Radiotech modding labs: КАРБОЛИТ РЕМОНТ и ВОССТАНОВЛЕНИЕ
Что такое карболит
Карболит, один из видов синтетических феноло-альдегидных смол, получаемый поликонденсацией фенола (крезолов) с формальдегидом в присутствии нефтяных сульфокислот (так называемого контакта Г. С. Петрова). Отечественная промышленность выпускает карболит с 1914.
Вот что нам поведал яндекс словарь.
Далее я собрал немного основной практической информации с радиофорумов ,по восстановлению карболитовых корпусов.ЧЕМ…
Полировка балистолом (ballistol) оружейное масло (можно найти в охотничьих магазинах).Полировка шеллачным лаком или сгущенной шеллачной политурой .
Полировка пастой ГОИ .
КАК…
Полировка карболита и эбонита. Отшлифовать поверхность детали шкуркой,
уменьшая ее зерно. Промазать поверхность растительным маслом,
сушить 4—5 час и протереть поверхность насухо.
Тампоном, пропитанным шеллачным лаком (или сгущенной шеллачной политурой),
протереть поверхность несколько раз до образования плотной блестящей пленки.
Высушить и протереть суконкой.
Политуру наносят плавными непрерывными движениями. Повторный слой наносят через 2-3 мин. после высыхания предыдущего.
За первый сеанс полирования наносят до 50 слоев,
до тех пор пока не появится равномерный блеск.
После первого этапа полирования поверхность выдерживают 2-5 суток.
Только тщательной полировкой, обязательно с применением пасты ГОИ.
Если есть глубокие царапины — зашпаклевать их шпаклёвкой на
основе эп.смолы + карболитовая пудра
(лучше всего взять карболит родной-т.е наскрести где нибудь изнутри корпуса)Ремонт карболитовых корпусов
Разбитый корпус электроизмерительного прибора можно восстановить с помощью эпоксидного клея, добавив в него в качестве наполнителя порошок карболита. Порошок этот можно получить, отпилив кусок карболита напильником. Порошок смешивают с приготовленным эпоксидным клеем в таком соотношении, чтобы получилась тестообразная масса.
Чтобы заделать щель или отверстие в корпусе, нужно подложить и закрепить с противоположной стороны два-три слоя писчей бумаги и заполнить щель (отверстие) приготовленной массой. После отвердения клея излишки его снимают напильником, шлифуют поверхность мелкозернистой шкуркой (смазывая техическим маслом) и полируют на полировальном круге.
Если приготовить порошок из того же материала, что и ремонтируемый корпус, и тщательно выполнить остальные операции, то обнаружить следы бывшей трещины или выбоины почти невозможно.
источник :
Практические советы мастеру-любителю по электротехнике и электронике.
О.Г.Верховцев
К.П.Лютов.
1984г.
Карболитовые изделия в домашних условиях — Про стройку и не только
26 Дек by adminСодержание статьи:
Резка полировка и обработка камня дома, самодельный станок
Перстни с лучистыми самоцветами. Кулоны, серьги, запонки и другие украшения с камнями. Письменные приборы, скульптуры. Колонны и цоколи зданий.
Во всех этих случаях камни прекрасно выполняют роль художественного, скульптурного и строительного материала, служат главной деталью художественно-прикладной композиции.
Красивые камни? А ведь самые обычные, рядовые, не драгоценные.
Красоту свою камень открывает не каждому: самое удивительное он дарит трудолюбивым. А труд это правильно разрезать камень, отшлифовать, отполировать или обработать по задуманной форме. За потраченный на него труд камень подарит картину, хранимую им тысячелетия, оживет и засверкает причудливыми красками и оттенками. И, однажды испытав радость «открытия» камня, увидев в нем удивительное, человек поневоле влюбляется в камень.
Любить камень — одно из замечательных увлечений. Любители камня собирают все минералы, включая рудные породы. Но особым вниманием удостаивают агаты, яшмы, кремни и переходные формы этих минералов. Эти, казалось бы обыденные камни поистине беспредельны в своем многообразии. И месторождений не перечесть. В самой Москве, в Рублеве, много кремней. В Дмитрове — агатовые кремни. В Голутвине, несколько минут езды от Москвы, агаты и кремни. В Ступино — это тоже под Москвой, агаты и хрустальные щетки.
А в целом по стране интересных для любителей камня месторождений не счесть — это и горные районы Урала, и Забайкалье, и Казахстан, и Кавказ, и Карелия, и вся страна.
Но найти камень, это лишь первый этап. За ним следует обработка. Режется камень с помощью так называемых отрезных дисков, которые продаются в магазинах алмазного инструмента.
Отрезные диски, которыми пользуются любители, имеют диаметр от 125 до 200 миллиметров и приводятся во вращение двитателем мощностью 160-200 ватт через ременный привод.
Режется камень при окружной скорости диска от 20 до 30 метров в секунду. Обязательно обильное водяное охлаждение диска с обеих сторон.
Как сделать станок для резки камня в домашних условиях
Для облегчения приводится одна из конструкций такого станка.
А как именно сделать станок для резки камня в домашних условиях, как подвести к нему охлаждение, этот вид творчества предоставляется самому любителю. Смотреть конструкцию станка —
Шлифовка камня для получения плоских пластин может производиться на обычном стекле с помощью абразивных порошков.
Несколько капель воды на стекло и небольшую порцию порошка — и можно начинать. В процессе шлифовки порошок добавляется небольшими порциями по мере износа абразива, а вода добавляется, чтобы поддерживать на стекле сметанообразную массу.
Переходя при шлифовке от крупных фракций порошка к более мелким, стекло шлифуемый камень и руки нужно промывать водой с мылом и щеткой: если в мелкую фракцию порошка попадет хотя бы несколько зерен крупного размера, работа будет испорчена.
После шлифовки камень полируется на механическом войлочном или фетровом круге диаметром от 150 до 200 миллиметров. При полировке нужен порошок окиси хрома и вода. Скорость вращения круга от 400 до 700 оборотов в минуту.
Я рассказал лишь об одном способе обработки камня, а их существует много. Любителям камня можно предложить одну нз рациональных конструкций станка для обработки небольших по размеру камней. Устройство станка понятно из схемы, поэтому мы дадим лишь некоторые рекомендации.

В качестве двигателя лучше использовать имеющиеся в продаже электродвигатели для стиральных машин — однофазные, мощностью от 180 до 230 ватт и развивающие 1400 оборотов в минуту. При таких характеристиках двигателя шкивы могут быть двухступенчатые, с передаточными числами 1:1 и 1:0,35.
Первая передача удобна для обработки камня на планшайбах с закрепленным абразивным материалом, а вторая более быстрая для обработки камня с насыпным абразивом.
Для передачи удобно использовать клиновидный ремень от автомобиля «Запорожец». Резьба крепления планшайбы может быть и правой и левой, лишь бы при работе под нагрузкой планшайба не сворачивалась с оси.
Размер корыта для сбора шлама должен быть примерно вдвое больше диаметра планшайбы, а высота бортов на два сантиметра выше поверхности планшайбы. На боковые стенки корыта можно прикрепить резину, чтобы камень, случайно выскочивший нз рук, не разбился.
Напомню, что вся обработка камня ведется с водой, но капельница на станке используется лишь при работе на планшайбах с закрепленным абразивом. При обработке насыпным абразивом смачивать камень водой лучше всего в отдельной ванночке.
Конечно, к станку следует иметь набор планшайб: чугунные, деревянные, металлические с наклеенным фетром и войлоком. Такой набор необходим для постадийной обработки и полировки.
Юный техник — для умелых рук 1985-04, страница 14
Для снятия повзрхностных налетов можно применить и химическую чистку. Преимущество ее в том, что образцы меньше страдают от царапин, сколов. В домашних условиях для этого используют 5—15-процентный раствор соляной или щавелевой кислоты. Но прежде надо убедиться, что ваши минералы не растворяются в кислоте. Не следует обрабатывать кислотой арагонит, азурит, они растворяются в ней очень быстро. Такио минералы, как бирюза, лазурит, обрабатывают очень осторожно, так как они, хотя и медленно, растворяются в кислоте. Чтобы размягчить органические остатки, которые могут встретиться на поверхностяк образцов, их вымачивают в уксусной кислоте. Жирные соединения удаляют бензином и ацетоном.
Очень эффективны для химической чистки минералов некоторые препараты бытовой химии Например, карбонатные известковые оболочки можно снять с минералов, прокипятив их с «Антина-кипином». Хорошо очищает даже труднодоступные участки поверхности моющее средство «Прогресс». Прозрачные минералы на последнем этапе химической обработки неплохо очищаются средствами для мытья стекла, хрусталя (например, ИПС).
Очень эффективна «химическая баня», если минералы прокипятить под давлением в скороварке. При этом пар проникает в самые недоступные места. После обработки камни тщательно промывают чистой водой.
РАСКАЛЫВАНИЕ И РЕЗКА
Очищенные и отмытые камни надо отсортировать. Некоторые любители собирают только окаменелости или красивые образцы, минералогические редкости. Многие собиратели коллекций подвергают образцы шлифовке и полировке. Это помогает полнее раскрыть красоту камня. Опытные любители находят в камне такие плоскости, разрезав по которым можно увидеть переливы красок, напоминающие пейзажи, а то и портреты.
Красивые, но менее интересные для коллекции камни можно отложить на поделки: мозаики, шкатулки, резные фигурки. Некоторые любители стараются подчеркнуть красоту камня сочетанием с металлом, деревом.
Прежде чем начать работу над поделкой, надо расколоть камень, удалив все лишнее. Для раскалывания (препарирования) крупных образцов следует изготовить специальные приспособления: струбцину с двумя зубцами из закаленного металла или тиски, в которых вмонтированы два уголка с победитовыми зубьями (рис. 7).
Режут камень специальными алмазными кругами или алмазными пилами, имеющимися в продаже. Станок для рэзки, шлифовки можно собрать на база электрического точила или электрического сверлильного устройства ЭЗС-1 (рис. 8). У него два выхода вала, один — оснащенный патроном 6, другой — наждачным кругом или специальной планшайбой, с алмазным покрытием (1). Мощность устройства ЭЗС-1 0,25 кВт, частота вращения 2800 мин,—
Можно применять для обработки камня и другие электродвигатели в диапазоне мощности от 0,25 до 0,5 кВт и частоте вращения от 15С0 до 3000 мин.— Подставкой под станок служит ящик 12 с откидной крышкой. Станок крепится к крышке болтами. Откидная крышка позволяет при некоторых операциях устанавливать станок в наклонное положение.
Со стороны патрона к ящику крепится приставной стол 11. Его высота регулируется, чтобы можно было работать режущими кругами различных диаметров.
На приставном столе установлена направляющая планка 9, выполненная из дюралюминиевого уголка 25X25 мм. Сбоку установлено защитное ограждение 7 режущего круга. По столу и защитному ограждению гроведена серэ-динная черта, которая помогает ориентировать камень при резке.
Для звукоизоляции станка дно ящи-ка-подстазки и опоры приставного стола обиваются резиной или войлоком.
Под приставной стол станка ставят поддон с водой для охлаждения режущего круга. Для уменьшения трения в воду можно добавить мыльный раствор. Второй поддон для воды устанавливают под планшайбой.
При р?зке камень подают вдоль направляющей планки, положение которой регулируют на толщину пластины камня, которую собираются отрезать. Подача камня — навстречу вращению режущего круга. Воду для охлаждения круга можно подавать и с помощью смоченного куска поролона, который держат левой рукой у боковой стороны режущего круга. Правой рукой подают камень.
Крупные камни лучше держать двумя руками, а поролон вместе с камнем прижимать к инструменту. Для устойчивости у камня предварительно срезают край, чтобы получить опорную площадку (рис. 9). А можно установить камень в специально подготовленную картонную коробку, залить цементом и после полного отвердения разрезать камень вместе с цементной подставкой. После резки цемент осторожно удаляют. Диаметр режущего инструмента ограничу,зает размер разрезаемого камня. Чтобы разрезать более крупный камень, его надрезают, как показано на рисунке 10, и в прорезанные пазы забивают три клина из тонких стальных пластин. Камень разбивают, осторожно ударяя г.о клиньям. Таким способом можно резать камни, размер которых немного превышает диаметр режущего инструмента.
Если необходимо разрезать треснувший камень, то его перед резкой проклеивают эпоксидным клеем. Трещины обводят на мокрой поверхности карандашом, так их лучшз видно. Перед проклейкой камень надо просушить, чтобы в трещинах не осталась вода. Для этого его нагревают над электроплиткой, а после охлаждают примерно до 60° С. На горячий камень кисточкой или палочкой наносят вдоль отмеченных трещин эпоксидный клей, так он глубже проникает и быстрее затвердевает. После этой операция камень становится
достаточно прочным, чтобы его можно было без опасений нарезать на тонки* пластины.
ШЛИФОВКА
Поверхность среза необходимо тщательно отшлифовать, чтобы ярче проступила красота камня.
Шлифовку можно выполнять на том же станке, описанном в разделе «Раскалывание и резка». Для удобства крышка подставки станка ставится наклонно под углом около 15 е (рис. 11).
Лучше всего прхменять для шлифовки алмазные планшайбы, но можно использовать и обычные абразивные круги, и так называемые прорезиновые.
Прорезиновые абразивные круги хороши тем, что в них можно делать канавки и шлифовать камни округлой формы. Кроме того, они безопасны в работе. Обычные абразивные круги дают много грязи за счет того, что сами быстро изнашиваются бывают случаи, когда они разлетаются на куски во время работы. Поэтому в целях безопасности поверх них обязательно должен быть надет плотный стальной кожух. В качестве кожуха можно использовать старую алюминиевую миску, у которой удалено дно (рис. 11). Шлифовку начинают на кругах с крупным алмазным или абразивным зерном от 300 до 60 мкм, второй этап шлифовки проводят на кругах с зерном от 60 до 40 мкм и последний этап — на кругах с зерном от 40 до 10 мкм.
При шлифовке обязательно нужна непрерывная подача воды. Можно, как и при резке, пользоваться куском влажного поролона. Но лучше установить над станком бачок с резиновым шлангом и краном, через который вода будет по каплям поступать к планшайбе и затем стекать по другой трубке в поддон, как показано на рисунке 11. Для защиты от разбрызгивания воды служит тот же металлический кожух-миска.
ПОЛИРОВКА
Основными инструментами для этой заключительной операции в обработке камня являются притиры, полировальные круги из войлока и ткани, а также щетки — волосяные или из растительных материалов (например, джута).
Притиры — самый важный инструмент для окончательной доводки поверхности камня. Их изготавливают в виде планшайб и ручные. Материал притира для обработки камня различен. Это могут быть чугун, олово, свинец, древесина, фторопласт, гематит, халцедон.
Сами притиры, как правило, выполняют тонкое шлифование, а для полировки добавляется увлажненная окись хрома или паста ГОИ. Вместо окиси хрома можно использовать зеленую краску под таким же названием, так так окись хрома — ее основной компонент. Полировать ею можно с помощью кожаного тампона. Недостаток окиси хрома и пасты ГОИ в том, что они въедаются в трещины камня и вымываются оттуда с трудом, с помощью бензина. Для полирования применяют также порошки окиси алюминия. Мяг-
Обработка природного камня
Так как большинство камней добывается в виде бесформенной массивной породы, они нуждаются в обработке, которая сделает возможным их дальнейшее применение в той или иной области. Исключение составляют породы, обладающие природной декоративной ценностью (валун, галька, коралл, жемчуг и т.д.). Разнообразная фактурная обработка природного камня придает ему эстетичный вид, помогает выявить и подчеркнуть декоративные свойства, либо скрыть недостатки.
Современные технологии обработки натурального камня
Механизированное камнерезное производство позволяет обрабатывать любые породы и предавать их поверхности после добычи и распиловки необходимую фактуру. Существуют следующие технологии обработки натурального камня для получения нужной фактуры поверхности. С некоторыми из них можно ознакомиться ниже.
Пиленная поверхность — получают путём распила заготовки. Для этого применяются станки с прямолинейным движением пильной рамы, ленточные, канатные и дисковые пилы. Поверхность становится шероховатой с прерывистыми бороздками глубиной до 5 мм.
Поверхности с такой фактурой применяются для мощения площадок, садовых дорожек, облицовки цоколей и стен. К тому же, эти изделия используются в качестве материала для последующей, более тонкой обработки – полировка, шлифовка, лощение.
Шлифованная поверхность – образуется в результате обработки заготовки шлифовальными кругами, на станках портального и мостового типа, шлифовально-полировальных конвейерах и шлифовально-полировальных станках для объемных изделий. Поверхность приобретает равномерную шероховатость, с неровностями рельефа высотой до 0,5 мм. Такая технология применима для светлых пород с невыраженным рисунком. Для темных, особенно с узором пород не подходит, так как значительно скрадывает рисунок и цвет.
Такие изделия применяются для отделки пола, площадок, ступеней лестниц и мест, где необходимо уменьшить скольжение.
Лощеная фактура – достигается при использовании специальных шлифовальных кругов с напылением микро-шлиф-порошков. Поверхность получается гладкой, но не имеет зеркального блеска. Лощение хорошо открывает рисунок, выделяя структуру камня.
Полученные таким образом плиты применяются для облицовки плоскости пола и наружных стен зданий.
Полированная – достигается при последующем шлифовании лощеной поверхности на конвейере кругами с порошковым напылением, а затем войлочными и матерчатыми круги. Особый блеск придает полированному камню применение пасты Гой или азотнокислого олова.
Полировка отлично раскрывает рисунок камня и подчеркивает цвет.
Такой материал применяется для внутренней отделки помещений, производства подоконников, столешниц и других элементов интерьера.
Раковистая – имеет равномерные впадины от 1 до 4 мм глубиной, сто придает камню особый декоративный внешний вид.
С такой фактурой плиты применяются для наружной отделки зданий и при оформлении интерьеров.
Оплавленная – получается в результате применения термической технологии обработки камня на термо-газо-струйном станке. Хорошо проявляет фактуру и цвет, создавая при этом впечатление, что камень слегка оплавлен.
Изделия после термической обработки применяются для отделки фасадов зданий, лестничных ступеней и устройства площадок.
Скалистая фактура поверхности – представляет собой имитацию грубо обработанной породы с наличием впадин и выступов от 50 до 200 мм, расположенных в хаотичном порядке и не прошедших дополнительную обработку. Эффект достигается путем скалывания породы с предварительно ослабленной поверхности.
Материал с такой фактурой для отделки фасадов больших зданий, подчеркивая их значимость и монументальность, а так же, природную связь с окружающим ландшафтом.
Распространенные способы обработки натурального камня
Современные способы обработки натурального камня подразделяют на 2 вида: механические и физико-механические.
К механическим способам относятся наиболее распространенные до настоящего момента такие способы как скалывание, ударное разрушение и резка.
При скалывании достигается: фактура плоской и рельефной скалы , бугристая, характеризующаяся на лицевой поверхности наличием равномерно распределенных впадин и бугров фактура и фактура рельефная, с наличием параллельно расположенных борозд высотой от 0,5 до 3 мм.
Резка – самый распространенный из современных способов обработки камня. Осуществляется методом дисковой, канатной или штрипсовой распиловки.
Штрипсовая распиловка разделяется на распиловку с использование стальной и чугунной дроби и на алмазно-штрипсовую распиловку.
Распиловка дисковая приобретает все более широкое распространение в обработке пород любой твердости и подразделяется на дисковую и алмазно-дисковую распиловку резцами.
Канатная распиловка получила широкое распространение при резке пород различной плотности. Ее развитие идет в 3-х направлениях: канатная с помощью абразива, алмазно-канатная и распиловка канатами, армированными твердосплавными шайбами.
Ударное разрушение камня наиболее широко используется в практике производства тесаных изделий. Чаще всего таким способом изготавливают ступени, основания памятников, устои мостов и другие элементы, где достигается точечная фактура обработки.
Достойное место в промышленности начинает занимать способ ультразвуковой декоративной обработки камня в абразивной среде. Протекает процесс очень медленно, но характеризуется очень высокой точностью.
К физико-механическим способам относится обработка токами высокой частоты и широко применяемый метод обработки камня термореактивными газовыми горелками керосиново-кислородного и бензиново-воздушного типов, который применяется для производства архитектурно-строительных деталей и изготовления монументов из пород высокой прочности.
Способ токов высокой частоты наиболее пригоден для обработки блоков-заготовок в производстве бордюров, парапетов, ступеней и т.д. Этот метод при использовании высокочастотные колебания до 20 МГц считается наиболее точным и перспективным.
Обработка натурального камня в домашних условиях
По степени сложности все камни делят на мягкие и твердые. Камни мягкие легко поддаются обработке тем же инструментом, что и металлические изделия, а твердые камни нуждаются в применении специального инструмента. Обработка камня в домашних условиях требует наличия отдельного помещения оборудованного вытяжной вентиляцией, так как такие работы как резка и шлифовка сопровождаются большим количеством каменной пыли, очень вредной для здоровья.
В домашних условиях для обработки натурального камня можно проводить такие работы как: резка, шлифовка, полировка камня и гравировка. Важно помнить, что резка, шлифовка и полировка камня проводится только с непрерывной подачей воды. Вода охлаждает режущий элемент, удаляет образующийся при работе шлам и значительно снижает уровень каменной пыли.
Резка – грубая осуществляется при помощи обычной болгарки и диска по камню. Более точная потребует применение станка типа пилорама с металлической, желательно подвижной платформой.
Шлифовка – осуществляется при помощи шлифовального станка (ручного или стационарного) или болгарки с соответствующими шлифовальными кругами. Самый простой способ шлифовки, но только для камней размером до 20-25 см длиной: на чугунную плиту нужно насыпать абразивный порошок и залить водой, сверху положить камень и тереть, пока он не приобретет нужную поверхность. Мелкозернистая структура чугуна способствует обработке камня.
Полировка – выполняется с применением специальных полировочных кругов и пасты Гой.
Гравировка – возможна при использовании приспособления для выполнения точных работ, либо при помощи набора резцов по камню и молотка. В этом случае гравировку нужно отполировать, используя электродрель и насадками для полировки.
Источники: http://farmer1.ru/text/sdelay-sam-rezka-obrabotka-kamen, http://zhurnalko.net/=sam/junyj-tehnik-dlja-umelyh-ruk/1985-04—num14, http://www.kamsad.ru/articles/953/
Комментариев пока нет!
Source: www.restart24.ru
Руководство по материалам электротехники для всех. Часть 6 / MakeItLab corporate blog / Habr
Продолжение руководства по материалам электротехники. В этой части продолжаем разбирать диэлектрики полностью синтетические по происхождению. Тоесть всем известные пластики. В этой части: карболит, гетинакс, текстолит.Добро пожаловать под кат (ТРАФИК)
Доступные природные материалы использовались широко, но, с развитием техники становилось всё более очевидным, что природные материалы порой полное дерьмо. Большой разброс свойств, подверженность гниению, трудности в добыче — поэтому поиски искусственных заменителей велись и ведутся всё время. Появление синтетических материалов — это революция не только техническая, но и экономическая, политическая. Вам больше не нужны колонии чтобы покрыть свои потребности в резине. Экипировка вашего солдата стала легче в несколько раз. В этом разделе — материалы, полученные «с нуля», а не попытка улучшить природные, как в предыдущем разделе.
Многие из приведенных материалов являются полимерами — материалами с длинными молекулами, состоящими из простых однотипных кирпичиков — мономеров. Полимеры можно разделить на две большие группы по их поведению при нагреве, это термопласты и реактопласты. Термопласты при нагревании плавятся, реактопласты при нагревании разлагаются.
Соответственно гору старых пластиковых игрушек из термопластов можно переплавить в новое изделие, а гору старых изделий из реактопластов так переработать не выйдет.
Полимер может состоять из чистого мономера, а может также содержать со-полимер, который встраивается в структуру молекулы. Например есть два мономера: А и Б. Молекула полимера из чистого А будет выглядеть так:
…-А-А-А-А-А-А-А-А-А-А-А-…
Молекула полимера из сополимеров А и Б может выглядеть так:
…-А-Б-А-Б-А-Б-А-Б-А-Б-А-Б-…
Или даже так:
…-А-А-Б-Б-А-Б-Б-Б-А-А-Б-Б-…
Введение сополимера позволяет изменить свойства пластмассы. Пример — полистирол и АБС пластик. Полистирол прозрачный хрупкий пластик, введение сополимера акрилонитрила и введение добавки из полибутадиена дает на выходе ударопрочный пластик.
Иногда, может дополнительно указываться стереорегулярность полимера. Допустим у нас есть мономер -Г-, который может вставать в цепочку полимера «вверх ногами» -L-. Полимер, в цепочке которого мономеры стоят как попало называется атактическим:
…-L-Г-Г-L-Г-L-L-L-Г-Г-L-Г-…
Если в полимере все несимментричные звенья смотрят в одну сторону, такой полимер называется изотактическим:
…-L-L-L-L-L-L-L-L-L-L-L-L-…
Если в полимере они чередуются, то такой полимер называется синдиотактическим:
…-L-Г-L-Г-L-Г-L-Г-L-Г-L-Г-…
Обычно, стереорегулярность влияет на важные для электроники свойства материала незначительно, поэтому не указывается.
Общие свойства полимеров
Полимеры, благодаря своей структуре из длинных молекул, обладают некоторыми общими
свойствами, которые стоит рассмотреть внимательнее.
1. Полимеры не имеют четкой температуры фазового перехода, как например металлы. Они словно карамель, с ростом температуры размягчаются, превращаясь в вязкую жидкость. Поэтому для полимеров «температура плавления» — это температура, при которой вязкость полимера уже позволяет ему течь, но это не означает, что до этой температуры он твёрдый.
Температура стеклования — это температура, ниже которой полимер из высокоэластичного состояния переходит в стеклообразное состояние, с ростом твердости и хрупкости. Представьте себе жевательный мармелад — при комнатной температуре он находится в высокоэластичном состоянии. Если его охладить ниже температуры стеклования в морозильной камере, то мармелад можно будет разбить, и осколки будут как от стекла.
Максимальная рабочая температура — температура при которой полимер может работать длительное время, без существенных изменений своих свойств. Часто с ростом температуры растет ползучесть полимера, поэтому при максимальной рабочей температуре прочностные свойства снижаются.
Указанные температуры могут отличаться при определении даже для одного и того же образца, при различии методик определения.
2. Полимеры подвежены старению и разрушению. Факторами, ускоряющими процесс старения полимера являются радиация, ультрафиолетовое излучение, высокая температура, агрессивная среда. Разные полимеры в разной степени подвержены старению, кроме того, различными добавками можно снизить скорость разрушения полимера. Так, нейлоновая стяжка на силиконовом шланге с горячей водой за пару лет потеряет эластичность и станет хрупкой, в то время как силиконовый шланг по прежнему будет мягким и гибким.
Лишь очень малое количество пластиков терпят длительный нагрев свыше 100°С — фторопласт-4, каптон, peek, силиконы. Во всех остальных случаях чем выше температура эксплуатации — тем быстрее протекают процессы старения и деструкции в полимере.
3. Полимеры проницаемы для газов и некоторых растворителей. Молекулы газа очень маленькие (чем меньше атомная масса, тем меньше размер атома, самый мерзкий в этом плане водород, он даже сквозь металлы протискивается.) поэтому могут постепенно проникать сквозь разветвленную молекулярную сеть пластика. Для предотвращения этого процесса поверхность полимера покрывают слоем металла. Обратите на это внимание при вскрытии упаковки продуктов питания. Металлизация в упаковке служит этой цели — не пропустить к продукту кислород. Металлопластиковые трубы содержат слой алюминия с той же целью — не допустить проникновение кислорода в теплоноситель, это вызывает коррозию.
Материалы на базе фенолформальдегидных смол
Фенол-формальдегидные смолы, как нетрудно понять из названия — продукт поликонденсации фенола и формальдегида. Молекулы полимера образуют разветвленную трехмерную структуру, что обуславливает механические свойства — твёрдость.
Ниже рассмотрим только фенол-формальдегидные пластмассы — фенопласты. Карбамид-формальдегидные, меламин-формальдегидные пластмассы — аминопласты, рассматривать не будем, их базовые свойства идентичны, методы обработки одинаковые, разница лишь в прочности, цвете.
Химическая структура бакелита (кусочек для примера) Полимеры с такой разветвленной беспорядочной структурой обычно твёрдые и хрупкие. Автор рисунка — Dirk Hünniger, взято из Википедии
Открыл процесс поликонденсации Лео Бакеланд — американский химик бельгийского
происхождения. Он и назвал новый материал, полученный при отверждении смолы — бакелитом.
В СССР аналогичный материал назывался «карболит» — от карболовой кислоты,
старого названия фенола.
Примеры использования фенолформальдегидных смол:
- Как самостоятельный материал в чистом виде в качестве клеев, лаков.
- С порошковыми наполнителями (придающими прочность или разбавляющими материал
- просто для экономии) и без — карболит/бакелит
- С наполнением из стекловолокна в хаотичном порядке — волокниты, например прессматериал АГ-4В
- С наполнением из слоев хлопчатобумажной ткани — Текстолиты
- С наполнением из стеклоткани — Стеклотекстолиты
- С наполнением из слоев проклееной бумаги — Гетинакс
Карболит (бакелит)
Представляет собой твёрдый термостойкий пластик. Если вы возьмете какое-либо устройство,
собранное до 1950 года, то практически все пластиковые детали в нем — это карболит.
Различные изделия из карболита — коробочка, розетка. Вилка, корпус вольтметра, гнезда, ручки регулировки.
Изделия получают как заливкой в формы, так и (чаще) прессованием порошка смолы с наполнителем в металлические формы с нагревом. При нагревании процесс полимеризации, уже частично начавшейся при производстве порошка, заканчивается, но, так как порошок в этот момент зажат под давлением в форме — то и вид конечного изделия повторяет форму. Серьезный недостаток такого метода в том, что нужно время, которое должно провести изделие в форме, чтобы набрать прочность, достаточную для раскрытия формы без разрушения, поэтому во многих задачах бакелит вытеснен термопластичными материалами, термопластавтомат может производить изделия заданной формы значительно быстрее.
Немного о процессе расскажет это американское рекламное видео прошлого века, оцените энтузиазм, с которым говорят о новом материале.
Корпус электросчетчика сделан из карболита.
На сегодняшний день изделия из карболита производятся массово, но он уже не так популярен как раньше, хотя есть задачи, где его заменить чем-либо трудно.
Плюшки
Термостойкий пластик. Может длительное время работать при температуре до +150°С Является реактопластом — не плавится, а разрушается от нагрева. Так карболитовый патрон для лампы накаливания при перегреве рассыпется, а не стечет к вам на голову.
Стойкий к растворителям, ГСМ (Горюче-смазочным материалам). Карболитовые детали без труда работают вблизи двигателя автомобиля, в условиях нагрева, контакта с маслом, бензином.
Твёрдый. Обычно карболитовые детали можно распознать по блестящей поверхности и по твёрдости, ноготь такой пластик не царапает и даже не цепляется. Большие плоские детали почти не гнутся, а при превышении усилия со звуком «хрум» ломаются.
Хорошо обрабатывается. В отличии от многих других пластиков хорошо шлифуется. Если попробовать шлифовать, например, полипропилен, то быстро от нагрева начнет образовываться «борода» из пластика. Карболит же отлично шлифуется и часто можно видеть следы шлифовки по периметру детали — удаление облоя.
Отличный внешний вид. Способность образовывать твёрдую глянцевую поверхность особенно заметна на внешнем виде ретроаппаратуры. Даже в магазине на полке ручки для резисторов из карболита смотрятся солиднее таких же, но из термопластиков.
Недостатки
Дороговизна. Особенность производства в виде прессовки из порошка определяет довольно высокую себестоимость изделий из-за низкой скорости процесса и наличия ручного труда. Изготовление деталей из термопластиков порой в разы дешевле.
Хрупкость. Оборотная сторона твёрдости, при ударах трескается, из него не сделать
гибкий шланг, сильфон и т.д.
Практически не подлежит вторичной переработке. Есть способы, но они не получили
широкого распространения.
Ограниченная цветовая гамма. Фенолформальдегидная смола сама по себе коричневого цвета, что затрудняет получение изделий светлых цветов. Этого недостатка лишены, например, меламинформальдегидные смолы из которых делают изделия белого цвета. Замечательный фильм 40х годов, в котором видно производство фенолформальдегидной смолы, формовка деталей прессованием, получение гетинакса, текстолита, галалита и многое другое.
Гетинакс
Гетинакс — это слоистый пластик, получаемый путем прессования бумаги, пропитанной
фенольной или эпоксидной смолой. В англоязычной литературе имеет название FR-2. (от FR — Flame Resistant — огнестойкий) (FR-1, FR-2, FR-3 это всё гетинаксы, разница только в материале связующего) У нас есть ГОСТ 2718-74 на гетинакс. Имеет низкую прочность, но при этом достаточно низкую цену. Является электроизоляционным материалом, изделия из гетинакса можно получать штамповкой, поэтому панели с ламелями, вставки, изоляционные шайбы, держатели контактов иногда изготавливают из гетинакса.
Примеры применения
Материал дешевых односторонних печатных плат. В задачах, где не требуется высокая надежность и есть возможность обойтись одним проводящим слоем, печатные платы изготавливают из гетинакса. В дешевых электронных китайских игрушках чаще всего гетинаксовые платы. Гетинакс недостаточно прочен для создания надежных переходных отверстий, поэтому двухсторонние и многослойные печатные платы из гетинакса не изготавливаются.
Различные изделия из гетинакса. Пластина специально была сломана, чтобы показать характерный рисунок на изломе. Гетинаксовый брусок слегка распух справа — результат расщепления слоев при резке.
Ламинированный гетинакс (слопласт, слоистый пластик) — гетинакс с наклеенной декоративной пленкой — материал внутренней отделки автобусов, вагонов поезда, столешниц. Прочный износостойкий трудногорючий материал.
Ламели подключения обмоток трансформатора сделаны из гетинакса, изолирующая ламели от сердечника подкладка, боковины оправки обмотки — гетинакс.
Примечание
Материал непрочный и склонен давать трещины при обработке, требуется особая осторожность при обработке резанием пилами с большим зубом. В силу низкой прочности мало пригоден в качестве конструкционного материала.
Источники
Продается многими компаниями, специализирующимися на электротехнических материалов.
Гуглить по «Гетинакс ГОСТ2718-74».
Текстолит
Текстолиты — это целый класс композиционных материалов, состоят из прессованной ткани со связующим. Например, хлопчатобумажная ткань пропитанная фенолформальдегидной смолой. Имеет характерный вид — на плоскостях и срезах видно плетение ткани. Обычно коричневого и темно-коричневого цвета. Зарубежом известны под торговыми марками Novotext, Turbax, Resitex, Cerolon, Textolit, Micarta. Материал известен с 30х годов 20 века.
Текстолит различных форм — пластины, прутки. Расположение ткани в материале различается — у прутков ткань намотана, а не уложена слоями.
Примеры применения
Как конструкционный материал. Текстолит прочен и не проводит ток, поэтому используется как материал прокладок, шайб, перегородок, вставок, шестерен и т.д. При нагревании он не ползет, это выгодно отличает его от термопластичных материалов.
Поделочный материал. Из текстолита часто изготавливают рукоятки ножей, приспособления и оснастку в условиях небольших мастерских. Текстолит хорошо обрабатывается, при этом не впитывает воду, стоек к воздействию горюче-смазочных материалов.
В зависимости от использованной в производстве ткани, наблюдаемая текстура может различаться.
Текстолит из тканей с разным шагом плетения. Текстолит всегда можно узнать по характерной текстуре и виду.
Материал доступен в продаже в России, но постепенно вытесняется другими материалами.
Ссылки на части руководства:
1: Проводники: Серебро, Медь, Алюминий.
2: Проводники: Железо, Золото, Никель, Вольфрам, Ртуть.
3: Проводники: Углерод, нихромы, термостабильные сплавы, припои, прозрачные проводники.
4: Неорганические диэлектрики: Фарфор, стекло, слюда, керамики, асбест, элегаз и вода.
5: Органические полусинтетические диэлектрики: Бумага, щелк, парафин, масло и дерево.
6: Синтетические диэлектрики на базе фенолформальдегидных смол: карболит (бакелит), гетинакс, текстолит.
7: Диэлектрики: Стеклотекстолит (FR-4), лакоткань, резина и эбонит.
8: Пластики: полиэтилен, полипропилен и полистирол.
9: Пластики: политетрафторэтилен, поливинилхлорид, полиэтилентерефталат и силиконы.
10: Пластики: полиамиды, полиимиды, полиметилметакрилат и поликарбонат. История использования пластиков.
11: Изоляционные ленты и трубки.
12: Финальная
Славный пластик «бакелит»! У него отменный вид! Или возвращение бакелитового болванчика
Помню, что в далеком детстве я пришла в гости к бабушке. У нее на комоде стояли два китайских болванчика. Они качали головами из стороны в сторону, если их немного стронуть с места. Волшебный вид куколок сразил меня наповал. Я выпросила одну из фигурок и принесла ее домой. Но недолго длилась моя детская радость. Болванчик упал с полки и у его головы откололся грузик. Так закончилось волшебство, ведь куколка была испорчена. Скорее всего ее выбросили, чтобы меня – ребенка не расстраивать. Прошло много лет, и недавно в антикварной лавке я встретила точно такого же болванчика родом из 50-х. Сделан он из интересного пластика под названием «бакелит».Путешествуя по просторам Интернета, я очень много узнала об этом удивительном материале.
Бакелит – материал, представляющий собой первый вид пластмассы. По сути, это сильновулканизированный каучук. Формальдегидные смолы конденсируют с фенолами в присутствии щелочи. Получается сырье, цветовой диапазон которого от светло-желтого до черного.
Ножи:
Машинка игрушечная:
Изделия из бакелита могут напоминать и слоновую кость, и янтарь, и эбонит. Бакелит с легкостью имитирует текстуру камня. То, что на первый взгляд, нефрит, яшма, или малахит, на поверку, может оказаться пластиком.
Гномики:
«Курочки клюют» — игрушка:
В 1863-ем году в бельгийском городке Гент родился Лео Бакеланд.
Мальчик вырос химиком и переехал жить в Нью-Йорк. Ученому было суждено изобрести фотобумагу. Но, именем Лео назвали его второе изобретение – бакелит. Из него, к примеру, в советские времена делали патроны для ламп накаливания, телефонные аппараты, шары на рукояти передач в старых авто, пуговицы. Но, сегодня не о прошлом, а о настоящем материала, его характеристиках и сферах применения.
Кувшины:
Материал – не просто пластик, а сверхпрочный и негорючий пластик. К тому же, он легкий и не растворяется в спирте. Устойчиво сырье и к едким химическим реагентам. Побеждают покрытие «бакелит» только серная и азотная кислоты, и то, в концентрированном виде.
Игрушка Божья коровка:
Формочка «Желуди»:
Мишка игрушечный:
Бакелит нашел применение в ювелирном деле. Сама Коко Шанель предлагала клиенткам своего бренда украшение из нерастворимого пластика. Дизайнеров привлекала неограниченная цветовая гамма материала. Стоит добавить в базовую смесь нужный пигмент, и получается зеленый, коричневый, красный, оранжевый или синий тон. Нравилась ювелирам и легкость сырья. Бакелит купить было так же просто, как и носить. Серьги не оттягивали уши, бусы не давили на шею. Из пластика и сегодня делают броши, браслеты, кольца.
Шанель была не единственной пропагандисткой материала среди людей высшего света. Энди Уорхол тоже любил бакелит. Ручка, статуэтки, броши, — в коллекции дизайнера были сотни предметов из негорючего пластика. Были, потому что в 1988-ом на аукционе «Сотбис» подборку мастера продали неизвестному покупателю за миллионы долларов.
Телефон, настольные приборы, сувениры:
Игрушечный телефон:
Кот в сапогах:
Украшениям из бакелита даже посвящена книга. Издание «The Bakelite Jewelry Book» написано Corinne Davidov. Правда, в 21-ом веке жидкий бакелит, или твердый приобрести проблематично. Точнее, проблематично приобрести первоначальный материал. Формула изменена. Из нее убрана часть формальдегидов и ядовитых веществ. Лео Бакеланд выпустил первую партию еще в 1909-ом.
Игра «Пятнашки»:
Настольная игра:
Ксилофон:
Тогда вред некоторых компонентов смеси не был доказан. Но, перед некоторыми современными мастерами стоит задача создать изделия, которые можно выдать за винтажные. Поэтому, в ход идут старые радиоаппараты, телефоны, те самые плафоны от лампочек. Вот мы и подошли ко второй сфере применения первого пластика, к промышленной.
Игрушка «Зайчик с коляской»:
Шахматы:
У многих в хозяйстве найдется сковорода из бакелита, точнее, с ручкой из него. В таких посудинах даже запекают пищу в духовке. Правда, при длительном воздействии высоких температур материал может обуглится, но плавится не будет и форму не поменяет. В домах россиян можно найти и настольные игры, фигуры в которых их огнеупорного пластика – шахматы, домино и шашки.
Электровилки:
В свойства бакелита входит отличная теплопроводность. Поэтому, пластик и стал плафонами для ламп, выключателями, вилками и розетками.
Заготовки разноцветные:
Шар желтый:
Над первыми слухами, что бакелит вреден посмеивались музыканты и любители искусства. Дело в том, что пластик шел на клавиши для фортепиано и прочие инструменты, а так же, на грампластинки. Поверить в то, что предметы наслаждения для слуха и души отравляют, люди искусства не могли и продолжали покупать бакелит. Вреден ли он, ученые спорят до сих пор.
В процессе производства выделяются пары формальдегидов. У рабочих фабрик случаются кожные экземы, раздражения. Но, готовый материал уже «не выбрасывает» во внешнюю среду ядовитые вещества. Поэтому, носить украшения из бакелита и давить на тормоза из него, безопасно для здоровья.
Браслеты из бакелита:
Брошь «Красная лошадка»:
Кошки:
Сейчас созданы десятки современных аналогов бакелита. Но, интересно, что аналоги были и во времена изысканий Лео Бакеланда. Одновременно с бельгийским химиком в России трудился некто Тарасов. Он создал карболит.
Так же назвали завод в Московской области, который открыли для производства нового материала в 1915-ом году. Правда, у отечественного сырья угол диэлектрических потерь при нагреве был больше, чем у бакелита. В остальном, пластик американский и русский почти «близнецы».
Брошь «Зонтик»:
Лошадка:
Собачка:
Камея:
Брошь «Скотч-терьеры»:
Брошь «Рог изобилия»:
Брошь «Ключ от сердца»:
Украшение «Попробуй — догони»:
Брошь «Смородина»:
Брошь «Красивый профиль»:
Брошь «Собачка с вишнями»:
Фламинго:
Брошь «Рука с веером»:
Винтажная брошь:
Брошь «Слон»:
Браслеты:
Бусы из бакелита:
Разные изделия из бакелита:
Забавные сувениры:
В завершение своего топика, я хочу добавить, что в антикварной лавке мною был куплен тот самый болванчик из моего детства.
Но недолго суждено было ему коротать свой век в одиночестве.
Скоро у него появился близнец.
Так выглядят эти куколки в разобранном виде:
У них есть подружка из тех далеких лет. У куклы голова сделана из колкого пластика, похожего на тортулон.
Мои милые девочки передают всем Вам, дорогие форумчане, свой «бакелитовый» привет!
Производство арболита своими руками: состав, пропорции, оборудование
Арболит (он же деревобетон) все чаще используется в малоэтажном строительстве. Во многом это связано с простотой производственной технологии и доступностью исходных компонентов. Именно о технологии, оборудовании и способах производства я расскажу в этой статье.
Производственное оборудование
Оборудование для производства арболита не отличается особой сложностью и габаритами. Его можно разместить на приусадебном или дачном участке, в любом боксе, цеху или просто на улице под навесом. Главное условие – наличие электроэнергии и удобство эксплуатации. Полный перечень заводского оборудования, необходимого для промышленного производства арбоблоков выглядит следующим образом:
- Шредер – измельчитель органических наполнителей (щепы, соломы и т.д.).
- Ёмкость для приготовления и розлива химических компонентов.
- Дозатор цемента.
- Дозатор органических наполнителей.
- Дозатор заполнителей для бетонного раствора.
- Бетоносмеситель для арболита принудительного типа действия.
- Подъёмно-поворотный бункер для приёма и дальнейшего розлива готового арболитового раствора.
- Система лебёдок для погрузочно-разгрузочных работ.
- Самозапечатываемые формы для отливки блоков.
- Вибропресс для арболита.
При кустарном производстве деревобетона, для собственных нужд, могут использоваться самодельные станки.
Состав арболита
Состав арболита регламентируется ГОСТ №19-222-84. Готовая к заливке арболитовая смесь состоит из следующих компонентов:
- Цементный раствор;
- Химические добавки;
- Органические наполнители.
Цемент
В качестве связующего компонента в производстве используется раствор на цементной основе. По ГОСТу, портландцемент для приготовления арболита должен иметь марку не ниже М-400.
Таблица . Технические характеристики цемента М-400
Добавлять песок в состав арболитного раствора не рекомендуется, так как это ухудшает показатели сцепки органических наполнителей с цементным вяжущим веществом. В результате блоки становятся менее прочными и склонными к расслоению и растрескиванию.
Химические добавки
Химические добавки предназначены для улучшения эксплуатационных характеристик арболита. В состав арболита входят следующие химические компоненты:
- Сернокислый алюминий, он же сульфат алюминия – неорганическая соль, хорошо растворимая в воде. При изготовлении арболита он используется в качестве гидроизолятора, увеличивающего стойкость материала к воздействию сырости.
Из-за высокой гигроскопичности, хранение сернокислого алюминия должно производиться в помещениях с низким уровнем влажности и в герметичной упаковке.
- Хлористый кальций – химический элемент, получаемый при промышленном производстве соды. Добавляется в арболитную смесь для связывания сахаров, содержащихся в органических заполнителях, что значительно повышает прочностные характеристики получаемого цементного раствора и позволяет повысить степень его сцепления с древесными компонентами.
- Жидкое стекло – водорастворённые силикаты натрия или калия. При изготовлении смеси для деревобетона, жидкое стекло выполняет роль отвердителя, а также для придания цементному раствору кислотоупорных и гидроупорных свойств.
- Гашёная известь добавляется в раствор для нейтрализации содержащихся в органических добавках природных сахаров и улучшения связующих качеств цемента и древесины.
Органические заполнители
В качестве наполнителя при производстве арболита используются отходы деревообрабатывающего производства. Главное отличие арболита от других видов лёгких бетонов состоит в том, что в его состав входят достаточно крупные компоненты – древесная щепа, костра льна, конопляная солома и т.д. От процентного содержания органического наполнителя зависят основные показатели материала: плотность, гигроскопичность, коэффициент теплопроводности и т.д.
- Древесная щепа – наиболее часто используемый заполнитель. Согласно ГОСТу, её размер не должен превышать 4 х 1 х 0,5 см. В связи с этим, технические характеристики арболитовых конструкций отличаются от характеристик опилкобетона и фибролита (стружкобетона).
Древесная щепа – главная составляющая арболитового блока
Нужный размер органической фракции получают при помощи специального станка-щепореза (шредера). Содержание щепы в общем объёме арболита может быть разным, и составлять от 30% до 90%.
- Льняная костра добавляется в таком же виде, в каком она получается на льноперерабатывающем заводе после предварительной обработки сырья.
- Конопляную солому перед использованием следует перемолоть в шредере.
Согласно техническим нормативам, льняные и конопляные наполнители должны иметь следующие размеры:
- Длина – от 15 до 25 мм.
- Ширина – от 2 до 5 мм.
В разных регионах для производства арболитовых блоков и панелей могут применяться и другие органические заполнители: рисовая и гречневая солома, отходы обработки хлопчатника и т.п.
В таблице даны технические характеристики арболита, изготовленных с применением разных органических наполнителей:
Технология производства
Технология производства арболита имеет ряд отличительных особенностей, которые касаются подготовки сырья, рецепта приготовления, дозировки компонентов. Её соблюдение обязательно как при промышленном выпуске, так и при производстве арболита своими руками в домашних условиях.
Подготовка органических заполнителей
Для деревобетона может использоваться щепа древесины хвойных пород – ели, сосны, пихты, а также лиственных деревьев с твёрдой древесиной – дуба, ясеня, берёзы.
Не рекомендуется применять в производстве щепу лиственницы и бука из-за химического состава – их древесина содержит значительно больше сахаров, что приводит к значительному снижению качества блоков. В крайнем случае, при производстве раствора с лиственничной или буковой щепой, придётся, как минимум, вдвое увеличить количество химдобавок – извести или хлористого кальция.
Щепа березы и ясеня – лучший наполнитель для арболитового блока
Первым шагом древесные отходы измельчаются посредством щепореза до размеров, регламентируемых ГОСТ №19-222-84 – не более 40х10х50 мм. Фактически же оптимальными размерами древесной фракции для формовки блоков являются 25х5х3 мм, так как более крупные компоненты хуже связываются цементным раствором и более склонны к расслаиванию в процессе эксплуатации.
После измельчения щепа просушивается. На крупных производственных линиях для этих целей применяют специальные сушилки барабанного типа, в которые подаётся горячий воздух.
Если арболит производится в домашних условиях, щепу складируют для просушки под навесами на срок не менее месяца, при температуре воздуха +15С.
Непосредственно перед замешиванием щепа замачивается на 6-8 ч в растворе воды с химическими добавками. Вода для этого должна соответствовать ГОСТу №23-732-79, где регламентируется её химический состав, кислотность и т.д. На деле же, при кустарном производстве деревобетона применяется любая доступная вода – из водопровода, реки или колодца. Единственное необходимое условие – она должна быть чистой и иметь температуру не ниже +15…+20С. После замачивания древесный наполнитель должен иметь влажность не более 30%.
Костра льна и солома конопли, для удаления из неё излишков сахаров, выдерживается на открытом воздухе не менее 2 – 3 месяцев при плюсовой температуре, либо замачивается в известковом молоке на 3-4 дня. Известковый раствор приготавливается в следующих пропорциях на 1 куб. м органики.
Органический заполнитель | Гашёная известь | Вода | Дополнительные условия |
1 куб. м костры льна или конопли | 2 – 2,5 кг | 150 – 200 л в зависимости от влажности наполнителя | Смесь перемешивается каждые 2 дня |
Пропорции смеси
Пропорции замеса могут незначительно изменяться, в зависимости от класса прочности деревобетона. Для получения более высокой марки арболита увеличивают долю цемента в общем объёме раствора. Ниже представлены рекомендуемые пропорции замеса раствора для деревобетона различных марок на куб готового раствора:
Марка | Портландцемент М-400 | Органический наполнитель | Химдобавки | Вода |
М-5 | 200 – 220 кг | 280 – 320 кг | 12-14 кг | 350 – 400 л |
М-15 | 250 – 280 кг | 240 – 300 кг | 12 кг | 350 – 400 л |
М-25 | 300 – 330 кг | 240 – 300 кг | 12 кг | 350 – 400 л |
М-50 | 350 – 400 кг | 220 – 240 кг | 10-12 кг | 350 – 400 л |
Химические добавки могут добавляться как по отдельности, так и комплексно. К примеру, строительные нормативы СН №54982 допускают смешивание сернокислого алюминия с известью в пропорции 8 кг и 4 кг на куб раствора.
Очерёдность загрузки
При замесе раствора важно соблюдать не только пропорции, но и очерёдность загрузки компонентов. Для изготовления качественной арболитной смеси обычные бетоносмесители, используемые для замеса бетона, не подойдут – щепа в них не сможет хорошо перемешаться с цементным раствором. Бетономешалка для арболита должна быть принудительного типа, например отечественные модели серии СБ, РН, импортные ZZBO и т.д. В них перемешивание компонентов производится не вращением барабана, а расположенным внутри него шнеком или лопастью.
Таблица 3. Технические характеристики принудительных смесителей серии СБ:
- Первым шагом в барабан смесителя насыпается подготовленная щепа в нужной пропорции.
- Затем бетоносмеситель запускается и в него заливается вода с растворёнными в ней химическими добавками. Органический заполнитель размешивается с химраствором в течение 30-60 секунд, чтобы щепки хорошо пропитались.
- После этого добавляется цемент и продолжается размешивание смеси в течение 3-5 минут, до получения однородной массы.
Формирование блоков
Формовка арбоблоков происходит с помощью специальных матриц, в которые заливается готовый раствор. Они изготавливаются из нержавеющей стали разборной конструкции для более лёгкого извлечения блоков.
Также такие формы можно изготовить самому из дерева или фанеры, обив их изнутри линолеумом или жестью. Размеры ячеек матрицы могут быть различными, в зависимости от потребностей в блоках тех или иных габаритов.
Трамбовка производится вручную, либо для этого используется вибростанок. В первом случае раствор заливается в формы слоями толщиной в 5 см, каждый из которых уплотняется металлической трамбовкой.
Во втором случае уплотнение раствора производится на вибростоле, которым обычно оборудуется промышленный станок для производства арболита.
Также при формовке для уплотнения раствора можно использовать ручной или механический пресс. Чтобы из уплотняемых блоков лучше выходил воздух, они периодически прокалывается металлическим стержнем.
Сушка
Сушка готовой продукции является завершающим этапом производственного процесса. В связи с особенностью конструкции, наилучшим вариантом является мягкий режим просушки.
Пропаривать арбоблоки по примеру железобетонных конструкций, не рекомендуется, так как материал теряет прочность из-за возрастающих внутренних напряжений. По этой же причине не следует пытаться ускорить высыхание блоков при помощи сушильных камер и других приспособлений.
Оптимальный режим просушки для арболита – температура 40-50 градусов, при влажности воздуха порядка 70-80%. В этом случае блоки набирают необходимую для распалубки прочность уже спустя 18-20 ч. что составляет около 1/3 от окончательной марочной. Дальнейшая выдержка материала производится при температуре 15-20 С в течение одной-двух недель – за это время деревобетон набирает окончательную прочность.
Бакелит — Википедия
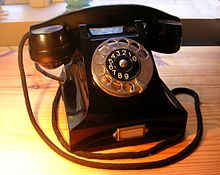
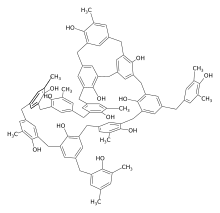
Бакелит (по имени американского химика и изобретателя Лео Бакеланда[1]), карболит, полиоксибензилметиленгликольангидрид — продукт поликонденсации фенола с формальдегидом в присутствии щелочного катализатора, резол (из группы фенолформальдегидных смол), термореактопласт. Образуется на начальном этапе синтеза фенолформальдегидной смолы. Вязкая жидкость или твёрдый растворимый легкоплавкий продукт от светло-жёлтого до чёрного цвета[2].
Используется в качестве связующего в производстве абразивных изделий холодного и горячего прессования и вальцевания, а также для других технических целей. Бакелит растворим в спирте, при длительном нагревании переходит в нерастворимую и неплавкую форму. Это свойство бакелита используется при изготовлении пластических масс. Спиртовые растворы бакелита применяют как лаки.
Ноготь на бакелите черты не оставляет. Бакелит плохой проводник тепла, хорошо сопротивляется давлению, трению, толчкам и ударам. По эластичности приближается к целлулоиду. Хорошо поддаётся обработке на токарном станке. Хороший изолятор, его диэлектрическая проницаемость — от 5,6 до 8,85, то есть выше, чем у гуттаперчи и так же велика, как у слюды. Вода, разведённые щелочи и кислоты на бакелит не действуют, лишь горячие концентрированные азотная и серная кислоты его разлагают. Бакелит устойчив до +300 °C, при более высокой температуре происходит обугливание, но полного сгорания не происходит.
Изначально бакелит создавался в качестве замены шеллаку — природной смоле, вырабатываемой тропическими насекомыми — лаковыми червецами. Произведя реакцию поликонденсации фенола и формальдегида, Лео Бакеланд сначала получил термопластичную фенолоформальдегидную смолу, которая отверждалась только в присутствии отвердителей. Данный полимер Лео Бакеланд назвал «Novolak», однако успеха на рынке он не имел. Продолжая исследования в области реакции между фенолом и формальдегидом, а также подбирая различные наполнители (асбестовый порошок и др.), Лео Бакеланд получил полимер, не требующий отвердителей[2], для которого не смог найти растворителя. Это навело его на мысль, что такой практически нерастворимый и не проводящий электричества полимер может оказаться очень ценным. В 1909 году Лео Бакеланд сообщил о полученном им материале, который он назвал «бакелитом». Данный материал был первым синтетическим реактопластом — пластиком, который не размягчался при высокой температуре. В 1909 году Лео Бакеланд получил патент на свой материал — U. S. Patent 0.942.809 Condensation product and method of making same. А в следующем 1910 году Лео Бакеланд основал компанию, которую назвал Bakelite Corporation.
Настольная лампа из карболита производства завода «Карболит» (Орехово-Зуево)В России также велись работы по созданию пластических масс на основе фенола и формальдегида, в частности, работы велись в лаборатории на шелкоткацкой фабрике в деревне Дубровке в окрестностях г. Орехово-Зуево. В 1914 году группа химиков: В. И. Лисев, Г. С. Петров и К. И. Тарасов — синтезировала карболит, российский аналог бакелита. Своё название карболит получил от карболовой кислоты, другого названия фенола. Для продвижения нового изобретения в России и за границей 6 октября 1915 года был основан торговый дом «Васильев и Ко». 26 октября 1916 года Московское Губернское правление выдало торговому дому свидетельство о том, что ему разрешается содержание завода для выработки диэлектрического материала под названием «карболит». Был учреждён завод в Московской губернии, Богородском уезде, 3-м стане Зуевской волости при селе Крестовоздвиженском. Завод получил название «Карболит», он существует и поныне. В 1919 году завод был национализирован, а в 1931 году включён в объединение «Союзхимпластмасс».
В настоящее время[источник?] фенолформальдегидные смолы и пластмассы на их основе выпускаются на многих отечественных химических заводах. Кроме готовых изделий и листовых материалов, промышленностью выпускаются бакелит жидкий (БЖ-1, БЖ-2, БЖ-3, БЖ-3У, БЖ-4) и бакелитовая смола/лак (СБС-1, СБС-2, СКС-1, СКС-2, С-1, С-35, С-45).
По целому ряду свойств пластмассы на основе фенолоформальдегидной смолы и сейчас остаются непревзойдённым материалом.[3] Для придания изделиям формы в резольную смолу добавляют (или добавляли ранее) различные наполнители, такие как древесная мука[4], целлюлоза, стекловолокно, порошок горных пород или металлов, текстильные волокна и тому подобные.[5]
В советском мотопроме бакелитовым лаком герметизировали стык центральных половин моторов[источник не указан 1854 дня].[значимость факта?] Бакелит был также чрезвычайно распространён в локомотивостроении 50-х годов 20-го века. Так, из бакелита изготавливались на замену прежним деревянным подвижные рамы форточек, оконные рамы, корпуса светильников и высоковольтных аппаратов. Большое количество бакелитовых деталей можно обнаружить в узкоколейном тепловозе ТУ2 (у локомотивов первого выпуска оконные рамы деревянные, а у самых поздних — штампованные стальные) и пассажирском вагоне ПВ51, выпускавшемся на Демиховском машиностроительном заводе (г. Орехово-Зуево).[источник не указан 1059 дней][значимость факта?] Также бакелит достаточно распространён среди материалов для курительных мундштуков, т.к. не деформируется при вдыхании горячего дыма и не выделяет токсичных паров, как простой пластик. Из бакелита изготавливали смертные медальоны для солдат ВОВ. В 1926-1945 гг. на Кёнигсбергской янтарной мануфактуре бакелит использовался как дешевый заменитель янтаря[6].
- ↑ Бакелит // Российский энциклопедический словарь / глав. ред. А. М. Прохоров. — М.: «Большая российская энциклопедия», 2000. — Книга 1. — С. 116.
- ↑ 1 2 Резол // Российский энциклопедический словарь / глав. ред. А. М. Прохоров. — М.: «Большая российская энциклопедия», 2000. — Книга 2. — Стр. 1313.
- ↑ Группы материалов, которые могут изготавливать, в том числе, с использованием резола, смотрите в статье фенолформальдегидная смола#Применение.
- ↑ Clegg, Brian Chemistry in its element – bakelite (неопр.). Royal Society of Chemistry — RSC.org. Дата обращения 4 мая 2014.
- ↑ Hans-Dieter Jakubke, Ruth Karcher (Hrsg.): Lexikon der Chemie, Spektrum Akademischer Verlag, Heidelberg, 2001. (нем.)
- ↑ Космовская-Церанович Б. Янтарь в Польше и мире. — Калининград: Музей янтаря, 2014. — С. 134.
- ГОСТ 4559-2017 «Бакелит жидкий. Технические условия».
- ГОСТ 901-2017 «Лаки бакелитовые. Технические условия».
- ГОСТ 10759-64 «Смола фенолоформальдегидная. Резол 300».
- ГОСТ 20916-87 «Плиты теплоизоляционные из пенопласта на основе резольных феноло-формальдегидных смол. Технические условия».
Технология изготовления арболита в домашних условиях
a href=http://www.arbolit.net/assets/files/2014/02/1387212921_arbolit.jpgimg class=alignleft wp-image-24541 title=Блок арболита alt=Блок арболита в домашних условиях src=http://www.arbolit.net/assets/files/2014/02/1387212921_arbolit-300×207.jpg width=300 height=207 //a
Арболит еще со времен Советского союза считается отличным стройматериалом, который пригоден для возведения стен в любых помещениях. Этот материал относится к легким бетонам, а в простонародье его еще величают опилкобетоном.
Производство арболита в домашних условиях — не такой уже и высокотехнологичный процесс, поэтому справиться с этой задачей вполне реально без специальных приспособлений.
h5Технология изготовления арболита/h5
Исходя из народного названия, несложно догадаться, что в состав материала, как и в состав любого бетона, входит цемент — марки 400 или 500. Для повышения показателей прочности также может использоваться и другой цемент.
Также из названия понятно, что в состав входят опилки. Но, не только опилки можно добавлять в арболит — это может быть также мелкая древесная щепа и стружка. Если какого-либо наполнителя недостаточно, то его заменяют остатками хвои, коры или листвы, но таких добавок в смеси может быть не более 5% от массы того наполнителя, который необходимо заменить.
Размеры органических материалов в составе арболита не должны превышать допустимых норм —, а это не более чем 5 мм в ширину и не более чем 25 мм в длину. Поэтому древесные отходы вначале пропускаются через дробилку, а уж после этого смешивают с цементом и химическими добавками.
В условиях заводского изготовления арболита добавление химических веществ обязательно, так как эти вещества способны нейтрализовать сахар, который в больших количествах содержится в органике, а так как он негативно сказывается на прочности готового вещества, то нейтрализация его обязательна.
Наиболее распространенным химическим реактивом является хлористый кальций, а также сернокислый алюминий. Если речь идет о производстве арболита в домашних условиях, то химических веществ может попросту не оказаться под рукой, поэтому многие домашние умельцы обходятся и без них.
Но сахар убрать нужно обязательно, потому что готовый материал будет вспучиваться, из-за того, что органика неизбежно начнет гнить. Чтобы предотвратить этот разрушительный процесс нужно выдержать все древесные отходы под открытым небом не меньше чем четверть года, а это значит, что нужно дать просохнуть опилкам, щепе и стружке 3–4 месяца на свежем воздухе.
На заметку: Самые лучшие перегородки для санузлов по низким ценам вы сможете купить в компании www.oki-doki.ru . Рекомендуем!
h5Производство арболита в домашних условиях/h5
Начинается производство арболита с обработки отходов деревообрабатывающего производства. Для начала дробленая органика заливается водой и хорошенько размешивается. Специалисты также советуют выдержать древесную массу в известковом растворе не меньше чем 3 часа. a href=http://www.arbolit.net/assets/files/2014/02/shepa.jpgimg class=alignright wp-image-24542 title=Опилки alt=деревянная стружка src=http://www.arbolit.net/assets/files/2014/02/shepa.jpg width=289 height=193 //a
Далее, замоченная в растворе известки древесина смешивается с цементом. Пропорции должны быть примерно таковы: вода, опилки и цемент в соотношении 4:3: 3.
Смешивать раствор лучше всего в бетономешалке, потому что совсем недопустимы комки, а такой консистенции можно добиться лишь с использованием этого инструмента.
Масса на выходе должна иметь немного рассыпчатую структуру, но при этом, если сжать немного раствора в кулаке, он должен приобретать форму плотного комка.
Если вы убедились в том, что раствор хорошо держит форму, значит, его можно дальше смело эксплуатировать по своему назначению. Как видите, мини-станок для производства арболита вам вряд ли понадобится, а вот бетономешалкой вооружиться не забудьте.
Вообще, арболит даже на западе признан экономически выгодным материалом, поэтому он там востребован, а вот наш рынок этому материалу еще предстоит завоевать.
Благодаря такой небольшой известности бизнес по изготовлению арболита сегодня очень прибылен, особенно в виду того, что материалы на его изготовление необходимы самые дешевые, а вот преимущества готового материала довольно весомы и нельзя не оценить по достоинству следующее:
ul
li- Материал подходит для изготовления таких конструкций, как перемычки, блоки и плиты. А также материал можно использовать для монолитной заливки несущих стен. /li
li- После затвердевания арболит легко поддается механическому воздействию, поэтому его можно без опаски распиливать, просверливать в нем дырки, забивать в него гвозди и даже ввинчивать шурупы и дюбеля. /li
li- Производство арболита славится простотой технологии и дешевизной «ингредиентов». /li
li- Затвердевшие блоки отлично воспринимают любой тип отделки, поэтому можно дать волю своей фантазии и смело испытывать на прочность арболит всяческими штукатурками или облицовочным кирпичом. Можно даже обшить его гипсокартоном без изготовления специального профилированного каркаса, потому что материал можно крепить сразу к стенам. /li
li- Теплоизоляционные свойства арболита на высочайшем уровне, поэтому дома из него не нуждаются в таких затратах отопления, как, к примеру, кирпичные дома. /li
li- Материал не пожароопасен, даже несмотря на то, что в его составе так много древесины — она ведь обработана известкой и прочей химией, и гореть не может. /li
li- Грибок, плесень, гниение — все это не страшно арболиту. /li
li- Прекрасная морозостойкость обеспечивает популярность стройматериала даже в суровых северных регионах. /li
li- В придачу ко всему вышеперечисленному высоки звукоизоляционные параметры опилкобетона. /li
/ul
Чаще всего арболитная смесь формируется в блоки, которые мало того, что легкие в весе, но и легко транспортируются, ну, а разнообразие зданий и конструкций, которые можно из него построить просто безгранично.
p style=text-align: center;a href=http://www.arbolit.net/assets/files/2014/02/arbolit_stanok_jpg_1306931664.jpgimg class=aligncenter size-full wp-image-24543 title=Арболитный станок alt=станок для арболита src=http://www.arbolit.net/assets/files/2014/02/arbolit_stanok_jpg_1306931664.jpg width=600 height=450 //a/p
h5Форма для изготовления арболитового блока/h5
Формы для изготовления блоков можно сделать самостоятельно из старых деревянных ящиков со съемным днищем. Опытные умельцы советуют внутри оббить такой ящик обыкновенным линолеумом для облегчения процедуры вынимания готового блока. Сверху стоит оставить немного места — около 20 мм, для того, чтобы была возможность дополнительно залить блок раствором штукатурки.
Итак, арболит — это экологически чистый материал, поэтому так важно ориентироваться на это качество, при постройке дома, который не будет оказывать негативного влияния на здоровье человека.
h4Видео-руководство: /h4
iframe src=//www.youtube.com/embed/TYPMVVbfpV8?feature=player_detailpage height=360 width=640 allowfullscreen= frameborder=0/iframe