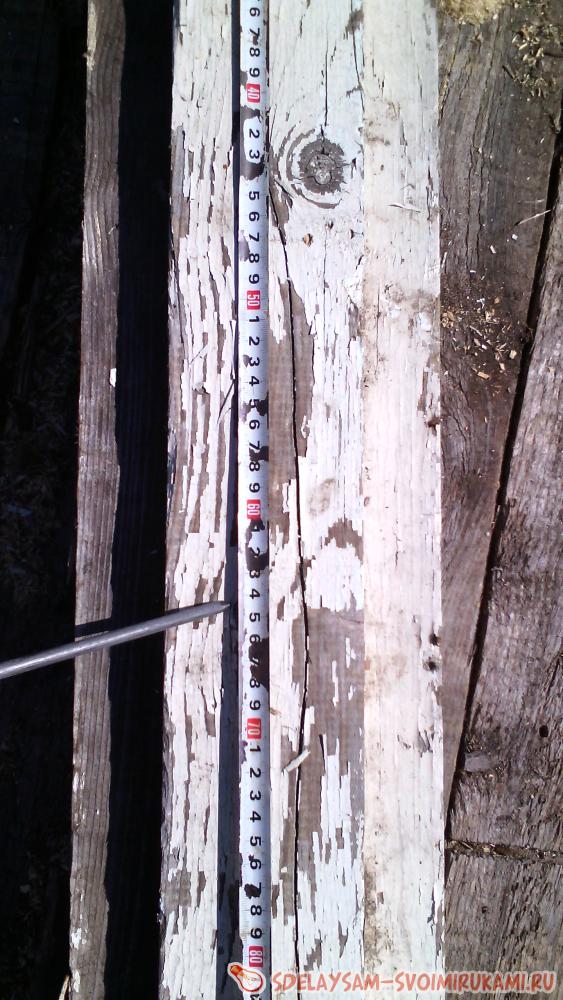
Отпиливаем две части, каждая из которых длиной 65 сантиметров.
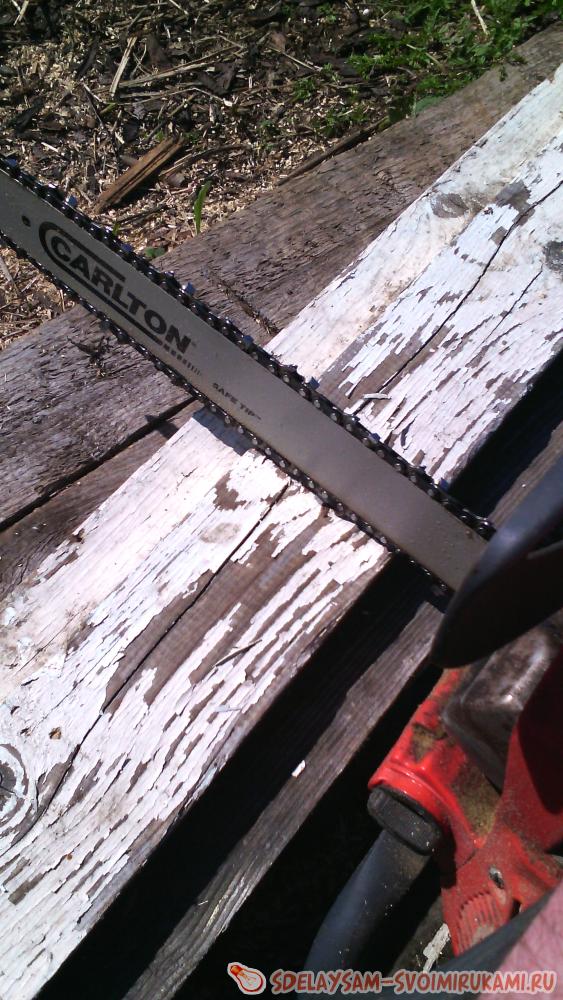
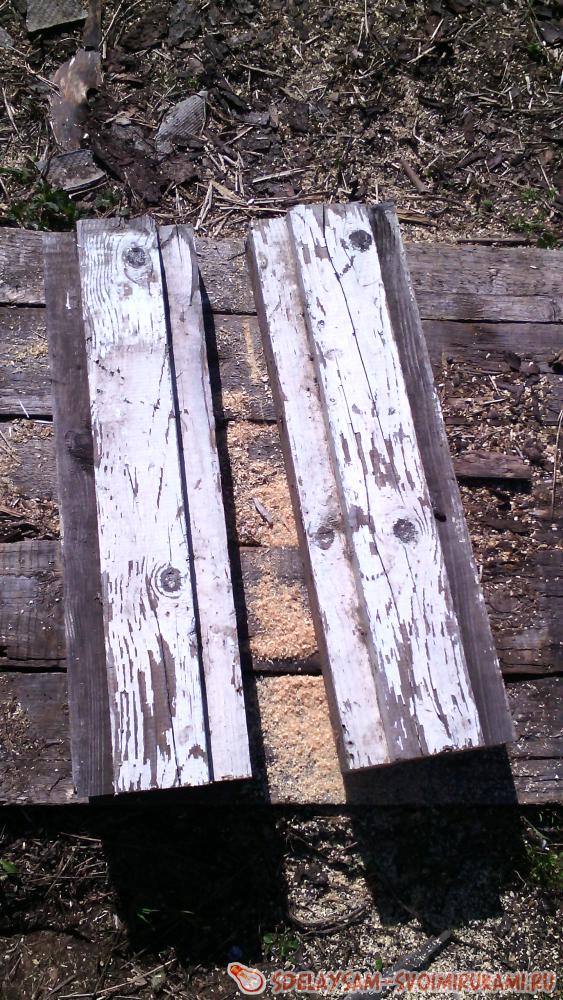
Ножки будущего стола сделаны из бруса, на котором отмеряем 60 сантиметров.
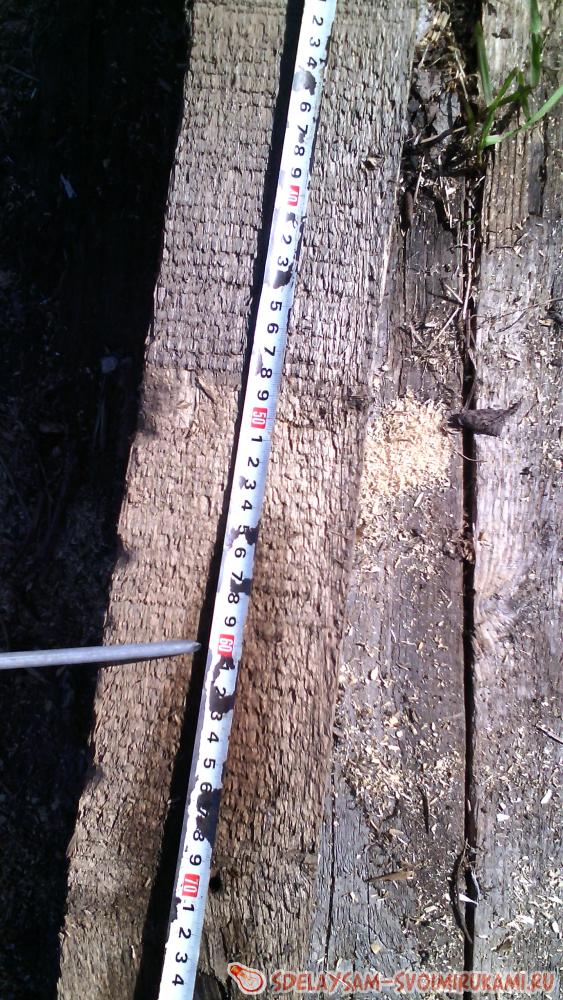
Отпиливаем две части одинаковой длины.
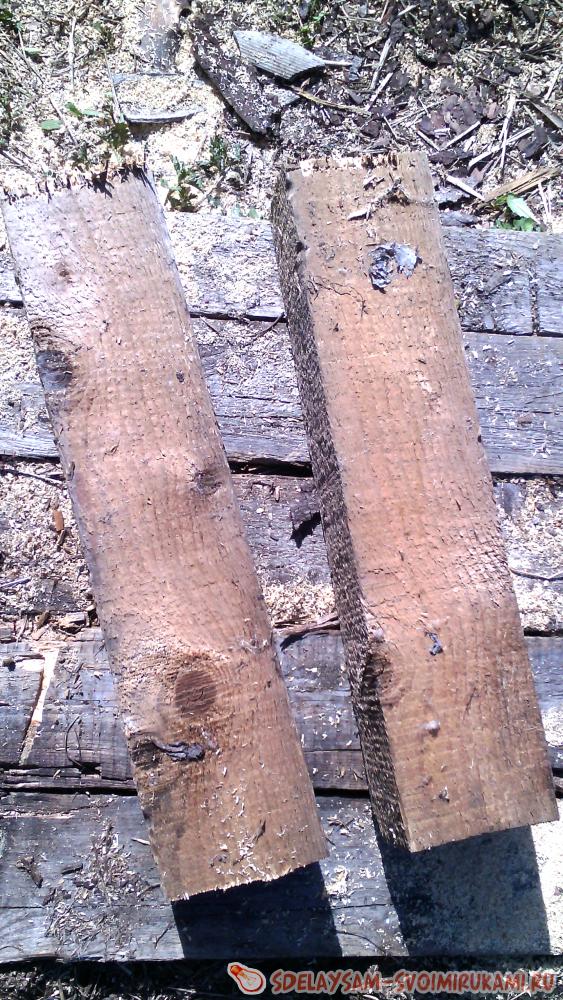
Устанавливаем куски подоконника — основы на небольшом расстоянии друг от друга. Сделав небольшой отступ от края основы, на впадины подоконника устанавливаем ножку – брус.
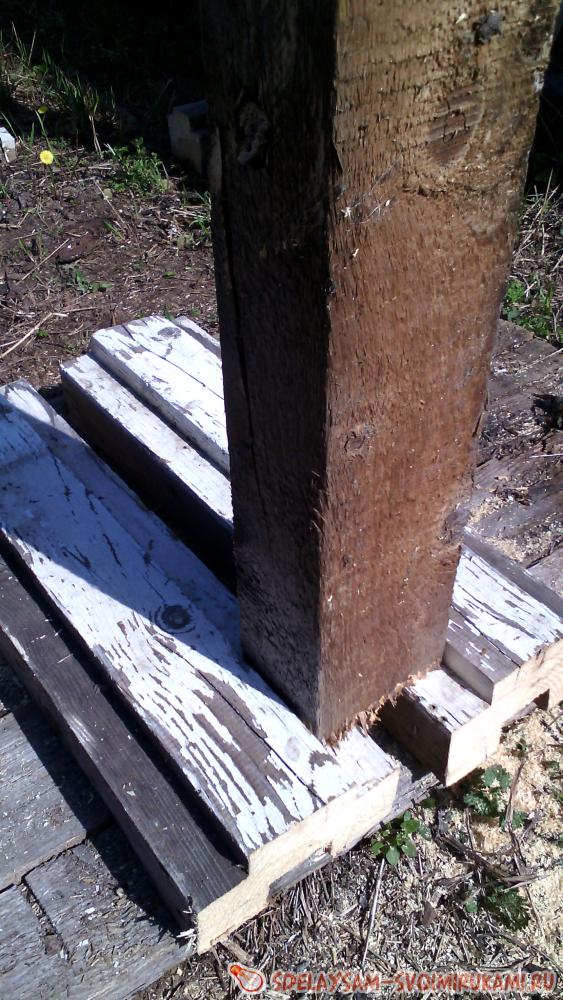
В ножку – брус вбиваем по гвоздю (длиной 120 мм) с каждой стороны, соединяя стыки ножки с частями подоконника. Гвозди вбиваем под наклоном (наискосок).
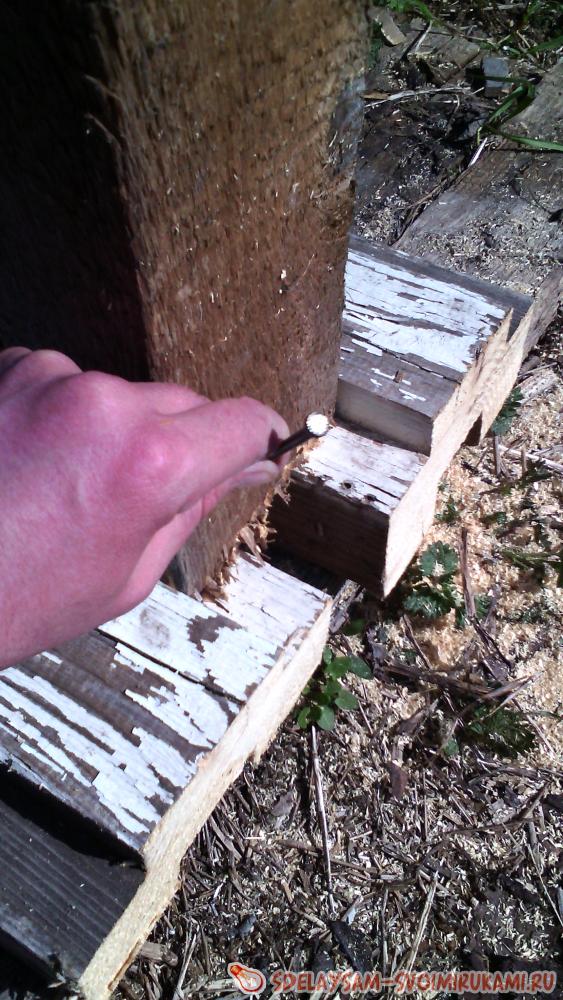
С противоположной стороны устанавливаем вторую ножку – брус, аналогично соединяя ее стыки с частями подоконника гвоздями.
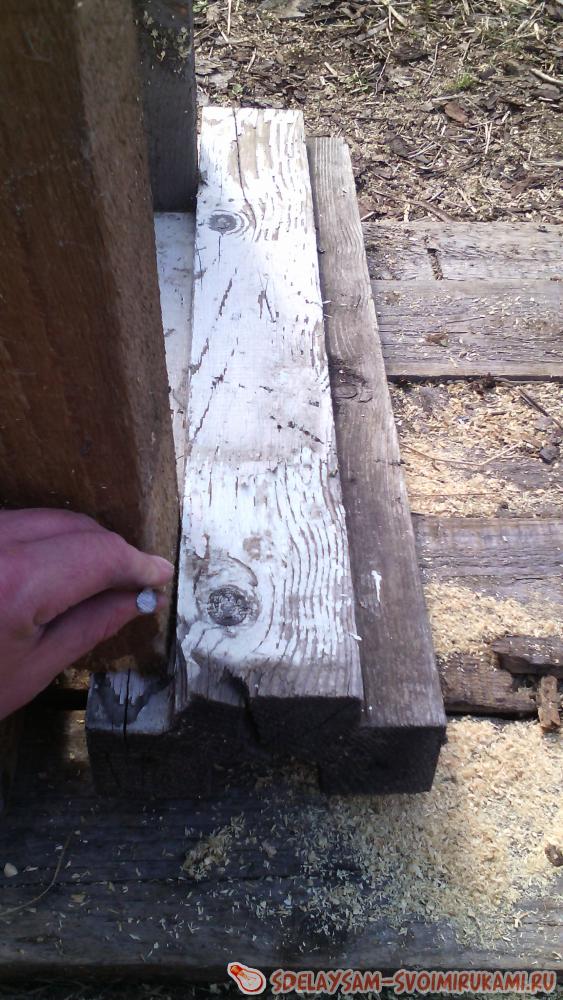
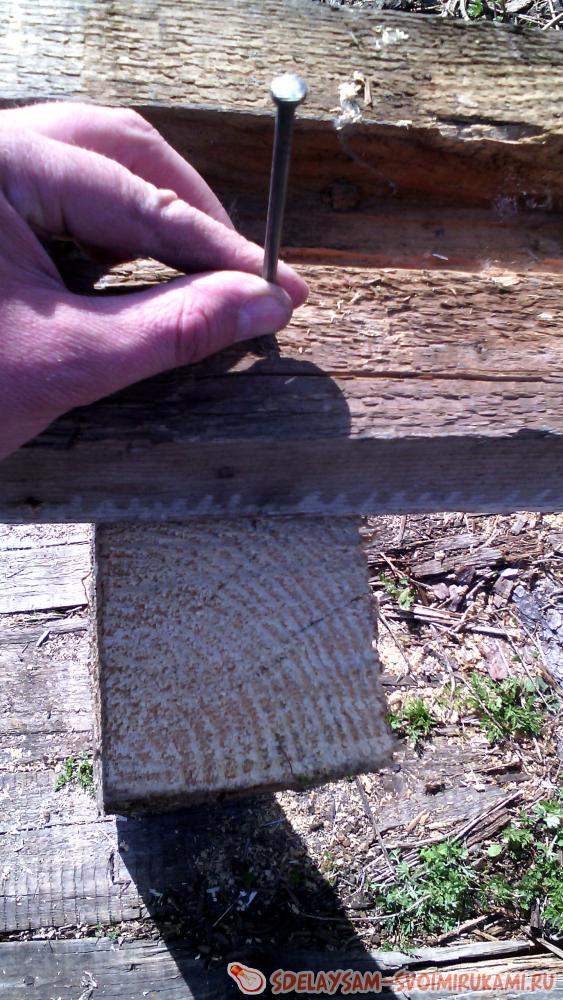
Для укрепления соединения частей столика, переворачиваем получившуюся конструкцию и забиваем гвозди по прямой, закрепляя стык ножки – бруса и основы – подоконника.
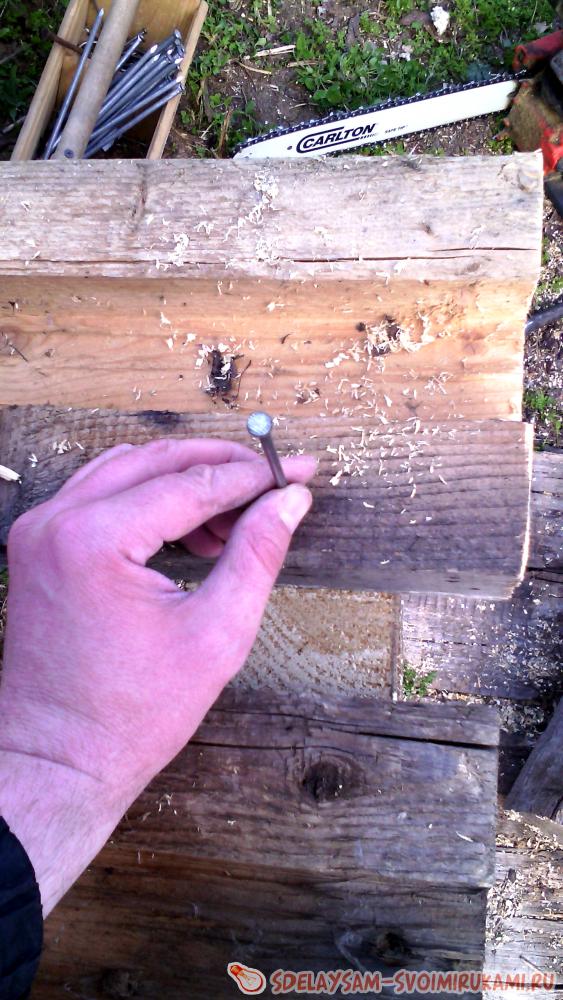
Основа стола готова.
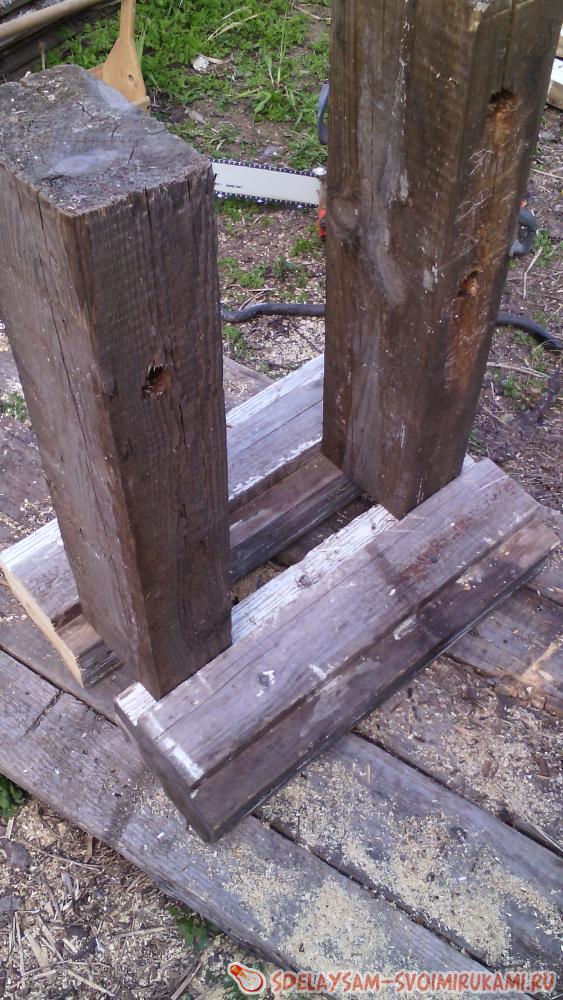
Второй этап: делаем столешницу.
Отпиливаем две толстые доски (половые), соединяем ими верх ножек – брусков. Прибиваем гвоздями длиной 120 мм, используем 4 штуки.
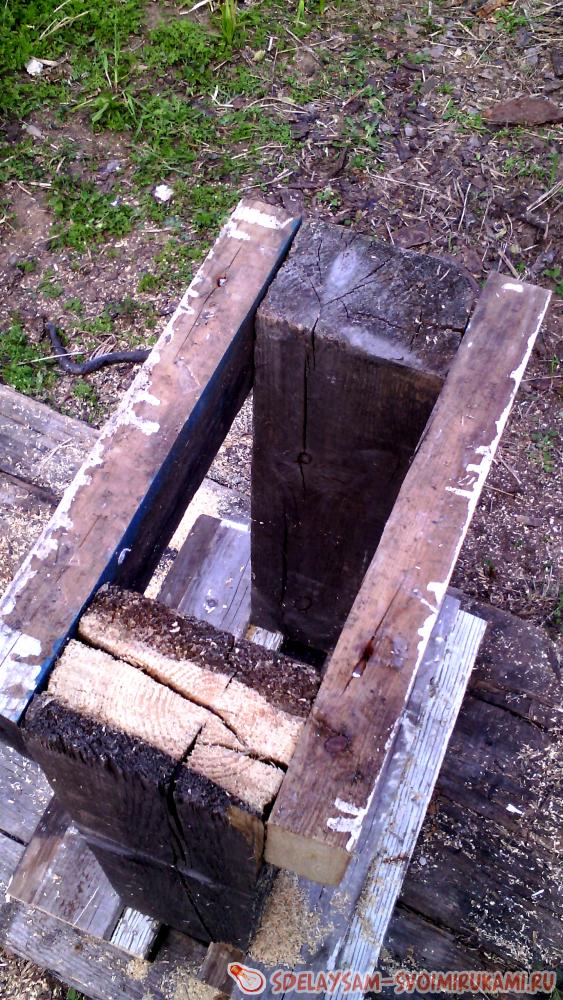
К незакрытым бокам ножек – брусков крепим две толстые доски. Длина досок равна длине столешницы (в данном мастер-классе она составляет один метр). Крепим гвоздями длиной 120 мм, используем 4 штуки.
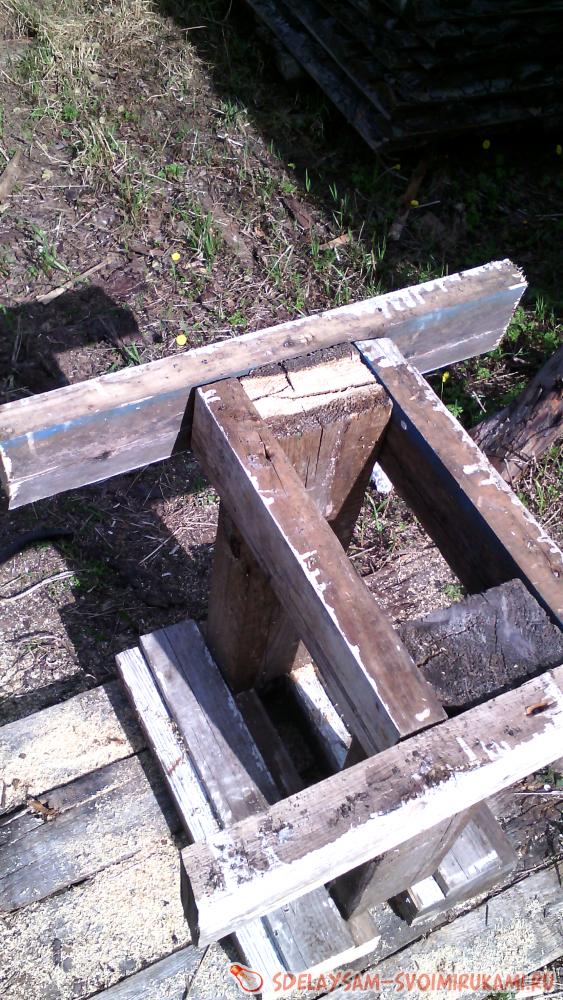
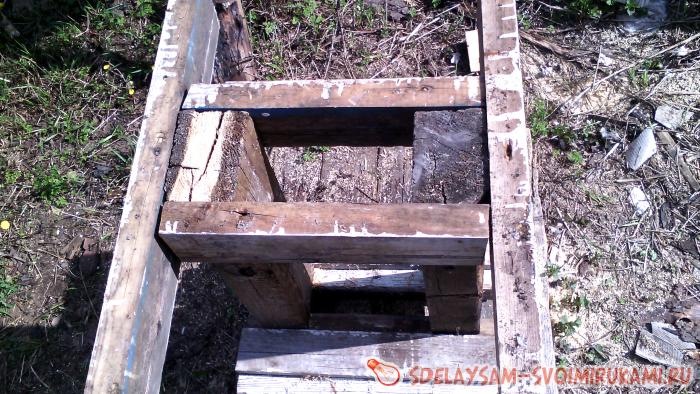
Для лицевой стороны столешницы используем гладкую обрезную доску.
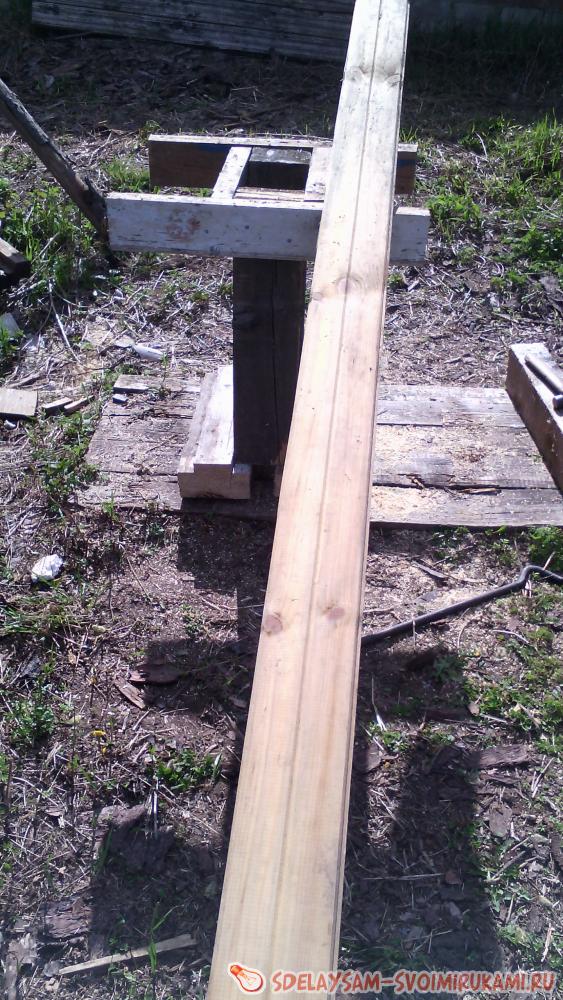
Пилим 5 отрезков длиной 90 сантиметров.
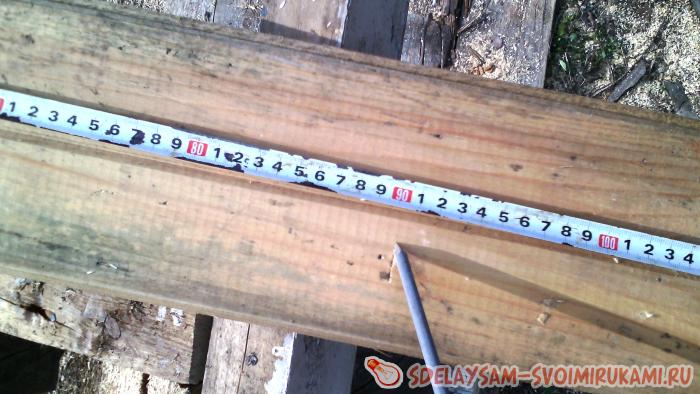
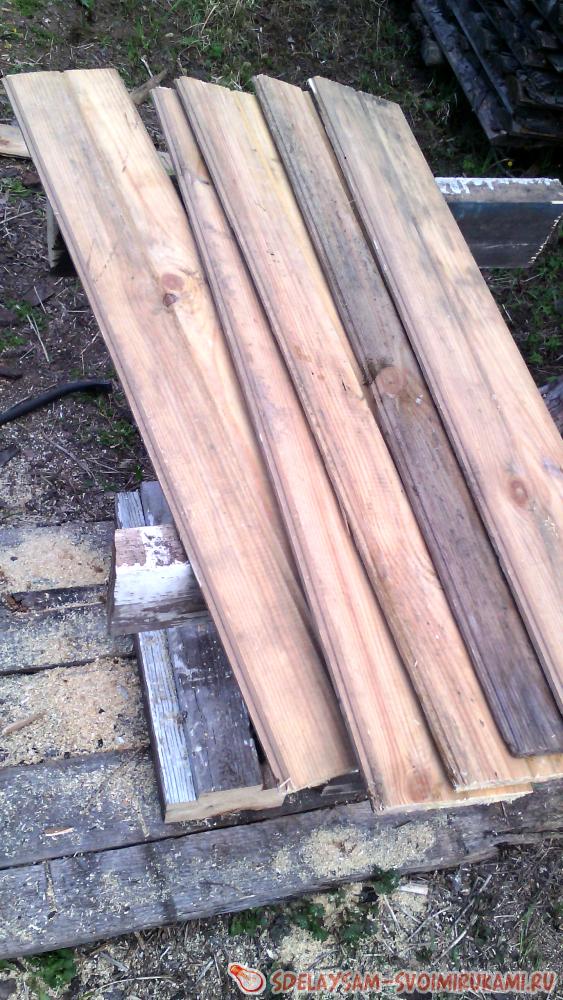
Кладем нарезку обрезной доски поверх прибитых метровых кусков толстой доски (располагая их поперек).
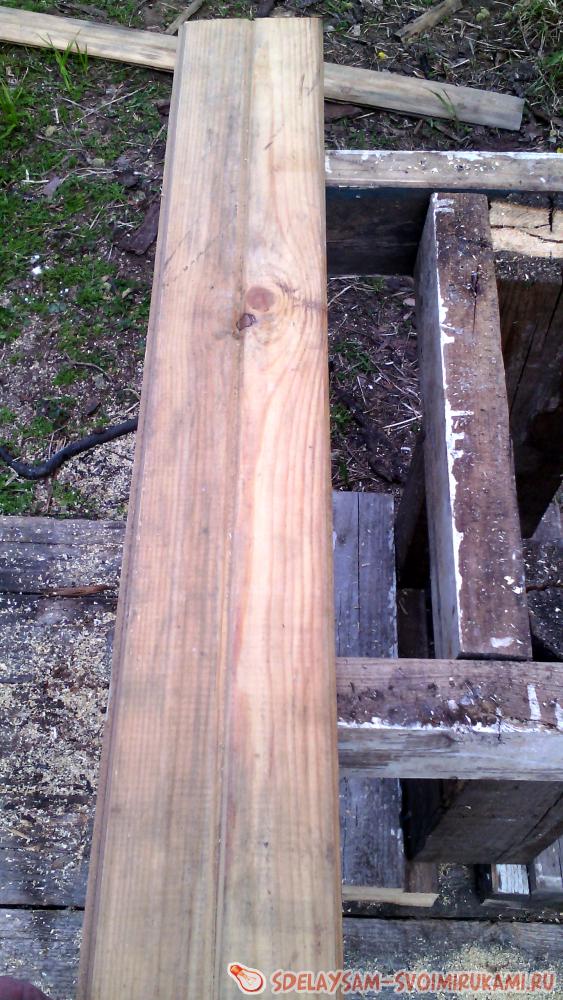
Гвоздями длиной 40 миллиметров прибиваем нарезку обрезной доски к двум метровым кускам толстой доски (забивая гвозди по обе стороны). Используем с каждой стороны столешницы по 10 гвоздей (20 штук всего: по 2 гвоздя в каждую досочку с каждой стороны).
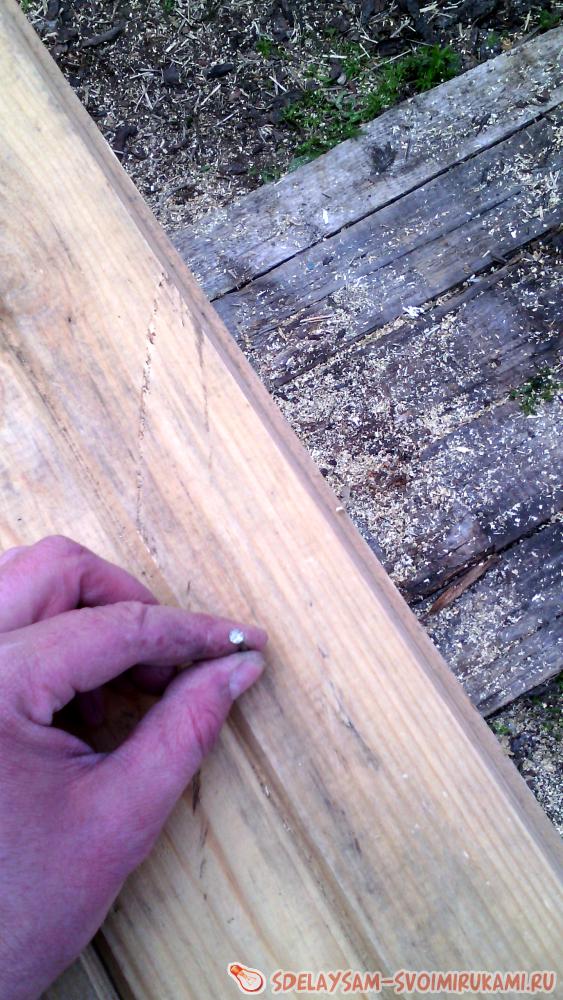
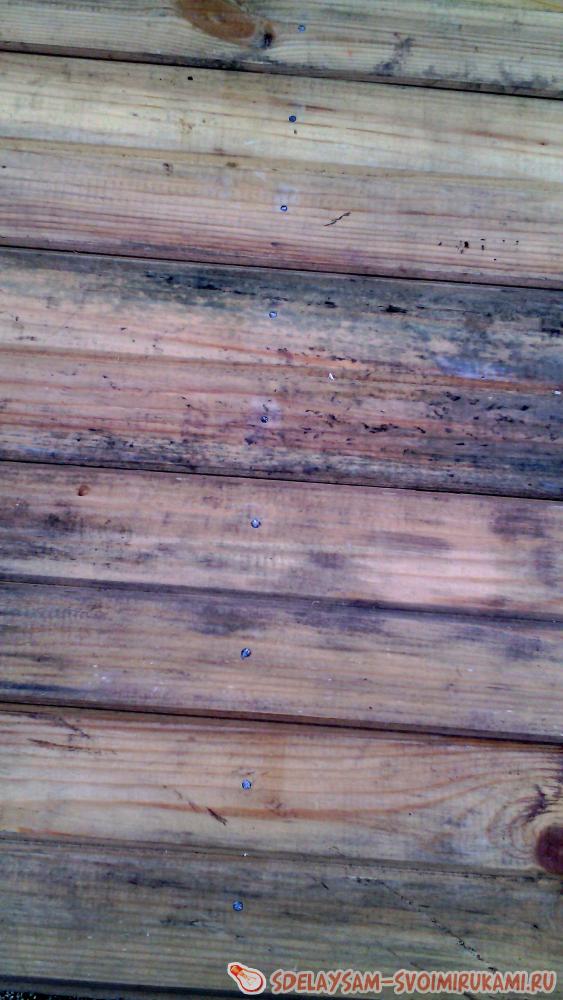
Под столешницей спиливаем торчащий угол толстых поперечных досок (к которым крепится лицевая часть столешницы).
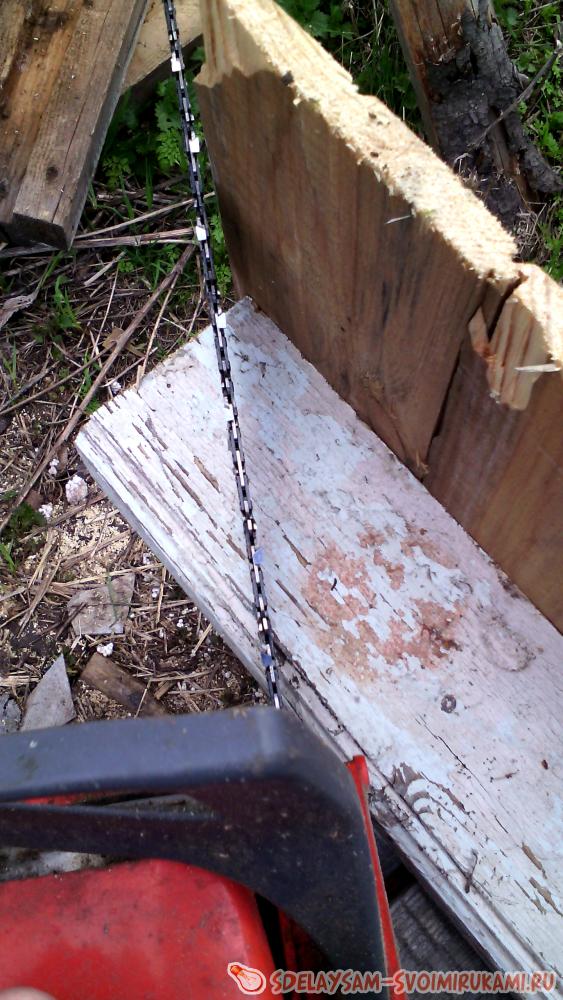
Вот такой симпатичный столик получается.
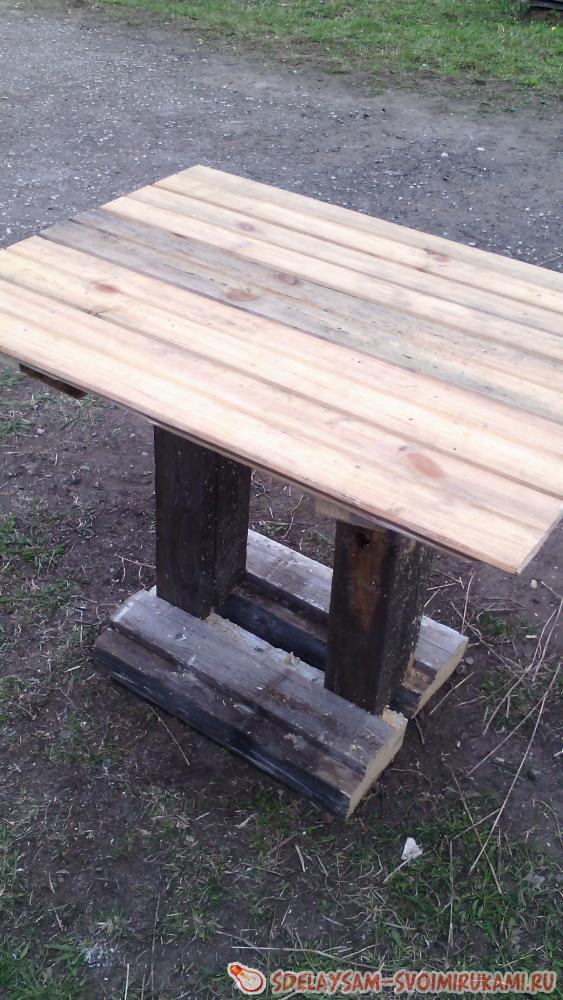
Этап третий: работаем над дизайном.
Чтоб столик радовал нас даже в дождливую погоду, красим его красками разных цветов.
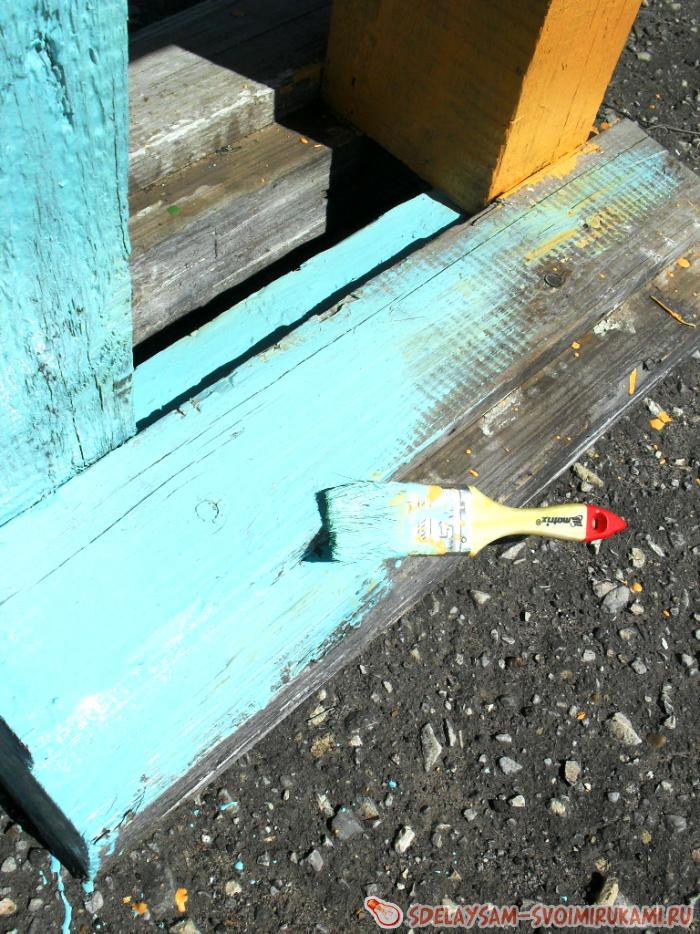
Вот и готов замечательный стол. Его не сдует порыв сильного ветра, он не завалится на бок, если пятилитровую кастрюлю с шашлыком поставить на самый край, а ножки не треснут под весом пляшущих на нем гостей. Приятного застолья!
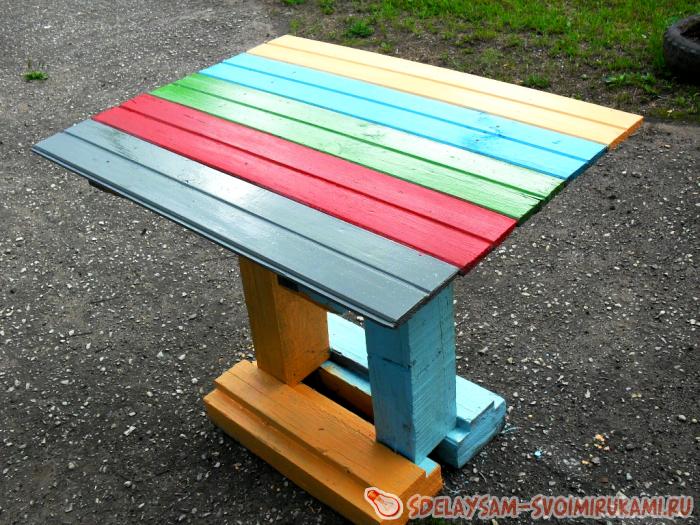
Стол со стильной столешницей из эпоксидки и доски

Интересную столешницу сделал мастер-самодельщик. Правильно подобрав цветовое решение, мастер сделал стильный стол, которая отлично впишется в любую обстановку.
Для изготовления стола мастеру понадобились следующие
Инструменты и материалы:
-Доски;
-Эпоксидная смола;
-Желтый пигмент;
-Рейка;
-Емкость;
-Скотч;
-Шлифмашинка;
-Горелка;
-Ножки для стола;
-Кисть малярная;
-Весы;
-Средства защиты;
-Крепеж;
-Отвертка;
-Краситель на водной основе;
-Дрель;
-Линейка;
-Крестики для плитки 8 мм;
-Акриловый лист;
-Двусторонний скотч.


Шаг первый: подготовка материала
Доску мастер приобрел в магазине строительных товаров. Важно, чтобы доска была ровной и сухой. Место работы должно быть сухим без пыли с температурой воздуха не менее 20 градусов. Эпоксидная смола тоже должна иметь температуру не ниже 20 градусов. Для того, чтобы добиться нужного эффекта столешница будет заливаться в четыре подхода.


Шаг второй: доски
Укладывает доски на рабочий стол в произвольном порядке. Зазор между досками делает 8 мм. Зазор между досками и рамкой 12 мм. Для контраста некоторые доски покрывает красителем на водной основе, другие слегка обжигает горелкой. Измеряет размер будущей столешницы по выложенным доскам. На каждую доску наклеивает стикер и убирает со стола.
Шаг третий: подготовка места заливки
На ровный рабочий стол наклеивает двусторонний скотч. На скотч приклеивает лист акрила. Вокруг акрила делает бортик из планки. Выбор акрила обусловлен его плохой адгезией, и к нему не будет прилипать эпоксидная смола. Акрил можно будет использовать несколько раз.
Шаг четвертый: подготовка эпоксидной смолы
Для своей столешницы мастер использует фирменную смолу GlassCast® 3. Смешивать ее нужно 2 части смолы с 1 частью отвердителя. Но сначала мастер делает расчет необходимого количества. При площади стола 1,28 кв.м. потребуется около 13 кг смолы. Далее мастер на электронных весах взвешивает нужное количество смолы и добавляет туда колер. Путем эксперимента мастер высчитал, что на один килограмм смолы требуется 3, 5 грамма пигмента. В таком случае цвет получается насыщенный и не теряет прозрачность. Полностью на 13 кг получается 45 грамм красителя. Мастер добавляет краситель в смолу (смола еще не смешана с отвердителем) и тщательно перемешивает.
Шаг пятый: первый слой
Первый слой составляет 3 мм. Высчитывает нужное количество смолы и отвердителя. В данном случае это будет 2, 56 смолы + 1, 28 отвердителя = 3,84 готового раствора. Замешивает смолу мастер в течении 3 минут, затем переливает в другую емкость и замешивает еще 3 минуты. После замешивания выливает смолу и разравнивает. При необходимости прогревает горелкой (это поможет удалить пузырьки воздуха).
Примерно через 12 часов смола приобретет стадию «В», при которой нажимая на смолу она слегка вдавливается, но к перчатке не прилипает. Именно в этот момент нужно заливать второй слой.
Шаг шестой: второй слой
Второй слой 1,5 мм. Замешивает нужное количество смолы. Выливает часть её на предыдущий слой. Намазывает нижнюю часть досок смолой и укладывает на стол. Нужно укладывать так, чтобы под досками не было воздушных карманов. Смазывает доски смолой со всех оставшихся сторон. С помощью крестиков выравнивает зазоры 8 и 12 мм. Оставляет на несколько часов. Затем удаляет крестики, и оставляет до застывания смолы до стадии «В».
Шаг седьмой: слой третий
На эту заливку уйдет больше всего смолы. Нужно будет залить смолой пространство между досками и немного над досками. Все, как и в предыдущих шагах: расчет, смешивание, заливка. После заливки обязательно горелкой выгоняет пузырьки воздуха. Ну и оставляет до стадии «В».
Шаг восьмой: четвертый слой
Четвертый слой последний и составляет 3 мм. При заливке особо тщательно нужно проливать углы и прилегающие поверхности. После заливки столешница должна высыхать не менее суток, а в идеале несколько. На время высыхания мастер закрывает ее крышкой. На полностью застывшей смоле при нажатии на поверхность гвоздем след не остается.


Шаг девятый: шлифовка
Удаляет бортик. Переворачивает столешницу и снимает акриловый лист. Затем шлифует торцевые части столешницы. Для шлифовки использует наждачную бумагу от 240 до 1200 с водой. После шлифовки полирует торцевые части.
Шаг десятый: установка ножек
Размечает места установок ножек. Сверлит крепежные отверстия. Прикручивает ножки стола.
Все готово.


Не грех и обмыть удачное завершение работы.

По ссылке «источник» внизу страницы доступно видео со всеми шагами изготовления стола.
Источник
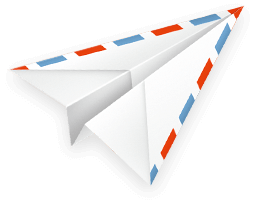
Получайте на почту подборку новых самоделок. Никакого спама, только полезные идеи!
*Заполняя форму вы соглашаетесь на обработку персональных данных
Становитесь автором сайта, публикуйте собственные статьи, описания самоделок с оплатой за текст. Подробнее здесь.Мебель своими руками из досок
В наши дни производителями предлагается настолько широкий ассортимент мебели и предметов интерьера, что особых проблем с выбором подходящего варианта даже у самых взыскательных потребителей нет. К тому же существует возможность разместить заказ на сборку по собственным эскизам. Однако собственноручное изготовление конструкций, несмотря на всю трудоемкость процесса, позволяет получить в итоге эксклюзивные изделия, зачастую выглядящие, как настоящие шедевры искусства.

Мебель своими руками из досок
Изготовление мебели своими руками — полезное хобби
Желая освежить убранство жилища, добавить в интерьер новые, интересные акценты или просто изготовить необходимый в хозяйстве предмет, многие задумываются о самостоятельном изготовлении мебели. Удобные и привлекательные конструкции можно произвести из различных материалов: металла, стекла, пластика, дерева и их комбинаций. Чаще всего выбор осуществляется исходя из стилистики интерьера и собственных предпочтений.

Материалы для кухонной мебели

Основные виды материалов для мебели
Однако и раньше, и в настоящее время самым популярным материалом для изготовления предметов мебели является древесина. Это легко объяснить.
- Материал относится к наиболее доступным.
- Брус и доска отлично поддаются любым видам обработки, из них можно произвести любые конструкции: начиная от стульев и стеллажей и заканчивая кроватями и стенками.
Самодельный стеллаж на четыре полки
- Дерево отличается прочностью и стойкостью к механическим воздействиям.
- Сегодня многих заботит проблема экологии. Применение новых, технологичных материалов часто вызывает вопросы относительно их воздействия на окружающую среду. Древесина — натуральна и экологична, она не выделяет вредные для здоровья человека и природы вещества и не вызывает аллергии.
Кровати из бруса
- Тактильные свойства материалов также важны при контакте с предметами. Изделия из дерева очень приятны на ощупь.
- Древесина оказывает положительное воздействие на психоэмоциональное состояние человека.
Журнальный стол из старых досок
- Деревянная мебель отлично сочетается практически со всеми стилями оформления помещений.
- Дерево привлекательно на вид. Разнообразие текстур различных пород позволяет подобрать интересные с точки зрения дизайна варианты.
Образцы пород древесины
Основным недостатком деревянных изделий является подверженность деформациям и разрушению вследствие воздействия внешней среды. Но с этой проблемой позволяют справиться представленные в широком ассортименте средства, содержащие антисептики, для обработки древесины.

Мебель из паллет на даче
Мебель может быть изготовлена из различных материалов: массива, щита, МДФ, фанеры, ДСП, ДВП. Самый доступный и популярный — цельные обрезные или клееные доски. Их можно приобрести специально или использовать подручные средства — материал, оставшийся от демонтажа конструкций, паллеты и т. д. При подготовке необходимых для создания конструкции материалов в первую очередь необходимо учитывать их влажность. Доски должны быть высушенными. Показатель влажности древесины, из которой собирается мебель, не может превышать 8%.

Область применения клееного мебельного щита
Для сборки предметов интерьера можно использовать различные виды дерева, различающиеся текстурой, оттенком и характеристиками. Все они подразделяются на 3 класса.
- Мягкие – большая часть хвойных пород, липа, ольха.
- Твердые – лиственница, ясень, дуб, бук.
- Очень твердые – тис, самшит, акация. Эти виды древесины редко используются при самостоятельном изготовлении предметов интерьера.

Породы древесины
При выборе материала необходимо учитывать, что мягкое дерево легче обрабатывать, но оно отличается меньшей стойкостью к износу. А мебель, например, из дуба будет долго служить. Однако он и значительно дороже.

С мягким деревом проще работать
Что нужно, чтобы своими руками изготовить мебель?
- Желание.
- Свободное время.
- Уверенность в своих возможностях, минимальные навыки работы с древесиной.
- Чертеж изделия, набор необходимого инструмента, материал и фурнитура.
- Наличие места для проведения работ. В идеале это должна быть мастерская, которую можно оборудовать на даче или, например, в гараже.

Потребуется специально обустроенное рабочее место
Изготовление мебели может длиться не один месяц, но результат обязательно оправдает ожидания. Своими руками можно изготовить мебель для квартиры, дачного дома, беседки, сада и т. д.

Изделия для бани могут быть достаточно простые
Цены на доски строительные
Доски строительные
Вешалка в прихожую
Одно из самых простых изделий, которые можно сделать самостоятельно, даже начинающему мастеру — вешалка для одежды.
Шаг 1. Готовится чертеж конструкции. Этот этап — чрезвычайно важен для расчета необходимых материалов и правильного изготовления сооружения.

Чертеж вешалки
Шаг 2. Подготавливаются комплектующие: доски (4 основных и 2 перекладины), крючки для одежды и сумок (четыре больших и 2 маленьких), саморезы для крепления конструкции и крючков. Доски могут быть цельными или склеенными из ламелей.

Доски и крючки для одежды
Шаг 3. Понадобятся инструменты: пила, лобзик, паяльная лампа, шлифовальная машинка (можно обойтись наждачной бумагой), шуруповерт. Помимо этого, нужно подготовить клей ПВА, лак и кисть для его нанесения (или распылитель).

Края нужно закруглить лобзиком
Цены на популярные модели электролобзиков
Электролобзик
Шаг 4. Планки отпиливаются по размеру. Для большей эстетичности рекомендуется закруглить края лобзиком.
Шаг 5. Древесина дочерна обжигается при помощи паяльной лампы. Такая технология позволяет значительно повысить долговечность дерева и стойкость к неблагоприятным воздействиям (климата, огня, насекомых). Помимо улучшения функциональных характеристик древесины, обжиг помогает сделать ее более выразительной, так как более четко проявляется структура дерева.

Обжиг древесины паяльной лампой
Важно! Обжиг можно начинать, когда огонь приобретет лиловый оттенок (обжиг желтым пламенем приведет к образованию сажи). При воздействии огонь должен быть направлен перпендикулярно к планке. При работе с открытым пламенем необходимо следить за пожарной безопасностью.

Бензиновая паяльная лампа
Цены на различные виды газовых горелок и паяльных ламп
Газовые горелки и паяльные лампы
Бока планок можно не обжигать, в таком случае конструкция будет более привлекательной.
Шаг 6. Обожженные доски обрабатываются наждачной бумагой или шлифуются.

Шлифовка обожженных досок
Шаг 7. Все элементы конструкции готовы к сборке.

Все элементы готовы к сборке
Шаг 8. Доски фиксируются саморезами. Места стыка для большей прочности обрабатываются клеем.

Доски собраны в единую конструкцию
Шаг 9. Наносится лак. Для этого используют распылитель или обычную кисть. Рекомендуется наносить несколько слоев с обязательным высыханием каждого предыдущего.

Нанесение лака
Шаг 10. Готовая вешалка крепится к стене. Фиксируются крючки для одежды.

Готовая вешалка на стене
Шаг 11. В нижней части двух планок закрепляются небольшие крючки, на которые можно вешать ключи или сумки.

Внизу небольшие крючки для ключей и сумок
Представленный вариант вешалки — один из наиболее простых. Можно дополнить конструкцию полкой для шапок.
Результат потраченных усилий — налицо. Получился удобный предмет интерьера, отлично подходящий по стилю и цвету к дизайну прихожей.

Простая вешалка в прихожую
Кровать из досок
Этот предмет мебели также совсем несложно изготовить самостоятельно. Предлагается вариант сборки двуспальной кровати размером 200 х 160 см.
Таблица. Что для работы потребуется.
Материалы, инструмент, крепеж | Фото |
---|---|
Доски и мебельный щит различного размера: · доски для ножек: 38 х 10 х 5 см — 4 шт.; · клееный щит для боковин: 200 х 20 х 1,8 см — 2 шт., 160 х 20 х 1,8 — 1 шт., 160 х 40 х 1,8 — 1 шт.; · рейки для упора обрешетки: 7 х 3 см — по две штуки длиной 200 и 160 см; · перемычки: 200 х 7 х 3 см — 2 шт.; · планки для обрешетки: 160 х 10 х 2,5 см — 16 шт. | ![]() Доски и мебельный щит |
Саморезы разного размера | ![]() Саморезы |
Болты 6 х 80 мм (с шайбой и гайкой) — 30 шт. | ![]() Болты |
Металлические уголки: 40 х 40 х 80 мм — 4 шт., 30 х 30 х 30 мм — 4 шт., 70 х 70 мм — 8 шт. | ![]() Металлический уголок |
Алкидно-уретановый лак, жидкие гвозди | ![]() Яхтный лак |
Лобзик, шуруповерт, шлифовальная машинка | ![]() Необходимые инструменты |
Цены на угловые шлифмашинки (болгарки)
Угловые шлифмашинки (болгарки)
Пошаговая инструкция по производству
Шаг 1. В соответствии с размерами нарезаются комплектующие:

Ножки для будущей кровати

Боковины
- рейки для упора обрешетки, перемычки, планки для обрешетки.
Все детали должны быть обработаны защитной пропиткой.
Шаг 2. При помощи болтов ножки соединяются с боковинами.

Ножки соединяются с боковинами
Шаг 3. К ножкам прикручиваются металлические уголки.

Прикрученный металлический уголок
Шаг 4. К боковинам монтируются рейки, на которые будет опираться обрешетка. При этом, помимо метизов, рекомендуется использовать клеевое соединение (можно воспользоваться жидкими гвоздями). Это повысит прочность и минимизирует риск появления в будущем скрипа.

Закреплены рейки для обрешетки
Шаг 5. Собираются все четыре стороны кровати.

Процесс сборки кровати
Шаг 6. К спинкам кровати прикручиваются рейки. В них необходимо сделать пропилы под перемычки.

Видны пропилы под перемычки
Шаг 7. В пропилы укладываются перемычки и фиксируются.

Перемычки зафиксированы
Шаг 8. К перемычкам прикручиваются уголки, предназначенные для установки дополнительных ножек. На каждую планку следует установить по две ноги.

Перемычки оснащены дополнительными ножками
Шаг 9. Монтируется обрешетка. В планках предварительно сверлятся отверстия под саморезы. Размер зазора между элементами обрешетки определяется индивидуально. Если доски не были отшлифованы ранее, их следует обработать после установки.

Смонтирована обрешетка
Шаг 10. Конструкция покрывается лаком. Видов лаков много. Материал обязательно должен быть предназначен для проведения работ внутри помещений. Для этих целей лучше всего подойдут акриловые, эпоксидные, полиуретановые или алкидно-уретановые составы.
Шаг 11. После этого осталось подобрать подходящий матрас и кровать можно использовать по назначению.
Внешне собранная кровать выглядит немного аскетично, но после размещения матраса, белья и красивого покрывала она будет смотреться совсем иначе. Для дачного дома она точно подойдет. Если же использовать некоторые столярные навыки, сделать линии более плавными и обработать поверхность декоративным составом, такой предмет интерьера может вписаться и в дизайн квартиры.

Кровать из дерева

Кровать из старых досок
Табурет из ненужных досок
Часто приходится сталкиваться с ситуацией, когда на даче валяются ненужные доски, которые никому не нужны. Вместо того, чтобы выбросить хлам или сжечь его, можно поступить по-другому.

Старые доски можно использовать с пользой
Из валяющихся старых досок выкраиваются четыре детали: сидение, боковины и перемычка.

Боковина будущего стула
Получившиеся заготовки необходимо обработать — на помощь придет наждачная бумага. Также для повышения эстетичности рекомендуется скруглить кромки.

Все детали обрабатываются наждачной бумагой
Теперь из гладких деталей без неровностей и заусенцев можно собрать стульчик.

Собранный стульчик из старых досок
Конструкцию остается обработать защитной пропиткой. При желании ее можно покрыть декоративным составом. Приложив совсем немного усилий и потратив минимум времени, можно изготовить простой, но надежный стульчик, сидя на котором, можно и шашлыки пожарить, и грядки прополоть.
Помимо предложенных вариантов самостоятельного изготовления мебели, которые довольно просты, можно замахнуться и на более сложные конструкции: комоды, шкафы-купе и даже кухню.

Шкаф своими руками — фото
Довольно часто в наших домах встречаются предметы интерьера, которые потеряли свой внешний вид, но выбросить их жалко. Вооружившись терпением, фантазией и нужными материалами, мебель можно отреставрировать.
Как дать новую жизнь старой столешнице из досок

Старая столешница из досок
Столешница изготовлена из сосновых досок. Большой плюс — они в достаточно хорошем состоянии, не растрескались, лишь потеряли внешнюю привлекательность. В таком состоянии стол, которому более 100 лет, использовать вряд ли кому-то понравится, если только не прикрыть его красивой скатертью. Как можно поступить?
- Следует удалить старое покрытие: можно воспользоваться средством для удаления слоя лака, но проще просто отшлифовать детали.
Шлифовка столешницы
- Столешница фрезеруется.
Деталь после фрезеровки
- На столешницу и ножки наносится специальное паркетное масло повышенной твердости (белого цвета) предназначенное для финишной отделки отшлифованных поверхностей из дерева. Оно используется для нанесения на конструкции внутри помещений. В рецептуру состава входят натуральные масла, обогащенные смолами, воск и пигменты, устойчивые к свету. Наносить средство можно в 1 или 2 слоя.
Паркетное масло нужно нанести двумя слоями
- К столешнице прикручиваются ножки.
Прикручены ножки
После реставрационных работ получился стол, который в состоянии украсить любой интерьер.
Как видно, старому, видавшему виды предмету интерьера, изготовленному из досок, можно дать новую жизнь. Какие же способы применяются при реставрации мебели?
Методы восстановления внешнего вида мебели
Восстановить и вернуть привлекательность деревянным конструкциям можно несколькими способами.
- Механический метод. При помощи шлифовки (сначала насадкой с крупным абразивом, затем — с мелким) можно снять верхний слой древесины со следами биопоражений и износа, удалить старое покрытие и придать поверхности гладкость. После проведения обработки изделие обязательно следует защитить средством с антисептиком, иначе оно долго не прослужит. Лакокрасочное покрытие удаляется и строительным феном.
Антисептик для древесины
- Составы для реставрации. В зависимости от состояния поверхности могут понадобиться: шпаклевка по дереву (для ликвидации трещин и сколов), ретуширующие карандаши (для маскировки мелких потертостей), восковой наполнитель (для устранения царапин).
Ретуширующие карандаши
- Декоративные средства. Обновить и придать поверхности новый облик можно при помощи лака, краски, пропитки, морилки, политуры, масла, воска и т. д.
Виды морилок
- Состаривание древесины. К этому, довольно популярному в последнее время, способу изменения внешнего вида деревянных изделий и покрытий относятся: браширование, которое заключается в обработке поверхности грубыми металлическими щетками с целью обнажить рельеф древесины и покрытии специальными составами, кракелюр (нанесение на детали средства, после высыхания которого доски покрываются сеткой трещин), обжиг открытым пламенем (он применялся при изготовлении вешалки) и обработка едкими химическими жидкостями, которые разъедают мягкие волокна досок.
Состаренная мебель на кухне
Использование всех приемов и средств позволяет кардинально изменить внешний облик мебели, особенно потерявшей привлекательность.
Цены на различные виды морилок
Морилки
Видео — Деревянная мебель своими руками. Мастер-класс по изготовлению декоративной балки
Стол и стулья для дачи своими руками из дерева фото, чертежи
Есть множество моделей столов для дачи в различных магазинах, также есть множество идей и вариантов самодельной мебели.
Если Вы собрались обустраивать участок своими силами, то для мебели мы рекомендуем использовать дерево, как самый экологичный и податливый материал.
Простой стол из досок от паллет
Паллеты нужно разобрать, доски высушить в течение 4 месяцев на проветриваемых штабелях. Для стола подойдут только ровные доски. Если Вам не нравятся следы от старых гвоздей, то можно использовать для такого стола новые гости.
Так как стол будет устанавливаться на улице, крепление досок друг к другу при помощи клея не подойдет.
- Подбираем высушенные доски так, чтобы края будущей столешницы получились ровными. Лишнее можно подрезать. (А-Б)
- Боковые части поддона шлифуем наждачкой с зерном 120 (грубой), а потом доводим до нужной гладкости наждачкой с зерном 220 (тонкой). (В)
- Неиспользованными планками скрепляем столешницу в тех местах, где идут стыки досок. На месте стыков досок используют по 2 самореза. (Г)
- Скрепляем саморезами столешницу, боковины и 2 доски. Переворачиваем конструкцию и шлифуем столешницу. (Г-Д)
- Ножки делают из шлифованных досок одинакового размера. Крепят их в диагональ на саморезы – по 2 на каждую. Для того, чтобы стол был более устойчивым, внизу делают перемычки (не ниже, чем 10 см от пола). (Е)
- Покрываем доски первым слоем лака. (Ж)
- Шлифуем поднявшийся ворс и кладем второй слой лака. (З)
Совет. Для того, чтобы доски не треснули от вкручивания саморезов, предварительно просверлите отверстия меньшего диаметра в нужных местах.
Стол из оставшихся досок
Такой способ подойдет, если у Вас есть остатки и обрезки разных досок. В этом примере использованы доски из сосны шириной 50 мм и толщиной 25 мм на раму для столешницы и с шириной 50 мм и толщиной 15мм на ножки. Стол делали длиной в 140 см, шириной 60 см и высотой ножек в 80 см.
- В первую очередь нужно отрезать две доски, равные длине столешницы (140 см). Затем делаем короткие бруски по 55 см – от нужной ширины стола (60 см) отнимаем двойную толщину доски, которую используем (5 см). Это заготовки для рамы под столешницу. Складываем их под прямым углом и крепим саморезами. (А)
- Делаем ножки – 4 доски по 80 см крепим саморезами к раме с внутренней стороны. (Б)
- Перекладины для увеличения устойчивости крепят под прямым углом примерно на высоте 40 см (середина ножек). (В-Д)
- Доски на столешницу крепят к раме финишными гвоздями. Перекладины соединяют друг с другом саморезами или гвоздями. (Е)
- Шлифуем получившуюся конструкцию и красим. (Ж-З)
Стол со склеенной столешницей
- Делаем ножки в Г-образной форме. Для них нужны доски с одинаковой толщиной (на примере 20 мм). Для крепления используем по 5 саморезов. Сперва просверливаем отверстия на 1-2 мм меньше диаметром, чем саморезы. Затем высверливаем углубления для шляпок саморезов или заглушек. Последние можно купить в магазине или сделать самостоятельно из деревянного стержня или смеси древесной пыли и шпаклевки по дереву.
Доски нужно соединять строго под углом в 90 градусов. Сначала места стыков промазывают столярным клеем, а потом скрепляют саморезами (по краям, в середине и в конце остальные 2). (А)
- После того, как клей высохнет, шкурим и лакируем поверхность ножек. (Б)
- Делаем столешницу из досок одинаковой толщины. Ширину можно брать разную. Главные условия – ровные края стола и плотная стыковка фрагментов.
Боковины нужно промазать клеем, на ровной поверхности стянуть струбцинами (желательно использовать не меньше 3 штук) так, чтобы не оставалось зазоров между досками, и оставляем сохнуть в течение суток. После высыхания струбцины снимаем, ровняем края столешницы и шлифуем. Форму столешнице можно придать любую на Ваш выбор. (В-Г)
- Отделочную рамку делаем из тонкой планки, ошкуренной и приклеенной к столешнице. Дополнительно для крепления можно использовать финишные гвозди. (Д)
- Рама для стола собирается по тому же принципу (см. пункт 4). Ее крепят клеем на тыльную сторону столешницы, через которую потом устанавливают конфирматы для мебели.
- Ножки крепятся на раму с внутренней стороны саморезами.
Садовый столик, соединенный со скамейками
Используемые доски – 38х89 мм (для этого примера). Можно взять стандартных размеров.
Используемые крепления:
- Шпильки с гайками и шайбами – длина 16 см, 24 шт.
- Гвозди – длина 8.0 см.
Изготавливаем сиденья.
- Берем доски нужного размера и тщательно шлифуем.
- На длинную доску крепим с торца короткие доски со спилом в 45 градусов.
- К спиленным опорам гвоздями крепим доски сиденья на небольшом расстоянии друг от друга.
- Сиденья соединяем между собой длинными досками (4 штуки) при помощи шпилек.
Делаем столешницу и ножки для нее.
Столешница скрепляется гвоздями и четырьмя поперечными досками со спилом в 52 градуса, установленных на расстоянии, достаточном для размещения между ними досок для ножек.
Перекрестие досок на ножку должно находиться в их середине. На каждой из досок выпиливаем углубление (паз) до середины ее толщины.
Складываем доски пазами, так они окажутся в одной плоскости, и закрепляем 4 гвоздями.
Вторую ножку делаем по аналогии с первой.
Собираем конструкцию.
Ножки располагают на равном удалении от скамеек. Все крепления (ножки-сиденья и ножки-столешница) делаем шпильками.
Примеры аналогичных и других простых вариантов столов для частного дома и дачи
Стол из эпоксидной смолы, мастер-класс по созданию в домашних условиях
Необычные дизайнерские решения все чаще встречаются в современных квартирах. Кроме стандартных материалов, для изготовления используются и такие, что позволяют воплотить в жизнь самые интересные идеи. Очень эффектно смотрится стол из эпоксидной смолы, который можно сделать своими руками. В комбинации с деревом этот материал позволяет создавать настоящие шедевры.
Дизайн и особенности конструкции
Столы из эпоксидной смолы характеризуются уникальным дизайном и могут вписаться в любой интерьер. Чаще всего их используют в кухнях и гостиных, при этом нет строгих требований к стилевому решению. Эпоксидка используется не только для изготовления новых изделий, но и для восстановления старой мебели. Многие модели производятся при помощи комбинирования нескольких материалов.
Особенность смолы в том, что она почти не усаживается после затвердевания, поэтому длительное время сохраняет свою изначальную форму. Кроме того, ее можно по-разному декорировать. Столы со смолой бывают нескольких типов конструкций:
- Комбинированные. В этом случае синтетический материал чередуется с элементами древесины.
- С присутствием опоры. Смолой заливают только верхний слой. Дополнительно используются различные декоративные элементы: листочки, монеты, цветы.
- Без присутствия опоры. Тут присутствует только эпоксидка. Таким способом изготавливаются небольшие журнальные столики. Они не предназначены для значительных механических нагрузок.
Изделие может быть прозрачным, одноцветным или комбинированным. Чаще всего используются светлые бирюзовые, голубые оттенки. Нередко конструкция снабжается дополнительной подсветкой или люминесцентным порошком. Столы ручной работы имеют высокую стоимость, но такую мебель можно изготовить и самостоятельно. Преимуществом процесса является снижение стоимости модели. Есть и другие плюсы: возможность проявить фантазию, восстановление старой мебели оригинальным способом.
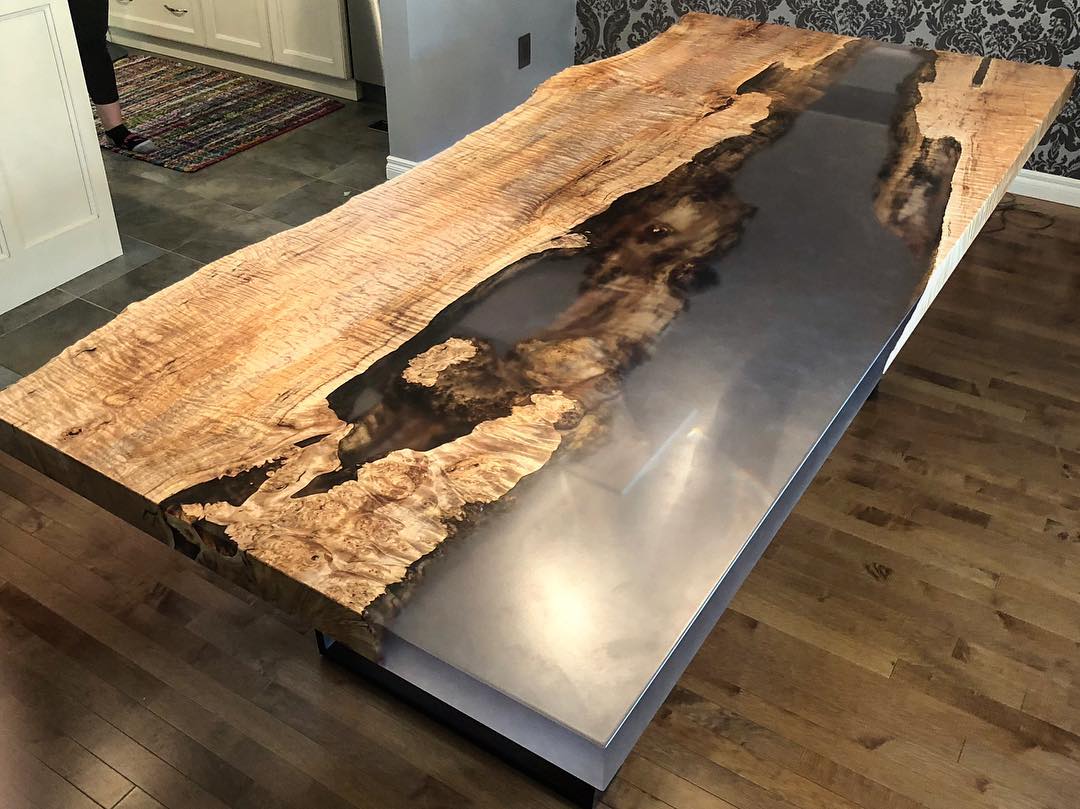
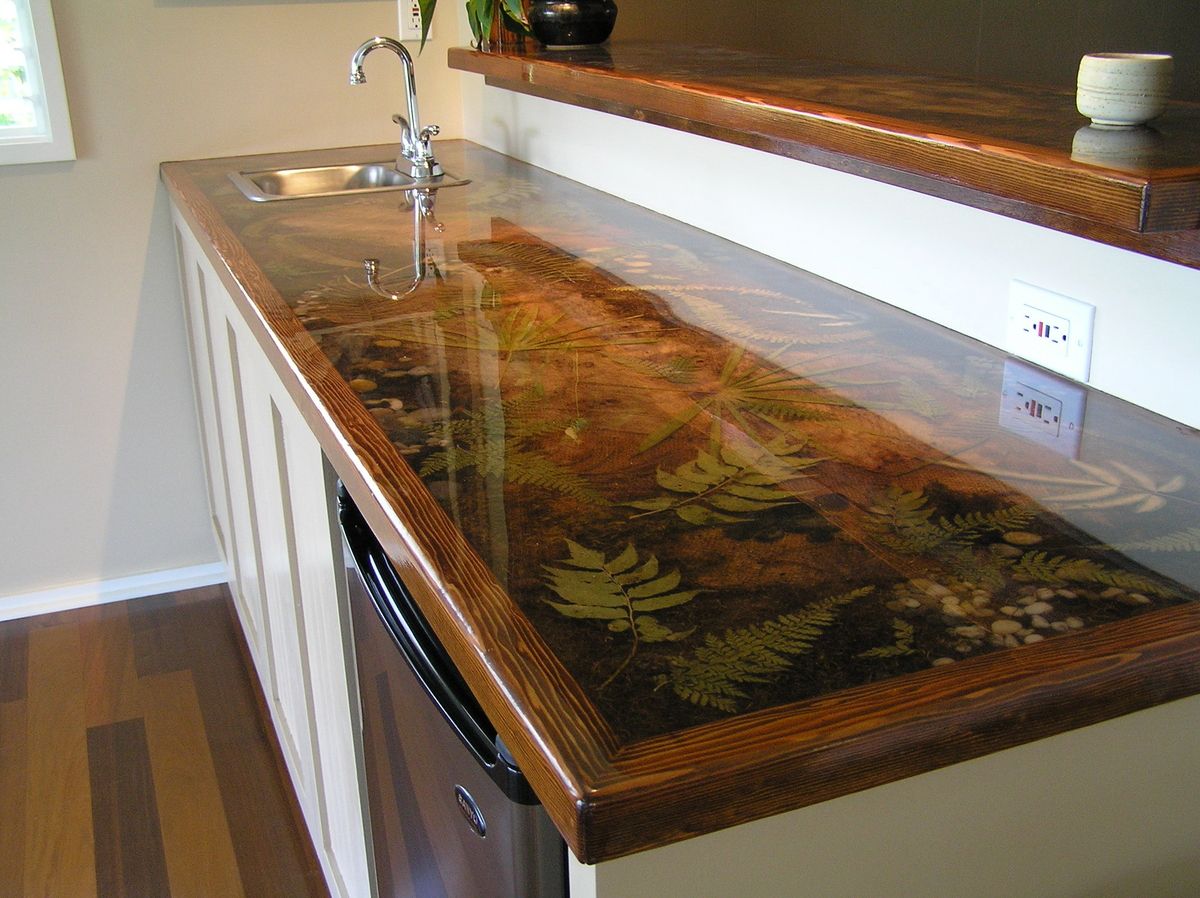
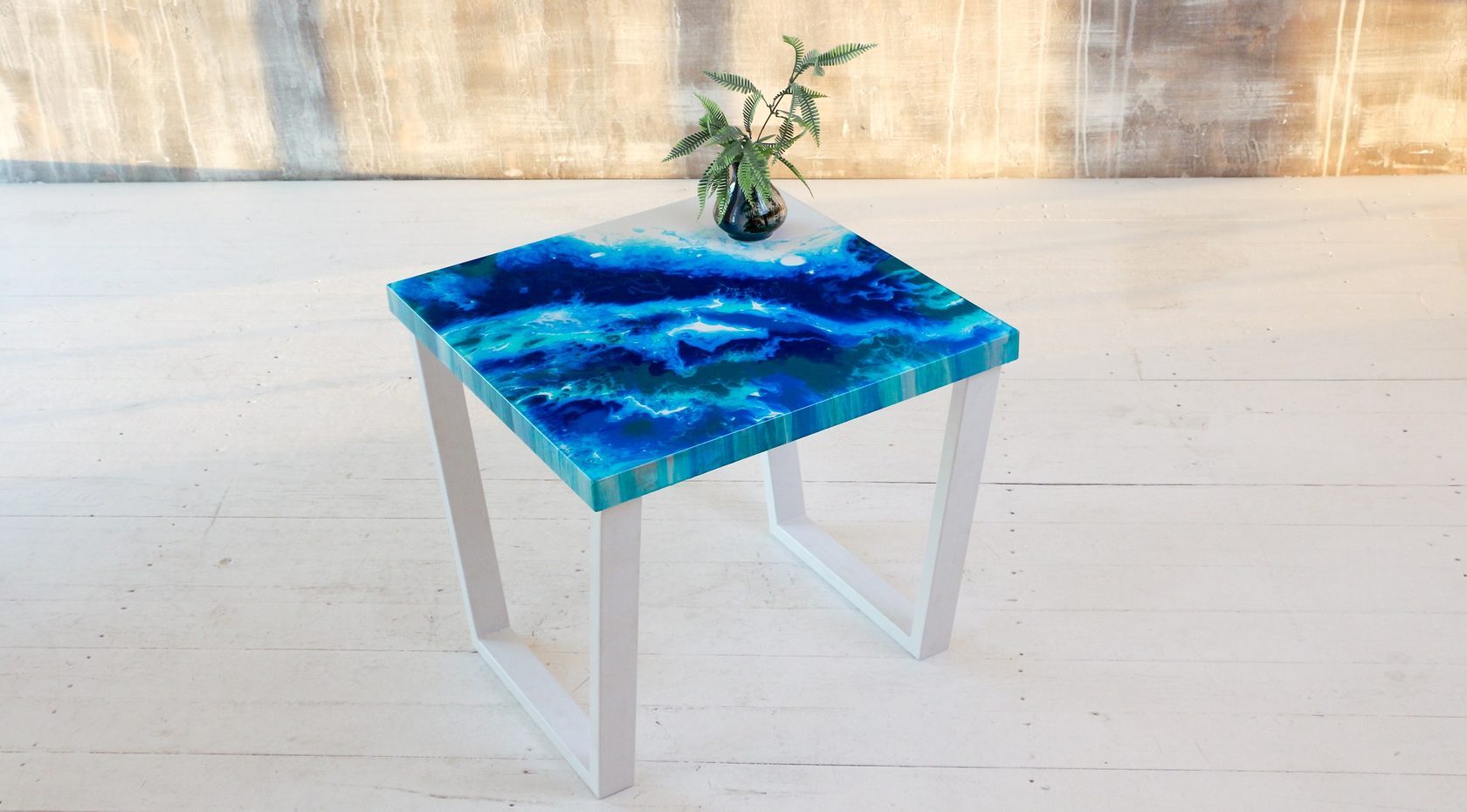
Свойства эпоксидной смолы
Эпоксидная смола – синтетический материал-олигомер. В чистом виде он не используется. Для получения твердого фрагмента смолу нужно полимеризировать при помощи отвердителя. Разные пропорции компонентов позволяют создать материалы с неодинаковыми физическими и механическими свойствами. Смола обладает такими качествами:
- прочность и устойчивость к воздействию химических веществ;
- отсутствие неприятного запаха при работе с эпоксидкой;
- процесс полимеризации происходит при температуре от -15 до + 80 градусов;
- незначительная усадка после затвердевания материала, его стабильная структура;
- слабая влагопроницаемость;
- высокая устойчивость к механическим повреждениям и абразивному износу;
- отсутствие потребности в дорогостоящем уходе.
При использовании дополнительных защитных компонентов такой стол становится невосприимчивым к воздействию прямых солнечных лучей.
Смола имеет и некоторые недостатки: при воздействии высоких температур она способна выделять вредные вещества. Для работы с веществом необходимо иметь определенные навыки и полностью соблюдать технологию применения. Такой материал имеет высокую стоимость.
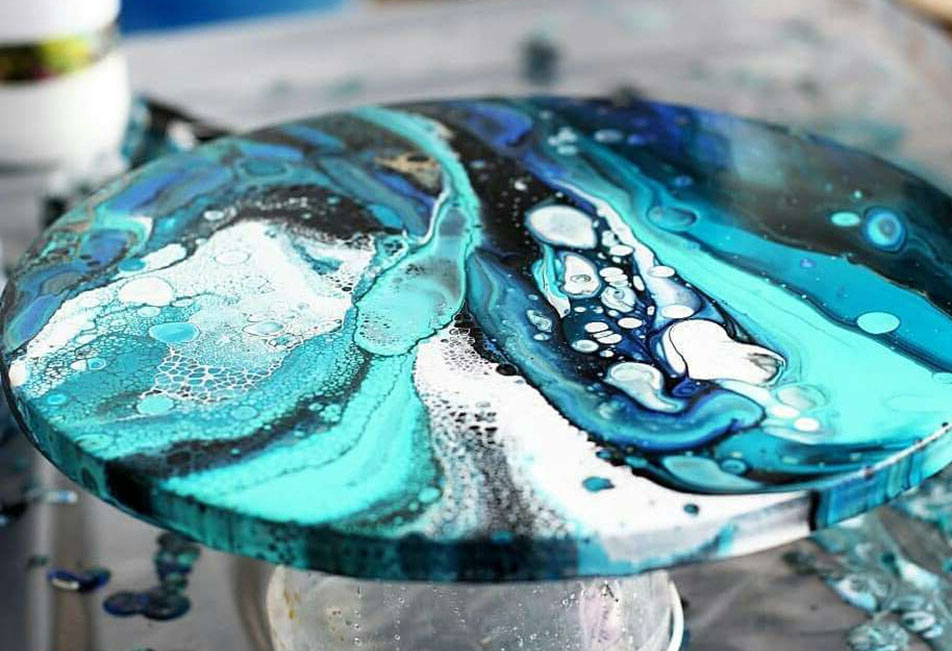

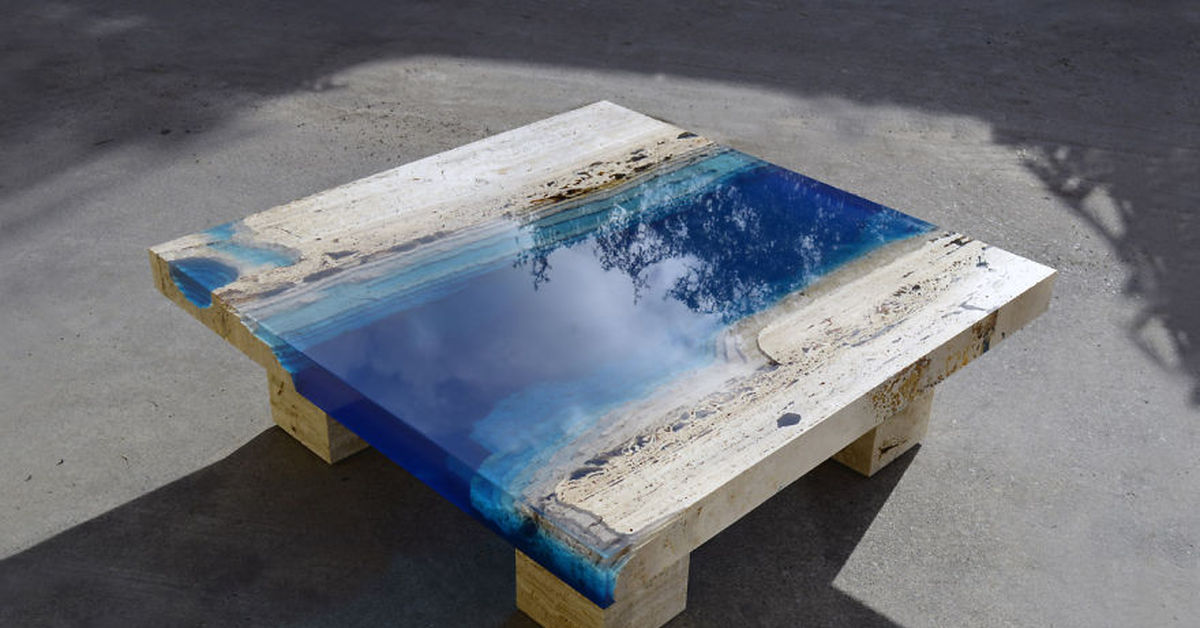
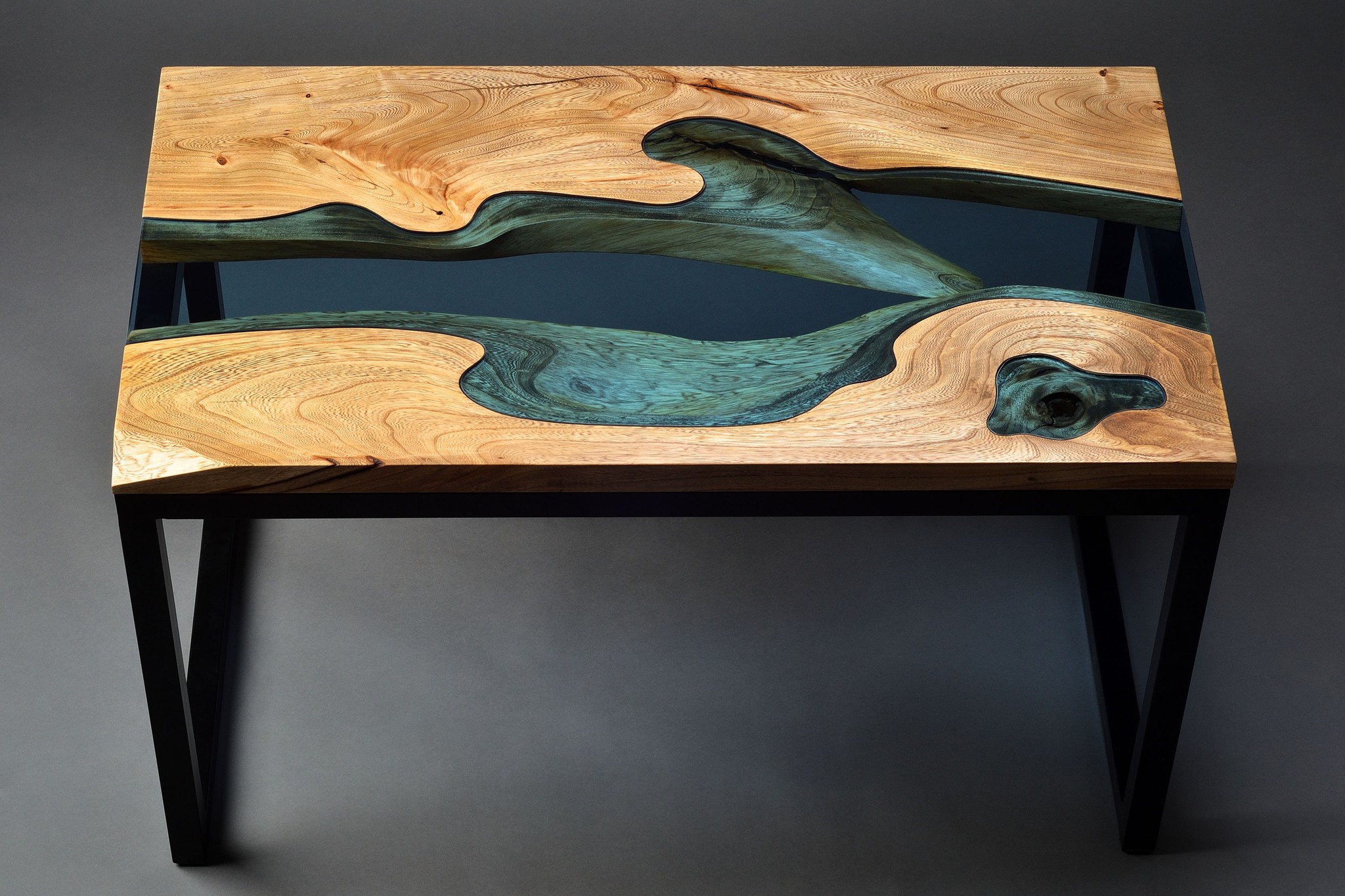
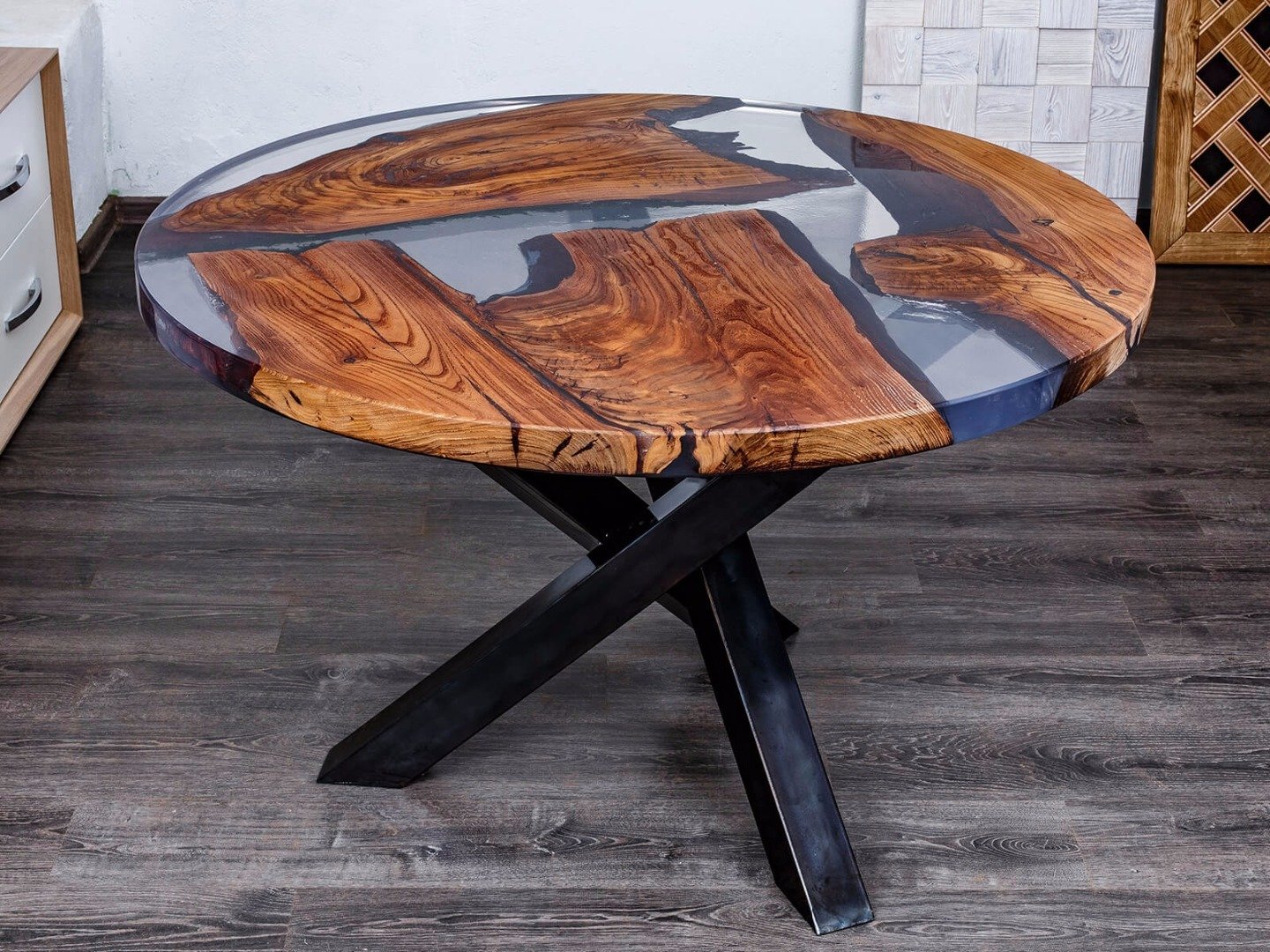
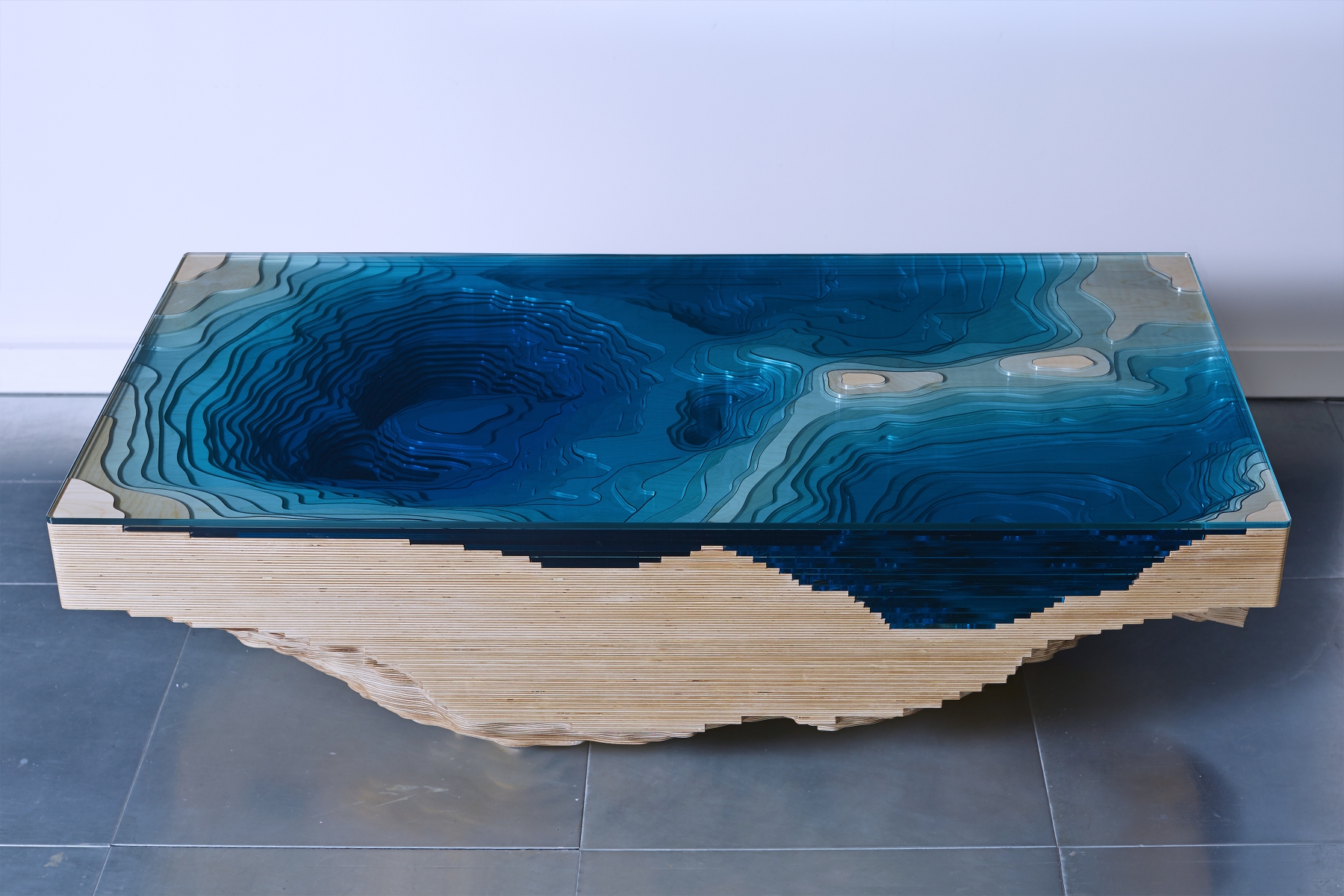
Популярные модификации
Изготовление стола из эпоксидной смолы – задание для мастера с хорошей фантазией. Кроме стандартных кусков древесины, для декорирования можно использовать люминесцентные краски или порошки, пуговицы, винные пробки, мох, листья растений, морские камни, булыжники.
Река
Особенностью конструкции стола-реки с эпоксидной смолой является то, что в ее основе одинаковое размещение элементов: между двумя кусками древесины локализуется вставка из указанного материала. Она может быть прямой или повторять изгибы дерева, широкой или узкой, с декоративными фрагментами, островками, камешками.
Формы столешниц тут бывают разными: круглыми, овальными, прямоугольными. Интересными являются варианты, в которых древесина играет роль речного берега, а смола – воды. Устанавливать данные изделия можно в гостиной и на кухне. Отлично смотрится модель в кабинете. С рекой можно сделать журнальный столик в стиле прованс, кантри. Что касается расхода материала, то на реку размерами 210 х 15 х 5 см надо около 13-14 кг вещества.
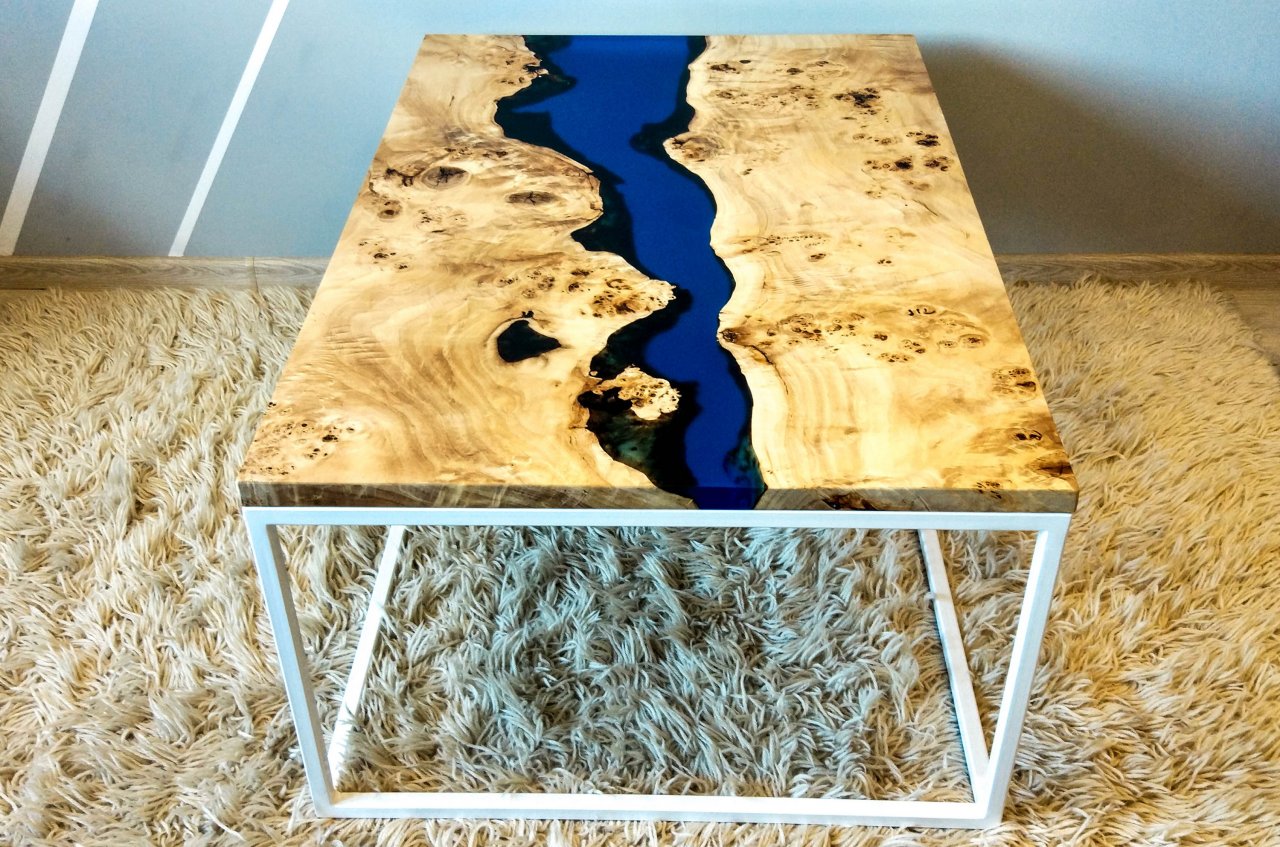
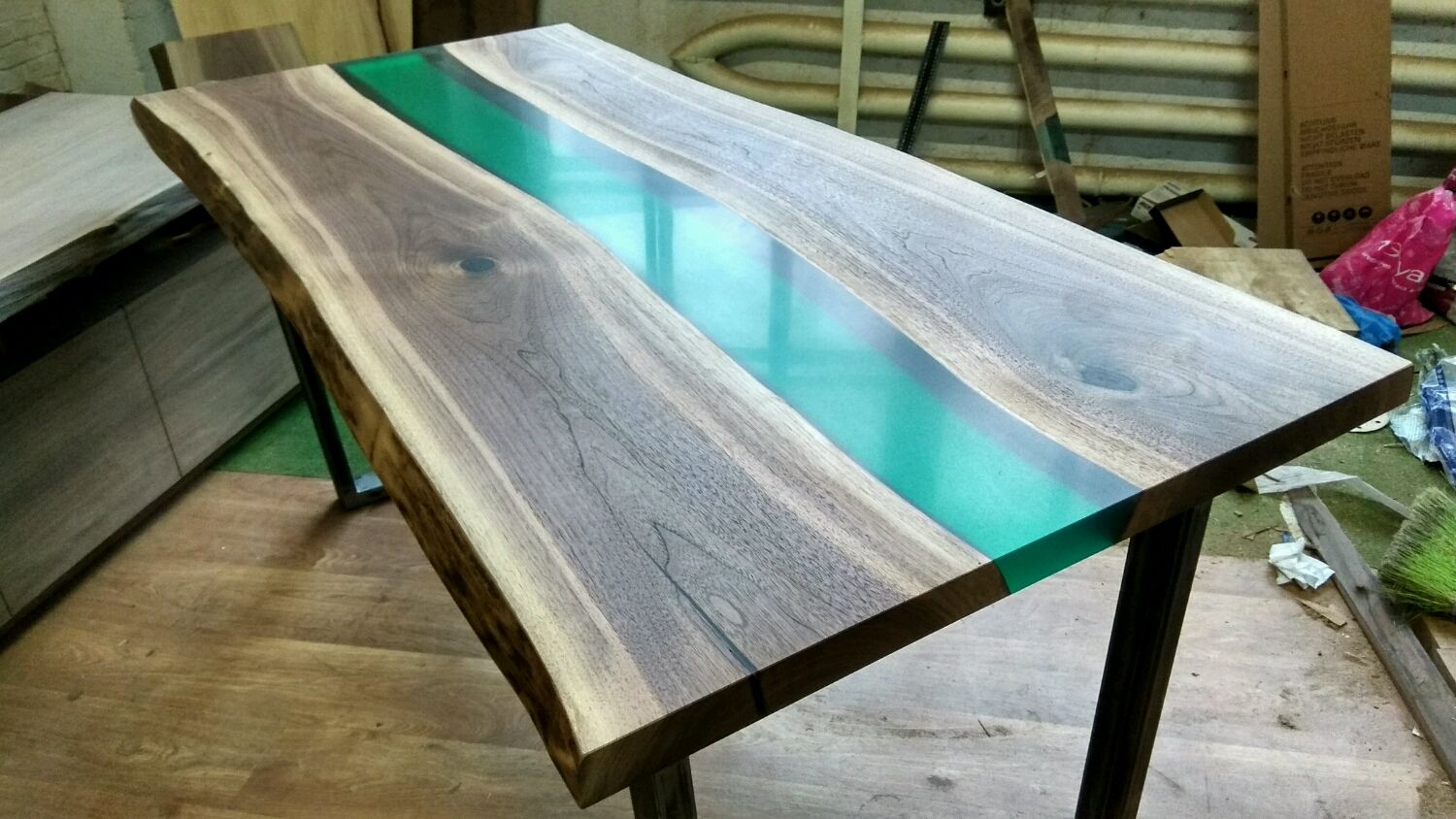
Сплошная поверхность
Для создания сплошного стола из жидкого стекла, требуется использование формы необходимого размера. Чаще всего такие конструкции производятся без опоры и не предусматривают интенсивной нагрузки. Столешницы такого типа применяются для производства журнальных или туалетных столиков. Для изготовления столешницы из эпоксидной смолы, размеры которой составляют 100 х 60 х 5 см, требуется около 30 л смолы.
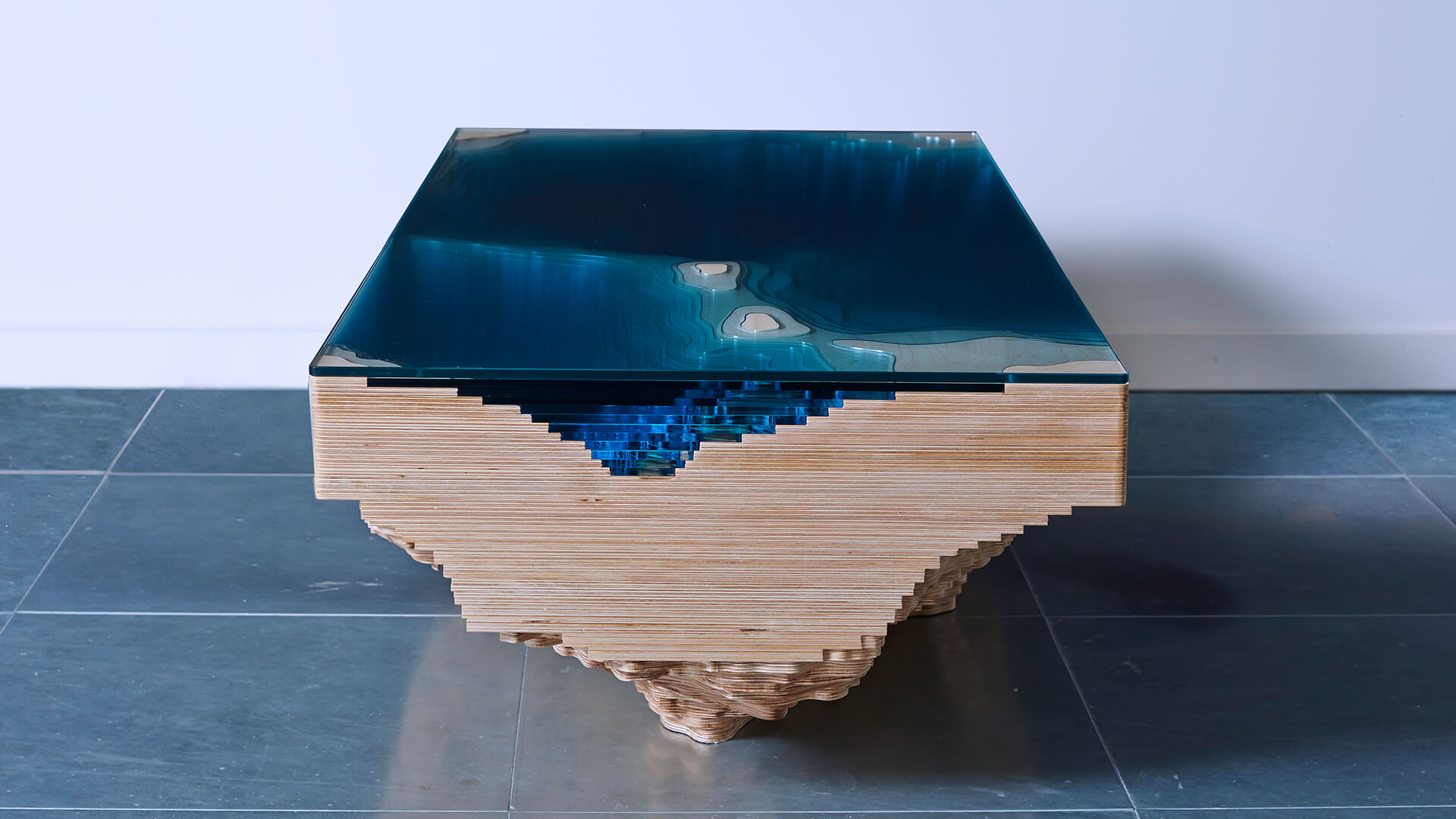
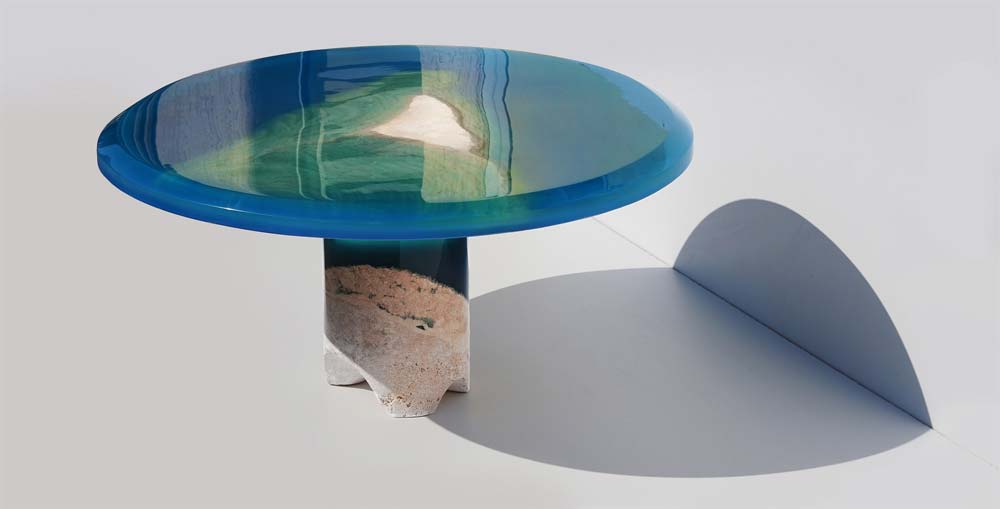
Из слэба
Слэбы – цельные массивные плиты из древесины или камня. Чтобы изготовить такое изделие в домашних условиях, берется более легкий материал. Дерево обычно представляет собой продольный спил ствола с оставшимися сучками, неровностями по краям. Это позволит создать уникальную модель.
Часто стол из слэба изготавливается из дуба. В таком формате можно смастерить кухонную поверхность, конструкцию для гостиной, кабинета. Толщина древесного материала при этом составляет от 5 до 15 см. Он не должен быть склеен или иметь других соединений. Для изготовления стола из слэбов с эпоксидной смолой средних размеров потребуется около 10 кг вещества.
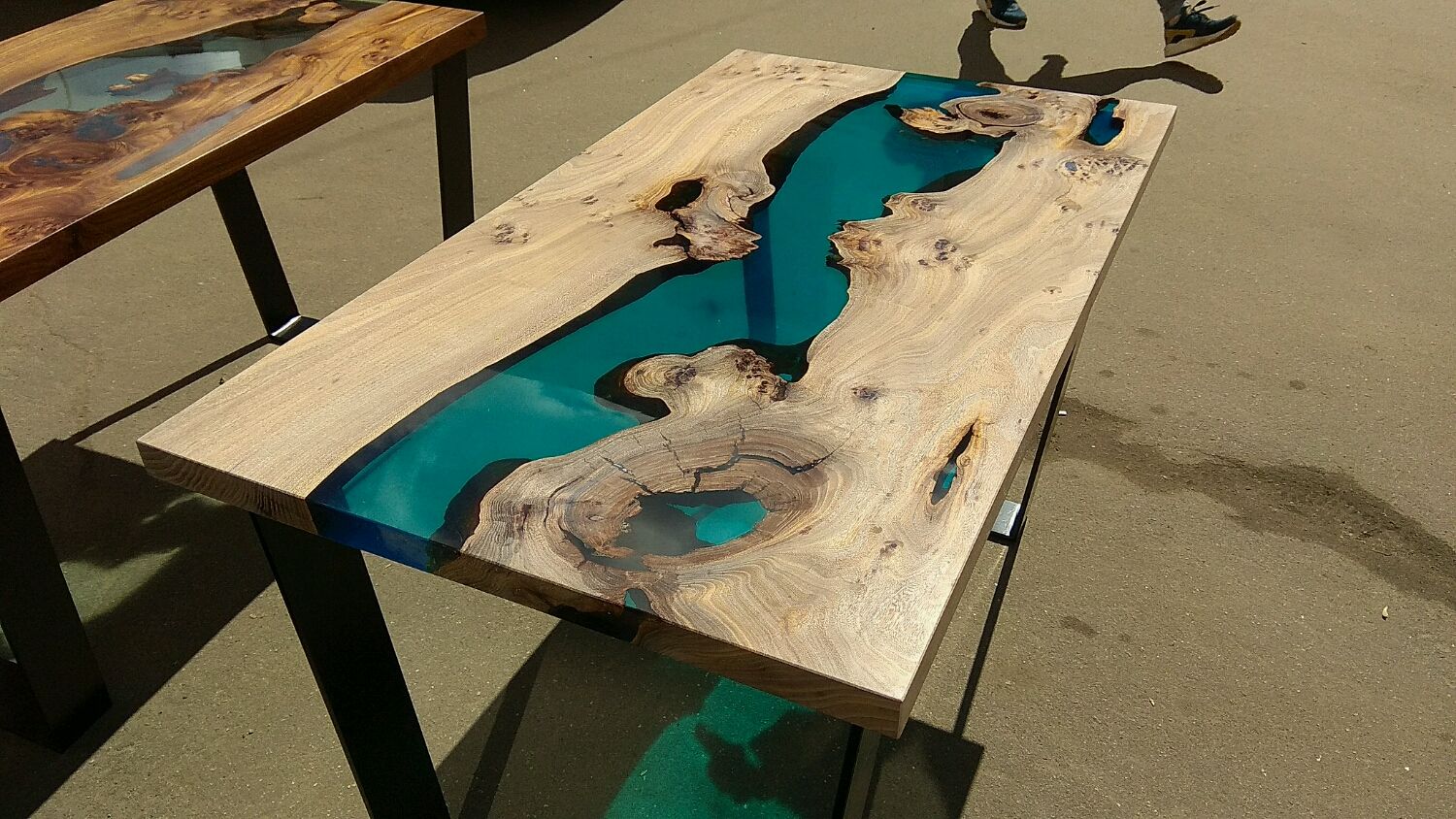
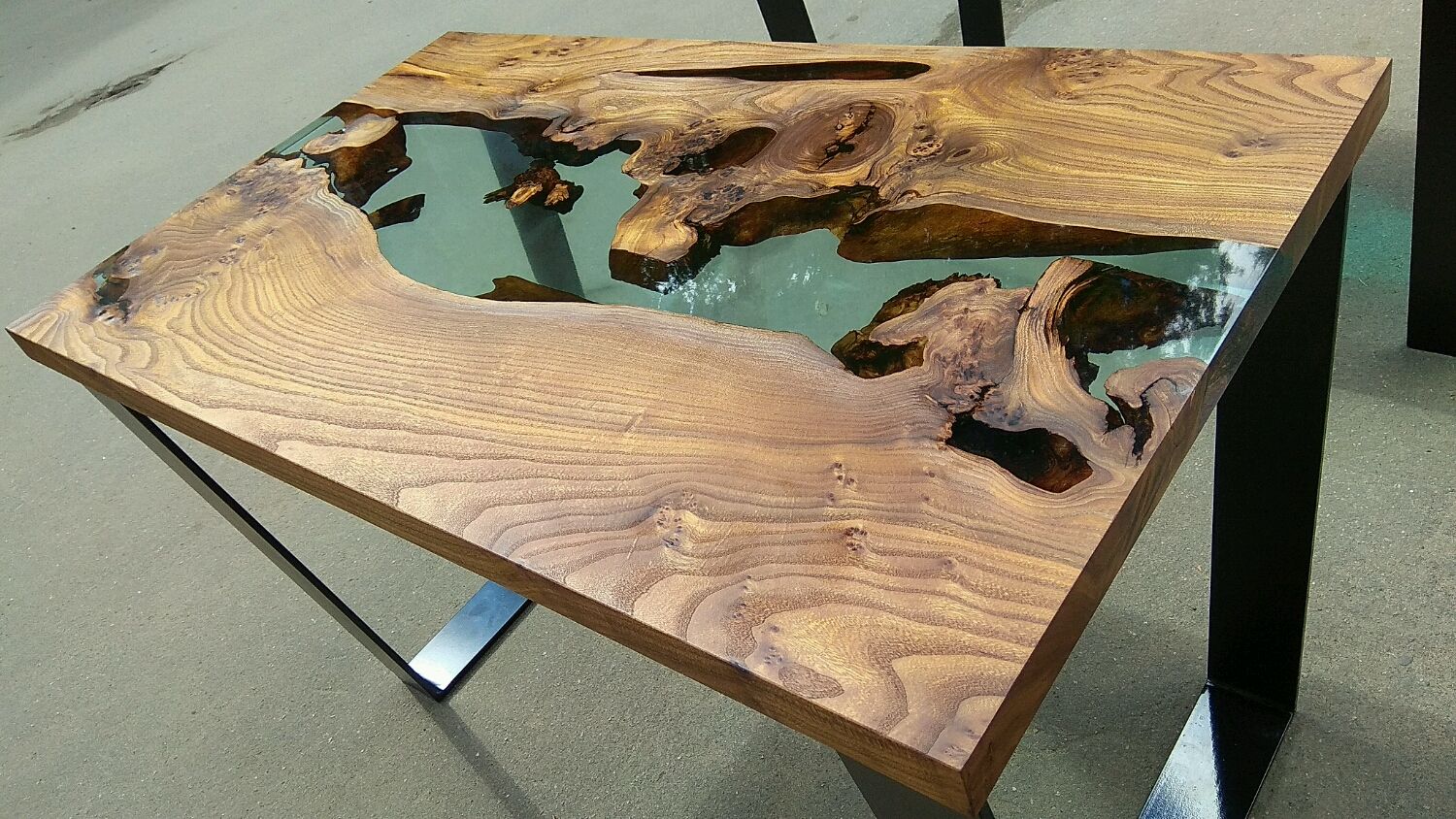
Из спилов
Столы из массива дерева смотрятся очень оригинально, богато. Не менее эффектно выглядят модели спилов древесного материала, покрытые раствором из эпоксидки. Чтобы залить такую столешницу, требуется минимум 7 кг полиэфирных веществ. Эта модель отлично подходит для кухни, дачи в стиле кантри, эко. Из какого бы пенька или цельного ствола ни были сделаны спилы, рисунок каждого из них будет уникальным.
Столы такого типа имеют разную форму: круглую, овальную, прямоугольную и даже квадратную. От ее выбора зависит количество используемых фрагментов. Материал должен иметь высокое качество и нужный диаметр. Треснутые элементы использовать не рекомендуется.
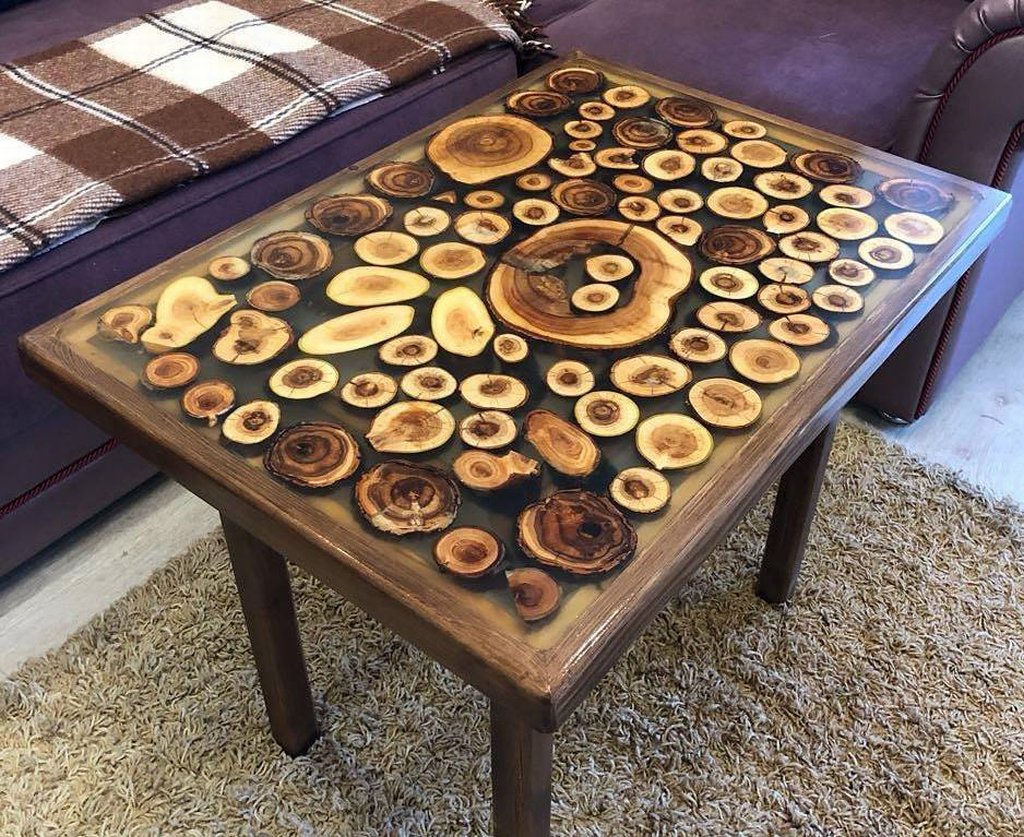
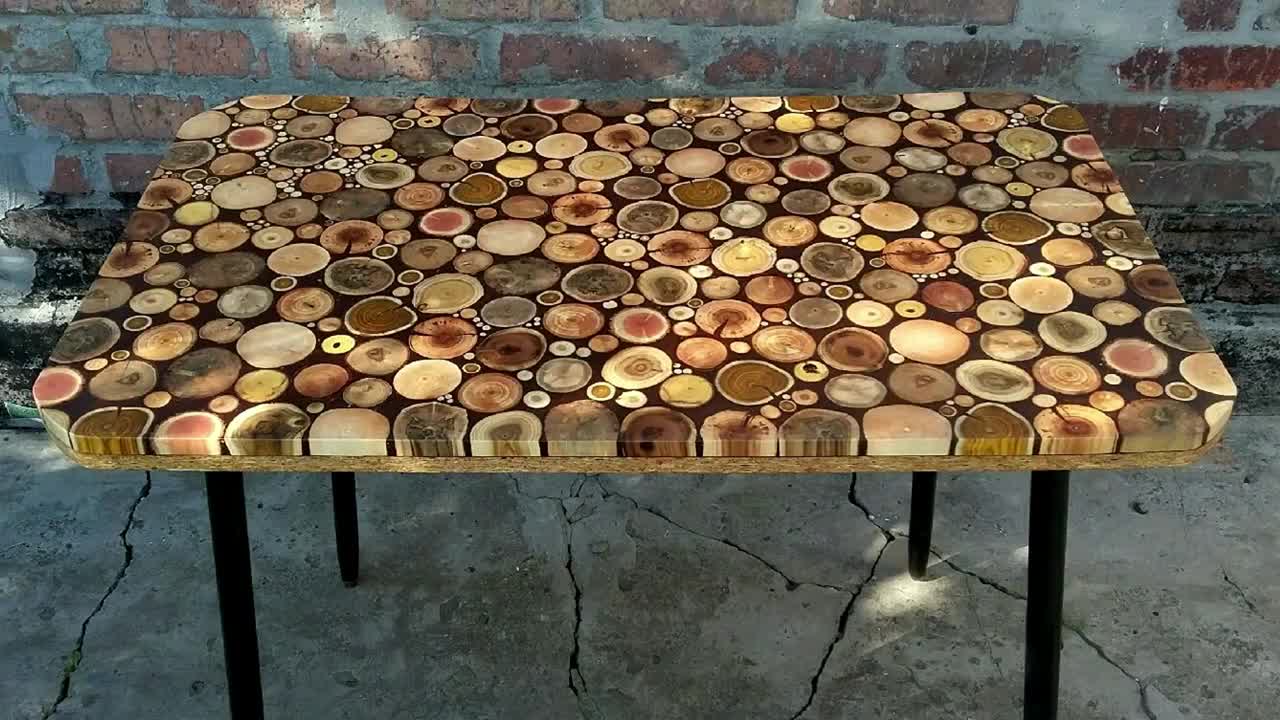
Выбор элементов каркаса
Стол из эпоксидной смолы, как и все другие модели, состоит из столешницы и опоры. Для их изготовления могут применяться совершенно разные материалы. Выбрать подходящий тип конструкции можно исходя из ее предназначения.
Столешница
При изготовлении стола из дерева и эпоксидной смолы необходимо выбрать, из каких именно элементов будет состоять верхняя часть. Отлично смотрится как залитый массив, так и отдельные его куски. Если материал мягкий, то следует использовать более жидкую смолу.
Чтобы сделать деревянный стол с эпоксидкой, можно использовать поперечно разрезанные доски, ветки, древесину с выемками, крупные спилы дерева. Причем сорт и твердость материала в одном изделии могут отличаться. С необработанными фрагментами работать сложнее, но изделие получается более красивым. Если конструкция делается из цельной доски, то тут производится заливка верхнего слоя смолой вместо лакирования поверхности.
Прозрачные столешницы тоже пользуются популярностью. Технология их изготовления предусматривает создание формы из фанеры или стекла. Наполнитель бывает совершенно разным: каменная засыпка, искусственный жемчуг, песок, ракушки, шишки.
Интересно смотрится вариант стола из эпоксидной смолы с объемными изображениями или диорамами внутри. А светящуюся модель можно вписать в любой интерьер, сделав обстановку более романтичной. Также можно соорудить эпоксидный стол из нескольких слоев застывшего материала, склеив их между собой.
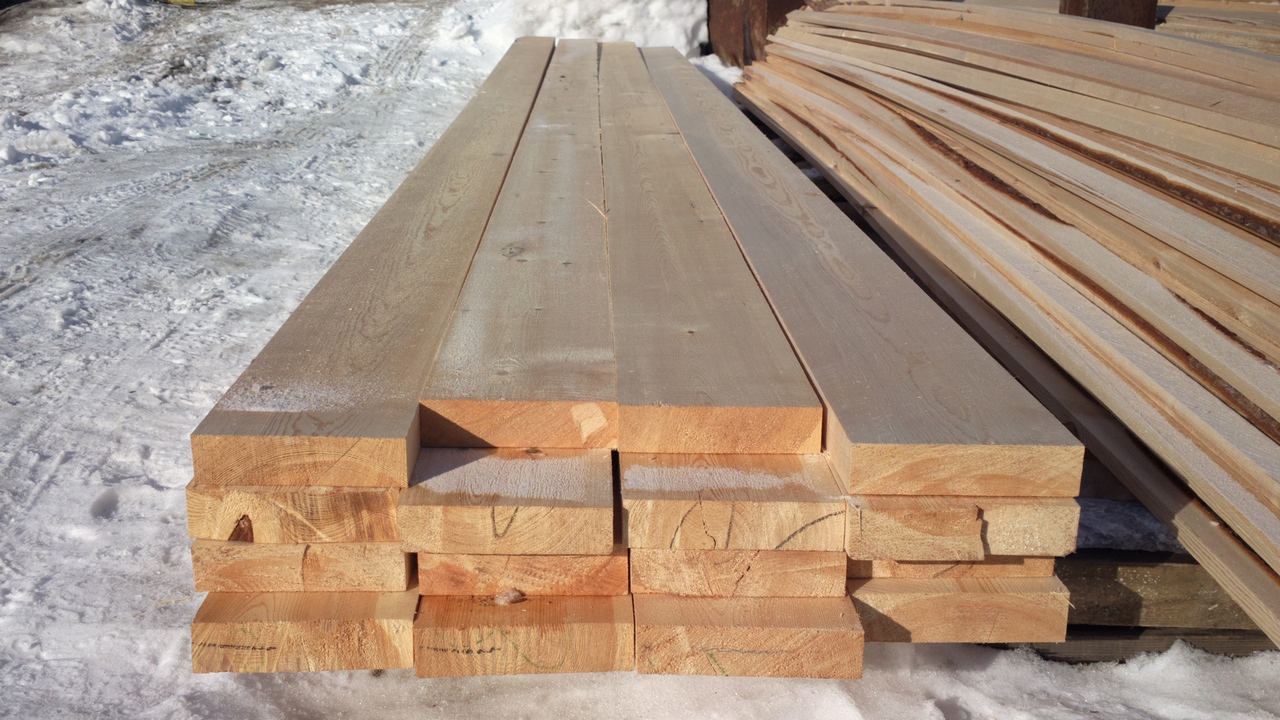
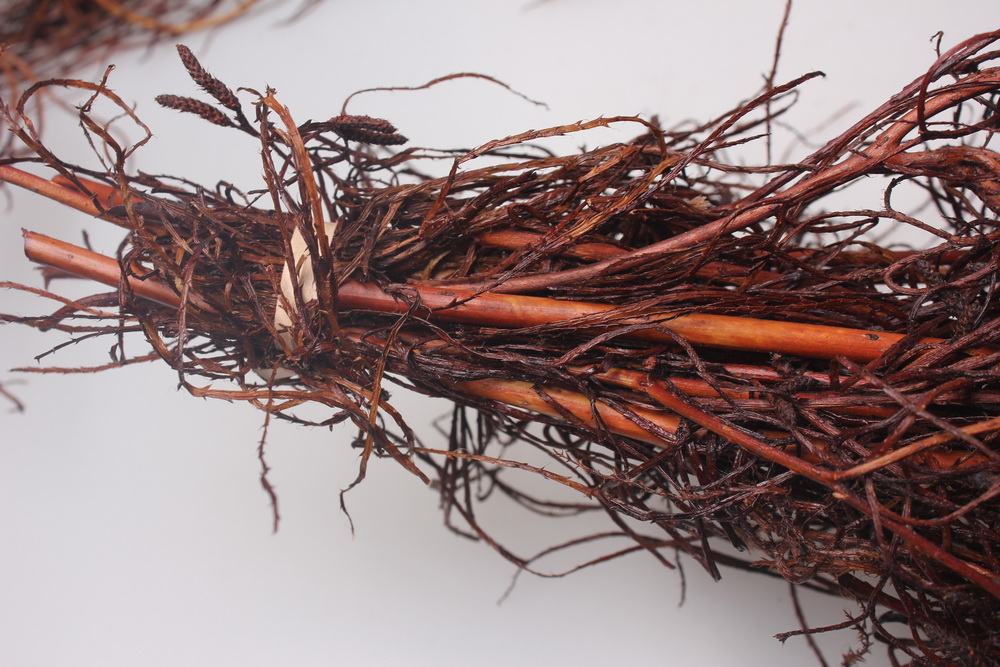
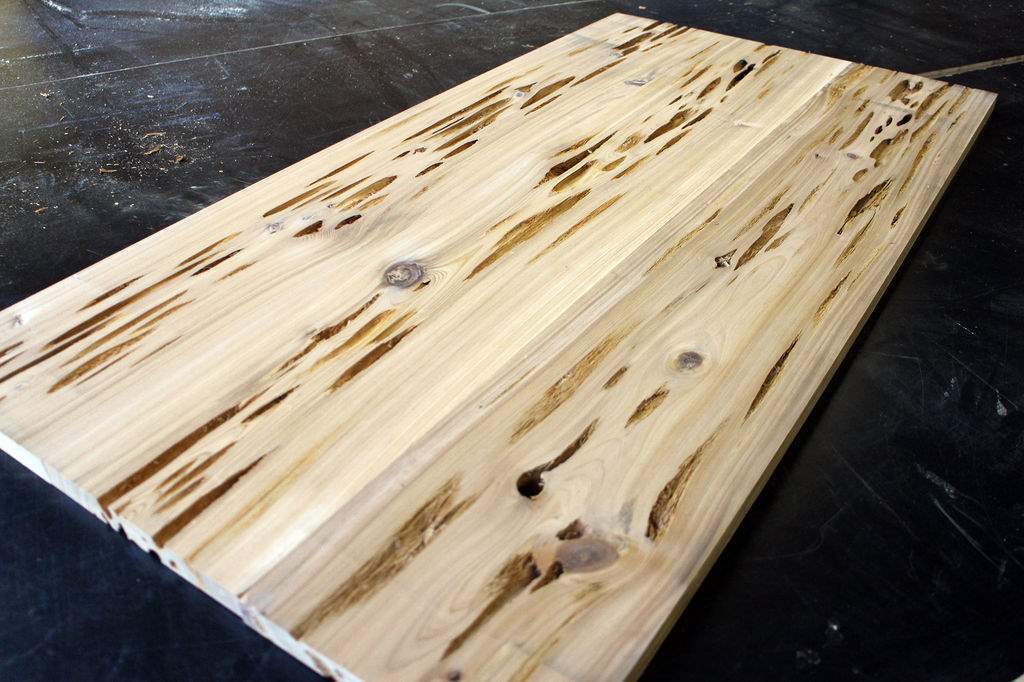
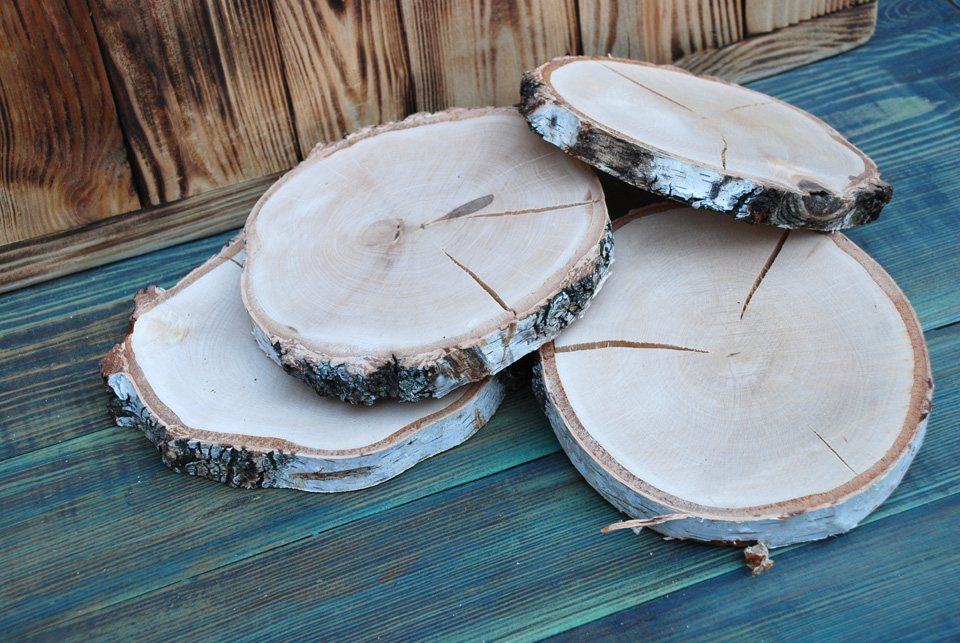
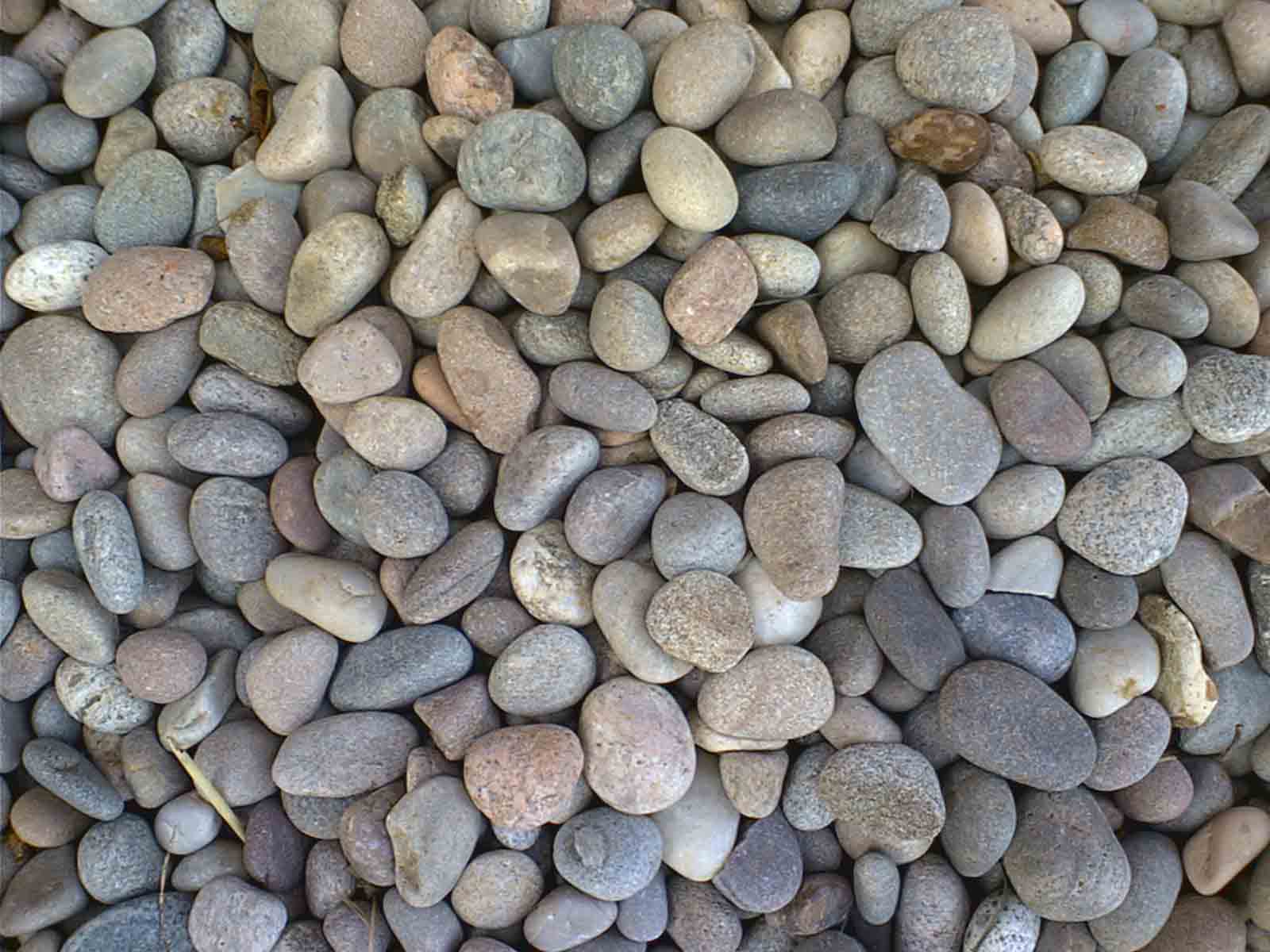
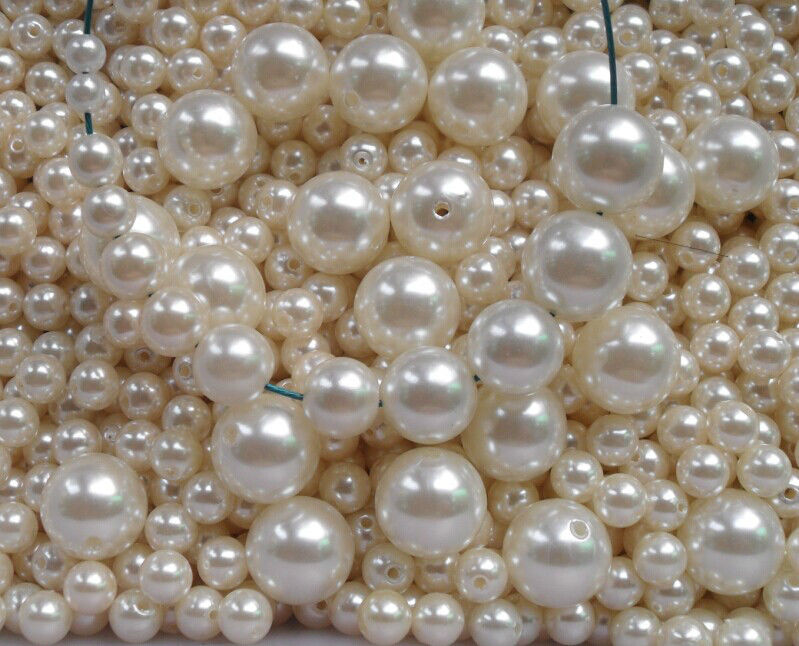
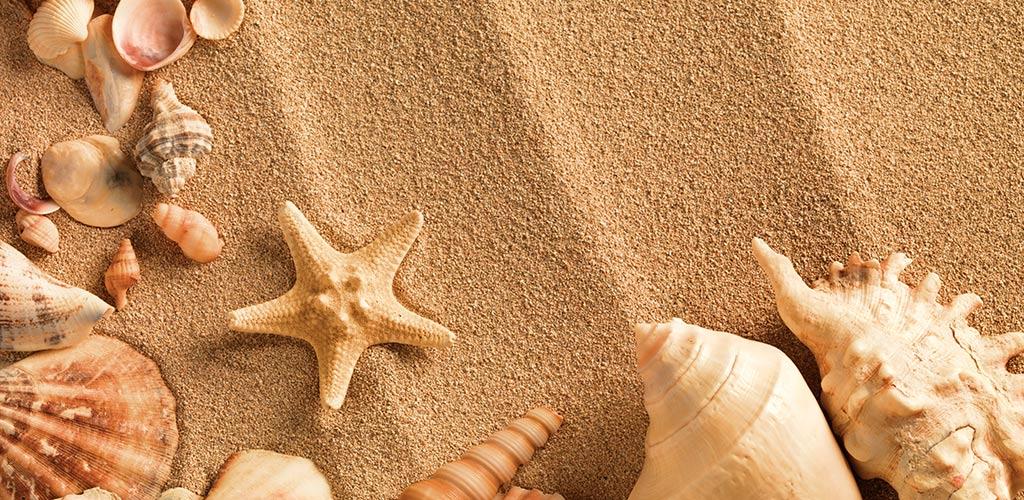
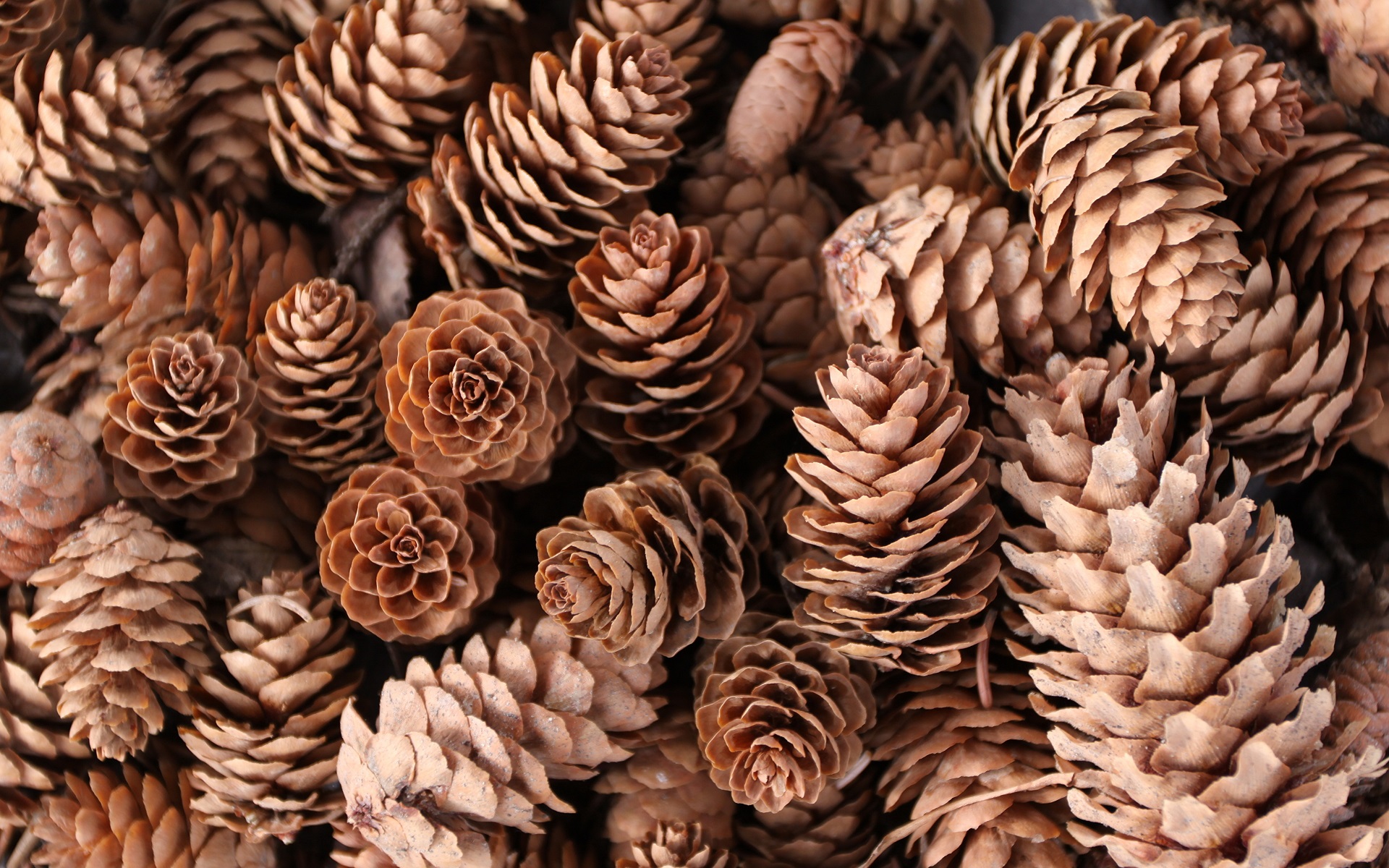
Основание
Чаще всего ножки, на которые устанавливаются столы из эпоксидной смолы, изготавливаются из дерева или металла. Каждый материал имеет свои особенности. Выбирать его нужно исходя из эксплуатационных параметров стола и общего интерьера.
Тип | Характеристики |
Деревянные | Смотрятся естественно, стильно, основательно. Они долговечны и практичны. Для изготовления опор лучше брать древесину дуба, бука или лиственницы. Они обеспечивают максимальную устойчивость изделию, отлично подходят для классического стиля оформления интерьера. |
Металлические | Даже если нужно изготовить стол из массива дерева с эпоксидной смолой, такие ножки станут устойчивой опорой. Ассортимент материалов шире: сталь, чугун, алюминий. Окрашивать опоры необязательно. Если металл используется в бытовых условиях, то он не требует дополнительной обработки. Железо является более прочным, чем дерево, остается устойчивым к механическим повреждениям. |
Что касается формы, то основание может быть сделано в виде отдельных ножек, квадратных или прямоугольных рам. В круглых моделях изумительно выглядит одна опора, сделанная из дерева или металла и зафиксированная по центру.
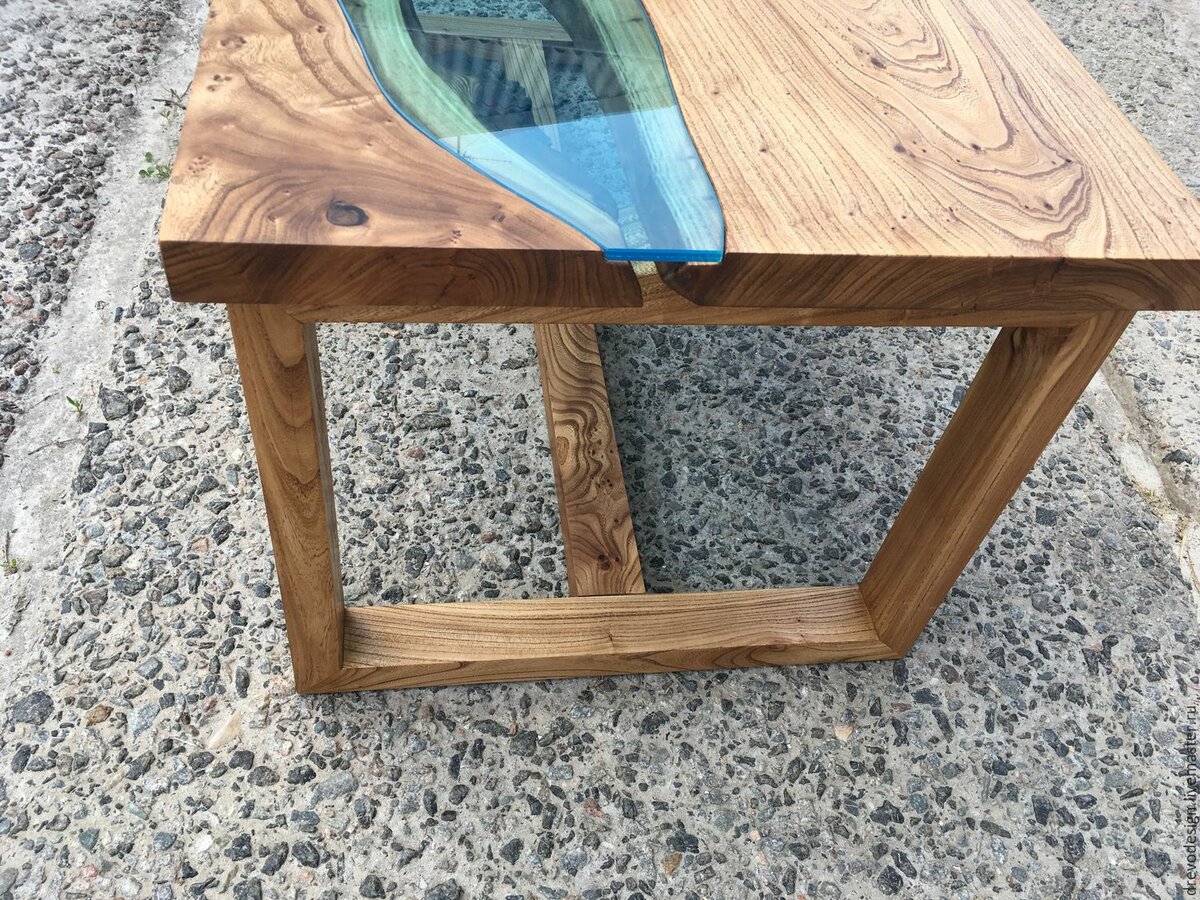
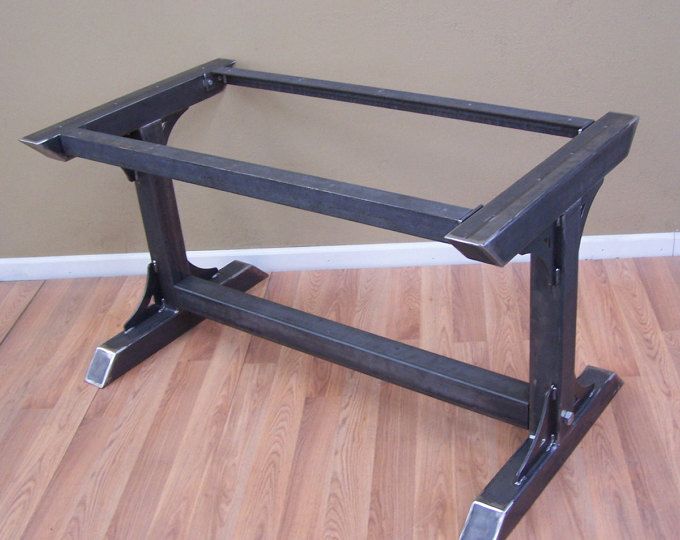
Технология работы
Для изготовления стола эпоксидная смола и дерево должны быть правильно выбраны. Не стоит отдавать предпочтение слишком дешевым составам, так как они быстро мутнеют и желтеют. Лучшим типом эпоксидки на стол является CHS Epoxy 520. Продается она обычно сразу с отвердителем. Смешивать эти вещества необходимо в пропорциях, указанных в инструкции.
Чтобы приготовить раствор, требуется 2 емкости. Сначала замешивается смола. При необходимости изменения ее цвета в вещество добавляется колер. После этого смесь нагревается до 30 градусов и тщательно размешивается. Теперь добавляется нужное количество отвердителя. Масса перемешивается до однородного состояния. Если в ней появились пузырьки, то их следует выдуть феном.
Чтобы сделать столы из дерева и эпоксидной смолы, нужно добиться правильной густоты состава. От этого зависит конечный результат. Существуют такие степени вязкости:
- Жидкая. Масса легко стекает с палочки. Она хорошо пропитывает древесину, проникая во все выемки, поры, уголки.
- Полужидкая. Такая форма состава используется при заливке круглого стола из эпоксидной смолы и дерева. Еще она применяется для изготовления декоративных деталей.
- Густая. Для производства заливки она не подходит. Применяется такой состав, если нужно отреставрировать стол из дуба. Еще такая консистенция используется для изготовления украшений.
Перед началом основной работы происходит первичная обработка без использования вспомогательного короба. Заливать надо все трещинки и отверстия, затем эти участки прогревают, чтобы ушли воздушные пузырьки. После просушки эти зоны надо отшлифовать, чтобы они были вровень с поверхностью доски. Далее требуется покрыть тонким смоляным слоем всю доску, выгнав воздух из пор, и основательно высушить.
Для изготовления столика из эпоксидной смолы своими руками требуется подготовка формы. С этой целью обычно применяется стекло, которое нужно хорошо очистить и обработать обезжиривателем. Нужно обращать внимание на наличии сколов, трещин, качество стыков.
Стол из эпоксидной смолы своими руками смастерить нетрудно, важно соблюдать технологию. Слой вещества не должен превышать 5-6 мм. Лить средство надо тонкой струей при помощи палочки. Для выравнивания смолы используется шпатель. Чтобы удалить пузырьки воздуха, нужно проколоть их иглой или продуть феном. Готовый стол из массива дерева и эпоксидной смолы нужно накрыть полиэтиленом, исключить попадание пыли и мусора.
После застывания изделия его нужно отшлифовать, отполировать и покрыть лаком. Грубый абразив для стола из эпоксидной смолы использовать нельзя. Шлифовка производится медленно, а на поверхность периодически наливается вода, чтобы она не перегревалась. После завершения процесса стол покрывается лаком.
Так как сделать стол с эпоксидной смолою нужно технологически правильно, важно соблюдать нюансы работы с составом. Смола быстро застывает в теплом помещении. Сверху греть слой нельзя, так как он деформируется. Кроме того, есть и другие особенности:
- во время застывания слоя нельзя допускать попадания прямого солнечного света на него, так как смола пожелтеет;
- при работе с составом нужно использовать средства защиты;
- замешивать смолу нужно медленно.
Если мастер занимается заливкой в зимнее время, не стоит оставлять столик из слэба на морозе, иначе смола расслоится. Изделие после высыхания может выделять токсины, поэтому на него нужно нанести защитный лак.
Чтобы работать с заливными материалами, нужно правильно рассчитать, сколько сырья понадобится. Тут следует воспользоваться такой формулой: V = А (длина) х В (ширина) х С (толщина). Так как смола плотнее воды, то нужно учитывать коэффициент и пользоваться такой формулой: V х 1,1. Стандартный расход вещества на 1 квадратный метр площади составляет 1,1 литра, если толщина слоя 1 мм.
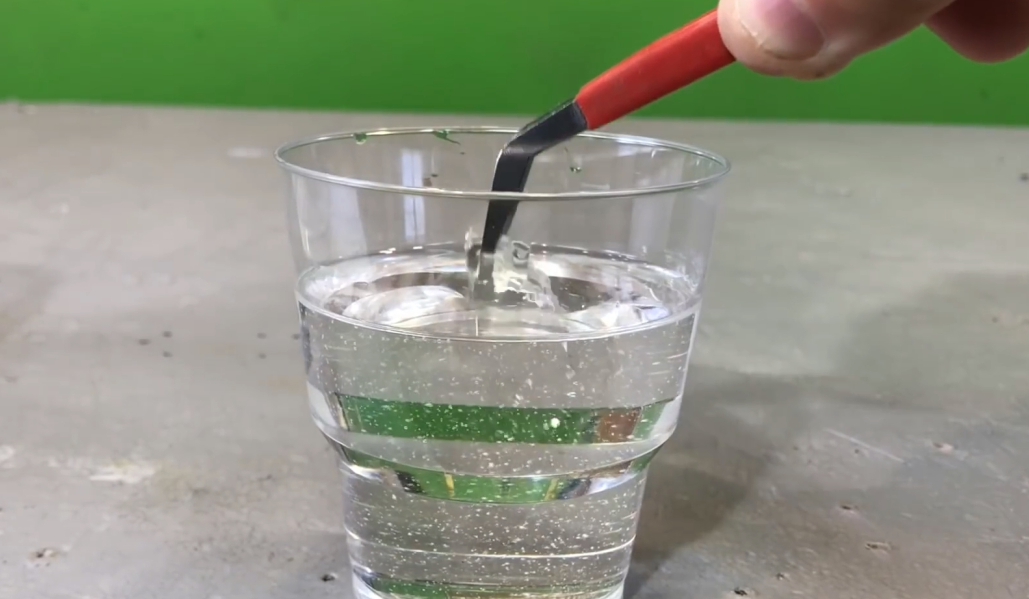
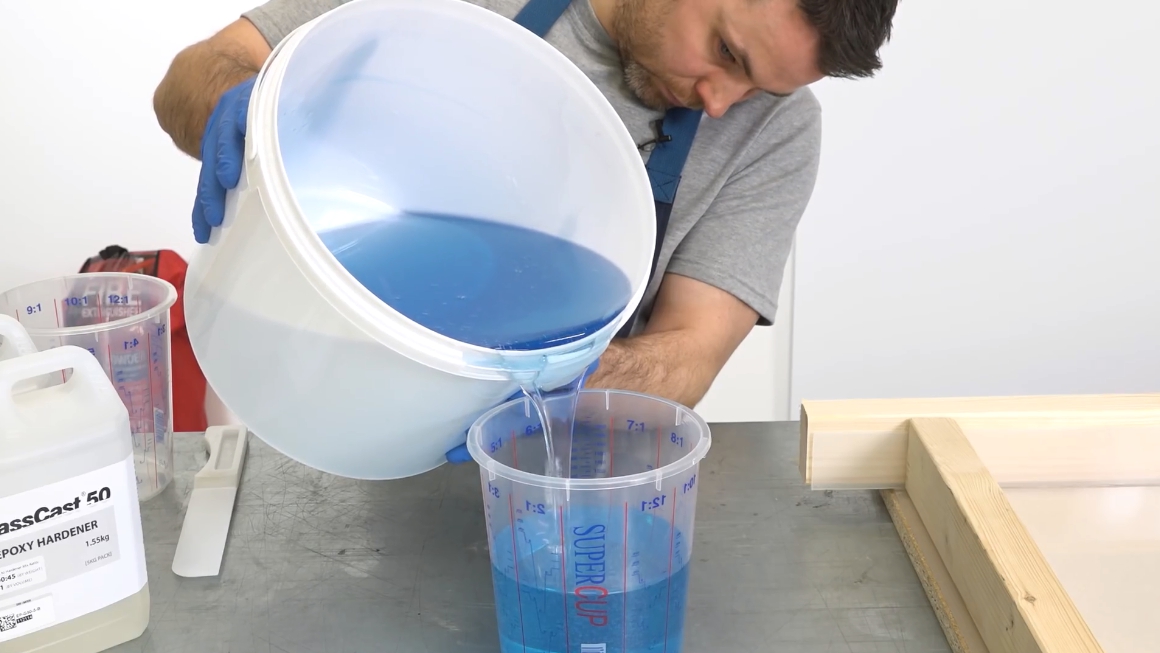
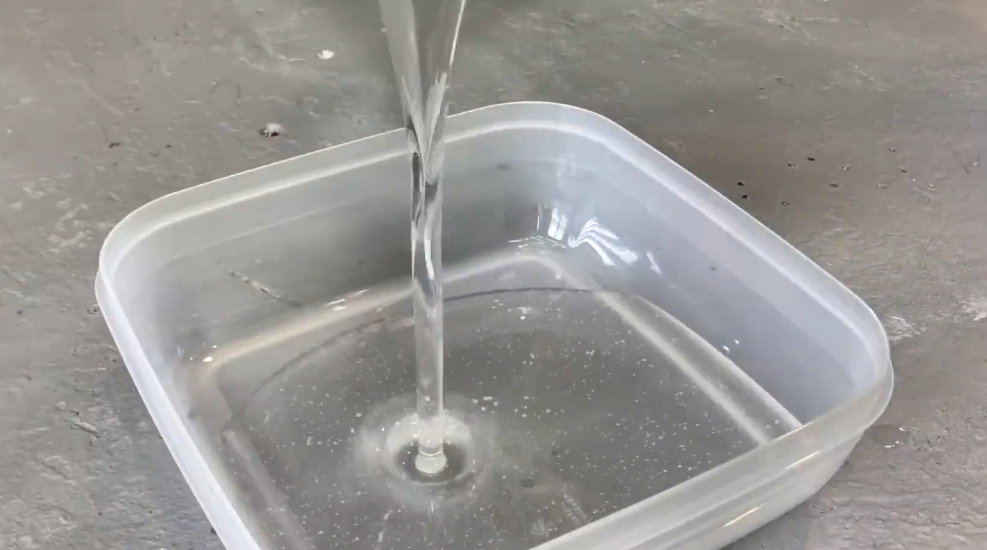
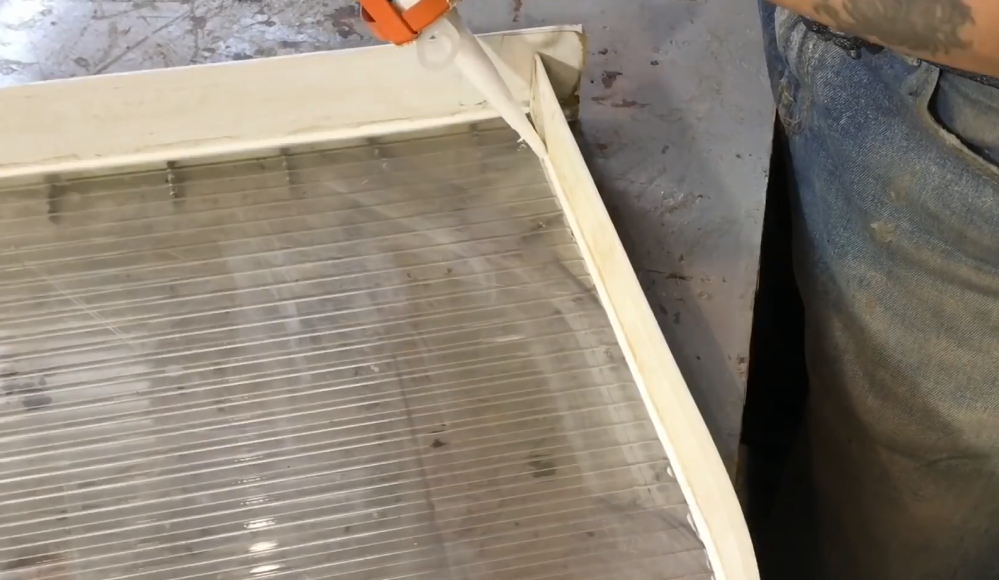
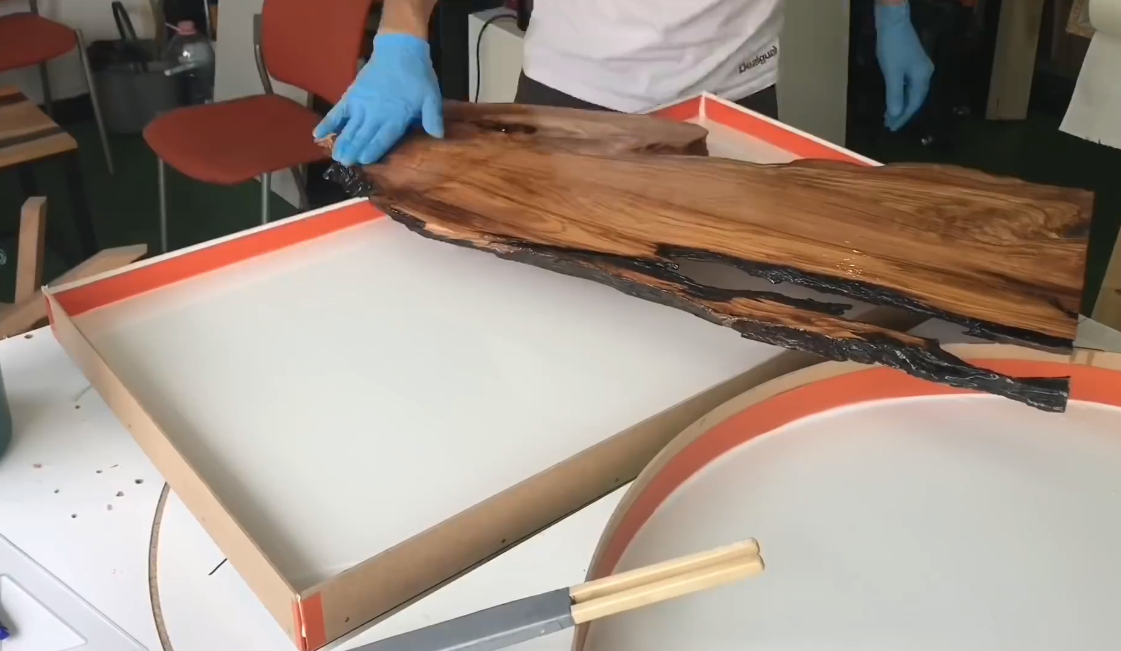
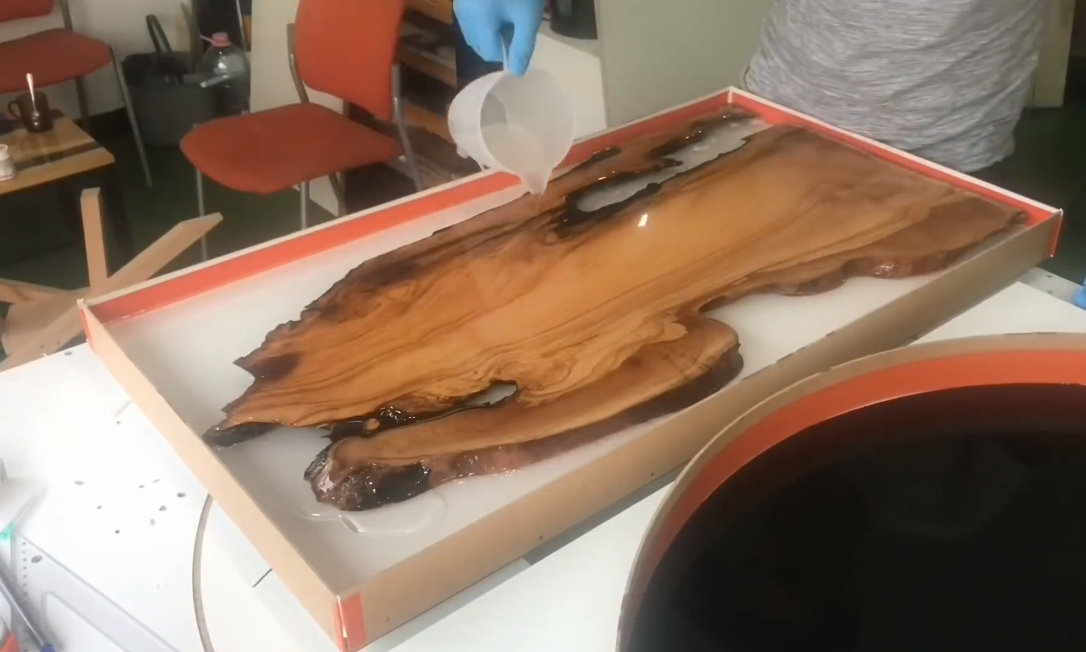
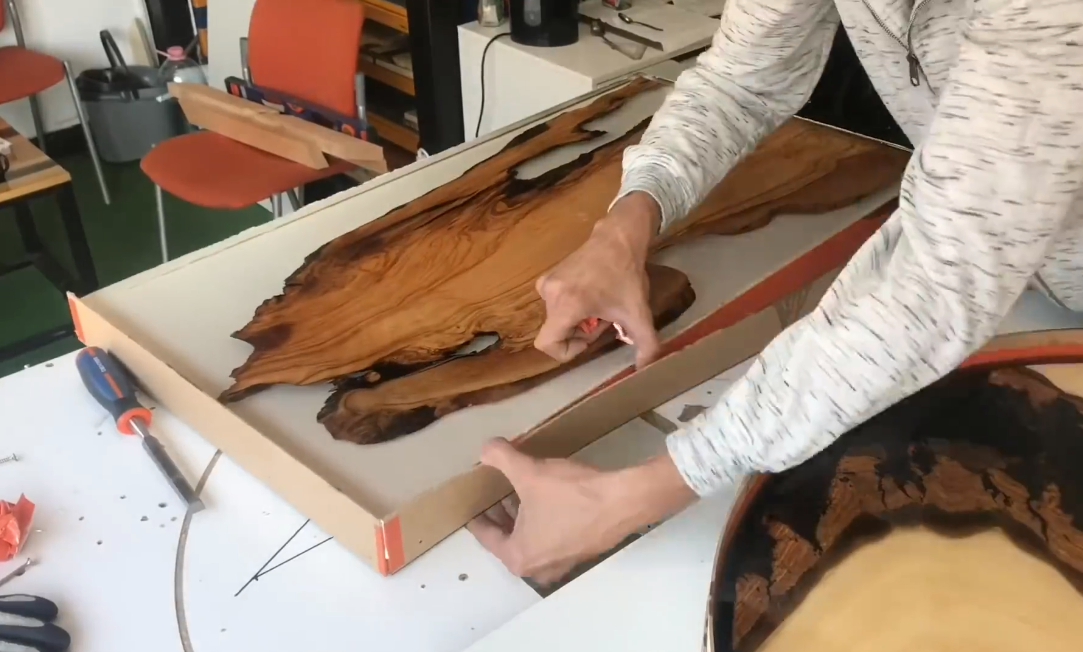
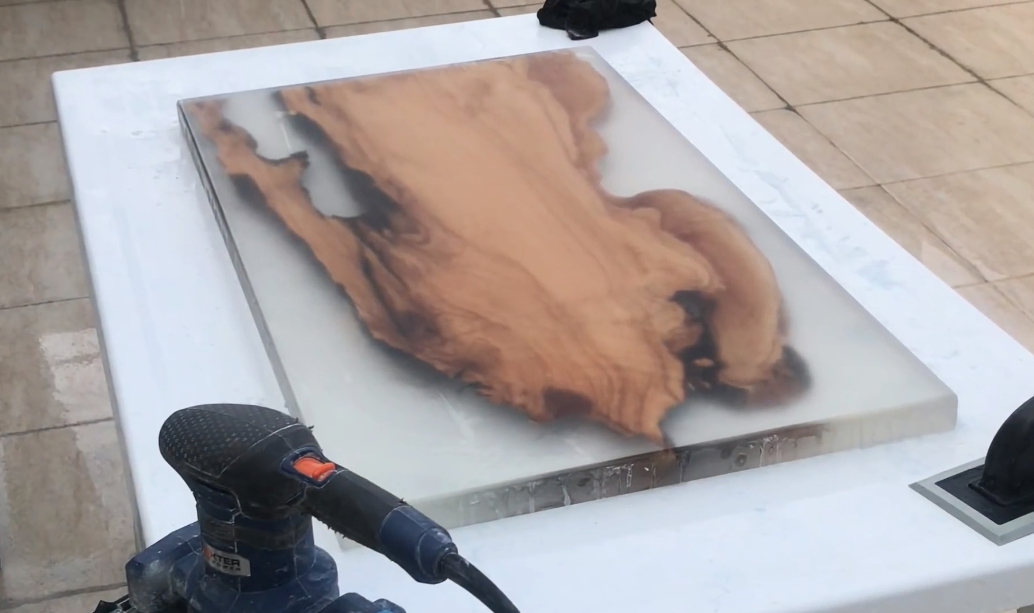
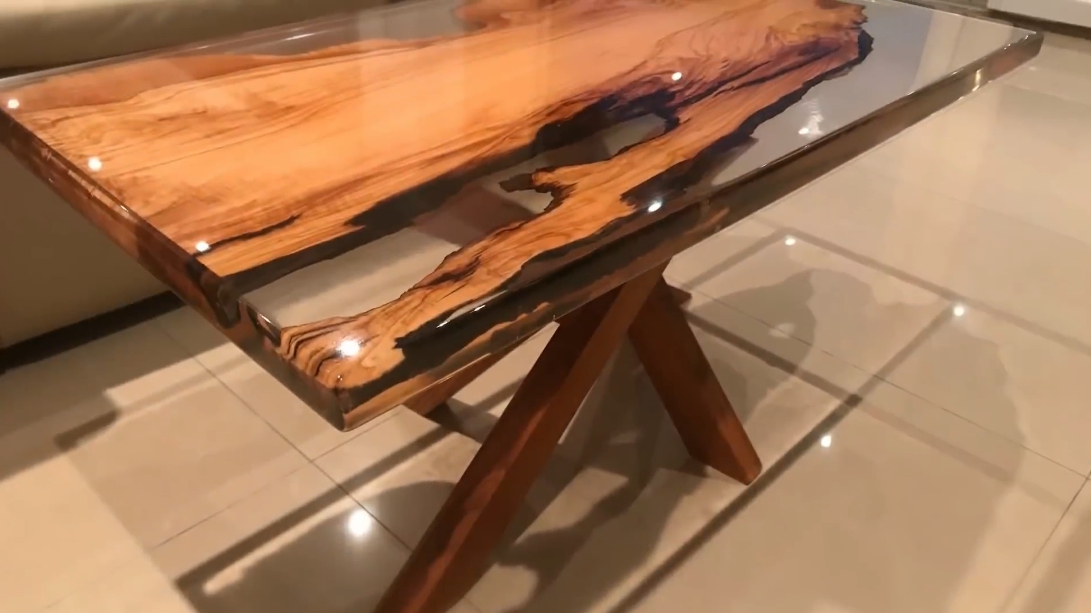
Пошаговый мастер-класс
Теперь можно рассмотреть, как сделать стол из эпоксидной смолы самостоятельно. Каждая модель имеет свои особенности изготовления. Изначально подготавливается инструмент и материал.
Журнальный столик из спила с рекой
Для изготовления лучше использовать дуб или вяз. Мягкие породы не рекомендуются. Мастер-класс по созданию журнального столика:
- Подготовка спила. Он должен быть хорошо отшлифован.
- Изготовление формы. Она должна иметь бортики с герметичными соединениями.
- Выкладывание фрагментов спила. Так как стол изготавливается с рекой, то между частями древесины оставляется ниша заданной формы и ширины.
- Колеровка и заливка смолы.
- Изготовление подстолья.
Конструкцию нужно накрыть полиэтиленом и дать застыть. Через 2-3 часа бортики можно снять. Далее производится финишная отделка изделия.
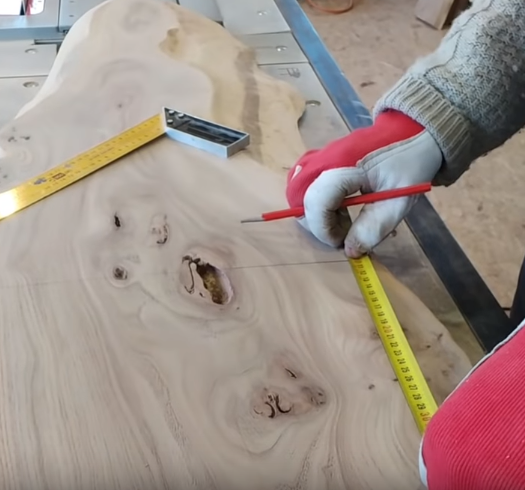
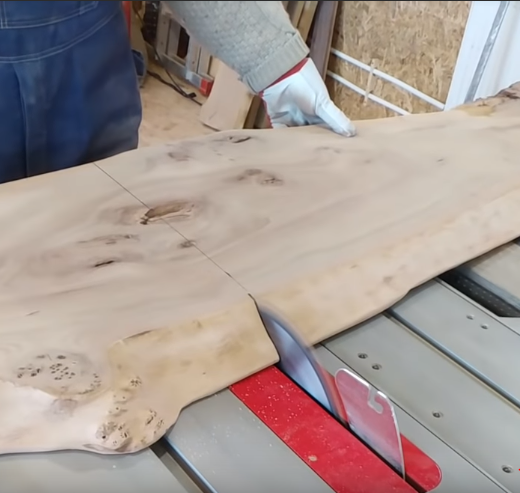
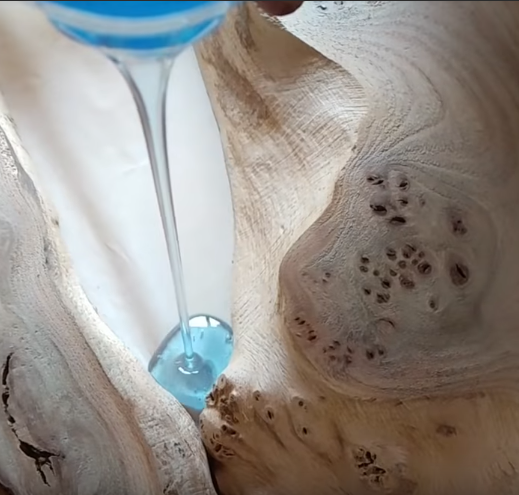
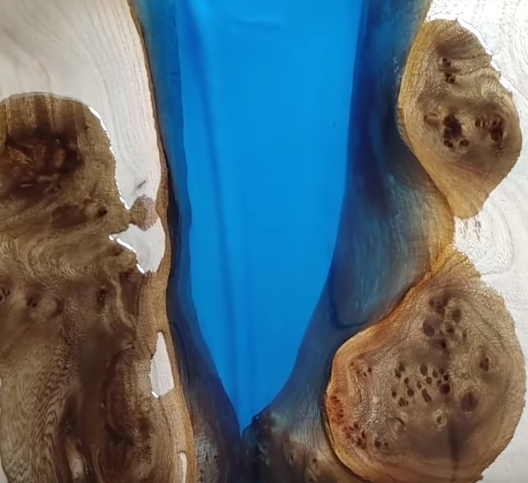
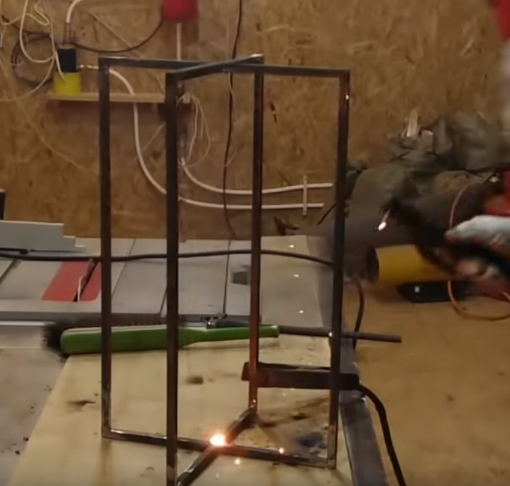
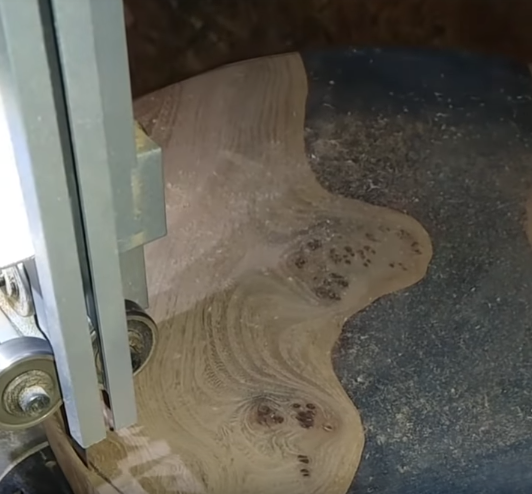
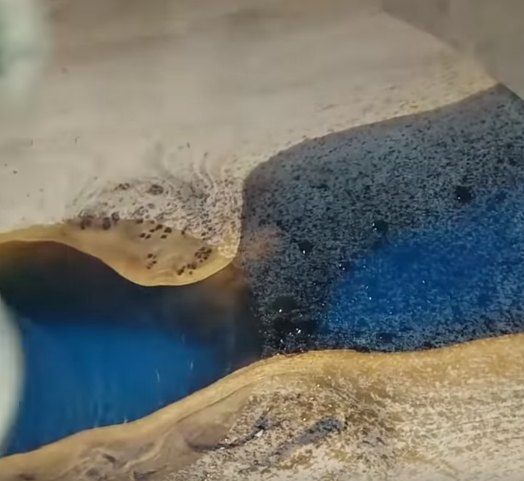
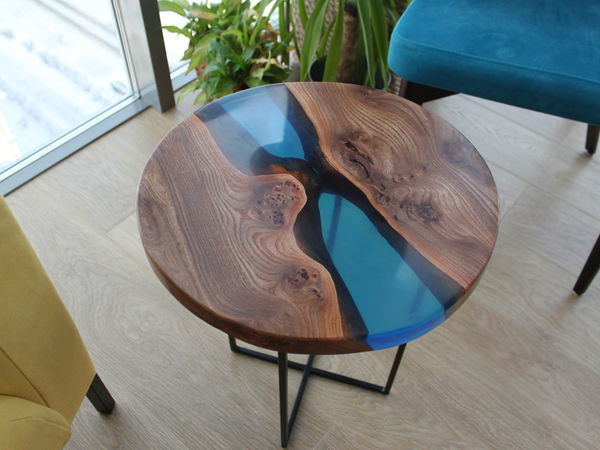
Обеденный из слэба
Тут нужно сделать чертеж с указанием точного размера столешницы. Для такой модели тоже нужно приготовить форму. Работа выполняется пошагово:
- Выбирается подходящий фрагмент древесины.
- Так как изделие делается из слэба дерева, то материал надо очистить от пыли, фрагментов гнили.
- Изготовление формы и укладка материала.
- Приготовление и заливка смолы.
- Производство и фиксация ножек.
Если используется несколько слэбов, то нужно избежать протечки смолы. После застывания излишки эпоксидки надо убрать при помощи шлифовальной машины. В последнюю очередь поверхность покрывается бесцветным лаком.
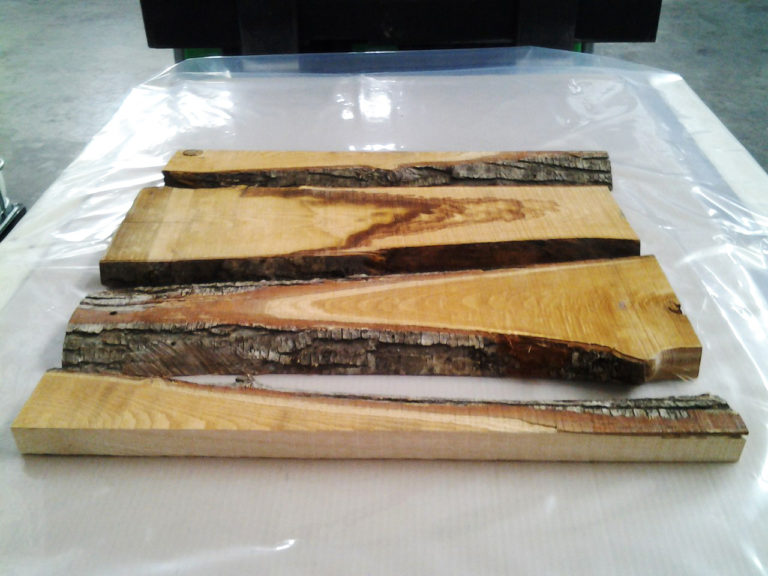
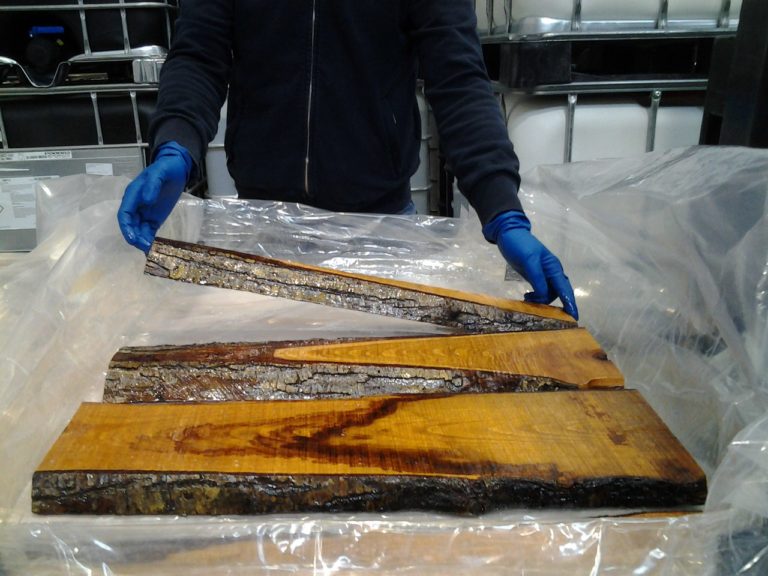
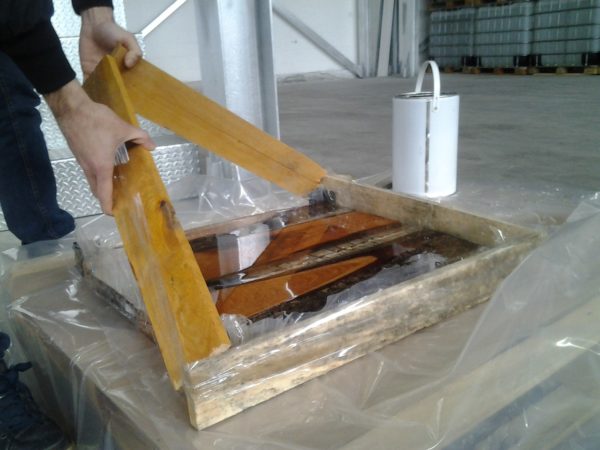
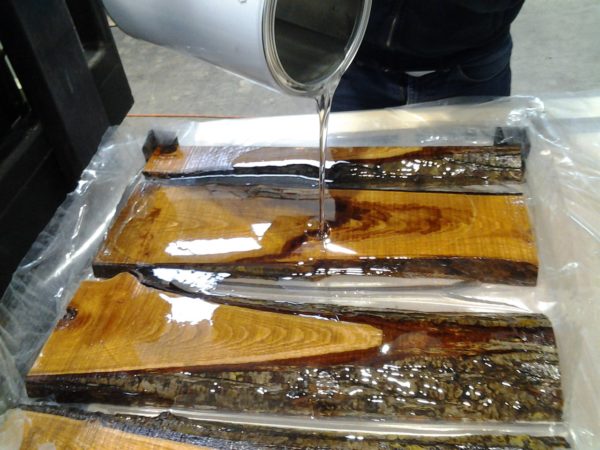
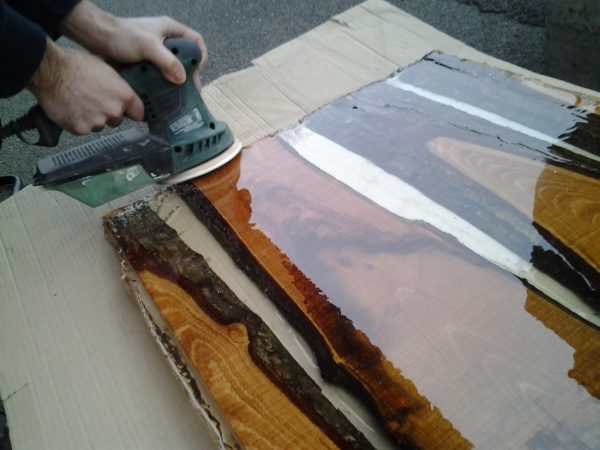
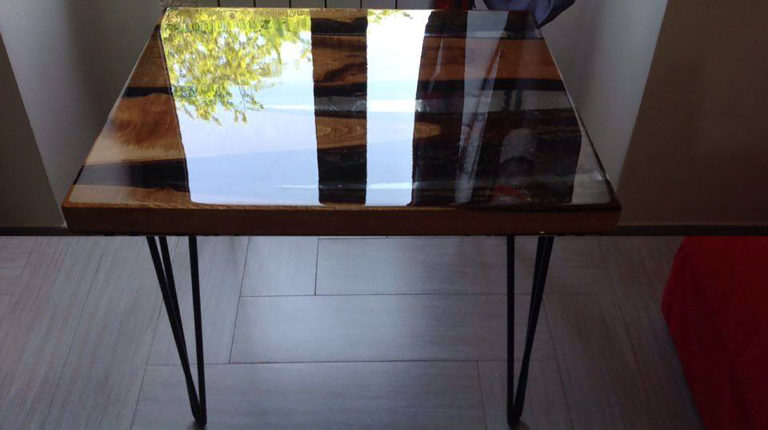
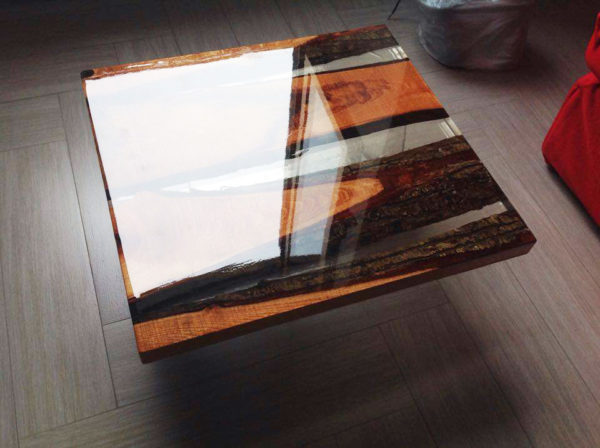
Из массива с добавлением люминесцентной краски
Для работы нужна эпоксидка, светящаяся краска и доска, которая должна быть с трещинами. Потребуется 3 фрагмента заданной длины. Далее производятся такие этапы работ:
- Формирование столешницы. Доски склеиваются между собой и оставляются на ночь для просушки.
- Очистка трещин от пыли и мусора.
- Шлифовка поверхности дерева. Перед заливкой смолы при помощи акриловой пленки и скотча надо защитить боковые и торцовые части массива.
- Подготовка эпоксидки. На этом этапе добавляется фотолюминесцентная краска: на 2 литра смолы используется 100 г красителя.
- Заливка трещин на поверхности дерева. Проц
Как у меня появился раскройный стол! Или модернизация гладильной доски
Ныла-ныла я своим, что акромЯ небольших вещей шить ничего не могу — неудобно, кроме гладильной доски раскрой делать негде (не на кровати же кроить хотя и там бывало, но честно-честно — неудобно. Вон, весеннее пальто второй год недошитое лежит, сарафан на лето в ткани, да в мечтах. Ну, сами понимаете, был весомый повод не шить крупные вещи.
Н-да, мысли материальны, донылась…
Едет вскоре ко мне внук! Погулять на свежем воздухе, с бабушкой да дедушкой пообщаться. Если кто не в курсе — нам второй месяц!
Посему собрались мы делать перестановку в Дочиной комнате, чтобы Максимке создать условия для проживания. В принципе перестановка небольшая, мешал только один из представителей мебели — либо комод, либо складной столовый стол-книжка. Именно кому-то из них предстояла ссылка в другую комнату, чтобы освободить место для детской кроватки. Выбор пал на стол, т.к. комод еще пригодится детские вещички хранить (специально пару ящиков освободили), а вот стол-книжка малышу ни к чему, поэтому и из комнаты вон!
Стол этот используется нами крайне редко, вернее лет 7 уже вообще не используется. Большие компании обычно собираются на даче, а близкие друзья по-домашнему — на кухне за круглым столом. Но стол хороший, крепкий, с металлической начинкой (вечный можно сказать), верхние лопасти я обновила, поэтому выглядит на свой возраст неплохо — выкидывать его не хотелось. А в нашей комнате места в обрез, все что можно уже поставлено на свои места.
Куда же тебя, родимый деть? — задумалась я… Вариант был только один — снять мою помощницу-гладильную доску с металлических ножек и… впихнуть под нее наш стол-книжку. Померяла — идеально по размерам подходит, доска у меня не щупленькая какая, а 40 см в талии ширину и стол также.
Одна беда — по высоте, даже с водруженной на стол гладильной доской, не хватает мне немного высоты конструкции, всего 4 см, но, сами понимаете, для привыкшего человека — катастрофа — это как на невысокую табуреточку приседать после обычного стула — все время ощущение неожиданного падения.
Стала думать, что надо бы что-то подставить… но что? Ножки нужны! Ну конечно, не зря же я хранила стеклянные синие баночки из под крема! Примерила — 4 см! Все срослось!
Тааак, теперь вопрос, как их прикрепить? Ну, с доской я церемониться не стала — приклеила баночки на горячий клей — как родные стали. Со столом посложнее — пачкать клеем столешницу жалко, но закрепить доску для удобства использования надо. Решилась на двухсторонний скотч — оказалось — прекрасно держит!
Разметила, установила — красота!
И тут до меня стало доходить, что, если переднюю крышку стола-книжки открыть, то у меня готовый раскройный стол, прямо на рабочем месте!
Вот так! Не думала, а только мечтала. Получила в результате!
Вывод: мысли материальны — мечтайте и получите!
P.S. Большие вещи шить все равно рановато, потому что у меня пока еще оверлока нет Поэтому поною, помечтаю еще! Проверю закономерность!